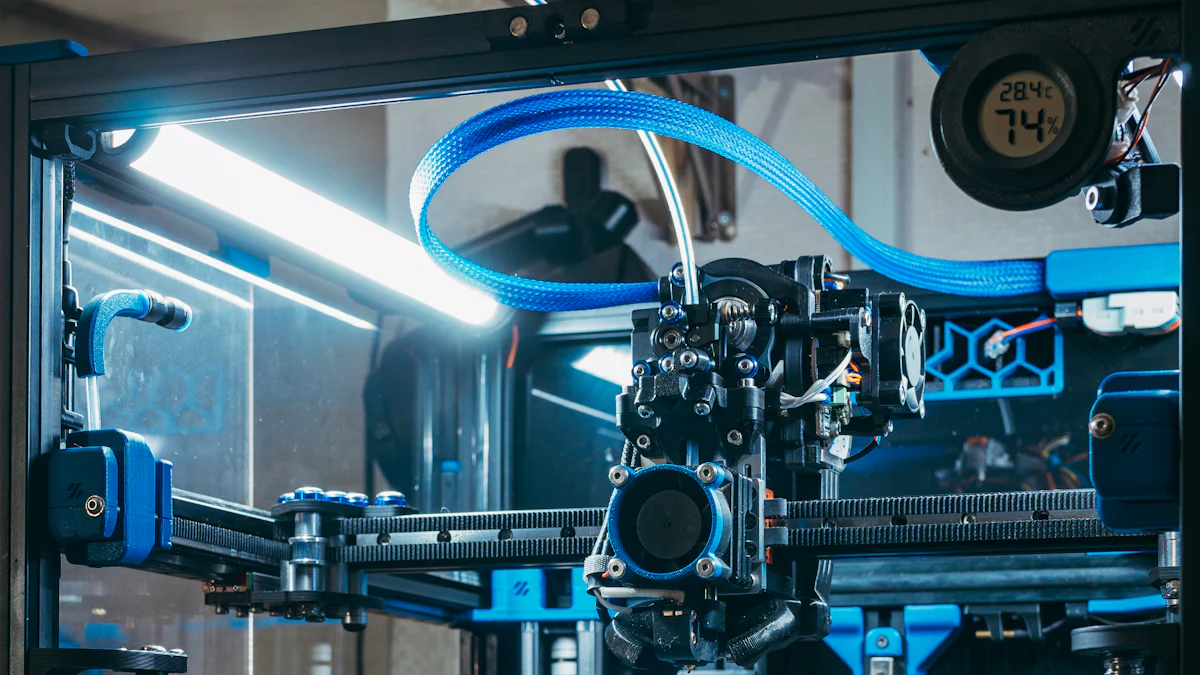
Is Metal Injection Molding the right choice for your project? This question often arises when you need to produce small, complex metal components. Metal Injection Molding, or MIM, combines the versatility of plastic injection molding with the strength and integrity of metal. This process has gained popularity due to its ability to create intricate parts that traditional methods struggle to produce. With the MIM market experiencing significant growth, especially in industries like automotive and electronics, understanding its potential benefits can help you make an informed decision.
Understanding Metal Injection Molding
What is Metal Injection Molding?
Metal Injection Molding (MIM) is a manufacturing process that combines the flexibility of plastic injection molding with the strength of metal. This innovative technique allows you to produce small, complex, and precision-shaped parts from a variety of materials. By using metal powders mixed with a plastic and wax binder, known as feedstock, MIM can create intricate geometries that traditional methods struggle to achieve.
The process begins by mixing fine metal powders with a thermoplastic binder to form a feedstock. This mixture is then injected into a mold cavity, similar to plastic injection molding. The resulting part undergoes several post-processing steps, including debinding and sintering, to remove the binder and fuse the metal particles together. This results in a solid metal part with superior strength and excellent surface finish.
MIM is particularly effective for high-volume production of small components with complex shapes. It offers significant cost savings, producing parts for up to 50% less than CNC machining or casting. The process is highly repeatable, ensuring consistent quality across large production runs. MIM provides design freedom, allowing for part consolidation and weight reduction compared to other fabrication techniques.
How Does MIM Work?
The Metal Injection Molding process involves several key steps:
-
Feedstock Preparation: You start by mixing metal powders with a polymer binder to create a feedstock. This mixture is processed through a twin-screw extruder, which pelletizes the feedstock for injection molding.
-
Injection Molding: The feedstock is injected into a mold cavity under high pressure. This step shapes the material into the desired form, much like plastic injection molding.
-
Debinding: After molding, the binder is removed from the part. This step involves chemical or thermal processes to ensure uniform debinding across all parts, which is crucial for maintaining consistency in part quality.
-
Sintering: The debound parts are heated to a high temperature in a controlled atmosphere. This causes the metal particles to fuse together, resulting in a dense, solid metal component.
-
Post-Processing: Depending on the application, additional steps such as machining or surface finishing may be required to achieve extremely tight tolerances or specific surface finishes.
MIM is ideal for producing medium to high quantities of complex metal components, especially those requiring tight tolerances and net shapes. It eliminates the need for costly secondary operations, making it a cost-effective alternative to traditional metal forming techniques like machining and investment casting.
By understanding the Metal Injection Molding process, you can determine if it aligns with your project’s needs, offering a balance of complexity, consistency, and cost-effectiveness.
Advantages of Metal Injection Molding
Efficiency in Production
Metal Injection Molding (MIM) offers remarkable efficiency in production. You can produce complex parts quickly, thanks to the streamlined process. Unlike traditional methods, MIM reduces labor and shortens production cycles. This efficiency stems from the ability to mold intricate designs in a single step. You avoid the need for multiple machining operations. The process also minimizes material waste, making it an environmentally friendly choice. When you need to manufacture medium to high volumes, MIM stands out as a time-saving option.
Cost-Effectiveness
MIM provides significant cost savings compared to other manufacturing techniques. You benefit from reduced labor costs and shorter production times. The process eliminates many secondary operations, which further cuts expenses. For medium to high production volumes, MIM proves to be more economical than CNC machining or casting. You can achieve up to 50% cost reduction compared to these traditional methods. The material savings also contribute to the overall cost-effectiveness. By choosing MIM, you ensure a budget-friendly approach without compromising on quality.
Ability to Produce Complex Parts
The ability to produce complex parts is a standout feature of MIM. You can create intricate geometries that are challenging for other methods. The process allows for high precision and excellent surface finishes. You can achieve tight tolerances and net shapes with ease. MIM supports a wide range of materials, including stainless steel and titanium. This versatility makes it suitable for various industries, from automotive to medical devices. When your project demands complexity and precision, MIM delivers exceptional results.
Complexity of the MIM Process
Steps Involved in MIM
The Metal Injection Molding (MIM) process involves several distinct steps, each crucial for producing high-quality metal components. Understanding these steps helps you appreciate the complexity and precision involved in MIM.
-
Compounding: You begin by mixing fine metal powders with a polymer binder to create a homogeneous feedstock. This step ensures that the metal particles are evenly distributed within the binder, which is essential for consistent part quality.
-
Molding: The feedstock is injected into a mold cavity under high pressure. This step shapes the material into the desired form, similar to plastic injection molding. The precision of this step allows you to achieve complex geometries and intricate details.
-
De-binding: After molding, the binder is removed from the part. This step involves chemical or thermal processes to ensure uniform debinding across all parts. Proper debinding is crucial for maintaining the integrity and strength of the final product.
-
Sintering: The debound parts are heated to a high temperature in a controlled atmosphere. This causes the metal particles to fuse together, resulting in a dense, solid metal component. Sintering enhances the mechanical properties and dimensional accuracy of the parts.
These steps highlight the meticulous nature of the MIM process. Each phase requires careful control and precision to ensure the production of high-quality components.
Challenges and Considerations
While MIM offers numerous advantages, it also presents certain challenges and considerations that you must address to ensure successful implementation.
-
Material Selection: MIM supports a wide range of materials, including stainless steel, titanium, and various alloys. Choosing the right material for your project is crucial, as it affects the mechanical properties and performance of the final product.
-
Mold Design: The design of the mold plays a significant role in the success of the MIM process. You need to consider factors such as part geometry, tolerances, and surface finish requirements when designing the mold. A well-designed mold ensures accurate and consistent part production.
-
Cost Implications: The initial cost of creating molds can be high, making MIM more suitable for medium to high-volume production. You should evaluate the cost-effectiveness of MIM based on your project’s production volume and complexity.
-
Process Optimization: Ongoing research aims to optimize the MIM process for larger components and improve binder systems. Staying informed about advancements in MIM technology can help you leverage new techniques and materials for better results.
By understanding these challenges and considerations, you can make informed decisions about whether MIM is the right choice for your project. Addressing these factors ensures that you maximize the benefits of MIM while minimizing potential drawbacks.
Applications of Metal Injection Molding
Industries Benefiting from MIM
Metal Injection Molding (MIM technology) is transforming various industries by enabling the production of complex metal parts with high precision and efficiency. You will find MIM particularly advantageous in sectors that demand intricate geometries and high-quality finishes.
-
Automotive Industry: MIM plays a crucial role in manufacturing components like gearboxes, turbochargers, and fuel injectors. The ability to produce lightweight and durable parts makes it a preferred choice for automotive manufacturers.
-
Medical Field: In the medical industry, MIM is instrumental in creating intricate surgical tools and implants. The process ensures excellent corrosion resistance and high mechanical strength, which are essential for medical applications.
-
Electronics Sector: For electronics, MIM offers the precision needed for producing small, complex parts such as connectors and heat sinks. The process supports a wide range of materials, allowing for customization based on specific electronic requirements.
-
Firearms Manufacturing: MIM is widely used in the firearms industry to produce components like triggers and hammers. The method provides the necessary strength and precision, ensuring reliable performance.
“MIM technology is revolutionizing the manufacturing industry by enabling the production of complex metal parts with high precision and efficiency.” This quote highlights the transformative impact of MIM across various sectors.
Common Products Made with MIM
The versatility of Metal Injection Molding allows you to create a wide array of products. Here are some common items produced using this innovative process:
-
Gears and Bearings: MIM excels in producing gears and bearings with precise dimensions and excellent surface finishes. These components are vital in machinery and automotive applications.
-
Surgical Instruments: The medical industry benefits from MIM’s ability to produce intricate surgical instruments. These tools require high precision and durability, which MIM effectively delivers.
-
Electronic Connectors: In electronics, MIM is used to manufacture connectors that require tight tolerances and complex shapes. The process ensures consistent quality and performance.
-
Watch Components: The watchmaking industry utilizes MIM for producing small, detailed parts like watch cases and gears. The method allows for high precision and excellent aesthetic finishes.
By understanding the industries and products that benefit from MIM, you can better assess its potential for your specific project needs. The process’s ability to produce complex parts with high precision and efficiency makes it a valuable tool in modern manufacturing.
Comparing MIM with Other Manufacturing Processes
MIM vs. traditional metal casting
When you compare Metal Injection Molding (MIM) to traditional metal casting, several key differences emerge. MIM excels in producing complex and precision-shaped parts. It achieves this with a variety of materials, often at a cost 50% less than casting. This makes MIM a cost-effective alternative for medium to high production volumes.
Traditional metal casting, on the other hand, suits simpler geometries and larger components. It involves pouring molten metal into a mold, which can limit the intricacy of the designs. Casting may require additional machining to achieve tight tolerances, adding to the overall cost and time.
Key Differences:
- Complexity: MIM handles intricate designs better than casting.
- Cost: MIM offers economic benefits for high-volume production.
- Precision: MIM provides superior surface finishes and tighter tolerances.
“MIM provides a cost advantage over machining and casting for medium to high production volumes provided secondary processing is minimal.”
MIM vs. CNC Machining
CNC machining and MIM serve different purposes in manufacturing. CNC machining offers precise control over properties and is ideal for low production volumes or simpler geometries. It involves removing material from a solid block, which can be time-consuming and costly for complex parts.
MIM, however, shines in producing medium to high quantities of complex components. It consolidates multi-component designs into a single part, reducing the need for secondary operations. This results in significant cost savings, especially for intricate designs.
Key Differences:
- Production Volume: MIM is more cost-effective for medium to high volumes.
- Design Complexity: MIM handles complex shapes better than CNC machining.
- Material Efficiency: MIM minimizes waste compared to CNC machining.
Is MIM Right for Your Project?
Factors to Consider
When deciding if Metal Injection Molding (MIM) suits your project, you should evaluate several critical factors. These considerations will help you determine the feasibility and benefits of using MIM for your specific needs.
-
Complexity of Design: MIM excels in producing intricate and complex parts. If your project involves detailed geometries that traditional methods struggle to achieve, MIM might be the right choice. Proper part design is crucial for maximizing the benefits of the MIM process.
-
Production Volume: MIM is most cost-effective for medium to high production volumes. The initial mold costs can be high, so projects with larger quantities benefit more from this process. For low-volume production, other methods might be more economical.
6 3. Material Requirements: Consider the materials you need for your project. MIM supports a wide range of materials, including stainless steel and titanium. If your project requires specific material properties, MIM can offer the necessary flexibility.
7 4. Cost Implications: Evaluate the overall cost-effectiveness of MIM. While the initial setup costs can be significant, the process often results in lower per-part costs for large production runs. Selecting a competent MIM supplier is key to cost-effective production of high-quality components.
- Quality and Precision: MIM provides excellent surface finishes and tight tolerances. If your project demands high precision and consistent quality, MIM can deliver these attributes effectively.
Project Suitability Checklist
To further assess if MIM is suitable for your project, use the following checklist:
- Does your project involve complex part geometries?
- Are you planning for medium to high production volumes?
- Do you require specific materials that MIM supports?
- Have you considered the initial mold costs and overall budget?
- Is high precision and quality a priority for your components?
- Have you identified a reliable MIM supplier?
By addressing these questions, you can make an informed decision about whether MIM aligns with your project goals. This checklist serves as a practical tool to guide you through the evaluation process, ensuring that you consider all relevant aspects before proceeding with MIM.
Starting a MIM Project
Initial Setup Considerations
Embarking on a Metal Injection Molding (MIM) project requires careful planning and preparation. You need to consider several key factors to ensure a successful start.
-
Design Evaluation: Begin by assessing your design’s complexity. MIM excels at producing intricate parts, so ensure your design takes full advantage of this capability. Consider integrating multiple components into a single piece to reduce assembly costs.
-
Material Selection: Choose the appropriate material for your project. MIM supports a variety of metals, including stainless steel, titanium, and copper. Each material offers unique properties, so select one that aligns with your project’s requirements.
-
Volume Assessment: Determine the production volume. MIM is most cost-effective for medium to high volumes. If your project involves large quantities, MIM can provide significant cost savings.
-
Prototype Testing: Before committing to full-scale production, consider creating prototypes. This step allows you to validate your design and make necessary adjustments. Fast prototyping services, such as DMLS metal 3D printing, can help you test your design efficiently.
-
Budget Planning: Evaluate the initial setup costs, including mold creation. While these costs can be high, the long-term savings in production make MIM a worthwhile investment for suitable projects.
Finding and Contacting Service Providers
Once you’ve considered the initial setup, the next step is finding the right service provider. Here are some tips to guide you:
-
Research Providers: Look for companies with expertise in MIM. Check their track record and client testimonials to gauge their reliability and quality of service.
-
Evaluate Capabilities: Ensure the provider can handle your specific material and design requirements. Some companies offer additional services like fast prototyping, which can be beneficial for testing your design.
-
Request Quotes: Contact multiple providers to get quotes. Compare their pricing, lead times, and additional services. This comparison helps you find the best fit for your project needs.
-
Discuss Your Project: Once you’ve shortlisted potential providers, discuss your project in detail. Share your design specifications, material preferences, and production volume. A good provider will offer insights and suggestions to optimize your project.
-
Contact Information: For more information on the MIM process, reach out to the engineering team of your chosen provider. They can offer guidance and support throughout your project.
By following these steps, you can set up your MIM project for success. Careful planning and choosing the right service provider are crucial to achieving high-quality results.
Metal Injection Molding (MIM) offers a compelling solution for projects requiring small to medium-sized parts with intricate geometries. You can achieve high precision and cost-effectiveness, especially for medium to high production volumes. Evaluate your project needs against MIM’s capabilities. Consider factors like design complexity, production volume, and material requirements. If MIM aligns with your goals, take the next steps by consulting with experienced service providers. This approach ensures you leverage MIM’s advantages, optimizing manufacturability and minimizing defects in your components.
If you have some projects about metal injection molding, or you don’t know how to choose the process, please contact us!