Introduction to Sintered Metal Parts
Sintered metal parts are components created through the powder metallurgy process, which involves compacting metal powders into a desired shape and then heating them to a temperature below the melting point to bond the particles together. This technique allows for the production of complex shapes and high-precision parts with excellent mechanical properties.
Applications of Sintered Metal Parts
Automotive Industry
Sintered metal parts are widely used in the automotive industry for components such as gears, bearings, bushings, and structural parts. Their cost-effectiveness and reliability make them ideal for high-volume production.
Industrial Machinery
In industrial machinery, sintered metal parts are used in applications such as pumps, compressors, and various types of machinery components. Their durability and ability to withstand harsh operating conditions are key benefits.
Consumer Electronics
Sintered metal parts are found in consumer electronics, including mobile phones, printers, and electric motors. Their precision and ability to produce small, intricate parts are valuable in these compact devices.
Aerospace
The aerospace industry utilizes sintered metal parts in various applications due to their lightweight and high-strength properties. These parts contribute to the efficiency and performance of aircraft systems.
Medical Devices
Sintered metal parts are used in medical devices for their precision and biocompatibility. Applications include surgical instruments, implants, and dental tools.
Sintered Metal Parts (3)
About Us
JHMIM As One-Stop Solution To Sintered Metal Parts Problems
20 Years Experence, Low 10%-15% Cost, 24 Hours Reply , LOW MOQ 2000 pcs
Advantages of Sintered Metal Parts
Cost-Effectiveness
Sintered metal parts are often more economical to produce than parts made using traditional manufacturing methods. The powder metallurgy process allows for high-volume production with minimal material waste, reducing overall manufacturing costs.
Material Efficiency
The powder metallurgy process is highly efficient in terms of material usage. The ability to recycle metal powders and the minimal waste produced make it an environmentally friendly manufacturing method.
Design Flexibility
Powder metallurgy allows for the creation of complex shapes and intricate geometries that are difficult or impossible to achieve with traditional manufacturing techniques. This design flexibility enables the production of parts with unique features tailored to specific applications.
Consistent Quality
The controlled nature of the powder metallurgy process ensures consistent quality and uniformity in each part produced. This consistency is critical for applications requiring high precision and reliability.
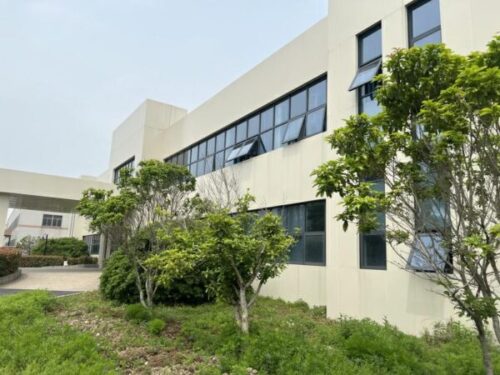
The production process involves several key steps:
- Powder Production: Creating fine metal powders from various metals or alloys.
- Compaction: Compressing the metal powder into a mold to form a “green” part.
- Sintering: Heating the green part in a controlled atmosphere to bond the metal particles.
- Secondary Operations: Additional processes like sizing, coining, heat treatment, machining, or surface treatment to achieve the final specifications.
Sintered metal parts can be made from a variety of materials, including:
The choice of material depends on the required properties of the final part, such as strength, hardness, electrical conductivity, or corrosion resistance.
Sintered metal parts offer several advantages over traditionally manufactured parts:
- Efficiency: Less material waste and often lower production costs.
- Precision: High dimensional accuracy and uniformity.
- Complexity: Ability to create complex shapes that might be challenging or impossible with traditional methods.
- Customization: Easier to produce custom parts in high volumes.
Sintered metal parts can achieve comparable strength and durability to forged or machined parts, especially when additional processes like heat treatment or machining are applied. The choice of metal powder and sintering conditions also play a crucial role in determining the final mechanical properties.
Yes, sintered metal parts can be heat-treated to enhance their mechanical properties such as hardness and strength. Heat treatment is a common secondary operation for improving the performance of sintered parts.
The maximum size of sintered metal parts is generally limited by the capabilities of the compaction equipment and the sintering furnace. However, advancements in technology are continually increasing the size limits. For very large parts, other manufacturing methods might be more suitable.
Quality assurance for sintered metal parts involves:
- Material Selection: Using high-quality metal powders.
- Process Control: Monitoring and controlling the compaction and sintering processes.
- Inspection: Conducting dimensional checks and mechanical testing on finished parts.
- Certification: Adhering to industry standards and certifications.
The lead time for producing sintered metal parts depends on several factors, including the complexity of the part, the volume of production, and the availability of materials. Generally, the powder metallurgy process allows for faster production times compared to traditional manufacturing methods, especially for large batches.