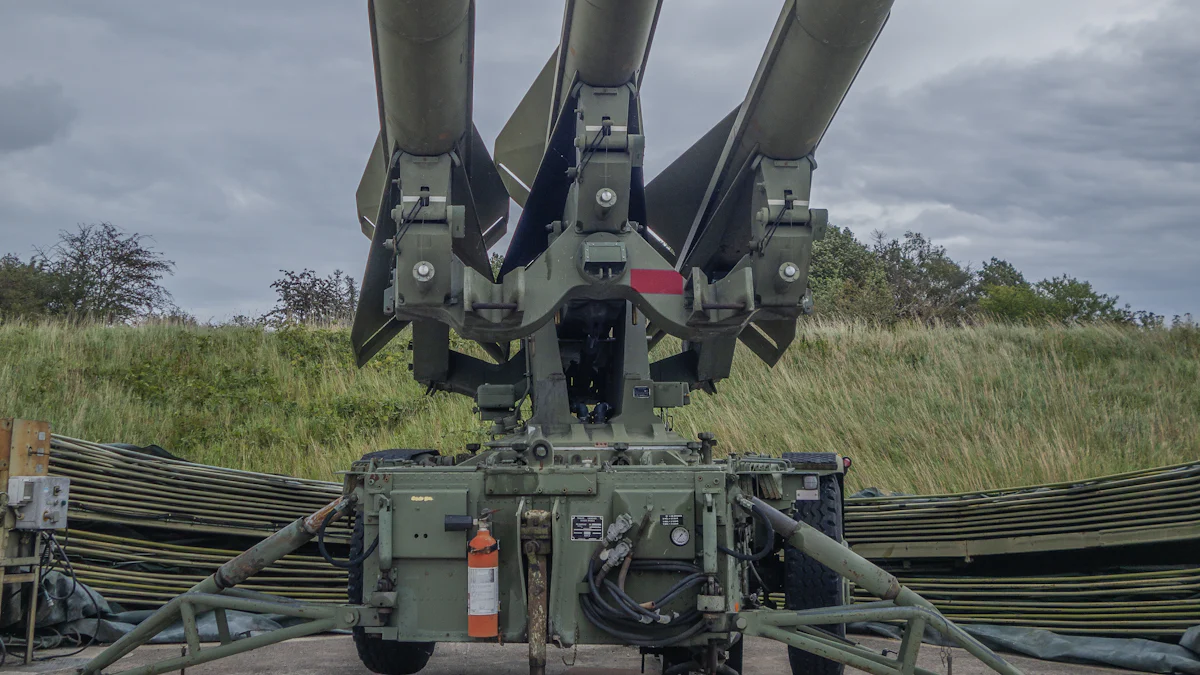
Indo-MIM leads the Metal Injection Molding (MIM) industry with unmatched expertise and innovation. As the world’s largest MIM parts manufacturer, it operates state-of-the-art facilities spanning over 0.80 million square feet in India and the United States. This extensive capacity enables the production of precision-engineered components for industries like aerospace, medical, and automotive. Serving customers in more than 45 countries, Indo-MIM combines advanced technology with a customer-focused approach. Its dedication to quality and efficiency ensures reliable solutions for complex manufacturing needs, setting a global benchmark in the MIM sector.
Key Takeaways
- Indo-MIM is the world’s largest MIM parts manufacturer, offering unmatched expertise and innovation in producing precision-engineered components.
- The Metal Injection Molding (MIM) process allows for the creation of complex, high-quality parts with minimal material waste, making it a cost-effective solution for various industries.
- Indo-MIM’s commitment to quality is reflected in its adherence to global standards and continuous improvement methodologies, ensuring reliable and high-performance products.
- With state-of-the-art facilities in India and the USA, Indo-MIM maintains complete control over production, reducing lead times and enhancing product quality.
- The company’s customer-centric approach emphasizes collaboration and customization, allowing for tailored solutions that meet specific client needs.
- Indo-MIM invests heavily in research and development, integrating advanced technologies like 3D printing to stay ahead in the competitive MIM market.
- A robust global presence with sales and support offices ensures that Indo-MIM remains accessible and responsive to customers across more than 45 countries.
Understanding Metal Injection Molding (MIM)
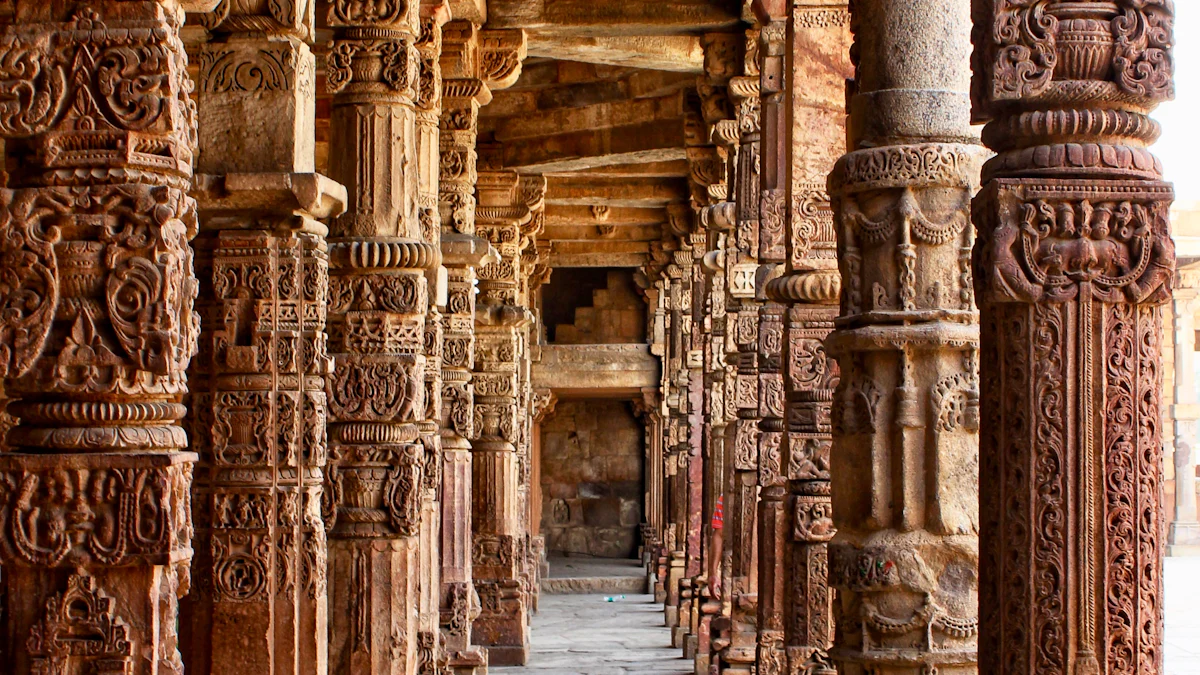
What is MIM?
Metal Injection Molding (MIM) combines the versatility of plastic injection molding with the strength and integrity of metal. This advanced manufacturing process involves mixing fine metal powders with a binder material to create a feedstock. The feedstock is then injected into molds to form intricate shapes. After molding, the binder is removed, and the part undergoes sintering, where it is heated to near its melting point. This step fuses the metal particles, resulting in a dense and robust component.
MIM stands out for its ability to produce small, complex parts with exceptional precision. Unlike traditional methods, MIM eliminates the need for extensive machining or finishing. It offers a streamlined approach to manufacturing, making it ideal for industries requiring high-quality components with tight tolerances.
Why MIM is a Preferred Manufacturing Method
Manufacturers favor MIM for its unique advantages over conventional fabrication methods. It excels in producing components with intricate geometries that are challenging or costly to achieve through machining or casting. MIM reduces material wastage significantly, as the process uses nearly all the raw material in the final product. This efficiency not only minimizes costs but also supports sustainable manufacturing practices.
The process also eliminates the need for secondary operations, such as additional machining or finishing. This feature enhances production speed and reduces labor costs. For high-volume production, MIM proves to be the most cost-effective solution. It delivers consistent quality across large batches, ensuring reliability and uniformity in every component.
Compared to other methods, MIM offers unmatched flexibility. It can produce parts with enhanced mechanical properties, such as high strength and durability. Industries like aerospace, medical, and automotive rely on MIM for its ability to meet stringent performance requirements. Its capability to handle complex designs and high production volumes makes it a preferred choice for modern manufacturing needs.
“MIM excels in producing small, highly complex parts that are difficult or cost prohibitive to produce with conventional technologies such as machining or casting.”
Indo-MIM’s Unique Strengths
Expertise and Experience
Indo-MIM has established itself as a pioneer in the Metal Injection Molding (MIM) industry. With decades of experience, the company has mastered the art of designing and manufacturing intricate precision components. Its expertise spans every stage of the process, from conceptualization to final production. This comprehensive approach ensures that every product meets the highest standards of quality and performance.
INDO-MIM Corporate Profile: “At the cutting edge of technology, INDO-MIM has finely-honed expertise for providing a total solution in conceptualizing, designing, and manufacturing complex precision components and sub-assemblies.”
The company’s ability to handle complex geometries and challenging requirements sets it apart. Industries such as aerospace, medical, and automotive rely on Indo-MIM for its proven track record of delivering reliable solutions. Its extensive experience allows it to anticipate challenges and provide innovative answers, ensuring customer satisfaction at every step.
Advanced Resources and Technology
Indo-MIM operates with state-of-the-art facilities equipped with advanced machinery and technologies. These resources enable the company to maintain precision and efficiency in its manufacturing processes. With in-house capabilities like precision machining, heat treatment, and surface finishing, Indo-MIM ensures complete control over production. This integration reduces lead times and enhances the overall quality of the final product.
INDO-MIM MIM Solution Complexity: “INDO-MIM can supply parts with complete finish as per the customer prints in lesser lead times compared to conventional manufacturing processes.”
The company also invests heavily in research and development to stay ahead in the industry. By incorporating cutting-edge technologies such as 3D printing, Indo-MIM continues to push the boundaries of what is possible in MIM. This commitment to innovation ensures that customers receive products that meet modern manufacturing demands.
Customization and Customer-Centric Approach
Indo-MIM places a strong emphasis on understanding and meeting the unique needs of its customers. Its customer-centric approach involves close collaboration with clients to develop tailored solutions. Whether it’s a prototype or a large-scale production run, Indo-MIM adapts its processes to align with specific requirements.
INDO-MIM LinkedIn: “As a fully integrated MIM parts producer, we excel in design, tooling, materials, and comprehensive finishing and assembly operations.”
The company’s ability to customize products extends to material selection, design optimization, and finishing options. This flexibility ensures that customers receive components that not only meet but exceed their expectations. Indo-MIM’s dedication to building long-term partnerships reflects its commitment to delivering value and fostering trust.
Commitment to Quality and Innovation
At Indo-MIM, quality and innovation form the foundation of everything we do. Our commitment to excellence begins with a robust Quality Management System (QMS) that adheres to globally recognized standards, including ISO 9001:2015, IATF 16949:2016, and AS 9100:2016. These certifications reflect our dedication to delivering products that meet and exceed customer expectations. By embedding meticulous attention to quality into our culture, we ensure that every component we produce aligns with the highest industry benchmarks.
We employ best-practice methodologies such as Lean Six Sigma, 5S Visual Management, and Kaizen Principles to drive continuous improvement. These approaches enhance efficiency, reduce waste, and maintain consistency across all production stages. For us, quality is not just a goal; it is a continuous journey. Every process, from design to delivery, undergoes rigorous scrutiny to guarantee precision and reliability.
Innovation is equally integral to our success. Indo-MIM invests heavily in research and development to stay ahead in the competitive MIM industry. By integrating advanced technologies like 3D printing and strategic supplier partnerships, we push the boundaries of what is possible. This forward-thinking approach enables us to create complex, precision-engineered components that meet the evolving needs of industries worldwide.
Our state-of-the-art facilities, spanning over one million square feet, house over 2,500 skilled professionals who bring expertise and creativity to every project. This team-driven environment fosters collaboration and innovation, ensuring that we remain at the forefront of the MIM industry. Customers across 45 countries trust us for our ability to deliver high-quality products with unmatched value.
“Meticulous attention to quality is ingrained in Indo-MIM’s culture.” This philosophy drives our relentless pursuit of excellence and positions us as a leader in the global MIM market.
Indo-MIM’s Global Presence
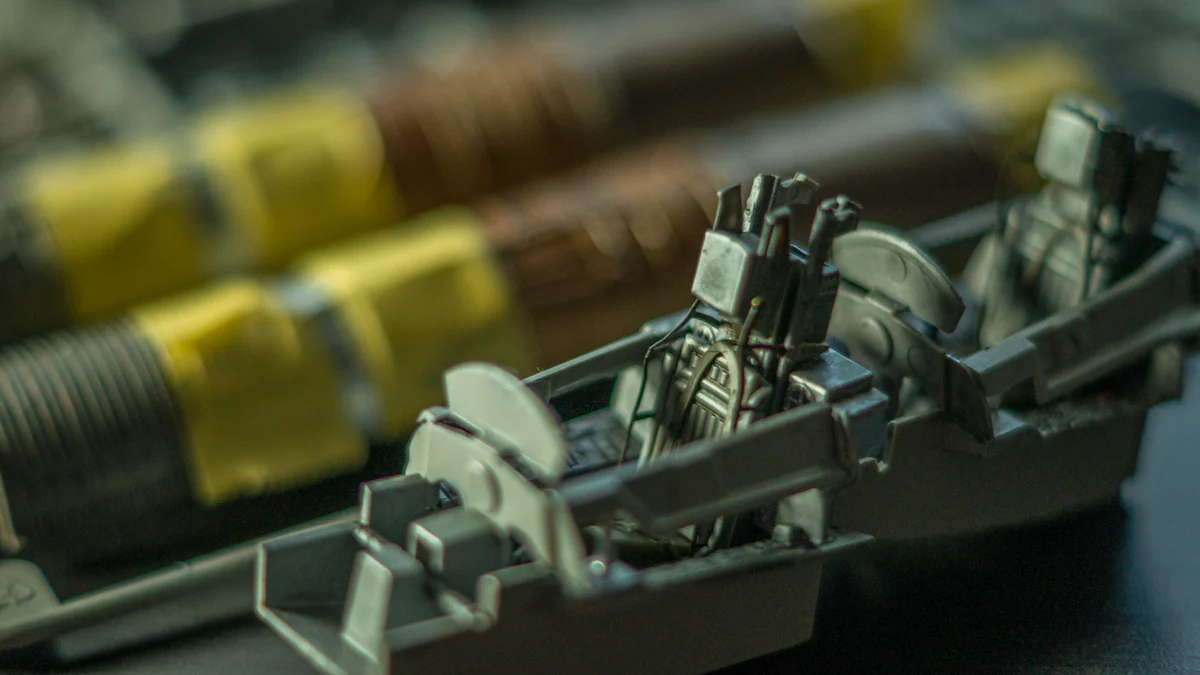
Headquarters and Manufacturing Facilities
At Indo-MIM, we take pride in our expansive and strategically located manufacturing facilities. Our headquarters in Bangalore, India, serves as the heart of our operations, housing cutting-edge technology and a highly skilled workforce. This facility spans over 0.80 million square feet, making it one of the largest MIM production capacities in the world. It is equipped to handle every stage of the Metal Injection Molding (MIM) process, from design and tooling to finishing and assembly.
In addition to our Indian headquarters, we operate a state-of-the-art facility in Texas, USA. This location strengthens our ability to serve customers across the Americas with reduced lead times and localized support. Both facilities adhere to stringent quality standards, ensuring that every component we produce meets global benchmarks. By maintaining advanced infrastructure in these key regions, we can deliver precision-engineered products efficiently and reliably.
Sales and Support Offices Worldwide
Our global presence extends beyond manufacturing. Indo-MIM has established a robust network of sales and support offices across the Americas, Europe, and Asia. These offices play a crucial role in connecting us with our customers, enabling seamless communication and personalized service. By being closer to our clients, we can better understand their unique requirements and provide tailored solutions.
Our sales teams work hand-in-hand with customers to ensure smooth project execution, from initial consultation to final delivery. Meanwhile, our support teams offer technical assistance and after-sales service, reinforcing our commitment to customer satisfaction. This global network allows us to cater to diverse industries, including aerospace, automotive, medical, and defense, across more than 45 countries.
“Indo-MIM’s global footprint ensures that we remain accessible and responsive to our customers, no matter where they are located.”
By combining world-class manufacturing facilities with a comprehensive global support network, Indo-MIM continues to set the standard for excellence in the MIM industry.
Indo-MIM leads the MIM industry with its unmatched expertise, innovation, and global reach. By maintaining the largest installed MIM capacity worldwide, it ensures precision and efficiency in every project. Its commitment to quality, supported by advanced technology and in-house manufacturing capabilities, guarantees superior results. Customers across industries trust Indo-MIM for its ability to deliver high-quality, complex components with exceptional value. With a focus on continuous improvement and customer satisfaction, Indo-MIM consistently sets new benchmarks, solidifying its position as a trusted partner and industry leader.
FAQ
What makes a good MIM part?
A good MIM part combines precision, durability, and cost-efficiency. The design must optimize material usage while maintaining structural integrity. At Indo-MIM, we focus on creating components with intricate geometries and tight tolerances. This ensures that the parts meet the functional and aesthetic requirements of various industries. By leveraging advanced technologies and high-quality materials, we deliver MIM parts that excel in performance and reliability.
“A good MIM part is one that balances complexity, strength, and cost-effectiveness.” – INDO-MIM, June 14, 2023
How does MIM compare to traditional manufacturing methods?
MIM surpasses traditional methods like machining and casting in several ways. It allows for the production of small, complex parts with minimal material waste. Unlike machining, which often involves extensive cutting and finishing, MIM streamlines the process by eliminating secondary operations. This results in faster production times and lower costs. Additionally, MIM offers greater design flexibility, enabling the creation of intricate shapes that are challenging to achieve with conventional techniques.
What industries benefit the most from MIM?
Industries requiring precision-engineered components benefit significantly from MIM. Aerospace, medical, and automotive sectors rely on MIM for its ability to produce high-strength, lightweight parts. The defense industry values MIM for its capacity to create durable components with complex geometries. Consumer electronics and industrial applications also utilize MIM for its efficiency and versatility. At Indo-MIM, we cater to a diverse range of industries, ensuring that each sector receives tailored solutions.
Why is Indo-MIM a leader in the MIM industry?
Indo-MIM leads the MIM industry due to its unmatched expertise, advanced resources, and global reach. With the largest installed MIM capacity worldwide, we deliver precision-engineered components efficiently. Our commitment to quality, innovation, and customer satisfaction sets us apart. By integrating cutting-edge technologies like 3D printing and maintaining stringent quality standards, we consistently exceed industry benchmarks.
What materials are used in MIM?
MIM utilizes a variety of metal powders, including stainless steel, titanium, and nickel alloys. The choice of material depends on the specific application and performance requirements. At Indo-MIM, we offer a wide range of material options to meet diverse industry needs. Each material undergoes rigorous testing to ensure it meets the desired mechanical properties and quality standards.
How does Indo-MIM ensure quality in its products?
We adhere to globally recognized quality standards, including ISO 9001:2015 and AS 9100:2016. Our robust Quality Management System (QMS) ensures that every component meets the highest industry benchmarks. We employ methodologies like Lean Six Sigma and Kaizen Principles to drive continuous improvement. By embedding meticulous attention to quality into our processes, we guarantee precision and reliability in every product.
“Meticulous attention to quality is ingrained in Indo-MIM’s culture.”
Can MIM handle high-volume production?
Yes, MIM is ideal for high-volume production. The process allows for consistent quality across large batches, making it cost-effective for mass manufacturing. At Indo-MIM, we leverage our extensive capacity and advanced resources to handle high-volume projects efficiently. Our streamlined processes ensure timely delivery without compromising on quality.
What role does innovation play at Indo-MIM?
Innovation drives everything we do at Indo-MIM. We invest heavily in research and development to stay ahead in the competitive MIM industry. By integrating advanced technologies like 3D printing, we push the boundaries of what is possible. This forward-thinking approach enables us to create complex, precision-engineered components that meet the evolving needs of industries worldwide.
How does Indo-MIM support its global customers?
We maintain a robust network of sales and support offices across the Americas, Europe, and Asia. This global presence ensures seamless communication and personalized service. Our teams work closely with customers to understand their unique requirements and provide tailored solutions. By being accessible and responsive, we reinforce our commitment to customer satisfaction.
What sets Indo-MIM apart from its competitors?
Our ability to combine expertise, innovation, and customer-centricity sets us apart. We offer end-to-end solutions, from design and tooling to finishing and assembly. Our state-of-the-art facilities and skilled workforce enable us to deliver high-quality products efficiently. By prioritizing quality, efficiency, and customer satisfaction, we have established ourselves as a trusted partner in the MIM industry.