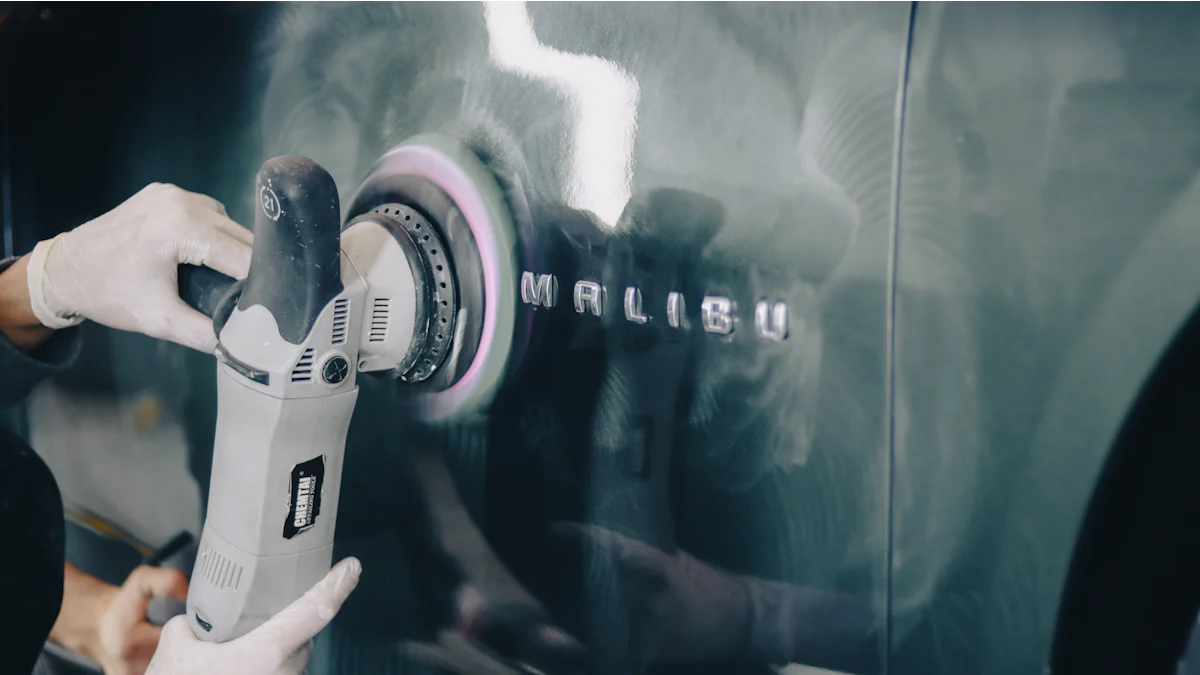
Metal injection molding parts polishing plays a crucial role in metal injection molding. It transforms parts from merely acceptable to truly exceptional. This process enhances the surface finish without altering the mechanical or chemical properties of the components. Metal injection molding parts polishing improves the appearance and boosts performance and precision. It ensures that parts are easier to clean and maintain. By refining the surface, metal injection molding parts polishing contributes significantly to the overall quality and consistency of metal injection molded parts. This step is indispensable for achieving the desired aesthetic and functional outcomes.
Key Takeaways
- Polishing is essential in metal injection molding, enhancing parts’ appearance and performance.
- Choosing the right polishing equipment, such as single-disc, double-disc, or water-sanding polishers, is crucial for achieving optimal results.
- Proper surface preparation, including cleaning and inspecting parts, lays the groundwork for a flawless finish.
- Using rough and fine polishing techniques ensures a smooth, reflective surface that meets high standards.
- Conducting thorough quality checks, including visual inspections and measuring surface smoothness, guarantees the parts meet required specifications.
- A meticulous polishing process not only improves aesthetics but also extends the lifespan and functionality of metal injection molded parts.
- Investing time in polishing can significantly enhance the quality and consistency of MIM components, making them suitable for various applications.
Best Equipment for Metal Injection Molding Parts Polishing
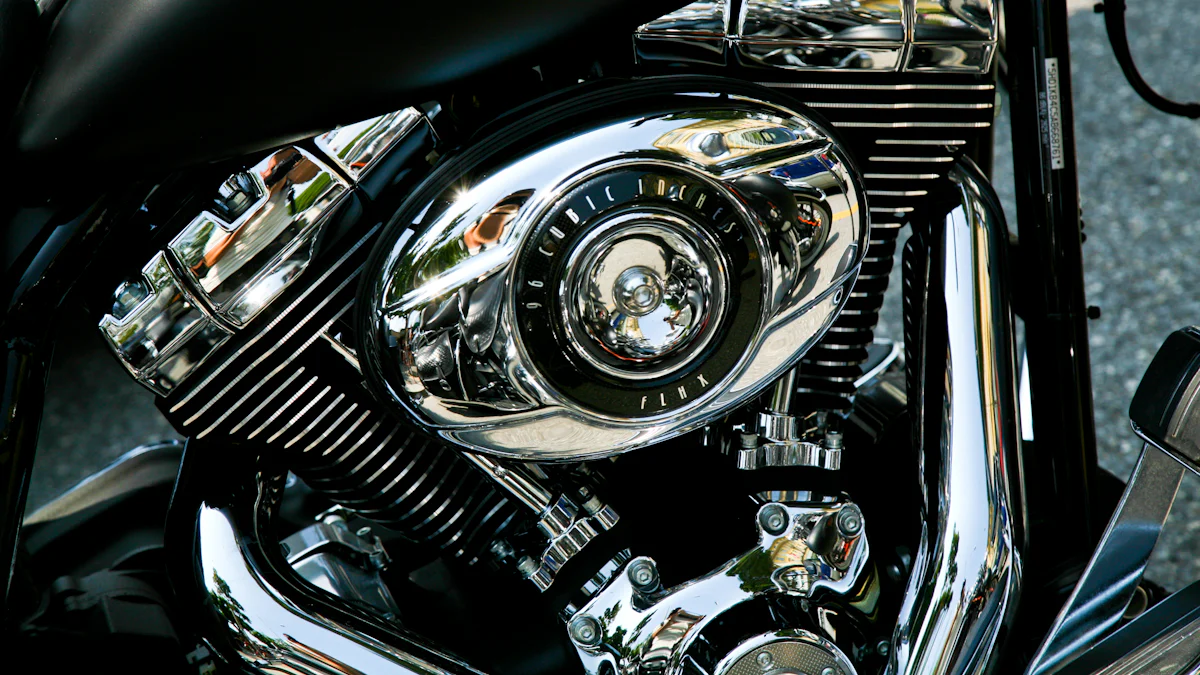
When it comes to metal injection molding parts polishing, selecting the right equipment is crucial. The choice of polisher can significantly impact the quality and efficiency of the polishing process. Here, I will discuss some of the best equipment options available for achieving optimal results.
Single-Disc Polishers
Features and Best Uses
A Single-Disc Polisher employs a single rotating disc to polish metal injection molding parts. This versatile tool is suitable for both rough and fine polishing tasks. It excels in handling various surface imperfections, making it a popular choice for many applications. The single-disc design allows for precise control, ensuring that the desired polishing effect is achieved.
Advantages and Limitations
The primary advantage of single-disc polishers lies in their simplicity and ease of use. They are ideal for straightforward polishing tasks and offer excellent maneuverability. However, they may not be as efficient for larger-scale operations or complex geometries. The single-disc design might also limit the speed at which large surfaces can be polished.
Double-Disc Polishers
Features and Best Uses
Double-Disc Polishers feature two rotating discs, which enhance the polishing process by providing more coverage and efficiency. This equipment is particularly beneficial for polishing metal injection molding parts with intricate structures. The dual-disc setup allows for simultaneous polishing of both sides of a part, reducing the overall processing time.
Advantages and Limitations
Double-disc polishers offer increased efficiency and are well-suited for high-volume production environments. They provide a balanced approach to polishing, ensuring uniformity across the surface. However, they may require more maintenance due to the complexity of having two discs. Additionally, the initial investment cost can be higher compared to single-disc polishers.
Water-Sanding Polishers
Features and Best Uses
Water-Sanding Polishers utilize water as a lubricant during the polishing process. This method is effective in reducing friction and heat, which can be beneficial for delicate metal injection molding parts. Water-sanding polishers are ideal for achieving a smooth, reflective finish on parts that require a high level of precision.
Advantages and Limitations
The use of water in the polishing process helps to minimize the risk of overheating and damage to the parts. This makes water-sanding polishers an excellent choice for sensitive materials. However, the presence of water requires additional considerations for drying and corrosion prevention. The equipment may also need more frequent cleaning to prevent water-related issues.
Methods to Achieve a Smooth, Reflective Surface on MIM Parts
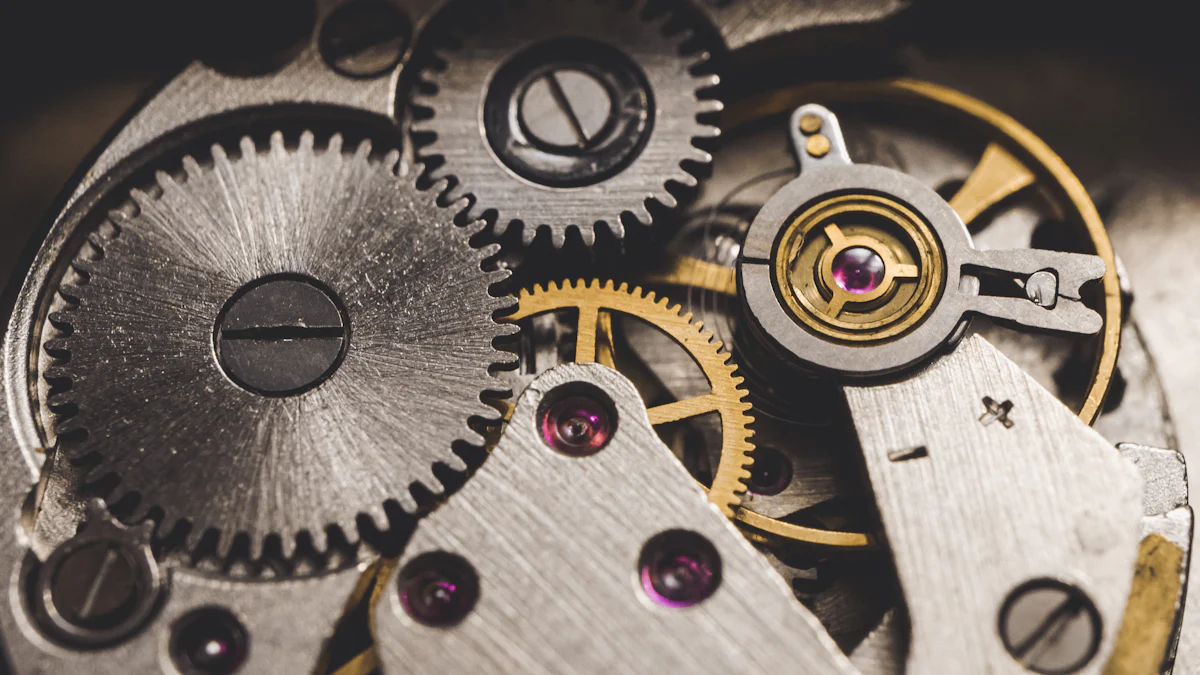
Achieving a smooth, reflective surface on metal injection molding parts requires a meticulous approach. This process not only enhances the aesthetic appeal but also improves the performance and durability of the parts. Here, I will outline the essential methods to ensure your MIM parts meet the highest standards.
Surface Preparation
Before diving into the polishing process, proper surface preparation is crucial. This step sets the foundation for achieving a flawless finish.
Cleaning and Initial Inspection
I start by thoroughly cleaning the MIM parts to remove any contaminants or residues. This step is vital because any leftover particles can interfere with the polishing process. After cleaning, I conduct an initial inspection to assess the surface condition. This inspection helps identify areas that may require special attention during polishing.
Identifying Imperfections
Once the parts are clean, I carefully examine them for imperfections such as scratches, pits, or black lines. These flaws can affect the final appearance and functionality of the parts. Identifying these imperfections early allows me to address them effectively during the polishing process.
Rough and Fine Polishing
Polishing involves two main stages: rough and fine polishing. Each stage plays a distinct role in achieving the desired surface quality.
Techniques for Rough Polishing
In the rough polishing stage, I use abrasive materials to remove surface irregularities. This step is essential for leveling the surface and preparing it for fine polishing. I often employ mechanical polishing techniques, which have proven effective in refining MIM components. The goal here is to create a uniform surface that is free from major defects.
Techniques for Fine Polishing
Fine polishing is where the magic happens. I use finer abrasives to achieve a smooth, reflective finish. This stage requires precision and patience, as it determines the final appearance of the MIM parts. Advanced polishing techniques, such as magnetic polishing, can be employed to enhance the surface quality further. These techniques ensure that the parts not only look good but also perform optimally.
Quality Checking
After polishing, quality checking is essential to ensure the parts meet the desired standards.
Visual Inspection
I begin with a visual inspection to assess the overall appearance of the parts. This step helps identify any remaining imperfections that may have been overlooked during polishing. A keen eye is necessary to spot subtle flaws that could impact the part’s performance.
Measuring Surface Smoothness
Finally, I measure the surface smoothness using specialized equipment. This measurement provides a quantitative assessment of the surface quality, ensuring that the parts meet the required specifications. Consistency in surface smoothness is crucial for maintaining the integrity and functionality of the MIM parts.
By following these methods, I ensure that metal injection molding parts polishing results in components that are not only visually appealing but also highly functional and durable. This meticulous approach is essential in meeting the rising demand for top-notch metal parts.
Polishing plays a pivotal role in metal injection molding (MIM), enhancing both the appearance and functionality of parts. By selecting the best equipment, such as single-disc, double-disc, and water-sanding polishers, I ensure optimal results. These tools, combined with meticulous methods, transform MIM parts into high-quality components. To achieve the best outcomes, I recommend focusing on surface preparation, employing advanced polishing techniques, and conducting thorough quality checks. This approach not only refines the surface but also extends the lifespan and performance of the parts, making them suitable for various applications.
FAQ
What is the role of polishing in metal injection molding?
Polishing is a crucial step in the metal injection molding (MIM) process. It transforms parts from merely acceptable to truly exceptional. This step enhances the appearance, performance, and precision of the parts. Polishing also improves cleanability and consistency, making it indispensable for achieving high-quality results.
Is MIM polishing a high labor intensity process?
Yes, MIM polishing is a high labor intensity process. It requires meticulous attention to detail and skilled labor to achieve the desired surface finish. The process involves multiple stages, each demanding precision and expertise to ensure optimal results.
Can MIM parts undergo additional treatments after polishing?
Absolutely. MIM parts can be subjected to various subsequent treatments based on technical requirements. These treatments may include thermal processing, surface finishing, straightening, machining, welding, and more. Polishing often serves as a preparatory step for these additional processes.
What equipment is best for polishing MIM parts?
The choice of equipment depends on the specific requirements of the polishing task. Single-disc polishers are ideal for straightforward tasks, while double-disc polishers offer increased efficiency for high-volume production. Water-sanding polishers are excellent for achieving a smooth, reflective finish on delicate parts.
How does polishing affect the performance of MIM parts?
Polishing significantly enhances the performance of MIM parts. By refining the surface, it reduces friction and improves corrosion resistance. This leads to better functionality and extended lifespan of the parts, making them suitable for a wide range of applications.
What are the common challenges in MIM polishing?
One of the main challenges in MIM polishing is achieving a uniform surface finish across complex geometries. The process requires careful handling to avoid introducing new imperfections. Additionally, maintaining consistency in quality across large batches can be demanding.
How do I ensure quality in MIM polishing?
To ensure quality, I recommend a thorough approach that includes proper surface preparation, advanced polishing techniques, and rigorous quality checks. Visual inspections and measuring surface smoothness are essential steps in verifying that the parts meet the required standards.
Why is surface preparation important before polishing?
Surface preparation is vital because it sets the foundation for a flawless finish. Cleaning and inspecting the parts remove contaminants and identify imperfections. This step ensures that the polishing process can proceed smoothly and effectively, leading to superior results.
What techniques are used in rough and fine polishing?
In rough polishing, abrasive materials remove surface irregularities, creating a uniform base. Fine polishing uses finer abrasives to achieve a smooth, reflective finish. Techniques like magnetic polishing can further enhance surface quality, ensuring the parts not only look good but also perform optimally.
How does polishing contribute to the overall quality of MIM parts?
Polishing plays a pivotal role in enhancing both the aesthetic and functional aspects of MIM parts. It ensures that the parts are visually appealing and meet high-performance standards. By refining the surface, polishing contributes significantly to the overall quality and consistency of metal injection molded parts.