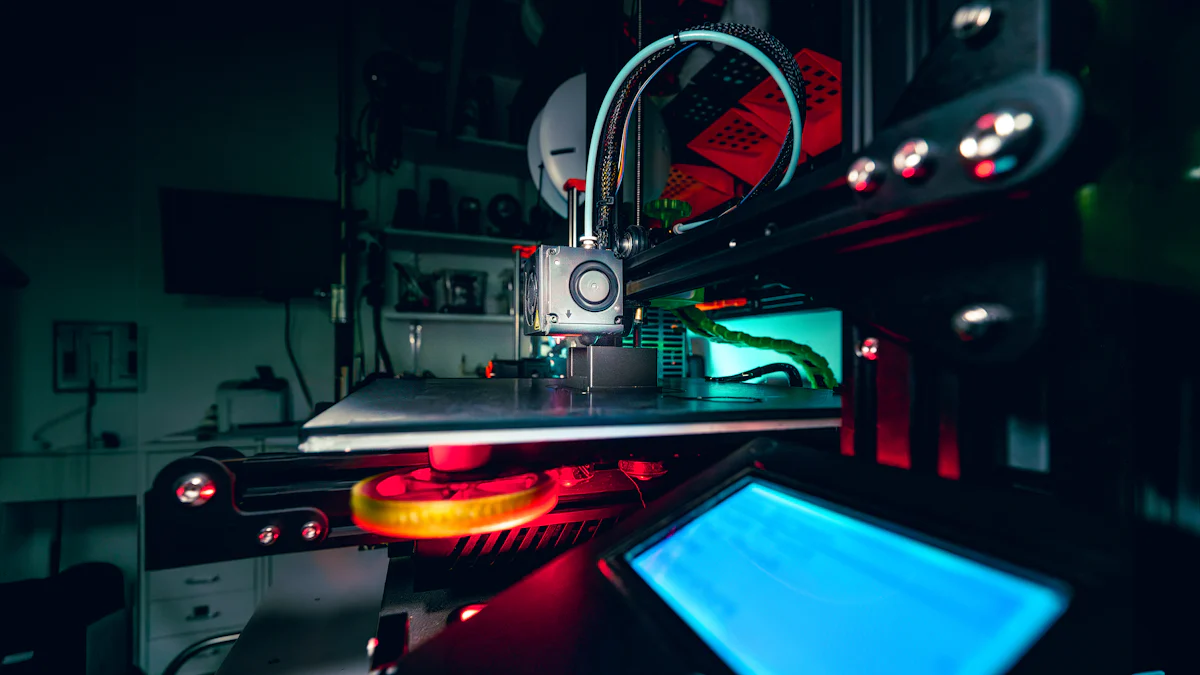
Metal Injection Molding (MIM) revolutionizes manufacturing by merging powder metallurgy with plastic injection molding. This process allows for the creation of intricate metal components with high precision. I find it fascinating to explore how Metal Injection Molding works. It starts with mixing metal powders and binders to form a feedstock. This mixture is then injected into molds, forming complex shapes. Afterward, the binder is removed, and the part undergoes sintering to achieve its final properties. The MIM market is growing rapidly, with projections reaching USD 6.75 billion by 2027, highlighting its increasing importance across industries.
Key Takeaways
- Metal Injection Molding (MIM) combines powder metallurgy and plastic injection molding to create intricate metal components with high precision.
- The MIM process involves four key stages: feedstock preparation, injection molding, debinding, and sintering, each crucial for achieving the final product’s quality.
- MIM is particularly advantageous for producing complex parts with tight tolerances, making it ideal for industries like automotive, medical devices, and consumer electronics.
- Cost-effectiveness is a major benefit of MIM, especially for large production runs, as it reduces per-unit costs and minimizes material waste.
- The versatility of materials used in MIM, including stainless steel and titanium, allows for tailored solutions that meet specific performance requirements.
- Compared to traditional casting and CNC machining, MIM offers superior precision and efficiency, particularly for small, intricate components.
- Understanding the MIM process can empower manufacturers to leverage its advantages for innovative and reliable product development.
The Process of Metal Injection Molding
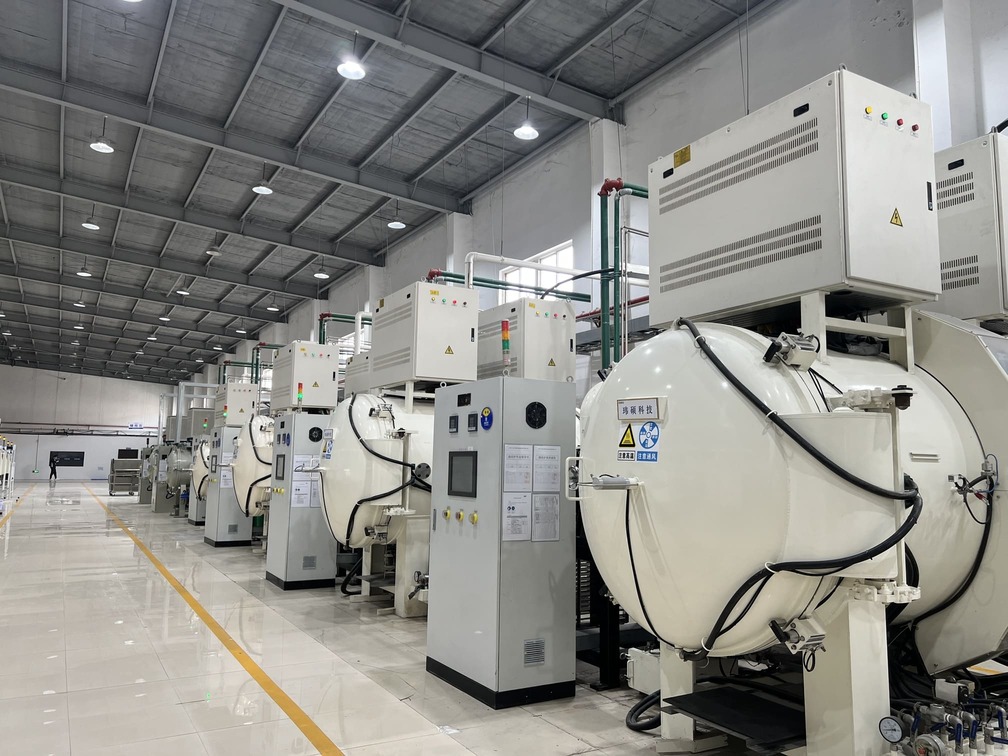
Understanding how Metal Injection Molding works involves delving into its intricate process. Each step plays a crucial role in transforming raw materials into precise metal components.
Feedstock Preparation
The journey begins with feedstock preparation. I start by mixing fine metal powders with binders, such as waxes and polymers. This combination forms a proprietary MIM feedstock. The goal is to create a homogeneous mixture that ensures reliability and repeatability during processing. Granulating the feedstock into pellets prepares it for the next stage.
Injection Molding
Next, I inject the prepared feedstock into precision molds. This step occurs in standard injection molding machines. The feedstock, now plasticized, enters the mold cavity at high pressure. This process allows me to form complex shapes with high accuracy. The resulting products, known as ‘green parts,’ require further processing to achieve their final properties.
Debinding
Debinding follows injection molding. I focus on removing the binders from the molded part. This step is essential to prepare the part for sintering. The debinding process ensures that the metal particles remain compacted, setting the stage for the final transformation.
Sintering
Sintering represents the final and crucial stage in the Metal Injection Molding process. I find this step fascinating as it transforms the ‘green parts’ into fully dense metal components. The process begins by heating the molded part to a temperature below its melting point. This heating causes the metal particles to bond together, solidifying and densifying the structure. The sintering furnace plays a vital role here, providing a controlled environment to ensure uniform heating.
During sintering, I pay close attention to the temperature and time settings. These parameters are critical in achieving the desired mechanical properties. The goal is to enhance the strength, hardness, and durability of the metal part. By carefully controlling the sintering conditions, I can produce components that meet stringent industry standards.
The sintering process not only solidifies the part but also reduces porosity, resulting in a near-net-shape product. This precision minimizes the need for additional machining, saving both time and resources. I appreciate how this step exemplifies the efficiency and effectiveness of Metal Injection Molding.
Advantages of Metal Injection Molding
Metal Injection Molding (MIM) offers several advantages that make it a preferred choice in manufacturing. I find these benefits particularly compelling as they highlight the efficiency and versatility of the process.
High precision and complexity
One of the standout features of Metal Injection Molding is its ability to produce parts with high precision and complexity. I can create intricate designs that would be challenging or impossible with traditional methods. The process allows for tight tolerances and fine details, which are essential in industries like medical devices and consumer electronics. By using MIM, I achieve a level of detail that enhances the functionality and aesthetics of the final product.
Cost-effectiveness for large production runs
When it comes to large production runs, Metal Injection Molding proves to be cost-effective. The initial setup costs may be higher due to mold creation, but the per-unit cost decreases significantly with volume. I appreciate how this scalability makes MIM an attractive option for mass production. The process minimizes material waste and reduces the need for secondary operations, further lowering costs. This efficiency is particularly beneficial in the automotive industry, where large quantities of components are required.
Material versatility
Material versatility is another advantage of Metal Injection Molding. I can work with a wide range of metals, including stainless steel, titanium, and copper. This flexibility allows me to choose the best material for specific applications, ensuring optimal performance. The ability to use different alloys also opens up possibilities for innovation and customization. Whether I need corrosion resistance, high strength, or thermal conductivity, MIM provides the material options to meet those needs.
Applications of Metal Injection Molding
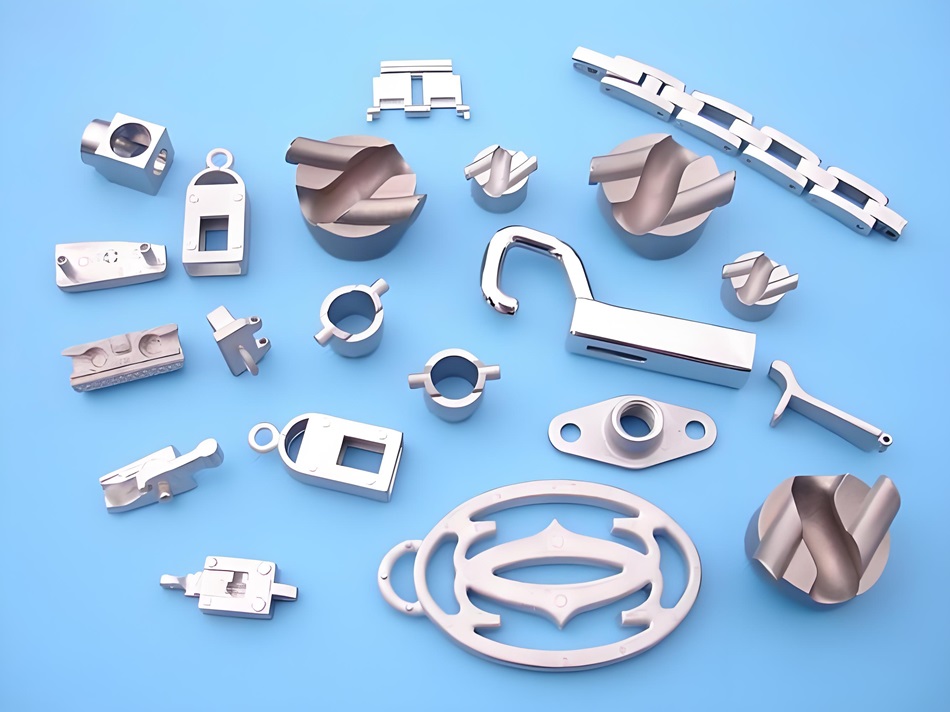
Automotive Industry
In the automotive industry, I see Metal Injection Molding (MIM) as a game-changer. This process allows me to produce complex components with high precision, which is crucial for automotive applications. The ability to create intricate designs means I can manufacture parts like gearboxes, turbochargers, and fuel injector nozzles with ease. These components require tight tolerances and fine details, which MIM provides. Additionally, the cost-effectiveness of MIM for large production runs makes it an attractive option for the automotive sector, where mass production is the norm. By using MIM, I can ensure that each part meets the stringent quality standards required in this industry.
Medical Devices
The medical device industry benefits significantly from Metal Injection Molding. I find MIM particularly useful for producing small, intricate components used in surgical instruments and implantable devices. The high precision and complexity achievable with MIM allow me to create parts that meet the rigorous standards of the medical field. For instance, I can manufacture components for minimally invasive surgical tools, which require exceptional accuracy and reliability. The material versatility of MIM also plays a crucial role here, as I can choose biocompatible metals like titanium for implants. This flexibility ensures that the final products are safe and effective for medical use.
Consumer Electronics
In the realm of consumer electronics, Metal Injection Molding offers unparalleled advantages. I can produce components with intricate geometries and high-quality surface finishes, which are essential for modern electronic devices. MIM allows me to create parts for smartphones, laptops, and wearable technology with ease. The process supports the production of connectors, housings, and other small metal components that require precision and durability. Moreover, the ability to manufacture large volumes of parts at a lower cost makes MIM an ideal choice for the fast-paced consumer electronics market. By leveraging MIM, I can contribute to the development of innovative and reliable electronic products.
Comparison with Other Manufacturing Methods
Metal Injection Molding vs. Traditional Casting
When I compare Metal Injection Molding (MIM) to traditional casting, several differences stand out. MIM excels in producing small, intricate parts with high precision. Traditional casting, on the other hand, often struggles with achieving the same level of detail and accuracy. In my experience, MIM allows me to create complex geometries that would be challenging or impossible with casting.
Expert Testimony:
Expert Guide, a leader in the field, notes that MIM has established itself as a competitive manufacturing process, particularly for applications requiring small precision components. This is partly due to the plethora of advantages MIM offers compared to alternative manufacturing techniques, such as reduced production time and minimized material waste.
Traditional casting involves pouring molten metal into a mold, which can lead to issues like shrinkage and porosity. These problems often require additional machining to achieve the desired finish. MIM, however, minimizes these issues by using a feedstock of metal powders and binders, resulting in near-net-shape components. This efficiency reduces the need for secondary operations, saving both time and resources.
Metal Injection Molding vs. CNC Machining
CNC machining and Metal Injection Molding serve different purposes in manufacturing. CNC machining excels in producing large, simple parts with high precision. However, it can be less efficient for small, complex components. I find MIM to be more suitable for these intricate designs, as it allows me to produce parts with fine details and tight tolerances.
Expert Testimony:
According to Longsheng Manufacturing, MIM is commonly used for manufacturing small, intricate parts where precision and material properties are critical, such as in the medical, aerospace, automotive, and electronics industries.
CNC machining involves cutting away material from a solid block, which can lead to significant material waste. MIM, in contrast, uses a feedstock that forms the part directly, minimizing waste. This process also supports high-volume production, making it more cost-effective for large runs. While CNC machining offers flexibility in prototyping and low-volume production, MIM provides a more efficient solution for mass production of complex components.
In exploring Metal Injection Molding (MIM), I have highlighted its transformative impact on manufacturing. The process involves feedstock preparation, injection molding, debinding, and sintering, each contributing to the creation of precise metal components. MIM stands out for its ability to produce complex geometries with high precision and minimal waste. Compared to traditional casting and CNC machining, MIM offers superior cost efficiency, especially for high-volume production. Its versatility in material choice further enhances its appeal across industries. I find MIM’s effectiveness and adaptability make it an invaluable asset in modern manufacturing.
FAQ
What is Metal Injection Molding (MIM)?
Metal Injection Molding (MIM) combines powder metallurgy with plastic injection molding. I use this process to create intricate metal components with high precision. It involves mixing metal powders with binders, injecting the mixture into molds, and then removing the binders before sintering the part to achieve its final properties.
How does the MIM process work?
The MIM process involves several stages:
- Feedstock Preparation: I mix metal powders with binders to form a homogeneous feedstock.
- Injection Molding: I inject the feedstock into precision molds to form complex shapes.
- Debinding: I remove the binders from the molded part.
- Sintering: I heat the part to solidify and densify it, achieving the final mechanical properties.
Each stage requires careful control to ensure consistent part quality and performance.
What are the advantages of using MIM?
MIM offers several advantages:
- High Precision and Complexity: I can produce parts with intricate designs and tight tolerances.
- Cost-Effectiveness: Ideal for large production runs, reducing per-unit costs.
- Material Versatility: I can work with various metals, including stainless steel and titanium.
These benefits make MIM a preferred choice in many industries.
What industries benefit from MIM?
Several industries benefit from MIM, including:
- Automotive: I produce complex components like gearboxes and fuel injector nozzles.
- Medical Devices: I create small, intricate parts for surgical instruments and implants.
- Consumer Electronics: I manufacture components for smartphones and wearable technology.
MIM’s versatility and precision make it suitable for diverse applications.
How does MIM compare to traditional casting?
MIM excels in producing small, intricate parts with high precision. Traditional casting often struggles with achieving the same level of detail. MIM minimizes issues like shrinkage and porosity, resulting in near-net-shape components that require less machining.
How does MIM compare to CNC machining?
CNC machining is ideal for large, simple parts. However, MIM is more efficient for small, complex components. MIM minimizes material waste and supports high-volume production, making it cost-effective for large runs.
What factors contribute to the popularity of MIM?
Several factors contribute to MIM’s popularity:
- Technological Advancements: Improved techniques enhance precision and efficiency.
- Economic Viability: Cost-effective for mass production.
- Sustainability: Reduces material waste compared to traditional methods.
These factors make MIM an attractive option for modern manufacturing.
What challenges does MIM face?
MIM requires careful control and optimization at each stage to ensure consistent quality. This complexity can make it challenging to implement and maintain. Specialized knowledge or expertise may be necessary to manage the process effectively.
Can MIM be used for prototyping?
While MIM is primarily used for mass production, it can also be used for prototyping. However, the initial setup costs may be higher due to mold creation. For low-volume production, CNC machining might be more cost-effective.
What materials can be used in MIM?
I can use a wide range of metals in MIM, including:
- Stainless Steel
- Titanium
- Copper
This material versatility allows me to choose the best option for specific applications, ensuring optimal performance.