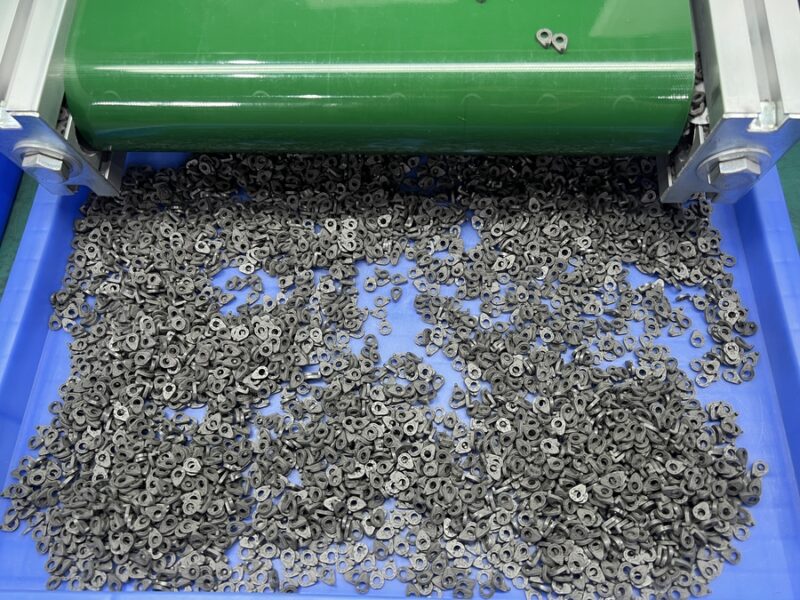
What are metal injection molding parts ?
Metal Injection Molding (MIM) is a manufacturing process that combines the design flexibility of plastic injection molding with the strength and durability of metal materials.
It is used to produce small, complex metal parts in high volumes.
Here are some key aspects of metal injection molding parts:
Characteristics:
- Small size: Typically fit in the palm of your hand, ranging from 0.05 to 100 grams
- Complex geometries: Can include overhangs, undercuts, threads, and other intricate features.
- High density: 94-97% of theoretical density, providing near-wrought properties.
- Excellent mechanical properties: Comparable to wrought or forged parts.
MIM parts common applications:
- Automotive: Sensor housings, gear synchronizers, fuel injectors, rivets, fasteners.
- Weapons: Sight mounts, safety levers, firing pins.
- Medical: Endoscopes, laparoscopic devices, implants, dental crowns.
- Consumer goods: Heat sinks, watch cases, buttons, switches, eyeglass frames.
A MIM tee pipe is a precisely manufactured, durable piping component created using the metal injection molding process.
A MIM tee pipe is a precisely manufactured, durable piping component created using the metal injection molding process.
Metal injection molding (MIM) enables the production of high-precision, complex transmission components with excellent strength and performance.
Metal injection molding (MIM) is used to produce laser transmitter components, offering high precision, complex geometries, and enhanced performance for advanced optical systems.
MIM needle entry components are precision-crafted parts for medical devices made using metal injection molding.
Metal injection molding (MIM) transmission is a process that combines metal powder and binders to form complex, high-precision transmission components.
A MIM charging gun handle is a durable, precisely manufactured component for electric vehicle chargers, created using metal injection molding.
MIM electric bicycle lock device is a high-precision, durable lock made using metal injection molding for enhanced security.
MIM oiling device parts are high-precision components for oiling systems made using metal injection molding.
MIM shift paddles are precision automotive components made using metal injection molding.
Metal injection molding (MIM) variable box lock block is a technique that produces high-strength, precision lock blocks for variable boxes using metal powders and binders.
Metal injection molding (MIM) zipper puller is a manufacturing process that creates durable and intricately designed zipper pullers using metal powder and binders.
MIM Factory tour (12)
Materials:
MIM can use a wide variety of metal alloys, including:
- Stainless steels (e.g., 17-4PH, 316, 420)
- Low alloy steels
- Superalloys (e.g., Inconel 625, Hastelloy X)
- Controlled expansion alloys
- Tungsten alloys
- Soft magnetic alloys
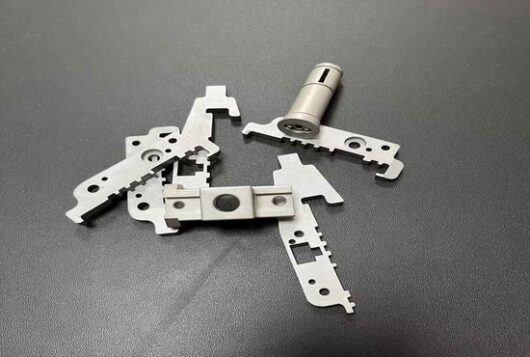

Advantages:
- High production volumes
- Low cost per part for complex geometries
- High dimensional accuracy and surface finish
- Ability to create very thin walls (< 100 micrometers)
Limitations:
- Best suited for large production batches
- Limited to relatively small parts
- High initial tooling investment.
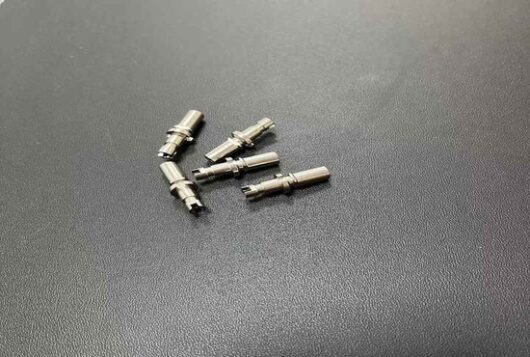
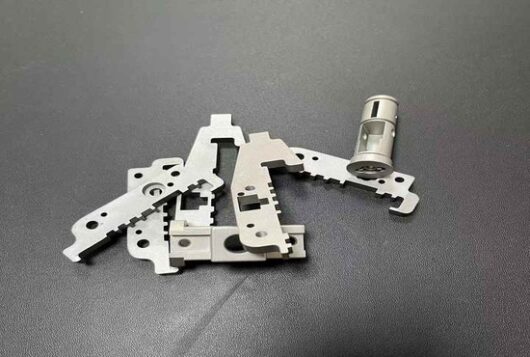
Design considerations:
- Uniform wall thickness is preferred
- Draft angles needed for easy part release
- Parting lines, gates, and ejector pin marks must be considered
- Cam actions may be needed for undercuts
Welcome to JHMIM – Your Trusted Partner for Metal Injection Molding (MIM) Solutions
At JHMIM, we specialize in providing high-quality metal injection molding (MIM) parts that meet the exacting standards of various industries. With our advanced technology and extensive experience, we deliver customized MIM solutions that address your unique needs.
Contact Us Today