MIM-Fe8Ni
Understanding MIM-Fe8Ni Specifications
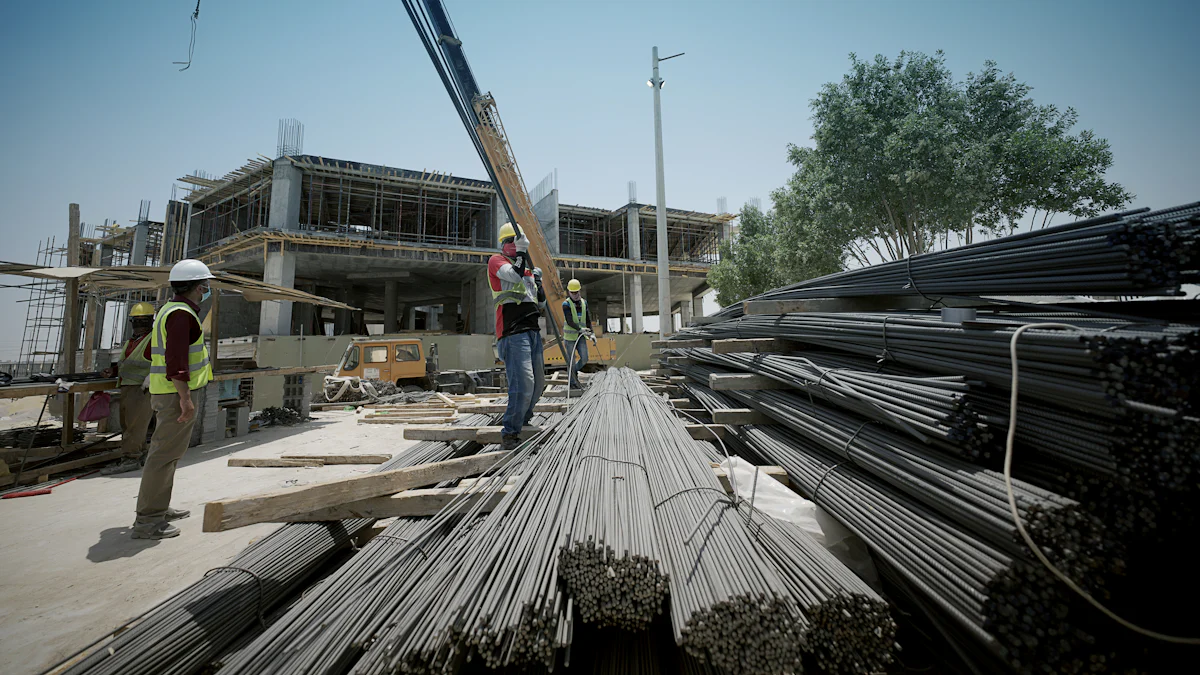
MIM-Fe8Ni, a prominent iron-nickel alloy, plays a crucial role in Metal Injection Molding (MIM). This material combines iron and nickel to create components with high precision and complexity. Its primary specifications include a nickel content ranging from 6.5% to 8.5%, with carbon levels kept below 0.1%. These specifications ensure the production of durable and reliable parts. Industries such as automotive benefit significantly from MIM-Fe8Ni, utilizing it for components like reverse gear stops in passenger cars. The alloy’s unique properties make it indispensable in applications demanding strength and precision.
Composition
Chemical Composition of MIM-Fe8Ni
Percentage of Iron
MIM-Fe8Ni primarily consists of iron, which forms the backbone of this alloy. Iron contributes to the alloy’s strength and durability, making it suitable for demanding applications. The precise percentage of iron ensures that the material maintains its structural integrity while allowing for the intricate designs achievable through Metal Injection Molding.
Percentage of Nickel
Nickel, ranging from 6.5% to 8.5%, plays a crucial role in enhancing the properties of MIM-Fe8Ni. This element improves the alloy’s corrosion resistance and toughness. Nickel’s presence allows the alloy to withstand harsh environments, making it ideal for components like reverse gear stops in passenger cars. The balance between iron and nickel is meticulously maintained to achieve the desired mechanical properties.
Additional Elements
Trace Elements
In addition to iron and nickel, MIM-Fe8Ni contains trace elements such as carbon, sulfur, and phosphorus. These elements, although present in small quantities, significantly influence the alloy’s characteristics. Carbon content remains below 0.1%, ensuring the material’s hardness and wear resistance. Sulfur and phosphorus, controlled within specific limits, contribute to the alloy’s machinability and overall performance.
Impact on Properties
The inclusion of these trace elements impacts the properties of MIM-Fe8Ni. Carbon enhances the alloy’s hardness, making it suitable for applications requiring wear resistance. Sulfur and phosphorus improve machinability, allowing for precise manufacturing processes. The careful control of these elements ensures that the alloy meets stringent performance standards, providing reliability in various industrial applications.
Mechanical Properties
Tensile Strength
Measurement Standards
Tensile strength serves as a critical indicator of a material’s ability to withstand forces that attempt to pull it apart. For MIM-Fe8Ni, industry standards such as ASTM E8/E8M guide the measurement of tensile properties. These standards ensure consistency and reliability in evaluating the material’s performance. By adhering to these guidelines, manufacturers can accurately assess the tensile strength of MIM-Fe8Ni, ensuring it meets the necessary specifications for demanding applications.
Comparison with Other Alloys
When comparing MIM-Fe8Ni to other iron-nickel alloys like Fe2Ni and Fe4Ni, notable differences emerge. Fe4Ni exhibits excellent tensile and yield strength, making it suitable for applications requiring high mechanical performance. However, MIM-Fe8Ni stands out for its specific use in components like reverse gear stops in passenger cars. This alloy balances strength with precision, offering a unique combination of properties that cater to specialized industrial needs.
Hardness
Testing Methods
Hardness testing evaluates a material’s resistance to deformation. For MIM-Fe8Ni, methods such as the Rockwell or Vickers hardness tests provide insights into its durability. These tests involve applying a specific force to the material and measuring the resulting indentation. By understanding the hardness of MIM-Fe8Ni, manufacturers can predict its wear resistance and suitability for various applications.
Relevance to Applications
The hardness of MIM-Fe8Ni directly impacts its application potential. In industries like automotive, where components endure significant stress, hardness ensures longevity and reliability. The alloy’s ability to maintain its structural integrity under pressure makes it an ideal choice for parts that require both strength and precision. This characteristic enhances its appeal across multiple sectors, including aerospace and manufacturing.
Ductility
Flexibility and Formability
Ductility refers to a material’s ability to deform under tensile stress without breaking. MIM-Fe8Ni exhibits notable ductility, allowing it to be shaped into complex forms without compromising its structural integrity. This flexibility proves advantageous in metal injection molding, where intricate designs are essential. The alloy’s formability enables the creation of detailed components, meeting the precise requirements of various industries.
Impact on Manufacturing
The ductility of MIM-Fe8Ni significantly influences manufacturing processes. Its ability to undergo deformation without fracturing facilitates efficient production of complex parts. Manufacturers benefit from reduced material waste and enhanced design possibilities. This property not only streamlines production but also contributes to cost-effectiveness, making MIM-Fe8Ni a preferred choice for high-precision applications.
Thermal Properties
Thermal Conductivity
Heat Transfer Efficiency
MIM-Fe8Ni exhibits notable thermal conductivity, which plays a crucial role in its heat transfer efficiency. This property allows the alloy to effectively dissipate heat, maintaining optimal performance even under high thermal loads. The ability to conduct heat efficiently ensures that components made from MIM-Fe8Ni remain stable and functional, reducing the risk of overheating and subsequent failure. This characteristic proves essential in applications where thermal management is critical, such as in automotive gearboxes.
Applications in High-Temperature Environments
The thermal conductivity of MIM-Fe8Ni makes it suitable for use in high-temperature environments. Industries often rely on this alloy for components that must endure elevated temperatures without compromising their structural integrity. For instance, in automotive gearboxes, MIM-Fe8Ni is used in gearboxes, where it withstands the heat generated during operation. Its ability to maintain performance under such conditions highlights its versatility and reliability in demanding applications.
Thermal Expansion
Coefficient of Expansion
The coefficient of thermal expansion (CTE) of MIM-Fe8Ni is a critical factor in its application. This measure indicates how much the material expands or contracts with temperature changes. A stable CTE ensures that the alloy maintains its dimensional accuracy, which is vital for components requiring precise tolerances. The controlled expansion of MIM-Fe8Ni prevents issues such as warping or misalignment, ensuring consistent performance across varying temperatures.
Implications for Design
Understanding the thermal expansion properties of MIM-Fe8Ni is essential for effective design. Engineers must consider the CTE when designing components to ensure compatibility with other materials and systems. The predictable expansion behavior of MIM-Fe8Ni allows for precise engineering calculations, facilitating the creation of composite parts with excellent strength and stiffness. This predictability enhances the material’s appeal in industries where precision and reliability are paramount, such as aerospace and automotive manufacturing.
Applications of MIM-Fe8Ni
Common Industries
Automotive
The automotive industry extensively utilizes MIM-Fe8Ni due to its exceptional strength and precision. Manufacturers rely on this alloy for producing components that require high durability and intricate designs. For instance, reverse gear stops in passenger cars benefit from the alloy’s ability to withstand mechanical stress while maintaining precise dimensions. This ensures reliable performance and longevity in automotive applications.
Aerospace
In the aerospace sector, MIM-Fe8Ni finds application in the production of components that demand both lightweight properties and high strength. The alloy’s ability to maintain structural integrity under extreme conditions makes it ideal for aerospace parts. Engineers value its precision and reliability, which are crucial for ensuring safety and efficiency in aerospace operations. The use of MIM-Fe8Ni in this industry highlights its versatility and adaptability to demanding environments.
Specific Uses
Component Manufacturing
MIM-Fe8Ni plays a significant role in component manufacturing across various industries. Its unique properties allow for the creation of small, complex parts with high precision. Manufacturers appreciate the alloy’s ability to produce components with tight tolerances, reducing the need for additional machining. This efficiency streamlines production processes and enhances cost-effectiveness, making MIM-Fe8Ni a preferred choice for component manufacturing.
Specialized Equipment
The production of specialized equipment often requires materials that can endure harsh conditions while maintaining performance. MIM-Fe8Ni meets these requirements, offering excellent mechanical properties and corrosion resistance. Industries such as electronics and electrical applications benefit from the alloy’s ability to produce custom iron-nickel components. Manufacturers emphasize its suitability for these applications, highlighting its adaptability and reliability in producing specialized equipment.
Advantages
Benefits Over Other Materials
Cost-Effectiveness
MIM-Fe8Ni offers significant cost advantages over other materials. Its ability to produce complex shapes with minimal waste reduces material costs. Manufacturers benefit from the efficiency of Metal Injection Molding, which allows for high-volume production at a lower cost per unit. This cost-effectiveness makes MIM-Fe8Ni an attractive option for industries seeking to optimize their manufacturing budgets without compromising on quality.
Performance Efficiency
The performance efficiency of MIM-Fe8Ni sets it apart from other alloys. Its excellent tensile and yield strength, combined with a hardness of 90 HV10, ensures that components made from this material can withstand demanding conditions. The alloy’s ability to maintain structural integrity under stress enhances its suitability for producing various MIM parts. This performance efficiency translates into reliable and durable components, meeting the stringent requirements of industries such as automotive and aerospace.
Environmental Impact
Sustainability
MIM-Fe8Ni contributes to sustainability efforts in manufacturing. The MIM process minimizes waste by utilizing nearly all the material in the production of parts. This efficient use of resources reduces the environmental footprint of manufacturing operations. Additionally, the durability and longevity of components made from MIM-Fe8Ni decrease the need for frequent replacements, further supporting sustainable practices by extending the lifecycle of products.
Recycling Potential
The recycling potential of MIM-Fe8Ni enhances its environmental appeal. Industries can recycle components made from this alloy, reducing the demand for raw materials and minimizing waste. The ability to reclaim and reuse MIM-Fe8Ni aligns with global efforts to promote circular economies. By incorporating recycled materials into new production cycles, manufacturers can contribute to environmental conservation while maintaining high-quality standards in their products.
MIM-Fe8Ni stands out as a versatile and reliable material in various industries. Its unique composition, combining iron and nickel, ensures high precision and durability. The alloy’s mechanical and thermal properties make it suitable for demanding applications, from automotive to aerospace. Understanding these specifications allows engineers to select the right material for specific needs, optimizing performance and cost-effectiveness. OptiMIM’s customizable process further enhances MIM-Fe8Ni’s appeal, offering industry-leading strength and elongation. This adaptability ensures that MIM-Fe8Ni remains a preferred choice for high-performance components.
Chemical Content
- MIM-Fe82Ni
- MIM-4605
- MIM-Fe2Ni
- MIM-2200(as sintered)
MIM-Fe82Ni | Density | UTS.Mpa | Y.S.(0.2%),Mpa | Elongation(in 25.4mm)% | Macro (apparent0 | Micro(converted) |
7.5 | 450 | / | 12 | 84 HRB | ≥50HRC |
Feed | OSF | |||||
C | Ni | Mo | Si | Fe | ||
FDC4605A | 0.4-0.6 | 1.5-2.5 | 0.2-0.5 | ≤1.00 | Bal | 1.216 |
FDC4605B | 0.4-0.6 | 1.5-2.5 | 0.2-0.5 | ≤1.00 | Bal | 1.2 |
FDC4605C | 0.4-0.6 | 1.5-2.5 | 0.2-0.5 | ≤1.00 | Bal | 1.19 |
FDC4605DE | 0.4-0.6 | 1.5-2.5 | 0.2-0.5 | ≤1.00 | Bal | 1.185 |
FDC2200MA | ≤0.10 | 1.5-2.5 | 0.2-0.5 | ≤1.00 | Bal | 1.216 |
MIM-Fe2Ni | Density | UTS.Mpa | Y.S.(0.2%),Mpa | Elongation(in 25.4mm)% | Macro (apparent0 | Micro(converted) |
7.5 | 280 | 115 | 25 | 55 HRB | ≥50HRC |
MIM-2200 | Density | UTS.Mpa | Y.S.(0.2%),Mpa | Elongation(in 25.4mm)% | Macro (apparent0 | Micro(converted) |
7.65 | 290 | 125 | 40 | 45HRB | / |