Metal injection molding and sintering represent two distinct methods for manufacturing metal parts from powders. Each process offers unique benefits and serves specific purposes. Metal injection molding excels at creating intricate, high-precision components in large quantities. Sintering, on the other hand, works better for simpler designs and smaller production runs. These differences make it essential to understand how each method functions and where they are most effective. Choosing between metal injection molding vs sintering depends on the complexity of the part, production scale, and cost considerations.
Key Takeaways
- Metal Injection Molding (MIM) is ideal for producing complex, high-precision parts in large quantities, making it suitable for industries like aerospace and medical devices.
- Sintering is a cost-effective method for simpler designs and smaller production runs, often used in electronics and consumer goods manufacturing.
- When choosing between MIM and sintering, consider factors such as part complexity, production volume, material requirements, and budget constraints.
- MIM offers high dimensional accuracy and strength, while sintered parts may require additional finishing to achieve desired surface quality.
- Prototyping and consulting with industry experts can help manufacturers make informed decisions about which method to use for their specific needs.
- Understanding the strengths and limitations of each process ensures that manufacturers align their production methods with project goals effectively.
Understanding Metal Injection Molding (MIM)
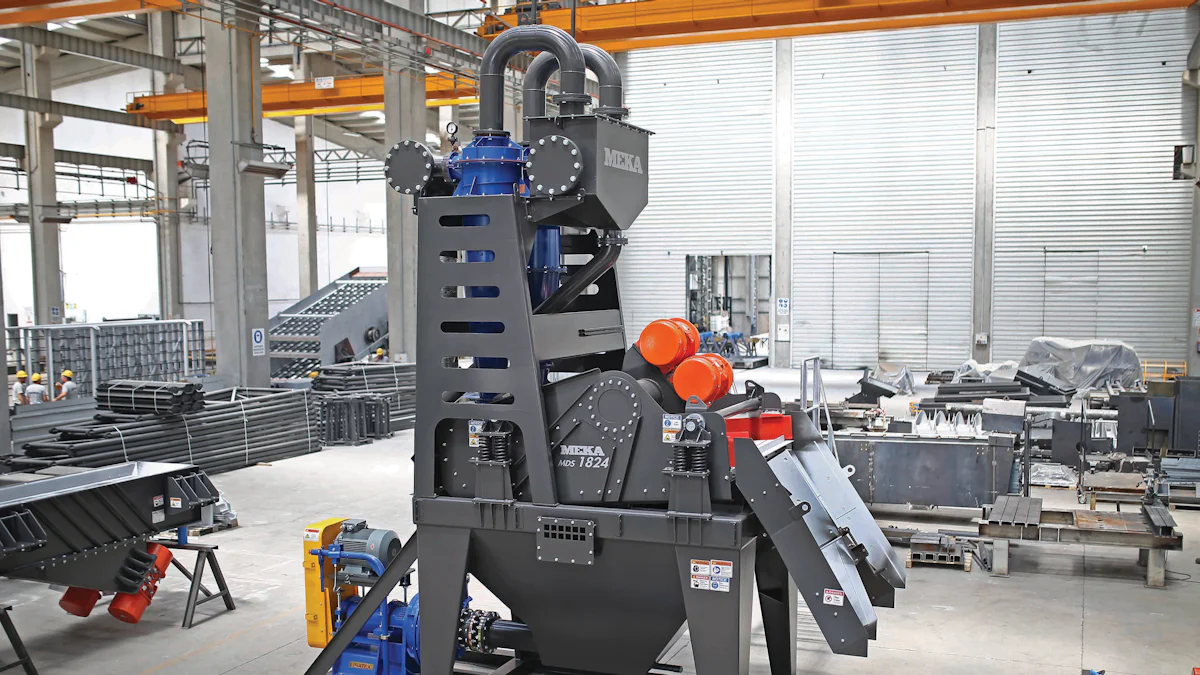
The MIM Process
Metal injection molding (MIM) combines the precision of plastic injection molding with the strength of metal. The process begins by mixing fine metal powders with a binder to create a feedstock. This feedstock is then injected into a mold cavity, forming a “green part.” After molding, the binder is removed through a debinding process, leaving behind a fragile “brown part.” The final step involves sintering, where the brown part is heated to near its melting point. This step fuses the metal particles, resulting in a dense and durable component. MIM allows manufacturers to produce complex shapes with tight tolerances, making it a preferred choice for intricate designs.
Advantages of MIM
MIM offers several benefits that make it a valuable manufacturing method: MIM offers several benefits
- Complex Geometry: MIM excels at producing parts with intricate shapes and fine details that other methods cannot achieve.
- Material Versatility: The process supports a wide range of metals, including stainless steel, titanium, and nickel alloys.
- High Precision: MIM delivers excellent dimensional accuracy, reducing the need for secondary machining.
- Mass Production: The method is highly efficient for large-scale production, lowering per-unit costs.
- Strength and Durability: Sintering enhances the mechanical properties of the final product, ensuring high strength and reliability.
These advantages make MIM an ideal solution for industries like aerospace, medical devices, and automotive manufacturing.
Limitations of MIM
Despite its strengths, MIM has certain limitations:
- High Initial Costs: The tooling and setup expenses can be significant, making it less suitable for small production runs.
- Size Constraints: MIM is better suited for small to medium-sized parts due to limitations in mold design and material shrinkage during sintering.
- Material Waste: While efficient, the process may generate some material waste during feedstock preparation and debinding.
- Longer Lead Times: The complexity of the process can result in extended production timelines compared to simpler methods like traditional sintering.
Understanding these limitations helps manufacturers decide when MIM is the right choice. comparing metal injection molding vs sintering reveals that each method serves distinct purposes, depending on the project’s requirements.
Understanding Sintering
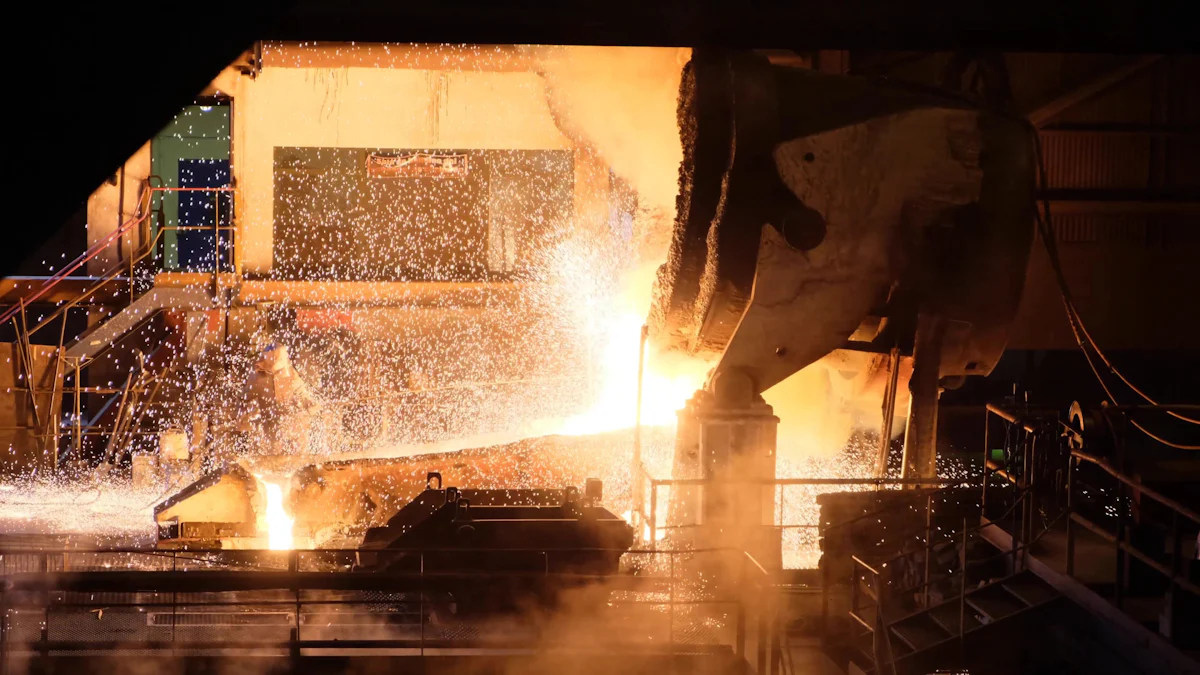
The Sintering Process
Sintering transforms powdered metal into solid components by applying heat and pressure.
Advantages of Sintering
Sintering offers several benefits that make it a practical choice for specific applications:
- Cost-Effectiveness: The process requires minimal tooling and setup costs, making it ideal for small production runs.
- Material Efficiency: Sintering minimizes material waste since unused powder can often be recycled.
- Simple Production: The method works well for straightforward designs, reducing complexity in manufacturing.
- Customizable Properties: Adjusting sintering conditions allows manufacturers to control the density, porosity, and strength of the final product.
- Energy Efficiency: Sintering consumes less energy compared to methods requiring molten metal, such as casting.
These advantages make sintering a preferred option for industries like electronics, automotive, and consumer goods.
Limitations of Sintering
Despite its benefits, sintering has limitations that may restrict its use:
- Limited Complexity: The process struggles to produce intricate shapes or fine details, unlike metal injection molding.
- Lower Strength: Sintered parts may have lower mechanical strength compared to components made through other methods.
- Size Restrictions: Large parts are challenging to produce due to difficulties in maintaining uniform density during compaction.
- Surface Finish: Sintered components often require additional finishing to achieve smooth surfaces or tight tolerances.
Understanding these limitations helps manufacturers decide when sintering is the right choice. Comparing metal injection molding vs sintering highlights how each method serves different needs based on design complexity, production volume, and cost considerations.
Comparing Metal Injection Molding and Sintering
Key Differences
Metal injection molding (MIM) and sintering differ in several key aspects, making each process suitable for specific applications. MIM involves injecting a metal-binder mixture into a mold to create complex shapes, while sintering compacts metal powders into simpler forms. MIM excels at producing intricate geometries with tight tolerances, whereas sintering works better for straightforward designs.
Additionally, MIM parts often achieve higher density and strength through advanced sintering techniques, while sintered components may have slightly lower mechanical properties.
Cost considerations further highlight their differences. MIM requires significant initial investment in tooling and equipment, making it less economical for small batches. Sintering offers a cost-effective alternative for projects with limited budgets or simpler requirements. These distinctions emphasize the importance of evaluating project needs when choosing between metal injection molding and sintering.
Applications
Aerospace manufacturers rely on metal injection molding for lightweight, high-strength components.
Sintering, by contrast, serves industries where simplicity and cost-efficiency are priorities. Electronics manufacturers use sintered parts for connectors and heat sinks. The automotive sector employs sintering for gears, bushings, and other straightforward components. Consumer goods companies also utilize sintered parts for products like tools and hardware.
Understanding these applications helps manufacturers align their production methods with project goals. Comparing metal injection molding vs sintering reveals how each process caters to different industries and design requirements.
Choosing the Right Method for Your Needs
Factors to Consider
Selecting the appropriate manufacturing method requires evaluating several critical factors. Each project has unique demands, and understanding these can guide the decision-making process.
- Part Complexity: Projects with intricate designs or fine details often benefit from metal injection molding. Sintering works better for simpler shapes with fewer geometric constraints.
- Production Volume: High-volume production aligns well with metal injection molding due to its efficiency in mass manufacturing. Sintering suits smaller production runs, where setup costs remain minimal.
- Material Requirements: The choice of material plays a significant role. Metal injection molding supports a broader range of metals, including high-performance alloys. Sintering may limit material options but offers flexibility in adjusting properties like density and porosity.
- Budget Constraints: Initial investment in tooling and equipment for metal injection molding can be substantial. Sintering provides a cost-effective alternative for projects with limited budgets.
- Mechanical Properties: Applications requiring high strength and durability often favor metal injection molding. Sintered parts may not achieve the same mechanical performance but can meet the needs of less demanding applications.
Carefully analyzing these factors ensures that manufacturers align their production methods with project goals.
Practical Recommendations
To make an informed decision, manufacturers should follow practical recommendations tailored to their specific needs:
- Prototype Testing: Before committing to a method, creating prototypes can help evaluate the feasibility of each process. Testing ensures that the chosen method meets design and performance requirements.
- Consulting Experts: Engaging with industry professionals or engineers can provide valuable insights. Their expertise helps identify the most suitable method based on technical and economic considerations.
- Balancing Cost and Quality: Manufacturers should weigh the trade-offs between cost and quality. For high-precision parts, investing in metal injection molding may yield better results. For simpler components, sintering offers a more economical solution.
- Scaling Production: For projects expected to scale over time, metal injection molding may prove more cost-effective in the long run. Sintering remains ideal for short-term or low-volume production needs.
- Evaluating Lead Times: Time-sensitive projects may require prioritizing methods with shorter production timelines. Sintering often delivers faster results for straightforward designs, while metal injection molding may involve longer lead times due to its complexity.
By following these recommendations, manufacturers can optimize their production processes and achieve desired outcomes. Understanding the strengths and limitations of each method ensures that the chosen approach aligns with project objectives.
Metal injection molding and sintering provide manufacturers with versatile solutions for creating metal components. Each method offers distinct advantages tailored to specific project needs. MIM excels in producing intricate, high-precision parts for large-scale production. Sintering, however, remains a cost-effective choice for simpler designs and smaller batches. Evaluating factors such as part complexity, production volume, and budget ensures the selection of the most suitable method. By understanding these processes, manufacturers can optimize their production strategies and achieve desired outcomes efficiently.
FAQ
What is the main difference between metal injection molding and sintering?
Metal injection molding (MIM) uses a combination of metal powders and a binder to create complex shapes through injection molding, followed by sintering. MIM excels in producing intricate designs, while sintering is better suited for straightforward shapes.
Which process is more cost-effective for small production runs?
Sintering is more cost-effective for small production runs. It requires minimal tooling and setup costs, making it an economical choice for low-volume projects. MIM involves higher initial investment in molds and equipment, which may not be justified for smaller batches.
Can both methods produce high-strength components?
Both methods can produce durable components, but MIM generally achieves higher strength and density. The advanced sintering techniques used in MIM enhance the mechanical properties of the final product. Sintered parts may have slightly lower strength due to their porosity and simpler production process.
What types of materials can be used in MIM and sintering?
MIM supports a wide range of metals, including stainless steel, titanium, and nickel alloys. This versatility allows manufacturers to meet specific material requirements.
Are there size limitations for parts produced by these methods?
Yes, both methods have size constraints. MIM is better suited for small to medium-sized parts due to mold design and material shrinkage during sintering. Sintering faces challenges in producing large parts because maintaining uniform density during compaction becomes difficult.
Which industries benefit most from MIM and sintering?
MIM serves industries requiring precision and complexity, such as aerospace, medical devices, and automotive manufacturing. Sintering benefits sectors like electronics, automotive, and consumer goods, where simplicity and cost-efficiency are priorities.
How does the surface finish compare between MIM and sintered parts?
MIM parts typically achieve a smoother surface finish with tighter tolerances, reducing the need for additional finishing. Sintered components often require post-processing to improve surface quality and meet specific dimensional requirements.
What factors should manufacturers consider when choosing between MIM and sintering?
Manufacturers should evaluate part complexity, production volume, material requirements, budget constraints, and mechanical property needs. These factors help determine which method aligns best with project goals.
Can MIM and sintering be combined in a single production process?
Yes, MIM inherently incorporates sintering as a final step to fuse metal particles and enhance part strength. However, traditional sintering does not involve the injection molding stage used in MIM.
Is one method faster than the other?
Sintering often delivers faster results for straightforward designs due to its simpler process. MIM may involve longer lead times because of the complexity of mold creation and the multi-step production process.
Pingback: What Is Additive Manufacturing of Titanium Parts - China Custom Titanium Components Manufacturing