What is the powdered metal process? The powdered metal process is a groundbreaking manufacturing technique that transforms metal powders into solid components through compaction and sintering. This innovative method ensures precision and consistency, making it essential for industries that demand intricate designs and high-quality parts. Its efficiency significantly reduces material waste, providing a cost-effective solution for large-scale production. Additionally, the process supports sustainability goals by recycling unused powders and minimizing environmental impact. With ongoing technological advancements, the powdered metal process continues to revolutionize modern production standards, seamlessly combining innovation with practicality.
Key Takeaways
- The powdered metal process transforms metal powders into solid components through compaction and sintering, ensuring high precision and minimal waste.
- This manufacturing method is cost-effective, especially for high-volume production, as it reduces material waste and eliminates extensive machining.
- Powdered metal technology supports sustainability by recycling unused powders and consuming less energy than traditional manufacturing methods.
- Industries such as automotive, aerospace, and medical benefit from the ability to create intricate designs and durable components tailored to specific needs.
- Secondary operations like machining and heat treatment enhance the properties of powdered metal components, ensuring they meet stringent quality standards.
- The process allows for high customization, making it ideal for producing patient-specific medical implants and advanced aerospace parts.
- As a versatile and eco-friendly manufacturing technique, the powdered metal process is revolutionizing modern production across various sectors.
How does the powdered metal process work?
The powdered metal process transforms raw metal powders into durable and precise components.
Powder creation
The journey begins with the production of metal powders. Manufacturers use various methods to achieve this, each tailored to specific material requirements.
Methods of powder production (e.g., atomization, reduction, electrolysis)
- Atomization: This method involves breaking molten metal into fine droplets using high-pressure gas or water. Once cooled, these droplets solidify into powder.
- Reduction: In this process, metal oxides are reduced using a chemical reaction, leaving behind pure metal powder.
Electrolysis produces metal powders by depositing metal ions onto a cathode in an electrolytic cell.
Each method offers unique advantages, allowing manufacturers to select the most suitable approach based on the desired properties of the final product.
Characteristics of metal powders (e.g., particle size, shape, and composition)
The quality of the metal powder significantly impacts the final component. Key characteristics include:
- Particle size: Smaller particles enhance compactness and uniformity.
- Shape: Spherical powders flow better during compaction, while irregular shapes may improve bonding during sintering.
- Composition: The choice of metal or alloy determines the strength, durability, and other properties of the finished part.
Compaction
Once the metal powder is ready, the next step involves shaping it into a desired form.
Explanation of pressing metal powders into molds
Compaction compresses the metal powder into a mold, creating a “green” part. This green part holds its shape but lacks the strength of the final product. High pressure ensures the particles bond together, forming a dense and uniform structure.
Tools and equipment used in compaction
Specialized tools and equipment play a crucial role in this stage:
- Presses: Hydraulic or mechanical presses apply the necessary force to compact the powder.
- Dies and molds: These tools define the shape and dimensions of the component, ensuring precision.
Sintering
Sintering transforms the compacted powder into a solid, robust component through heat treatment.
Overview of the sintering process and its purpose
During sintering, the green part is heated to a temperature below its melting point. This process fuses the particles, enhancing strength and durability. Sintering eliminates voids and improves the part’s structural integrity.
Temperature and time considerations in sintering
The sintering temperature and duration depend on the material and desired properties. For instance:
- Temperature: Higher temperatures promote better bonding but may risk distortion.
- Time: Prolonged sintering ensures uniformity but increases production time.
Manufacturers achieve optimal results by carefully controlling these factors, and producing components that meet stringent quality standards.
Secondary operations
Secondary operations refine and enhance components created through the powdered metal process. These additional steps ensure the final product meets specific performance and aesthetic requirements.
Additional processes like machining, heat treatment, or coating
After sintering, components often undergo secondary processes to achieve desired properties or finishes. These operations include:
- Machining: This process removes excess material or fine-tunes dimensions. It ensures precise tolerances and smooth surfaces. For example, I have seen manufacturers use CNC machines to create intricate details on sintered parts.
- Heat treatment: Heat treatment alters the microstructure of the material. It improves hardness, strength, or wear resistance. For instance, carburizing or quenching enhances the durability of gears and bearings.
- Coating: Coatings protect components from corrosion or wear. Techniques like electroplating or powder coating add a protective layer. These coatings also improve the appearance of the final product.
Each of these processes tailors the component to its intended application, ensuring it performs optimally in real-world conditions.
Enhancing the final product’s properties
Secondary operations significantly enhance the properties of powdered metal components. These improvements include:
- Increased durability: Heat treatment strengthens the material, making it more resistant to stress and wear.
- Improved precision: Machining ensures components meet exact specifications, which is crucial for industries like aerospace and automotive.
- Enhanced functionality: Coatings provide additional features, such as resistance to rust or improved conductivity.
“The powder metallurgy process involves four fundamental stages: powder preparation, blending and mixing, compacting, and sintering.” However, secondary operations play a pivotal role in elevating the quality and functionality of the final product.
By incorporating these additional processes, manufacturers can produce components that not only meet but exceed industry standards.
What are the benefits of the powdered metal process?
The powdered metal process offers numerous advantages that make it a preferred choice in modern manufacturing.
Cost efficiency
Reduced material waste compared to traditional methods
I have observed that traditional manufacturing methods, like machining, often result in significant material waste. In contrast, the powdered metal process minimizes waste by using only the required amount of material. The compacting and sintering stages ensure that nearly all the metal powder contributes to the final product. This efficiency not only reduces costs but also aligns with sustainability goals.
Lower production costs for high-volume manufacturing
When producing components in large quantities, the powdered metal process becomes highly economical. The ability to create near-net shapes eliminates the need for extensive secondary machining, saving both time and resources. Additionally, specialized equipment, such as high-pressure die-casting machines and sintering furnaces, streamlines production, further reducing costs. Manufacturers can achieve consistent quality without incurring excessive expenses, making this process ideal for industries like automotive and aerospace.
Material Conservation
Efficient use of raw materials
The powdered metal process ensures optimal use of raw materials. By compacting metal powders into precise molds, manufacturers avoid the excess material typically removed during machining. This method maximizes the utility of every particle, resulting in efficient resource utilization. For example, I have seen how powder blending and mixing systems allow manufacturers to tailor material compositions, ensuring that no resources go to waste.
Recycling potential of unused powders
Unused metal powders from the process can be collected and reused, further enhancing material conservation. This recycling capability reduces the need for new raw materials, lowering production costs and environmental impact. Companies specializing in powder handling and control automation provide advanced systems to recover and reuse powders efficiently. This approach not only conserves resources but also supports eco-friendly manufacturing practices.
Precision and complexity
Ability to create intricate shapes and designs
The powdered metal process excels in producing complex and intricate designs that would be challenging with traditional methods. The use of specialized molds and dies allows manufacturers to create components with detailed geometries and tight tolerances. For instance, I have seen how this process enables the production of gears with precise tooth profiles, ensuring optimal performance in mechanical systems.
Consistency in part quality and dimensions
Consistency is a hallmark of the powdered metal process. Each component undergoes the same compacting and sintering procedures, resulting in uniform quality and dimensions. Advanced equipment, such as robotics and laboratory testing systems, ensures that every part meets stringent industry standards. This reliability makes the process suitable for applications where precision is critical, such as in medical implants or aerospace components.
“The powdered metal process combines efficiency, precision, and sustainability, making it a cornerstone of modern manufacturing.”
By leveraging these benefits, manufacturers can produce high-quality components while minimizing costs and environmental impact. The powdered metal process continues to set new benchmarks in efficiency and innovation.
Environmental benefits
The powdered metal process stands out as an environmentally friendly manufacturing technique. Its ability to conserve energy and reduce emissions makes it a preferred choice for industries aiming to minimize their ecological impact.
Reduced energy consumption
I have observed that the powdered metal process requires significantly less energy compared to traditional manufacturing methods. Processes like machining or casting often involve extensive material removal or high-temperature melting, which consumes vast amounts of energy. In contrast, powder metallurgy operates at lower temperatures during sintering and uses near-net shaping techniques. This approach eliminates the need for excessive machining, reducing energy demands.
Specialized equipment, such as high-temperature sintering furnaces, optimizes energy usage by maintaining precise temperature control. These furnaces ensure efficient heat distribution, minimizing energy waste. Additionally, advanced technologies in powder blending and mixing systems streamline the preparation phase, further conserving energy. By integrating these innovations, manufacturers achieve energy-efficient production without compromising quality.
Lower carbon footprint compared to other manufacturing methods
The powdered metal process contributes to a lower carbon footprint, aligning with global sustainability goals. Traditional methods often generate substantial greenhouse gas emissions due to energy-intensive operations and material waste. Powder metallurgy, however, minimizes waste by utilizing nearly all the metal powder during compaction and sintering. This efficiency reduces the need for raw material extraction, which is a major source of carbon emissions.
Moreover, the ability to recycle unused powders enhances the process’s eco-friendliness. Companies specializing in powder handling and control automation provide systems that recover and reuse leftover powders, ensuring minimal environmental impact. By adopting these practices, manufacturers not only reduce emissions but also promote a circular economy.
“Powder metallurgy combines precision, efficiency, and sustainability, making it a cornerstone of eco-conscious manufacturing.”
The environmental benefits of the powdered metal process extend beyond energy savings and emission reductions. It represents a shift toward responsible production, where innovation meets environmental stewardship. As industries continue to prioritize sustainability, this process will play a pivotal role in shaping a greener future.
Applications of the powdered metal process
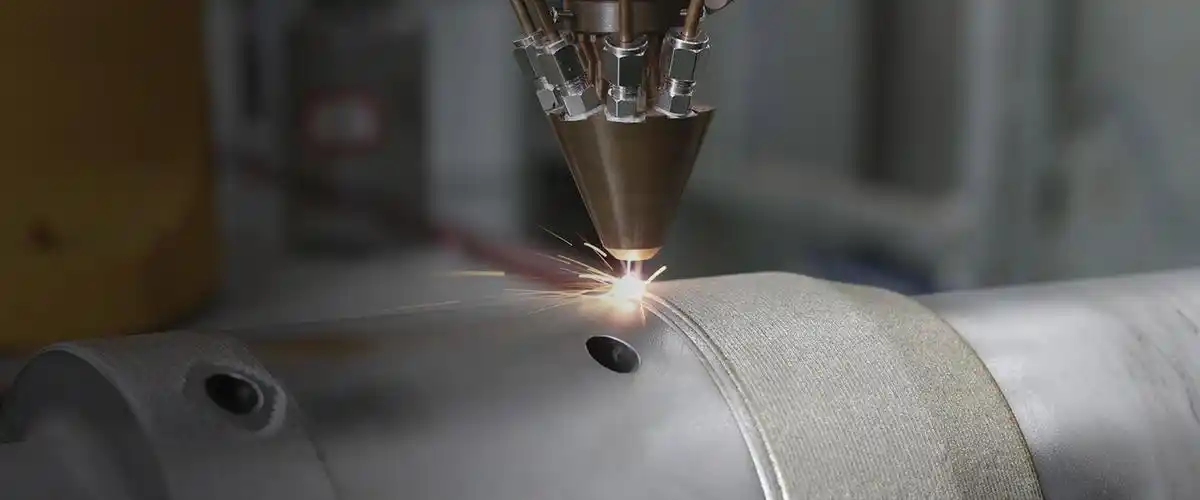
Its ability to produce precise, durable, and cost-effective components makes it indispensable in sectors like automotive, aerospace, medical, and consumer goods. Let’s explore its applications in detail.
Automotive industry
The automotive sector relies heavily on powdered metal technology to meet its demand for high-performance and lightweight components.
Production of gears, bearings, and engine components
I have seen how powdered metal technology revolutionizes the production of critical automotive parts. Manufacturers use this process to create gears, bearings, and engine components with exceptional precision. The ability to form these parts directly from molds ensures minimal material waste. Unlike traditional machining, which removes material in bulk, powdered metal processing uses only what is necessary. This efficiency not only reduces costs but also supports sustainable manufacturing practices.
Benefits for lightweight and durable parts
Automotive manufacturers prioritize lightweight materials to improve fuel efficiency and reduce emissions. Powdered metal components meet this need by offering a perfect balance of strength and weight. For example, I have observed how powdered metal gears maintain durability while being significantly lighter than their machined counterparts. This advantage enhances vehicle performance without compromising safety or reliability.
“Powdered metal parts provide the automotive industry with a unique combination of precision, durability, and sustainability.”
Aerospace industry
The aerospace industry demands components that can withstand extreme conditions while maintaining high performance. Powdered metal technology excels in meeting these stringent requirements.
High-performance components for aircraft and spacecraft
In aerospace applications, powdered metal parts deliver unmatched performance. I have noticed how manufacturers use this process to produce turbine blades, structural components, and fasteners for aircraft and spacecraft. The sintering process ensures these parts achieve the necessary strength and resistance to wear. This reliability is crucial for ensuring safety and efficiency in aerospace operations.
Use of advanced materials like titanium alloys
Powdered metal technology enables the use of advanced materials, such as titanium alloys, which are essential in aerospace engineering. Titanium alloys offer excellent strength-to-weight ratios and corrosion resistance. By leveraging powdered metal processes, manufacturers can create intricate designs with these materials, which would be challenging to achieve through traditional methods. This capability allows for the production of lightweight yet robust components, reducing overall aircraft weight and improving fuel efficiency.
“The powdered metal process plays a pivotal role in advancing aerospace innovation by enabling the use of cutting-edge materials and designs.”
Medical field
The medical field benefits greatly from the precision and customization offered by powdered metal technology. This process supports the creation of tools and implants that meet the highest standards of quality and performance.
Creation of surgical tools and implants
I have observed how powdered metal technology facilitates the production of surgical tools and implants with exceptional accuracy. Surgeons rely on tools that are not only durable but also ergonomically designed. Powdered metal processes ensure these tools meet these requirements. Additionally, implants such as joint replacements and dental fixtures benefit from the process’s ability to produce biocompatible materials with precise dimensions.
Customization for patient-specific needs
One of the most remarkable advantages of powdered metal technology in the medical field is its ability to create patient-specific solutions. For instance, I have seen how manufacturers use this process to produce custom implants tailored to an individual’s anatomy. This level of customization improves patient outcomes and reduces recovery times. The process also supports the integration of advanced materials, such as cobalt-chromium alloys, which enhance the durability and functionality of medical devices.
“Powdered metal technology empowers the medical field to deliver innovative solutions that improve patient care and outcomes.”
The versatility of the powdered metal process continues to drive advancements across industries. Its ability to produce high-quality, efficient, and sustainable components ensures its relevance in meeting the evolving demands of modern manufacturing.
Consumer goods
The powdered metal process has become a game-changer in the production of consumer goods. Its ability to create precise, durable, and cost-effective components makes it an ideal choice for manufacturing tools, electronics, and appliances.
Manufacturing of tools, electronics, and appliances
I have seen how powdered metal technology revolutionizes the production of everyday items. Manufacturers use this process to create components for tools, such as drill bits and cutting blades, that require exceptional strength and wear resistance. The sintering stage ensures these parts achieve the necessary durability to withstand repeated use.
In electronics, powdered metal components play a critical role in devices like smartphones, laptops, and gaming consoles. For instance, I have observed how manufacturers produce intricate connectors and heat sinks using this method. These parts ensure efficient performance and longevity, which are essential for modern electronic devices.
Appliances also benefit significantly from powdered metal technology. Components like motor parts, gears, and housings are produced with high precision, ensuring smooth operation and reliability. The ability to form these parts directly from molds reduces material waste and enhances production efficiency.
“Powdered metal processing allows manufacturers to meet the growing demand for high-quality consumer goods while maintaining cost-effectiveness and sustainability.”
Cost-effective production of small, complex parts
The powdered metal process excels in creating small, intricate components that would be challenging or expensive to produce using traditional methods. I have noticed how this technology enables manufacturers to achieve near-net shapes, minimizing the need for extensive machining. This efficiency not only reduces production costs but also shortens lead times.
For example, I have seen how manufacturers use powdered metal to produce tiny gears for watches and precision parts for cameras. These components require tight tolerances and consistent quality, which the powdered metal process delivers effortlessly. Unlike machining, which often involves removing material in bulk, this method forms parts directly from molds, resulting in minimal waste.
Additionally, the scalability of the powdered metal process makes it ideal for high-volume production. Manufacturers can produce thousands of identical parts with consistent quality, meeting the demands of industries that rely on mass production. This capability ensures that consumer goods remain affordable without compromising on performance or durability.
“By leveraging the powdered metal process, manufacturers can create complex, high-quality components at a fraction of the cost, making it a cornerstone of modern consumer goods production.”
The powdered metal process continues to drive innovation in the consumer goods sector. Its ability to balance precision, efficiency, and cost-effectiveness ensures its relevance in meeting the evolving needs of consumers worldwide.
The powdered metal process stands out as a versatile and efficient manufacturing method. It transforms raw metal powders into precise, durable components while minimizing waste and conserving resources. This process offers significant benefits, including cost savings, material efficiency, and the ability to create intricate designs with consistency. Its applications span industries such as automotive, aerospace, medical, and consumer goods, showcasing its adaptability and value. As sustainability becomes a priority, this eco-friendly process continues to lead innovation in manufacturing. I encourage you to explore its potential further or reach out with any questions.
FAQ
What is the powdered metal process?
The powdered metal process involves transforming metal powders into solid components through compaction and sintering.
How are metal powders created?
Metal powders are produced using methods such as atomization, reduction, and electrolysis. Atomization breaks molten metal into fine droplets, reduction uses chemical reactions to extract pure metal, and electrolysis deposits metal ions onto a cathode. Each method offers unique advantages depending on the desired properties of the final product.
What materials are commonly used in the powdered metal process?
Manufacturers often use materials like stainless steel, brass, copper, iron, and bronze. These metals can be blended with other alloys to achieve specific mechanical properties. For example, titanium alloys are popular in aerospace applications due to their strength and lightweight nature.
What industries benefit from powdered metal components?
The powdered metal process serves a wide range of industries, including:
- Automotive: Gears, bearings, and engine components.
- Aerospace: Turbine blades and structural parts.
- Medical: Surgical tools and implants.
- Consumer goods: Electronics, appliances, and tools.
Its versatility makes it indispensable for both high-performance and everyday applications.
Why is the powdered metal process considered sustainable?
This process minimizes material waste by using only the required amount of metal powder. Unused powders can be recycled, reducing the need for new raw materials. Additionally, it consumes less energy compared to traditional manufacturing methods, lowering its carbon footprint.
Can powdered metal parts be customized?
Yes, powdered metal parts offer high customization. Manufacturers can tailor material compositions and designs to meet specific requirements. For instance, medical implants can be customized for individual patients, while aerospace components can be optimized for extreme conditions.
What are the advantages of sintering in this process?
Sintering fuses compacted metal powders into solid components using heat. This step enhances the strength, durability, and structural integrity of the parts. It also eliminates voids, ensuring the final product meets stringent quality standards.
Are powdered metal components durable?
Powdered metal components are highly durable. The process allows for the creation of high-strength parts that can withstand wear and stress. For example, powdered metal brake pads and gears in the automotive industry demonstrate exceptional performance under demanding conditions.
How does the powdered metal process reduce costs?
This process reduces costs by minimizing material waste and eliminating extensive machining. It is particularly cost-effective for high-volume production, as it allows manufacturers to produce near-net shapes with consistent quality.
What are some unique applications of powdered metal technology?
Powdered metal technology is used for both common and specialized applications. Examples include:
- Heat shields for spacecraft re-entry.
- Electrical contacts for high-current flows.
- Gas filters for industrial use.
- Everyday items like light bulb filaments and lubricant-infiltrated bearings.
Its adaptability ensures it meets diverse manufacturing needs across industries.