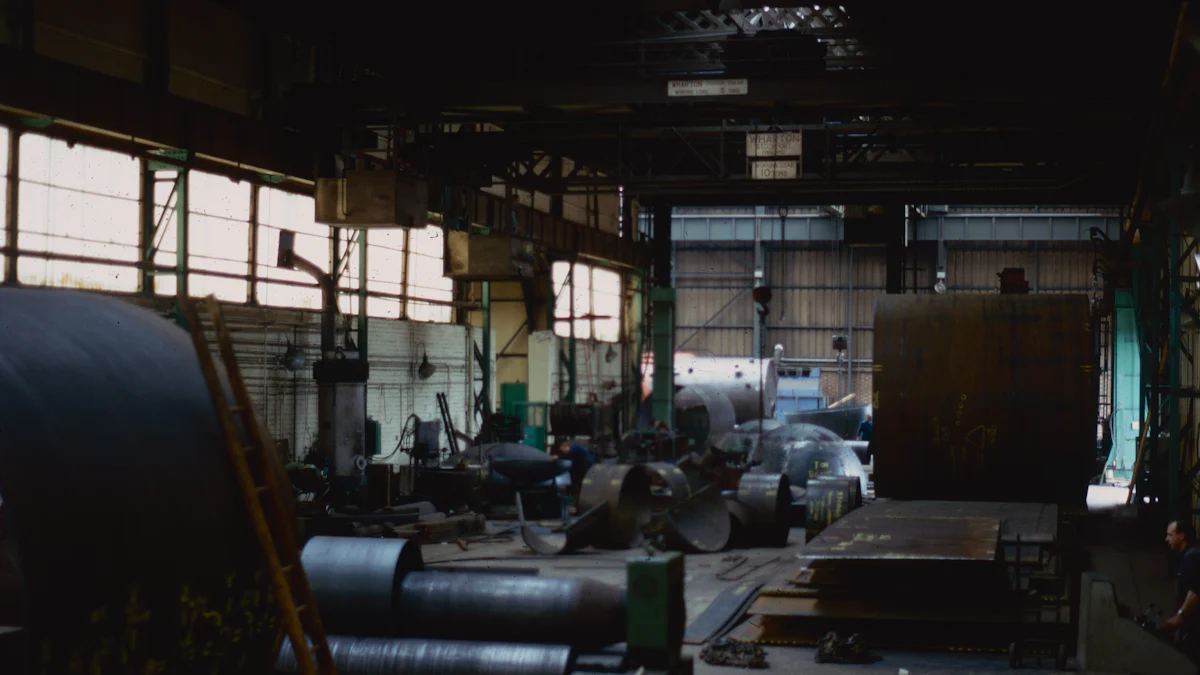
In the realm of metal injection molding, debinding in metal injection molding plays a pivotal role. It involves removing the binder from the molded part, transforming it into a porous structure known as the brown part. This step is crucial because it ensures that the metal particles remain intact while the binder is eliminated. The process not only affects the structural integrity but also influences the final quality of the product. By employing methods like thermal, solvent, or catalytic debinding, manufacturers can optimize the efficiency and effectiveness of this essential phase in metal injection molding.
Key Takeaways
- Debinding is essential for maintaining the structural integrity of molded parts, ensuring they retain their shape while removing binders.
- The quality of the final product is heavily influenced by effective debinding, which leads to uniform and defect-free components.
- Choosing the right debinding method—thermal, solvent, or catalytic—can optimize efficiency and reduce production costs.
- Common challenges in debinding include incomplete binder removal and part distortion, which can be mitigated through careful process control.
- Integrating debinding with the sintering process can streamline operations and enhance overall productivity.
- Utilizing advanced monitoring systems and eco-friendly solvents can improve the debinding process while minimizing environmental impact.
- Regular quality checks and optimized process parameters are crucial for achieving high-quality outcomes in metal injection molding.
Importance of Debinding in Metal Injection Molding
In the world of metal injection molding, debinding stands as a crucial phase. It ensures that the final product meets the desired standards of quality and performance. Let’s delve into why debinding holds such significance.
Ensuring Structural Integrity
I have found that maintaining structural integrity during debinding in metal injection molding is paramount. The process involves removing binders without compromising the geometry of the part. This step transforms the green part into a brown part, which retains its shape while allowing binders to escape during sintering. Successful debinding requires a delicate balance. Removing too much binder can damage the part, while insufficient removal can lead to defects. By carefully controlling the debinding process, I ensure that the parts remain structurally sound and ready for the next stage.
Impact on Final Product Quality
The quality of the final product heavily depends on effective debinding. When I execute debinding correctly, it results in a uniform and defect-free brown part. This uniformity is crucial because any inconsistencies can lead to flaws in the sintered product. The debinding process directly influences the density and mechanical strength of the final component. By optimizing debinding, I can enhance the overall quality, ensuring that the end product meets stringent industry standards.
Cost Implications of Effective Debinding
Effective debinding in metal injection molding also has significant cost implications. By minimizing defects and ensuring high-quality output, I reduce the need for rework and scrap. This efficiency translates into cost savings for manufacturers. Additionally, by selecting the appropriate debinding method—be it thermal, solvent, or catalytic—I can optimize energy consumption and reduce operational costs. The choice of method depends on the specific requirements of the part and the desired outcome. By carefully considering these factors, I can achieve cost-effective production without compromising quality.
Methods of Debinding in Metal Injection Molding
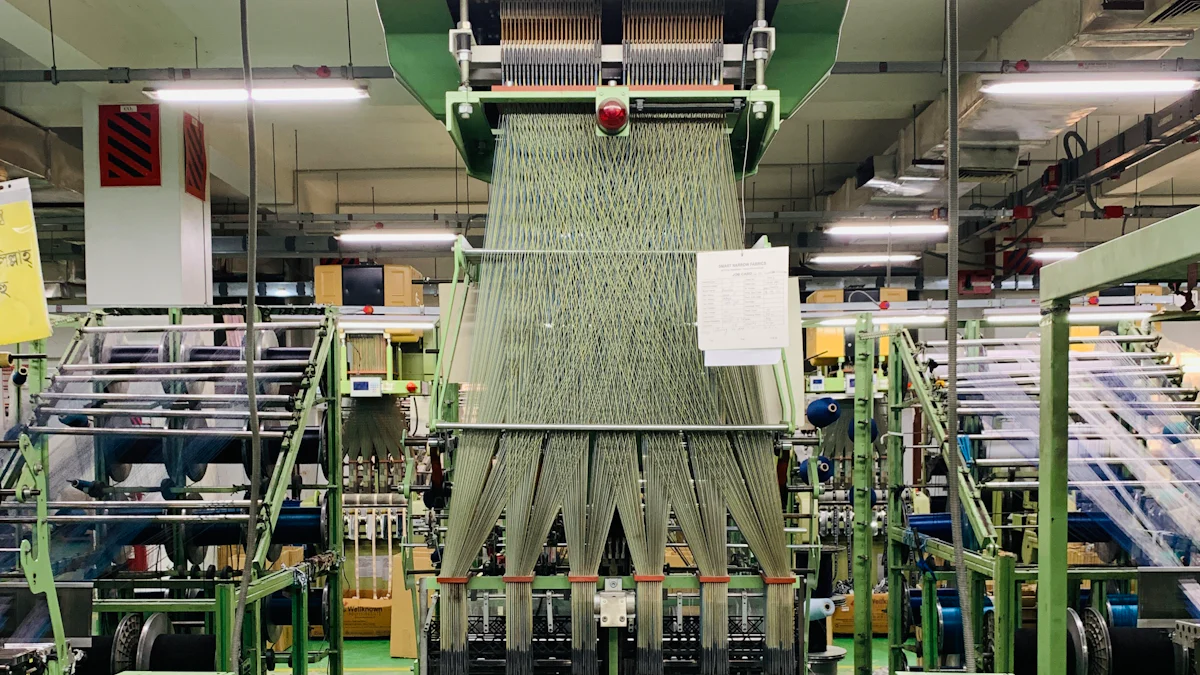
In the intricate process of metal injection molding, debinding plays a crucial role. I employ various methods to ensure the effective removal of binders, each with its unique advantages and challenges. Let’s explore these methods in detail.
Thermal Debinding
Process Overview
Thermal debinding involves heating the green part to elevated temperatures. This process gradually removes the binder material through evaporation or decomposition. I carefully control the temperature to prevent any damage to the part’s structure. The process requires precise temperature management to ensure that the binder is removed without affecting the metal particles.
Advantages and Disadvantages
Thermal debinding offers several advantages. It provides a uniform removal of binders, which is essential for maintaining the part’s integrity. Additionally, it does not require any chemical solvents, making it an environmentally friendly option. However, the process can be time-consuming and energy-intensive. The need for precise temperature control also adds complexity to the operation.
Solvent Debinding
Process Overview
Solvent debinding involves immersing the green part in a suitable solvent. This method dissolves the binder material, allowing it to be washed away. I select the solvent based on the binder’s chemical composition to ensure effective removal. The process requires careful handling of solvents to prevent any adverse effects on the part.
Advantages and Disadvantages
Solvent debinding offers a faster binder removal compared to thermal methods. It allows for selective removal of specific binder components, providing flexibility in the process. However, the use of chemical solvents poses environmental and safety concerns. Proper disposal and handling of solvents are crucial to minimize any negative impact.
Catalytic Debinding
Process Overview
Catalytic debinding involves a solid-to-vapor catalytic degradation process. I use a catalyst to accelerate the breakdown of the binder material. This method allows for efficient removal of binders without the need for high temperatures or solvents. The process requires precise control of the catalytic reaction to ensure complete binder removal.
Advantages and Disadvantages
Catalytic debinding offers several benefits. It provides a rapid and efficient binder removal process, reducing the overall cycle time. The method also minimizes the risk of part distortion due to lower processing temperatures. However, the need for specific catalysts and controlled reaction conditions adds complexity to the process. The cost of catalysts can also be a consideration for manufacturers.
By understanding these methods, I can optimize the debinding process in metal injection molding. Each method offers unique benefits and challenges, allowing me to tailor the process to meet specific production requirements.
Challenges in the Debinding Process
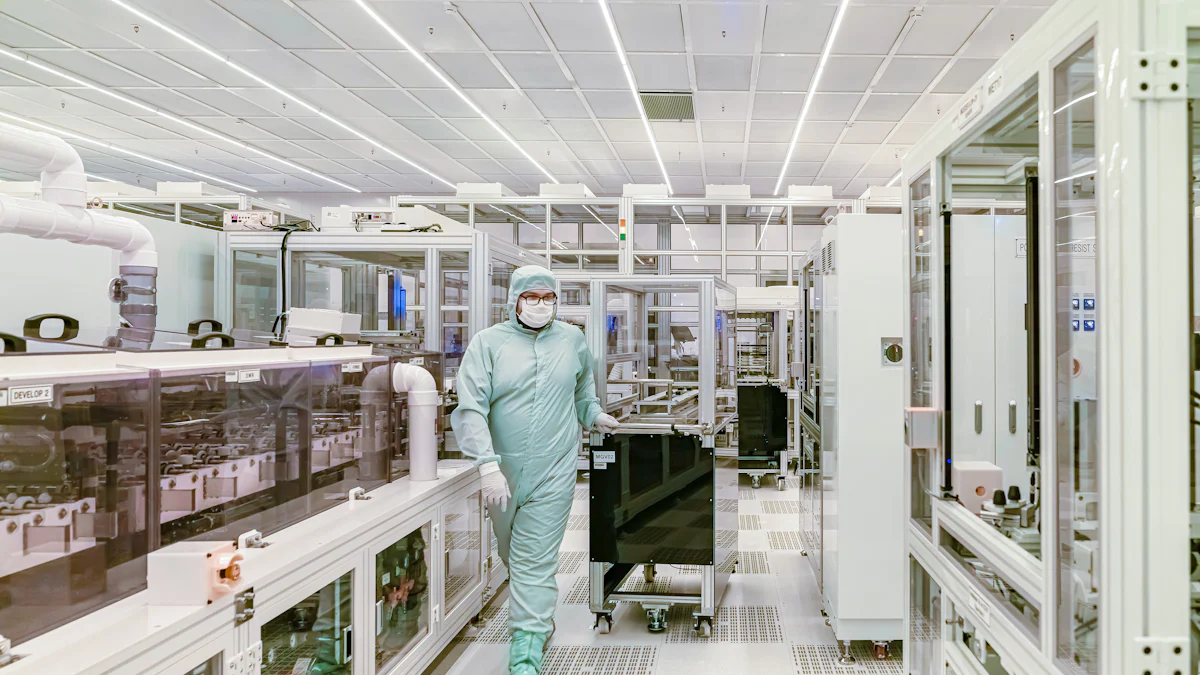
In the intricate world of metal injection molding, the debinding process presents several challenges. As I navigate through this critical phase, I encounter common issues that require careful attention and strategic solutions.
Common Issues Faced
-
Incomplete Binder Removal: One of the most prevalent challenges is ensuring complete binder removal. The binder supports the metal powder in the green part, and any residue can compromise the sintering process. This residue can prevent the formation of a dense, defect-free structure, leading to inferior product quality.
-
Part Distortion: During debinding, maintaining the geometry of the part is crucial. The removal of binders can lead to distortion if not managed properly. This issue often arises when the process lacks precise control, resulting in parts that do not meet dimensional specifications.
-
Time-Consuming Process: As noted by Chartier et al., the debinding stage is often the most time-consuming step in metal injection molding. The need for gradual and controlled binder removal extends the production timeline, impacting overall efficiency.
-
Defect Introduction: The risk of introducing defects during debinding is significant. These defects can manifest as cracks, voids, or surface irregularities, which affect the final product’s performance and appearance.
Solutions and Best Practices
To address these challenges, I employ a series of best practices and solutions that enhance the debinding process:
-
Optimized Process Parameters: I meticulously control temperature, time, and atmosphere conditions to ensure complete binder removal without compromising part integrity. This approach minimizes the risk of defects and distortion.
-
Selection of Appropriate Debinding Method: Choosing the right debinding method—thermal, solvent, or catalytic—is crucial. Each method offers unique advantages, and I select based on the specific requirements of the part and desired outcomes. For instance, thermal debinding, as highlighted by experts, provides smooth binder removal and is easier to control compared to other methods.
-
Integration of Debinding and Sintering: By integrating debinding with the sintering process, I streamline operations and reduce cycle time. This integration allows for a seamless transition from the brown part to the final sintered product, enhancing overall efficiency.
-
Regular Monitoring and Quality Checks: Continuous monitoring of the debinding process ensures early detection of potential issues. I implement regular quality checks to verify that parts meet the required standards before proceeding to the next stage.
By implementing these solutions and best practices, I overcome the challenges associated with debinding in metal injection molding. This proactive approach not only improves product quality but also enhances operational efficiency, ultimately leading to successful manufacturing outcomes.
Optimizing the Debinding Process
In the realm of metal injection molding, optimizing the debinding process is crucial for enhancing efficiency and product quality. Through careful analysis and the adoption of innovative techniques, I can significantly improve the outcomes of this critical phase.
Tips for Improving Efficiency
To boost the efficiency of the debinding process, I focus on several key strategies:
-
Precise Temperature Control: I meticulously manage the debinding temperature to ensure optimal binder removal. By analyzing the kinetics of thermal debinding, I can determine the ideal temperature settings. This approach minimizes energy consumption and reduces processing time.
-
Optimized Debinding Time: I adjust the debinding time based on the specific requirements of each part. By conducting kinetic analysis, I identify the optimal duration for binder removal. This method prevents over-processing and maintains part integrity.
-
Controlled Heating Rate: I carefully regulate the heating rate during thermal debinding. A gradual increase in temperature allows for uniform binder removal. This technique reduces the risk of part distortion and enhances overall efficiency.
-
Selection of Appropriate Method: I choose the most suitable debinding method—thermal, solvent, or catalytic—based on the part’s characteristics. Catalytic debinding, for instance, offers faster binder removal and higher handling strength compared to thermal methods.
-
Integration with Sintering: By integrating debinding with the sintering process, I streamline operations. This integration reduces cycle time and improves overall productivity.
Innovations and Technological Advances
The field of metal injection molding continually evolves, with new technologies enhancing the debinding process. Here are some innovations I incorporate:
-
Advanced Kinetic Analysis Tools: I utilize sophisticated tools for kinetic analysis. These tools provide insights into the optimal parameters for thermal debinding. They offer a theoretical basis for process optimization.
-
Automated Monitoring Systems: I implement automated systems to monitor the debinding process. These systems provide real-time data on temperature, time, and atmosphere conditions. They enable precise control and early detection of potential issues.
-
Environmentally Friendly Solvents: In solvent debinding, I explore the use of eco-friendly solvents. These alternatives reduce environmental impact and enhance safety. They offer a sustainable solution for binder removal.
-
Innovative Catalysts: For catalytic debinding, I experiment with new catalysts. These catalysts accelerate the degradation process, reducing cycle time. They also improve the efficiency of binder removal.
By adopting these tips and innovations, I optimize the debinding process in metal injection molding. This proactive approach not only enhances efficiency but also ensures high-quality outcomes.
In the intricate process of metal injection molding, debinding plays a pivotal role. It ensures the removal of binders, transforming the green part into a structurally sound brown part. I explored key methods like thermal, solvent, and catalytic debinding, each with unique advantages and challenges. Effective debinding is crucial for achieving high-quality final products. To optimize this process, I recommend precise temperature control, selecting the appropriate method, and integrating debinding with sintering. These strategies enhance efficiency and product quality, ensuring successful outcomes in metal injection molding.
FAQ
What is the debinding process commonly referred to as in Metal Injection Molding (MIM)?
In the realm of Metal Injection Molding, the debinding process is simply known as debinding. It involves extracting the binder from a molded part, transforming it into a porous structure known as the brown part.
What are the debinding methods employed in Metal Injection Molding (MIM)?
In MIM, I employ several debinding methods to ensure effective binder removal. These include thermal debinding, catalytic debinding, solvent debinding, and supercritical fluid debinding. Each method offers unique advantages and challenges, allowing me to tailor the process to specific production needs.
What is the debinding process typically employed in the production of metal and ceramic components?
The debinding process is crucial in producing metal and ceramic components. I utilize techniques such as metal injection molding (MIM), ceramic injection molding (CIM), and powder compacting to achieve high-quality results.
What is the primary difference between metal injection molding and plastic injection molding in terms of post-processing?
The main difference lies in the post-processing requirements. In plastic injection molding, parts are nearly complete when ejected from the mold. However, in metal injection molding, parts require additional steps like debinding and sintering to achieve the desired properties and quality.
How does thermal debinding differ from solvent debinding?
Thermal debinding involves heating the green part to remove binders through evaporation or decomposition. It requires precise temperature control. Solvent debinding, on the other hand, uses a chemical solvent to dissolve and wash away the binder. Each method has its own set of advantages and challenges, which I consider when selecting the appropriate approach.
Why is debinding considered a critical step in metal injection molding?
Debinding is critical because it ensures the removal of binders without compromising the part’s geometry. This step transforms the green part into a structurally sound brown part, ready for sintering. Effective debinding directly impacts the final product’s quality, density, and mechanical strength.
Can debinding affect the cost of metal injection molding?
Yes, debinding can significantly impact costs. By minimizing defects and ensuring high-quality output, I reduce the need for rework and scrap, leading to cost savings. Additionally, selecting the appropriate debinding method helps optimize energy consumption and operational costs.
What challenges might I face during the debinding process?
Common challenges include incomplete binder removal, part distortion, and the introduction of defects. These issues require careful attention and strategic solutions to ensure successful outcomes in metal injection molding.
How can I optimize the debinding process?
To optimize debinding, I focus on precise temperature control, selecting the appropriate method, and integrating debinding with sintering. I also explore innovations like advanced kinetic analysis tools and environmentally friendly solvents to enhance efficiency and product quality.