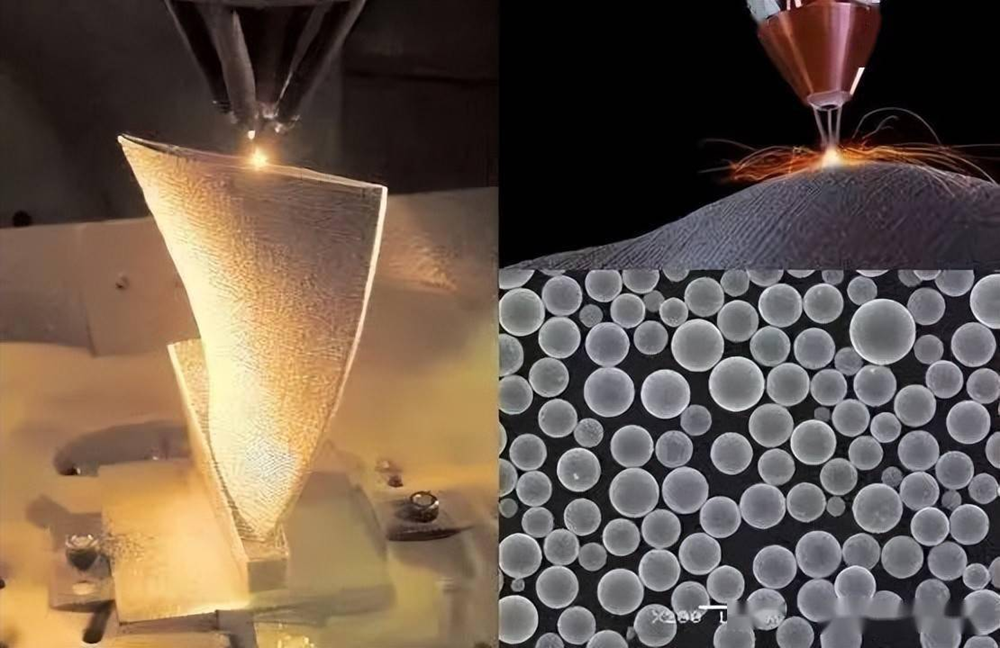
Metal powders are crucial in determining the success of powder metallurgy additive manufacturing. Their characteristics significantly influence the efficiency of manufacturing processes and the quality of the final components produced. Key factors such as particle size, shape, and material composition dictate how powders perform during production. Flowability is essential for seamless operation, while reusability is vital in maintaining cost-effectiveness. Each of these attributes requires meticulous consideration to achieve the best outcomes. By mastering these aspects, you can harness the full potential of powder metallurgy additive manufacturing to create high-quality, precise, and reliable components.
Key Takeaways
- Understand particle size’s critical role in determining printed components’ quality; aim for a median size of around 45 µm for optimal flowability and precision.
- Prioritize uniform particle distribution to enhance packing density, which reduces defects and improves the structural integrity of your components.
- Choose spherical particles for better flowability and packing density, while considering irregular particles for specific applications that require enhanced mechanical interlocking.
- Evaluate the alloy composition and purity of metal powders to ensure they meet your specific application’s mechanical, thermal, and chemical requirements.
- Implement effective recycling strategies for metal powders to reduce costs and support sustainability, while maintaining rigorous quality control to prevent degradation.
- Optimize flowability by managing factors such as particle shape, size, surface texture, and moisture content to ensure smooth operation during the manufacturing process.
- Test different powder combinations to find the ideal balance of properties that enhance the performance and reliability of your additive manufacturing projects.
Particle Size and Distribution
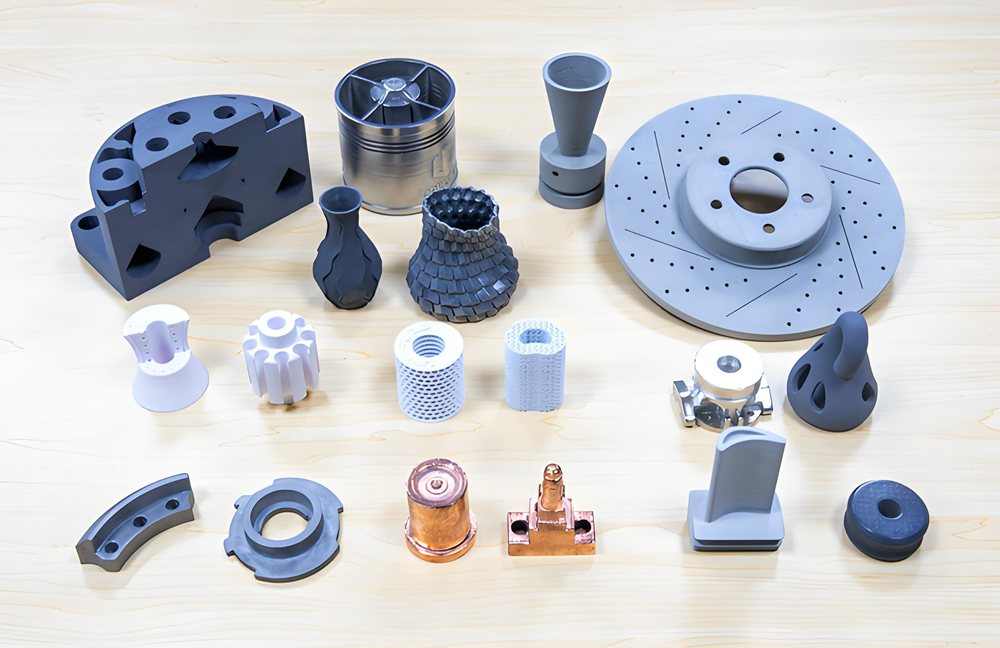
Powder Metallurgy Additive Manufacturing
Importance of Particle Size
Particle size plays a pivotal role in powder metallurgy additive manufacturing. It directly affects how powders behave during the printing process. Smaller particles often provide better surface finish and finer details in the final product. However, they may also lead to challenges like reduced flowability or increased risk of contamination. Larger particles, on the other hand, enhance flowability but might compromise the resolution of the printed components.
You must carefully select the particle size to match the requirements of your specific application. For instance, a median particle size (D50) of around 45 µm is commonly preferred in many additive manufacturing techniques. This size strikes a balance between flowability and precision. By understanding the relationship between particle size and performance, you can optimize your manufacturing process for superior results.
Uniformity in Particle Distribution
Uniform particle distribution ensures consistent performance throughout the additive manufacturing process. When particles vary significantly in size, they can create uneven packing density. This inconsistency may lead to defects such as porosity or weak mechanical properties in the final product.
A well-distributed powder allows for better packing density, which reduces voids and enhances the structural integrity of your components. Uniformity also improves the flowability of the powder, ensuring smooth operation during printing. You should always evaluate the particle size distribution of your metal powders before use. Tools like laser diffraction or sieve analysis can help you assess this critical property.
By prioritizing uniformity in particle distribution, you can achieve higher-quality outputs and reduce the likelihood of production errors.
Particle Shape
Spherical vs. Irregular Particles
The shape of metal powder particles plays a critical role in additive manufacturing. You will often encounter two primary shapes: spherical and irregular. Spherical particles are smooth and round, while irregular particles have uneven, jagged surfaces. Each type offers distinct advantages and challenges.
Spherical particles excel in flowability. Their smooth surfaces allow them to move freely through the additive manufacturing system, ensuring consistent material deposition. This characteristic makes them ideal for high-precision applications where uniformity is essential. Additionally, spherical particles tend to pack more efficiently, reducing voids and enhancing the density of the final product.
Irregular particles, on the other hand, may offer better mechanical interlocking. This feature can improve the strength of certain components. However, their uneven surfaces often hinder flowability, leading to potential disruptions during the printing process. Irregular shapes may also result in inconsistent packing, which could compromise the structural integrity of your components.
When selecting powders, you should consider the specific requirements of your application. Spherical particles are generally preferred for most additive manufacturing techniques due to their superior performance. However, irregular particles might be suitable for niche applications where their unique properties provide an advantage.
Influence on Packing Density
Particle shape directly impacts packing density, which affects the quality and strength of your printed components. Spherical particles typically achieve higher packing density because their uniform shape allows them to fit together more efficiently. This reduces voids and enhances the structural integrity of the final product.
Irregular particles, with their uneven surfaces, often create gaps when packed. These gaps can lead to porosity, which weakens the material and may cause defects. Lower packing density also affects thermal conductivity during the printing process, potentially resulting in uneven melting or sintering.
To optimize packing density, you should evaluate the shape of your metal powders carefully. Spherical particles generally provide better results, but blending them with a small percentage of irregular particles can sometimes improve mechanical properties. Testing different powder combinations can help you find the ideal balance for your specific needs.
By understanding how particle shape influences packing density, you can make informed decisions that enhance the quality and reliability of your additive manufacturing projects.
Material Composition
Alloy Composition and Purity
The composition and purity of metal powders directly influence the performance and quality of your additive manufacturing projects. Alloys which combine two or more metallic elements, offer unique properties tailored to specific applications.
Purity is equally critical. Impurities in metal powders can lead to defects such as porosity, cracking, or reduced mechanical strength in the final product. Contaminants may also affect the powder’s reactivity during the manufacturing process, compromising its performance.
When evaluating alloy composition and purity, consider the specific demands of your application. Whether you need corrosion resistance, high strength, or thermal stability, selecting the right combination of elements will help you achieve optimal results.
Tailoring Powders for Specific Applications
Customizing metal powders for specific applications allows you to unlock the full potential of additive manufacturing. Different industries, such as aerospace, automotive, and medical, require unique material properties to meet their stringent standards. For instance, aerospace components often demand lightweight materials with high strength, while medical implants require biocompatible alloys.
Tailoring powders involves adjusting factors like alloy composition, particle size, and surface treatments. You can modify these characteristics to enhance performance and meet the precise needs of your project. For example, adding trace elements to an alloy can improve its wear resistance or thermal conductivity. Similarly, surface coatings can reduce oxidation or improve bonding during the printing process.
Collaborating with material scientists or powder suppliers can help you develop customized solutions. By tailoring powders to your specific requirements, you can achieve superior performance, reduce waste, and enhance the efficiency of your powder metallurgy additive manufacturing processes.
Flowability and Packing Density
Factors Influencing Flowability
Flowability determines how easily metal powders move through the additive manufacturing system. It directly impacts the consistency and efficiency of powder deposition during the printing process. Several factors influence the flowability of powders, and understanding these can help you optimize your operations.
-
Particle Shape: Spherical particles exhibit superior flowability due to their smooth surfaces. They roll and slide more easily compared to irregular particles, which often interlock and resist movement.
-
Particle Size: Larger particles generally flow better than smaller ones. Fine powders may clump together because of higher surface area and stronger interparticle forces, reducing their ability to flow freely.
-
Surface Texture: Smooth surfaces enhance flowability, while rough or porous particles can create friction and hinder movement. Surface treatments or coatings can improve this property.
-
Moisture Content: Excess moisture can cause powders to stick together, forming clumps that disrupt flow. Keeping powders dry and storing them in controlled environments helps maintain optimal flowability.
-
Additives: Flow agents, such as silica or alumina, are sometimes added to powders to reduce friction and improve flow characteristics. These additives can be particularly useful for fine or irregular powders.
By evaluating these factors, you can identify and address flowability issues before they affect your production. Consistent flowability ensures smooth operation and reduces the risk of defects in powder metallurgy additive manufacturing.
Packing Density and Its Impact
Packing density refers to how tightly metal powder particles pack together in a given volume. It plays a crucial role in determining the quality and mechanical properties of the final product. Higher packing density minimizes voids, leading to stronger and more reliable components.
-
Impact on Structural Integrity: Dense packing reduces porosity, which enhances the strength and durability of printed parts. Low packing density, on the other hand, can result in weak spots or structural defects.
-
Thermal Conductivity: During the printing process, heat must transfer efficiently through the powder bed. High packing density improves thermal conductivity, ensuring uniform melting or sintering of the material.
-
Dimensional Accuracy: Uneven packing density can cause inconsistencies in layer thickness, affecting the precision of the printed component. Achieving uniform packing density helps maintain dimensional accuracy.
-
Powder Efficiency: Densely packed powders use space more effectively, reducing material waste. This efficiency contributes to cost savings and sustainability in manufacturing.
To optimize packing density, you should consider both particle shape and size distribution. Spherical particles with a narrow size range typically achieve the best results. However, blending powders with varying sizes can sometimes improve packing by filling gaps between larger particles. Testing different combinations allows you to find the ideal balance for your specific application.
By prioritizing flowability and packing density, you can enhance the performance and reliability of your powder metallurgy additive manufacturing processes.
Powder Recycling and Reusability
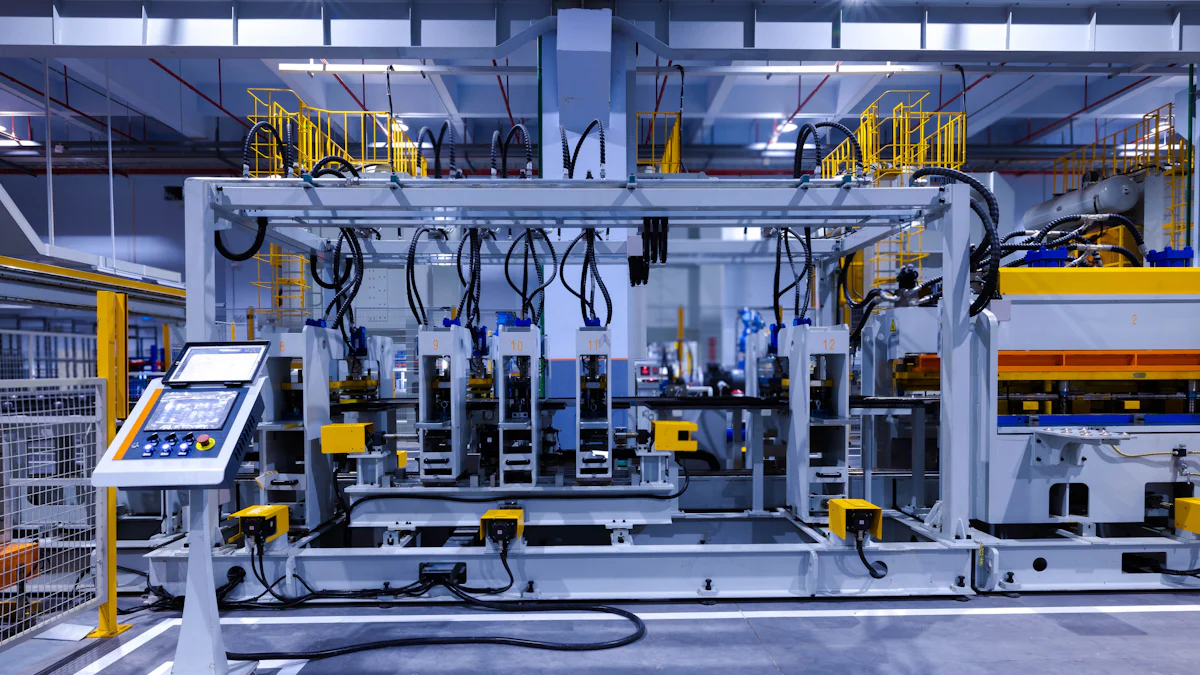
Benefits of Powder Recycling
Recycling metal powders offers significant advantages for additive manufacturing. It helps you reduce material costs, which is especially important when working with expensive alloys like titanium or nickel-based materials. By reusing powders, you can maximize the value of your resources and improve the overall cost-efficiency of your production process.
Recycling also supports sustainability efforts. It minimizes waste by repurposing unused or excess powder from previous manufacturing cycles. This approach aligns with environmentally conscious practices, which are increasingly important in modern industries. By adopting recycling strategies, you contribute to reducing the environmental impact of your operations.
Another benefit lies in maintaining a steady supply of materials. Recycling allows you to reuse powders without constantly relying on new purchases. This ensures that your production remains uninterrupted, even during supply chain disruptions. Consistent access to materials enhances your operational reliability and flexibility.
Challenges of Reusing Powders
While recycling offers many benefits, it also presents challenges that you must address to ensure successful reuse. One major concern is the potential degradation of powder quality over multiple cycles. Factors like oxidation, contamination, or changes in particle size distribution can affect the performance of recycled powders. These issues may lead to defects in the final product if not properly managed.
Another challenge involves maintaining consistent material properties. Recycled powders may exhibit variations in flowability, packing density, or chemical composition. These inconsistencies can disrupt the additive manufacturing process and compromise the quality of your components. You need to implement rigorous testing and quality control measures to mitigate these risks.
Storage conditions also play a critical role in powder reusability. Exposure to moisture, air, or extreme temperatures can degrade the powder’s characteristics. Proper storage solutions, such as sealed containers or climate-controlled environments, are essential to preserve the integrity of recycled powders.
To overcome these challenges, you should establish clear protocols for powder recycling. Regularly analyze the physical and chemical properties of your powders to ensure they meet the required standards. Collaborating with material experts or suppliers can help you develop effective recycling strategies tailored to your specific needs. By addressing these challenges, you can unlock the full potential of powder recycling while maintaining high-quality results in your additive manufacturing processes.
Selecting the right metal powder is the foundation of success in powder metallurgy additive manufacturing. You must evaluate critical factors like particle size, shape, composition, flowability, and reusability to ensure optimal results. Each characteristic directly impacts process efficiency and product quality. By mastering these elements, you can enhance performance, reduce production costs, and achieve superior outcomes. Understanding these principles empowers you to create reliable, high-quality components while maintaining a competitive edge in the industry.
FAQ
What is powder metallurgy additive manufacturing?
Powder metallurgy additive manufacturing (PMAM) is a process where metal powders are used to create components layer by layer. This technique combines the principles of powder metallurgy additive manufacturing and 3D printing to produce complex, high-precision parts.
Why is particle size important in additive manufacturing?
Particle size directly affects the performance of metal powders during the manufacturing process. Smaller particles provide finer details and smoother surface finishes but may reduce flowability. Larger particles improve flowability but can compromise resolution. Selecting the right particle size ensures optimal results for your specific application.
How does particle shape influence the manufacturing process?
The shape of metal powder particles impacts flowability, packing density, and the quality of the final product. Spherical particles flow more easily and pack more efficiently, reducing voids and enhancing structural integrity. Irregular particles may offer better mechanical interlocking but often hinder flowability and create inconsistencies.
What role does material composition play in powder metallurgy additive manufacturing?
Material composition determines the mechanical, thermal, and chemical properties of the final product. Alloys tailored for specific applications, such as titanium for lightweight strength or nickel for high-temperature resistance, ensure that components meet performance requirements. Purity also plays a critical role in preventing defects and maintaining consistent material composition.
How can you improve the flowability of metal powders?
You can enhance flowability by using spherical particles, maintaining optimal particle size, and reducing surface roughness. Storing powders in dry, controlled environments prevents moisture-related clumping. Adding flow agents like silica can further improve movement through the manufacturing system.
What is the significance of packing density in additive manufacturing?
Packing density affects the strength, durability, and precision of printed components. High packing density minimizes voids, improves thermal conductivity, and enhances structural integrity. Achieving uniform packing density ensures consistent layer thickness and reduces the risk of defects.
Can metal powders be recycled in additive manufacturing?
Yes, metal powders can be recycled to reduce costs and support sustainability. Recycling unused or excess powders from previous cycles maximizes resource efficiency. However, you must monitor for quality degradation, such as oxidation or contamination, to maintain consistent performance.
What challenges arise when reusing metal powders?
Reusing powders can lead to issues like reduced flowability, changes in particle size distribution, or contamination. These factors may affect the quality of the final product. Proper storage, rigorous testing, and quality control measures help mitigate these challenges and ensure successful reuse.
How do you select the right metal powder for your application?
To choose the right powder, evaluate factors like particle size, shape, material composition, flowability, and reusability. Consider the specific requirements of your project, such as strength, thermal stability, or corrosion resistance. Collaborating with material experts can help you make informed decisions.
What industries benefit most from powder metallurgy additive manufacturing?
Industries like aerospace, automotive, and medical benefit significantly from PMAM. Aerospace uses it for lightweight, high-strength components. Automotive manufacturers rely on it for complex parts with precise tolerances. The medical field employs it for biocompatible implants and custom prosthetics.
Pingback: How Much Does Sintered titanium 3d Printing Cost ? - China Custom Titanium Components Manufacturing