Powder Metallurgy Materials And Hardness
Powder metallurgy is a method of preparing metal parts by powder forming and sintering processes. In powder metallurgy, commonly used materials include iron, copper, aluminum, titanium, and other metal materials, as well as steel, stainless steel, and other alloy materials. These materials have excellent properties and a wide range of applications, becoming an important material for powder metallurgy.
Iron powder is one of the most commonly used materials in powder metallurgy. Because iron powder has good compressibility and plasticity, metal parts of various shapes can be prepared by pressing and sintering processes. The strength of the iron powder material depends on its density and the parameters of the sintering process. Under normal circumstances, the greater the density, the greater the strength, and the sintering temperature and time in the sintering process will also affect the strength of iron powder materials. By optimizing sintering parameters, different strength iron powder materials can be obtained to meet different application requirements.
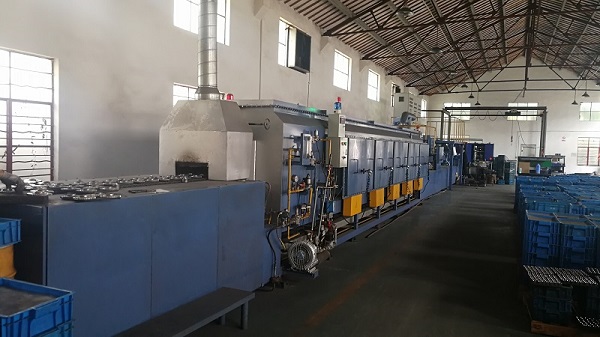
Copper powder is another commonly used powder metallurgy material. Compared with iron powder, copper powder has higher electrical and thermal conductivity. Copper powder materials can also be prepared by pressing and sintering processes to produce various shapes of parts. Similar to iron powder materials, the strength of copper powder materials also depends on its density and the parameters of the sintering process. Appropriate sintering temperature and time can improve the strength of copper powder material while maintaining its good electrical and thermal conductivity.
Aluminum powder is one of the light materials commonly used in powder metallurgy. Aluminum powder material has good compressibility and plasticity and can be prepared by pressing and sintering processes of various shapes of parts. Due to the low density and good corrosion resistance of aluminum powder, aluminum-pressed products are widely used in aerospace, automotive manufacturing, and electronics industries. The strength of the aluminum powder material also depends on its density and the parameters of the sintering process. High density and proper sintering processes can improve the strength and wear resistance of aluminum products.
Titanium powder is one of the high-performance materials in powder metallurgy. Titanium powder material has the advantages of good corrosion resistance, high strength, and low density, titanium products are widely used in aerospace, medical machinery chemical industry, and other fields. Titanium powder can be prepared by pressing and sintering processes to produce various shapes of parts.
In addition to a single metal powder, powder metallurgy can also be used to prepare alloy materials. Steel is a common powder metallurgy alloy material. By mixing different proportions of iron powder and carbon powder, and adding appropriate alloying elements, various steel powder materials with excellent properties can be prepared. The strength and properties of steel powder materials depend on their composition and the parameters of the sintering process.
Stainless steel is a commonly used powder metallurgy alloy material. Stainless steel powder is composed of iron powder and alloying elements (chromium, nickel, etc.), with good corrosion resistance and high strength. Powder metallurgy of stainless steel by pressing and sintering process to prepare various shapes of parts.
Commonly used powder metallurgy materials include iron, copper, aluminum, titanium, and other metal materials, which have different characteristics and application fields.
Powder metallurgy materials
|
chemical component | physical and mechanical properties | |||||||||
C | Cu | Mo | Fe | density D g/cm3 |
strength of extension ob MPa |
ductility % |
impact toughness a k J/cm2 |
apparent hardness
HB |
|||
Sintered iron | F0001J F0002J F0003J |
≤0.1 | — | – | margin | ≤1.5 | ≥6.4 ≥6.8 ≥7.2 |
≥100 ≥150 ≥200 |
≤3.0 ≥5.0 ≥7.0 |
≤5.0 ≥10。0 ≥20。0 |
≥40 ≤50 ≥60 |
Sintered-carbon steel | F0101J F0102J F0103J |
0.1~0.4 | – | — | margin | ≤1.5 | ≥6.2 ≥6.4 ≥6.8 |
≥100 ≥150 ≥200 |
≥1.5 ≤2.0 ≥3.0 |
≥5.0 ≥10.0 ≥15.0 |
≥50 ≥60 ≥70 |
F0111J F0112J F0113J |
0.4~0.7 | — | — | margin | ≤1.5 | ≥6.2 ≥6.4 ≥6.8 |
≥150 ≥200 ≥250 |
≥1.0 ≥1.5 ≥2.0 |
≥5.0 ≥10.0 ≥10.0 |
≥60 ≥70 ≥80 |
|
F0121J F0122J F0123J |
0.7~1.0 | — | – | margin | ≤1.5 | ≥6.2 ≥6.4 ≥6.8 |
≥200 ≥250 ≥300 |
≥0.5 ≥0.5 ≥1.0 |
≥3.0 ≥5.0 ≥5.0 |
≥70 ≥80 ≥90 |
|
Sintered copper steel | F0201J F0202J F0203J |
0.5~0.8 | 2~4 | margin | ≤1.5 | ≥6.2 ≥6.4 ≥6.8 |
≥250 ≥350 ≥500 |
≥0.5 ≥0.5 ≥0.5 |
≥3.0 ≥5.0 ≥5.0 |
≥90 ≥100 ≥110 |
|
Sintered copper aluminum steel | E0211J E0212J |
0.4~0。7 | 2~4 | 0.5~1.0 | margin | ≤1.5 | ≥6.4 ≥6.8 |
≥400 ≥550 |
≥0.5 ≤0.5 |
≥5.0 ≥5.0 |
≥120 ≥130 |
JH MIM Powder Metallurgy plant produces pressed products of different materials, with a complete product quality inspection system and competitive prices. If you have a custom metal product project, whether it is auto parts, electronic products, gear, etc., feel free to contact JH MIM to give you the best service.