Sintered vs. Machined Gears
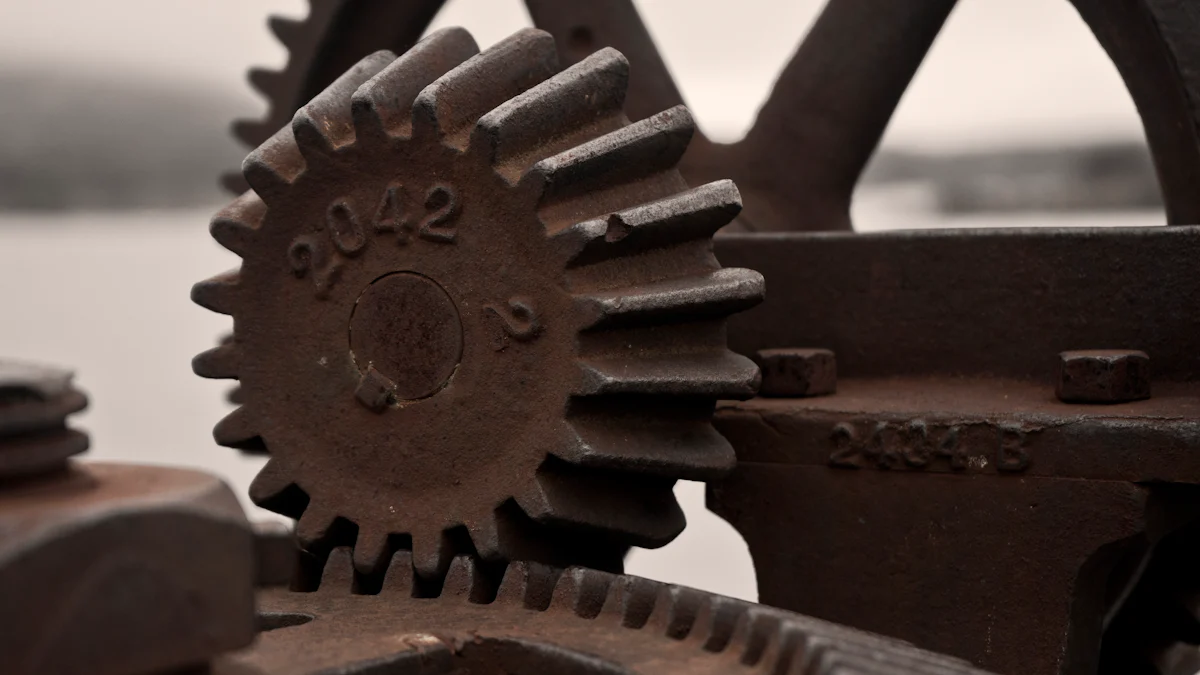
When deciding between sintered vs. machined gears, understanding their distinct advantages is crucial. Sintered gears excel in cost-effectiveness and complex geometry capabilities, making them ideal for high-volume production with reduced material waste. In contrast, machined gears offer superior volume repeatability and precision, ensuring consistent performance. Each gear type serves specific applications, with sintered gears being more powerful in terms of hardness and durability, while machined gears provide higher precision. By evaluating factors like cost, precision, and strength, you can choose the best gear type for your needs.
Key Takeaways
- Sintered gears are cost-effective and ideal for high-volume production, making them a sustainable choice for projects with budget constraints.
- Machined gears offer superior precision and strength, making them essential for applications that require high reliability and performance.
- Consider the specific application requirements when choosing between gear types; sintered gears excel in complex designs, while machined gears are better for high-stress environments.
- Sintered gears may have limitations in strength and surface finish due to their inherent porosity, which can affect performance in precision-critical applications.
- Investing in machined gears can lead to long-term savings due to their durability and lower maintenance costs, despite their higher initial price.
- Evaluate factors like cost, precision, and strength to ensure optimal gear selection for your mechanical systems.
Sintered Gears
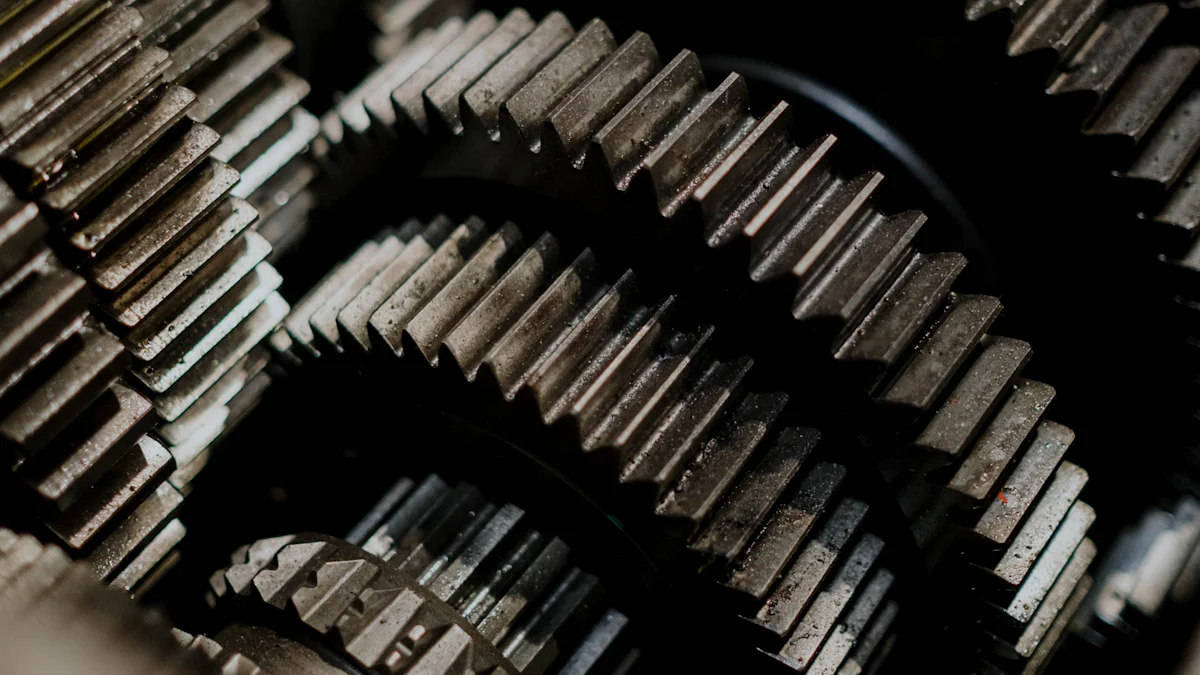
Advantages
Cost-effectiveness
I find that sintered gears offer a significant advantage in terms of cost-effectiveness. The manufacturing process, which involves powder metallurgy, allows for the production of gears at a lower cost compared to traditional machining methods. This efficiency stems from the reduced material waste and energy consumption during production. For projects requiring mass production, sintered gears provide an economical solution without compromising on quality.
Material efficiency
The material efficiency of sintered gears stands out as a key benefit. By utilizing powdered metal, the process ensures high material utilization, minimizing waste. This approach not only conserves resources but also contributes to a more environmentally friendly manufacturing process. In my experience, this efficiency translates into both cost savings and a reduced environmental footprint, making sintered gears a sustainable choice.
Complex shapes and designs
Sintered gears excel in producing complex shapes and designs. The sintering process allows for the creation of intricate geometries that would be challenging or costly to achieve through traditional machining. This capability provides flexibility in design, enabling customized solutions for specific applications. Whether it’s for automotive components or consumer electronics, sintered gears can meet diverse design requirements with ease.
Disadvantages
Limited strength
Despite their advantages, sintered gears have limitations in terms of strength. The inherent porosity of the material can lead to reduced load-bearing capacity compared to machined gears. For applications requiring high strength and durability, this limitation may necessitate additional considerations or alternative solutions.
Surface finish limitations
Surface finish is another area where sintered gears may fall short. The sintering process can result in a rougher surface compared to machined gears, which might affect performance in precision applications. While post-processing techniques can improve the finish, they may add to the overall cost and complexity of the production process.
Porosity issues
Porosity remains a challenge in the production of sintered gears. This characteristic can impact the mechanical properties of the gears, such as strength and wear resistance. In applications where high precision and reliability are critical, the porosity of sintered gears might pose a concern. Addressing these issues often requires careful consideration of the specific application requirements and potential trade-offs.
Machined Gears
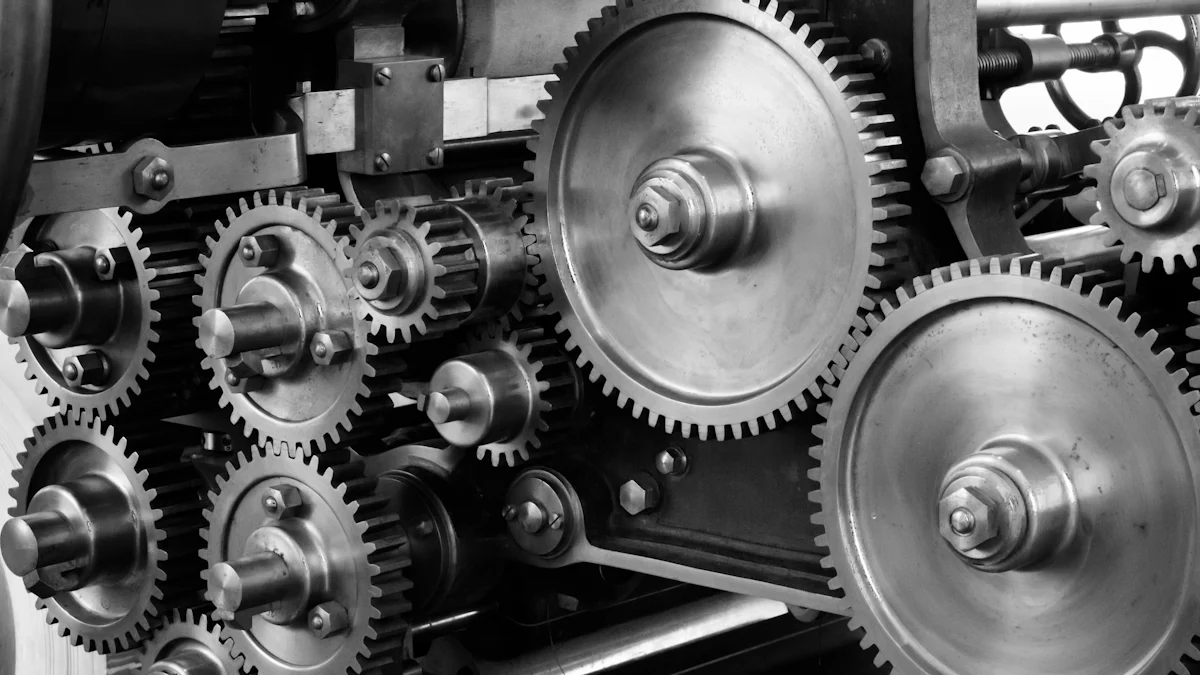
Advantages
High precision
I appreciate the high precision that machined gears offer. The gear machining process, including techniques like gear grinding, achieves exceptional accuracy and surface integrity. This precision ensures that gears operate smoothly at high speeds and under significant loads. In my experience, machined gears consistently meet the strict tolerances required in demanding applications, such as automotive transmissions and industrial machinery.
Superior strength
The superior strength of machined gears stands out as a key advantage. By employing processes like heat treatment, these gears gain enhanced durability and load-bearing capacity. This strength makes them ideal for applications where reliability and performance are critical. I have found that machined gears excel in environments with high wear conditions, ensuring long-lasting functionality.
Better surface finish
Machined gears provide a better surface finish compared to their sintered counterparts. Techniques like lapping and grinding result in a smooth and refined surface, which is crucial for high-precision applications. This superior finish not only enhances the aesthetic appeal but also contributes to improved performance by reducing friction and wear. In my projects, the quality of the surface finish has been a decisive factor in choosing machined gears over other options.
Disadvantages
Higher cost
Despite their advantages, machined gears come with a higher cost. The intricate machining processes and the need for skilled labor contribute to increased production expenses. For projects with budget constraints, this cost factor may pose a challenge. However, I believe that the investment in machined gears often pays off in terms of performance and reliability.
Material waste
Material waste is another consideration when opting for machined gears. The subtractive nature of machining processes results in significant material removal, leading to waste. This aspect can impact both cost and environmental sustainability. In my view, careful planning and optimization of the machining process can help mitigate this issue, but it remains a factor to consider.
Longer production time
The production time for machined gears tends to be longer compared to sintered gears. The complexity of machining operations, along with the need for secondary processes like heat treatment and surface finishing, extends the manufacturing timeline. For projects with tight deadlines, this longer production time can be a drawback. However, I find that the quality and precision of machined gears often justify the wait.
Key Factors Comparison
When evaluating sintered and machined gears, several key factors come into play. These factors help determine the most suitable gear type for specific applications.
Cost Implications
Initial investment
The initial investment for machined gears tends to be higher. The intricate machining processes require specialized equipment and skilled labor, which increases upfront costs. In contrast, sintered gears offer a more cost-effective solution. The powder metallurgy process reduces material waste and energy consumption, leading to lower initial expenses. For projects with budget constraints, sintered gears provide an economical alternative without sacrificing quality.
Long-term cost efficiency
Long-term cost efficiency varies between the two gear types. Machined gears, with their superior precision and durability, often result in lower maintenance costs over time. Their high load-bearing capacity and wear resistance contribute to extended service life, reducing the need for frequent replacements. Sintered gears, while initially cheaper, may incur additional costs due to their limitations in strength and surface finish. However, for applications where these factors are less critical, sintered gears can offer significant long-term savings.
Precision and Accuracy
Tolerances
Machined gears excel in precision and accuracy. The machining process achieves tight tolerances, making them ideal for precision-critical applications. This high level of accuracy ensures consistent performance, even under demanding conditions. Sintered gears, on the other hand, have broader tolerances. While suitable for less precision-critical uses, they may not meet the stringent requirements of certain industries.
Consistency
Consistency is another area where machined gears shine. Their production process ensures superior volume repeatability, resulting in uniformity across batches. This consistency is crucial for applications requiring reliable performance. Sintered gears, although cost-effective, may exhibit lower volume repeatability. This characteristic can impact consistency, especially in high-volume production scenarios.
Strength and Durability
Load-bearing capacity
Machined gears offer exceptional load-bearing capacity. Their robust construction and heat treatment processes enhance strength, making them suitable for heavy-duty applications. Sintered gears, while durable, have inherent porosity that limits their load-bearing capabilities. For applications requiring high strength and durability, machined gears provide a more reliable solution.
Wear resistance
Wear resistance is a critical factor in gear selection. Machined gears, with their superior surface finish and material properties, exhibit excellent wear resistance. This attribute ensures longevity and reduces the risk of failure in high-stress environments. Sintered gears, despite their cost advantages, may face challenges in wear resistance due to porosity issues. In applications where wear resistance is paramount, machined gears offer a more dependable choice.
Application Suitability
Automotive industry
In the automotive industry, I find that both sintered and machined gears have their unique advantages. Sintered gears, with their cost-effectiveness and ability to produce complex shapes, are ideal for high-volume production of components like oil pump gears and timing gears. Their material efficiency and reduced waste make them a sustainable choice for mass production.
“Sintered gears offer cost-effective production but may have lower volume repeatability,” which can be a consideration in applications where consistency is crucial.
On the other hand, machined gears excel in applications requiring high precision and strength. For example, in automotive transmissions, the superior strength and tight tolerances of machined gears ensure reliable performance under high loads and speeds. The better surface finish of machined gears also contributes to smoother operation and reduced wear, which is essential for the longevity of automotive components.
Consumer electronics
In consumer electronics, the choice between sintered and machined gears depends on the specific application requirements. Sintered gears, with their ability to produce intricate designs, are well-suited for small, complex components found in devices like printers and cameras. Their cost-effectiveness makes them an attractive option for high-volume production, where budget constraints are a concern.
However, for applications requiring high precision and reliability, such as in high-end audio equipment or precision instruments, machined gears are the preferred choice. The high precision and superior surface finish of machined gears ensure consistent performance and durability, which are critical in maintaining the quality and functionality of these devices.
Industrial machinery
In industrial machinery, the demands for strength, durability, and precision often dictate the choice of gear type. Machined gears, with their exceptional load-bearing capacity and wear resistance, are ideal for heavy-duty applications such as gearboxes, conveyors, and milling machines. Their ability to withstand high stress and maintain tight tolerances ensures reliable operation in demanding environments.
Sintered gears, while not as strong as machined gears, still find their place in industrial applications where cost and material efficiency are prioritized. For example, in less critical components or where high-volume production is needed, sintered gears provide a cost-effective solution without compromising on basic functionality.
In evaluating gear options, I find that both sintered and machined gears offer distinct advantages. Sintered gears excel in cost-effectiveness and material efficiency, making them ideal for high-volume applications. Machined gears, however, provide superior precision and strength, essential for heavy-duty and precision-driven industries. When choosing between these gears, consider the specific needs of your project. For budget-conscious, high-volume production, sintered gears are a viable choice. For applications demanding high precision and durability, machined gears are indispensable. Ultimately, understanding these factors ensures optimal gear selection for any mechanical system.
FAQ
What are the main differences between sintered and machined gears?
Sintered gears are produced using powder metallurgy, which allows for cost-effective mass production with minimal material waste. They excel in creating complex shapes. Machined gears, on the other hand, are crafted through subtractive processes like milling and grinding. This results in higher precision and superior surface finish, making them ideal for applications requiring tight tolerances.
Which gear type is more cost-effective?
Sintered gears generally offer a more cost-effective solution, especially for high-volume production. The powder metallurgy process reduces material waste and energy consumption, leading to lower initial expenses. However, machined gears, despite their higher upfront cost, may provide long-term savings due to their durability and precision.
How does the strength of sintered gears compare to machined gears?
Machined gears typically offer superior strength and load-bearing capacity. Their robust construction and heat treatment processes enhance their durability. Sintered gears, while durable, have inherent porosity that can limit their strength. For applications requiring high strength, machined gears are often the preferred choice.
Can sintered gears achieve the same precision as machined gears?
Machined gears excel in precision and accuracy, achieving tight tolerances necessary for demanding applications. Sintered gears have broader tolerances, making them suitable for less precision-critical uses. While they can meet many design requirements, they may not match the precision of machined gears in certain industries.
What factors should I consider when choosing between sintered and machined gears?
When selecting a gear type, consider factors such as cost, precision, strength, and application suitability. Sintered gears are ideal for budget-conscious, high-volume production with complex designs. Machined gears are indispensable for applications demanding high precision and durability. Evaluating these factors ensures optimal gear selection for your project.
How can I extend the life of my gears?
To extend gear life, use suitable materials and lubricants. Regular maintenance and cleaning also play a crucial role in preventing early failure. By ensuring proper lubrication and addressing wear issues promptly, you can enhance the longevity and performance of your gears.
Are there specific industries where one gear type is preferred over the other?
Yes, different industries have preferences based on their specific needs. In the automotive industry, both gear types find applications. Sintered gears are used for high-volume components, while machined gears are preferred for high-precision parts. In consumer electronics, sintered gears suit complex, small components, whereas machined gears are chosen for high-end devices requiring precision.
What are the environmental impacts of using sintered versus machined gears?
Sintered gears offer an environmentally friendly option due to their high material efficiency and reduced waste. The powder metallurgy process conserves resources. Machined gears, while precise, result in more material waste due to their subtractive nature. However, careful planning and optimization can mitigate this impact.
How do I determine the right gear type for my project?
Choosing the right gear type involves assessing your project’s specific requirements. Consider factors like budget, precision needs, strength, and application environment. Consulting with gear specialists can provide valuable insights and help you make an informed decision that aligns with your project’s goals.