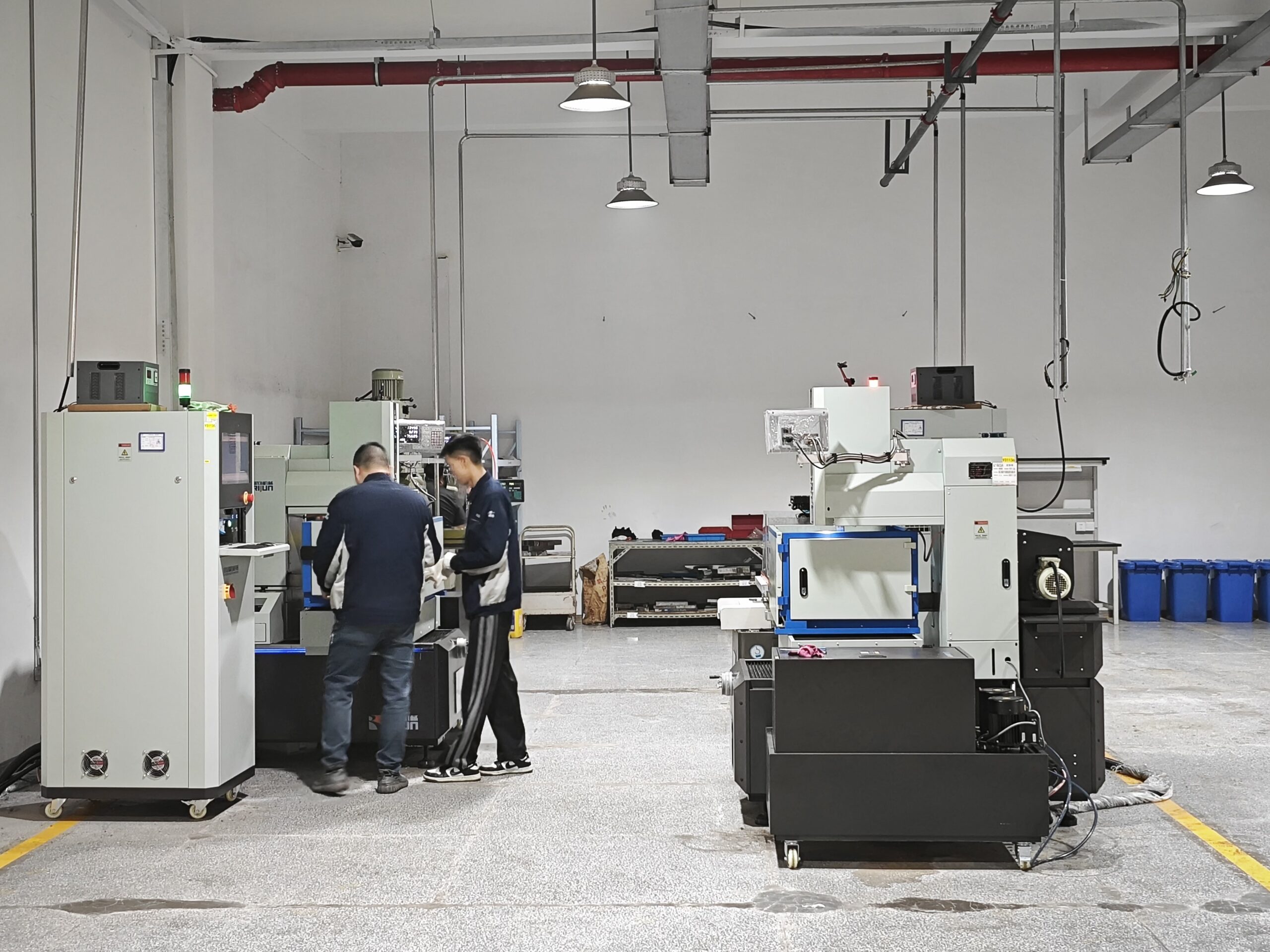
Metal injection molding (MIM) stands as a pivotal technique in modern manufacturing, offering a blend of precision and efficiency. The central question arises: How can efficiency be maximized in metal injection molding? Efficiency in MIM not only enhances production outcomes but also significantly impacts the industry by reducing costs and waste. The market for MIM is expanding rapidly, with projections indicating growth from
4.6billionin2024to4.6 billion in 2024 to
9.5 billion by 2033. This growth underscores the importance of designing for metal injection molding, which ensures optimal material usage and superior product quality. Enhanced efficiency in MIM promises to revolutionize various sectors, including automotive and electronics, by meeting the increasing demand for complex, miniaturized components.
Benefits of Metal Injection Molding
Cost-Effectiveness
Metal injection molding (MIM) is a cost-effective solution in the manufacturing industry. By utilizing powdered metals mixed with a plastic binder, MIM minimizes material waste. This process allows manufacturers to reuse feedstock, significantly reducing production expenses. Unlike traditional machining, which often requires extensive post-processing, MIM produces components with high precision and complex geometries without additional operations. This efficiency translates into lower costs for secondary operations and a faster production rate. For projects demanding high volume and complexity, MIM proves to be the most economical choice.
Precision and Complexity
MIM excels in producing intricate parts with exceptional precision. The process enables the creation of complex geometries that are challenging to achieve through other metalworking methods like casting or forging. Manufacturers can produce small, high-precision components consistently, meeting tight tolerances and high-performance requirements. This capability makes MIM ideal for industries such as automotive and electronics, where precision and complexity are paramount. The ability to maintain consistency across medium to large production volumes further enhances its appeal.
Versatility
The versatility of MIM lies in its ability to work with a wide range of materials. This flexibility allows manufacturers to tailor the properties of the final product to meet specific application needs. Whether it’s strength, corrosion resistance, or thermal conductivity, MIM can accommodate various material requirements. Additionally, the process supports the production of parts with varying wall thicknesses, ensuring the integrity of the final product. This adaptability makes MIM a preferred choice for diverse applications, from medical devices to consumer electronics. By minimizing material waste and offering design flexibility, MIM contributes to sustainable manufacturing practices.
Comparing MIM with Other Manufacturing Processes
MIM vs. Traditional Casting
Metal Injection Molding (MIM) and traditional casting both serve the purpose of shaping metal parts, yet they differ significantly in their processes and outcomes.
Moreover, MIM generates less material waste compared to casting. The ability to reuse feedstock in MIM contributes to its cost-effectiveness, especially for small to medium-sized parts. Traditional casting, on the other hand, often requires additional machining and finishing processes, increasing both time and cost. For industries requiring high-volume production with complex designs, MIM offers a more efficient and economical solution.
MIM vs. CNC Machining
CNC machining and MIM both produce high-precision components, but they cater to different needs. CNC machining involves subtractive manufacturing, where material is removed from a solid block to create the desired shape. This method can be time-consuming and material-intensive, especially for complex parts. MIM, however, forms parts directly from metal powder, minimizing waste and reducing the need for post-processing.
The ability to produce consistent, high-quality components makes MIM a preferred choice for industries like automotive and electronics, where precision and efficiency are paramount.
MIM vs. Additive Manufacturing
Additive manufacturing, commonly known as 3D printing, and MIM both allow for the creation of complex parts, yet they differ in scalability and material properties. Additive manufacturing builds parts layer by layer, offering unparalleled design freedom. However, it often falls short in terms of material strength and production speed for large volumes.
MIM, on the other hand, excels in producing durable parts with intricate geometries suitable for high-volume manufacturing. The process ensures close tolerances and consistent quality, which additive manufacturing may struggle to maintain at scale. While 3D printing is ideal for rapid prototyping and custom, low-volume production, MIM provides a cost-effective solution for producing high-precision components in large quantities. This makes MIM particularly advantageous for industries that demand both complexity and consistency in their products.
Strategies for Maximizing Efficiency in MIM
Selecting the Right Materials
Material selection plays a pivotal role in metal injection molding (MIM). The choice of materials directly influences the final product’s properties, such as strength, hardness, and corrosion resistance. Manufacturers can choose from a wide range of metal powders and alloys, allowing them to tailor the material properties to meet specific application needs. Collaborating with an expert in MIM ensures optimal material choices, enhancing the overall efficiency of the process. By selecting the right materials, manufacturers can achieve desired performance characteristics while minimizing costs and waste.
Optimizing Design for Manufacturability
Design optimization is crucial for maximizing efficiency in MIM. Manufacturers must focus on creating designs that are not only functional but also manufacturable. This involves considering factors such as wall thickness, part complexity, and material flow. By optimizing these elements, manufacturers can reduce the likelihood of defects and improve production efficiency.
Designing for Metal Injection Molding
Designing for Metal Injection Molding requires a deep understanding of the process’s capabilities and limitations. Engineers should aim to create designs that leverage MIM’s strengths, such as its ability to produce complex geometries with high precision. Maintaining moderate wall thicknesses is essential to prevent defects and ensure the integrity of the final product. Additionally, incorporating features that facilitate material flow and reduce stress concentrations can enhance manufacturability. By focusing on these aspects, manufacturers can streamline the production process and achieve higher efficiency.
Utilizing Appropriate Equipment
The choice of equipment significantly impacts the efficiency of the MIM process. Manufacturers must select machines that are capable of handling the specific requirements of their projects. This includes considering factors such as machine capacity, precision, and automation capabilities. Advanced equipment with automation features can reduce labor costs and increase production speed, making MIM a more cost-effective solution. Regular maintenance and calibration of equipment also play a vital role in ensuring consistent quality and minimizing downtime. By investing in the right equipment, manufacturers can enhance the efficiency and reliability of their MIM operations.
Process Optimization
Process optimization in Metal Injection Molding (MIM) involves refining each stage to enhance efficiency and product quality. Manufacturers can achieve significant improvements by focusing on several key areas:
-
Feedstock Preparation: Ensuring the homogeneity of the metal powder and binder mixture is crucial. Consistent feedstock quality leads to uniform part properties and reduces defects. Manufacturers should regularly monitor and adjust the mixing process to maintain optimal conditions.
-
Injection Molding Parameters: Fine-tuning parameters such as temperature, pressure, and injection speed can significantly impact the final product’s quality. Manufacturers must carefully calibrate these settings to ensure proper material flow and fill the mold completely. This precision minimizes defects and enhances the structural integrity of the parts.
-
Debinding and Sintering: These stages are critical for removing the binder and solidifying the metal particles. Optimizing the debinding process involves controlling the temperature and time to prevent part distortion. During sintering, manufacturers should focus on achieving the right balance between temperature and duration to ensure full densification without compromising part dimensions.
-
Quality Control: Implementing rigorous quality control measures throughout the MIM process ensures consistency and reliability. Manufacturers should employ advanced inspection techniques, such as X-ray tomography or laser scanning, to detect any deviations from the desired specifications. Regular quality checks help identify potential issues early, allowing for timely adjustments and reducing waste.
By concentrating on these aspects, manufacturers can maximize the benefits of MIM, including lower tooling costs, shorter lead times, and increased design flexibility. The process’s inherent efficiency and precision make it an ideal choice for producing complex parts with high repeatability.
Boosting efficiency in metal injection molding (MIM) hinges on several key strategies. By selecting the right materials, optimizing design for manufacturability, and utilizing appropriate equipment, manufacturers can significantly enhance their production processes. Designing for Metal Injection Molding ensures that components meet high precision and complexity requirements while minimizing waste. Implementing these strategies not only reduces costs but also improves product quality and consistency. As the MIM market continues to grow, adopting these insights will empower businesses to stay competitive and meet the increasing demand for intricate, high-quality components.