What is Powder Metallurgy?
Powder Metallurgy, often referred to as PM, is a versatile manufacturing process that produces metal parts and components from fine metal powders. It offers unique advantages over traditional methods such as casting and machining, allowing for greater customization of materials, greater cost-efficiency, and greater design flexibility. In this article, we will examine the key aspects of powder metallurgy and its applications in various industries.
1. Metal Powder Production
The first step in powder metallurgy is the production of metal powders. This can be achieved through a variety of methods including atomization, mechanical alloying and chemical processes. In atomization, a metal alloy is melted and then rapidly cooled to form small droplets that solidify into fine powder particles. In mechanical alloying, elemental powders are combined in a high-energy ball mill to produce a uniform alloy composition. The chemical processes consist in reducing the metal salts to obtain powders with the desired properties.
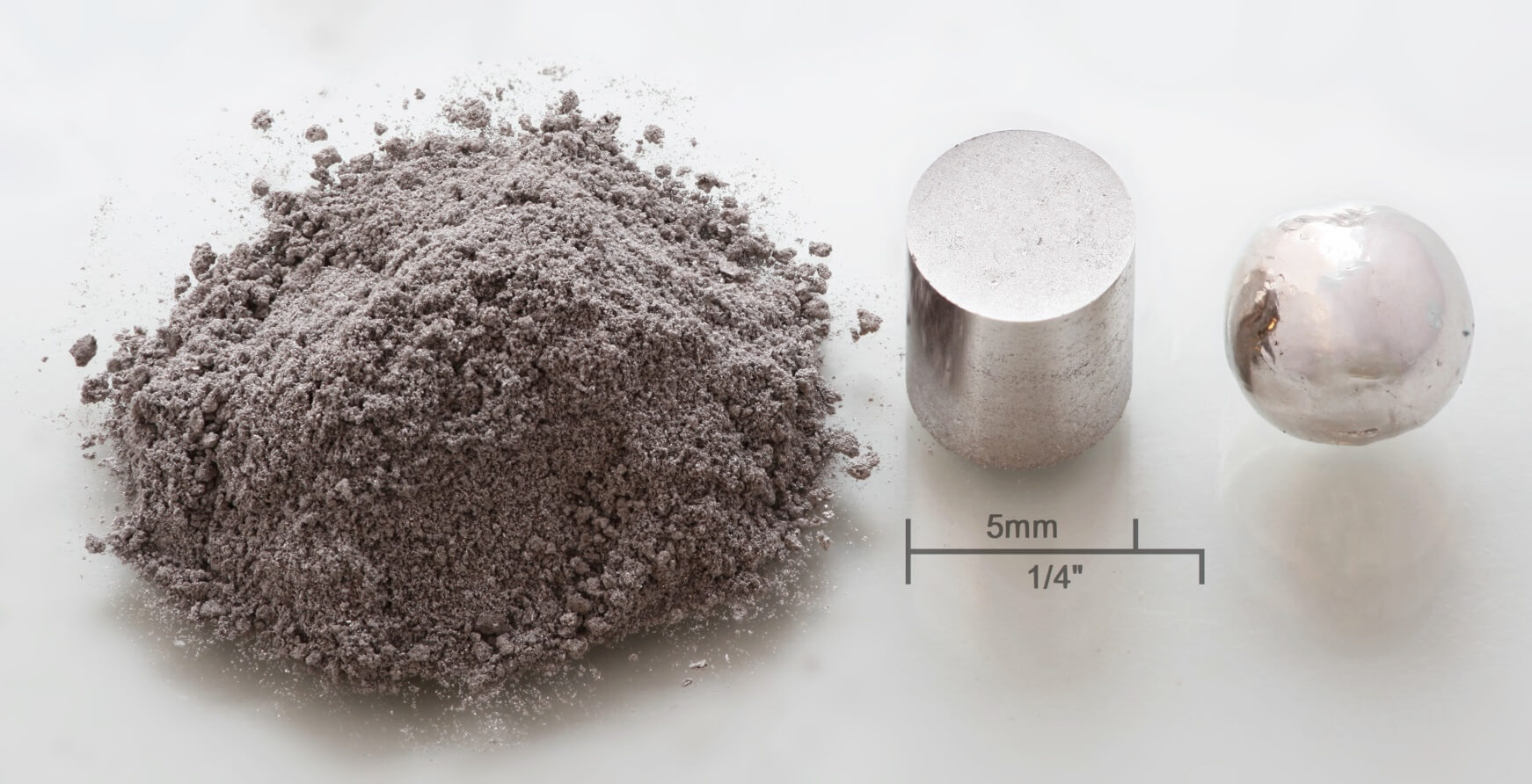
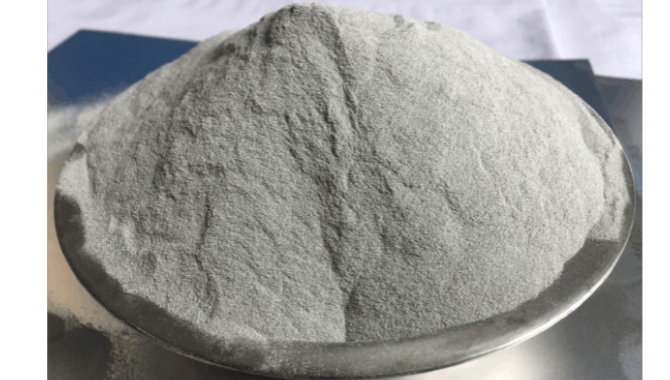
2.Metal Powder Blend
Once the metal powders are prepared, they are thoroughly mixed together to obtain a custom alloy composition. This mixing process allows the incorporation of different metal powders or alloying elements to achieve specific properties such as increased strength, corrosion resistance, or electrical conductivity. The powders are thoroughly mixed to ensure an even consistency.
3.Compaction
After mixing, the mixed powders are compacted into the desired shape using special equipment under high pressure. This densification process usually occurs at room temperature or with the application of heat, referred to as hot densification. The compression creates a “green” hardware part, i.e. a compact but filigree structure.
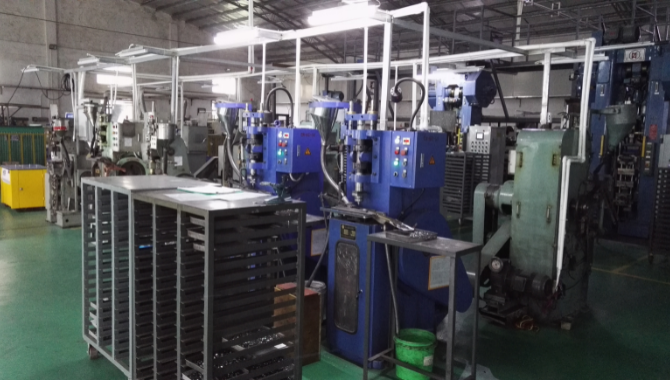
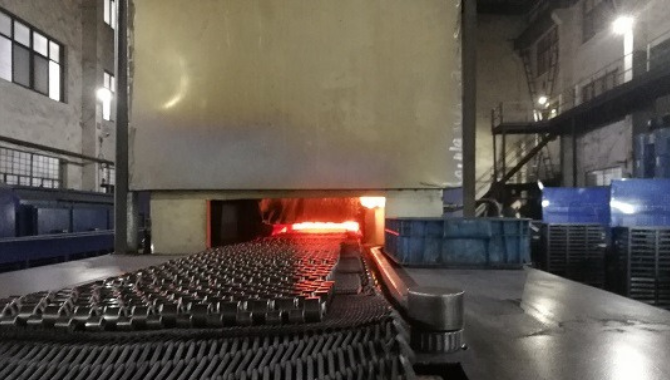
4.Sintering
The blank then undergoes a thermal process called sintering. Sintering is the process of heating a part below its melting point, fusing the metal particles together through diffusion, resulting in a denser, stronger part. During sintering, the shape of the workpiece is retained and at the same time, it is given additional strength. The sintering process can also help to remove any residual porosity in the blank.
Powder Metallurgy Applications:Powder Metallurgy is used in many industries including automotive, aerospace, electronics, healthcare, energy and more.Some notable applications include:
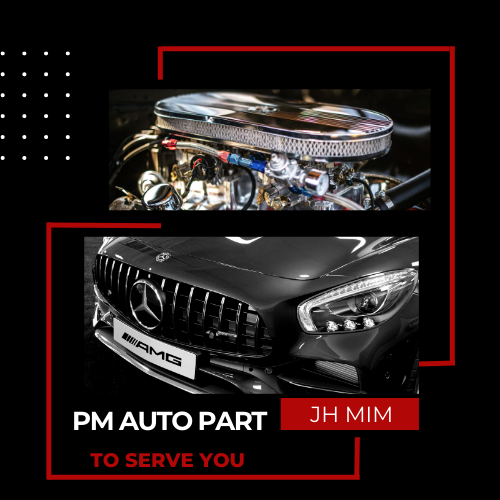
Powder metallurgy is used extensively in the automotive industry to manufacture various components such as gears, bearings, valve seat inserts and camshafts. These components feature excellent wear resistance, high strength and dimensional stability, making them ideal for demanding automotive applications.
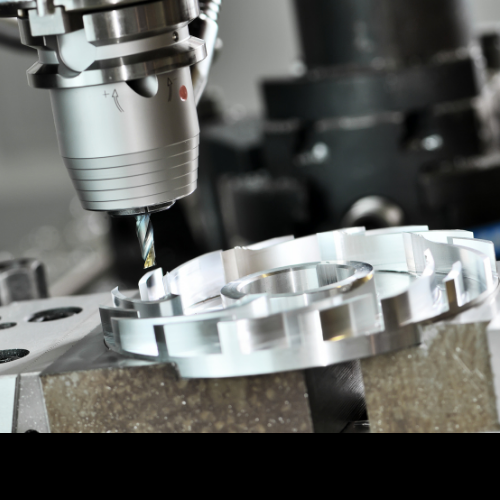
In the aerospace industry, powder metallurgy is used to manufacture complex shaped components such as turbine blades, structural parts and heat shields.This process enables the production of lightweight, efficient parts with complex designs, ensuring optimal performance and durability.
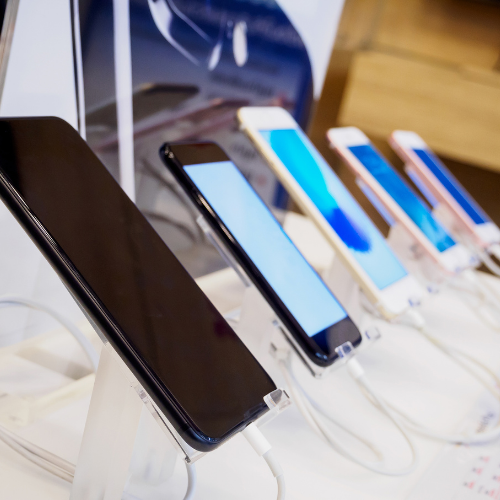
Powder metallurgy plays a key role in the manufacture of electrical contacts, magnetic components and electrical connectors for various electronic devices. The precise control of alloy composition and the ability to incorporate insulating materials into components make powder metallurgy an excellent choice for electrical applications.
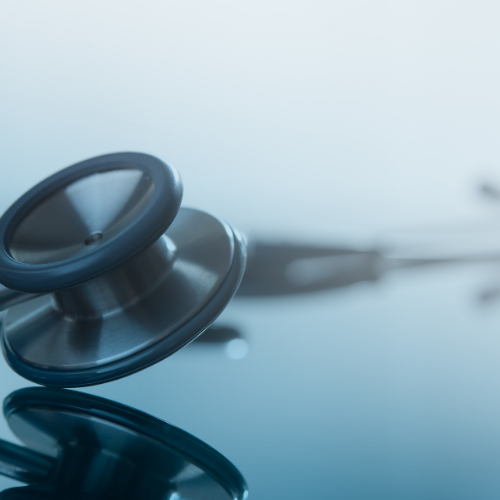
The healthcare industry uses powder metallurgy to manufacture medical implants, dental components and surgical instruments. Powder metallurgy enables the production of biocompatible materials with excellent mechanical properties, ensuring safety and durability in medical applications.
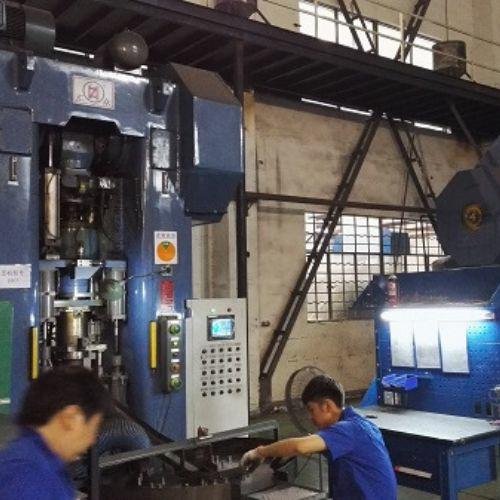
Powder metallurgy is a very versatile and efficient manufacturing process that offers many advantages over conventional methods. Thanks to adaptable material properties, cost efficiency and design flexibility, powder metallurgy finds a wide range of applications in a wide variety of industries. From the automotive and aerospace industries to electronics and healthcare, the possibilities of this process are enormous.
JH MIM POWDER METALLURGY
As technology and research continue to advance, powder metallurgy is expected to continue to expand its applications and contribute to the development of innovative materials and components. Its ability to handle complex geometries, improve material performance, and meet the needs of diverse industries makes powder metallurgy the preferred manufacturing technique of the future.
If you have any further questions or need more help with making PM parts, do not hesitate to contact JH MIM