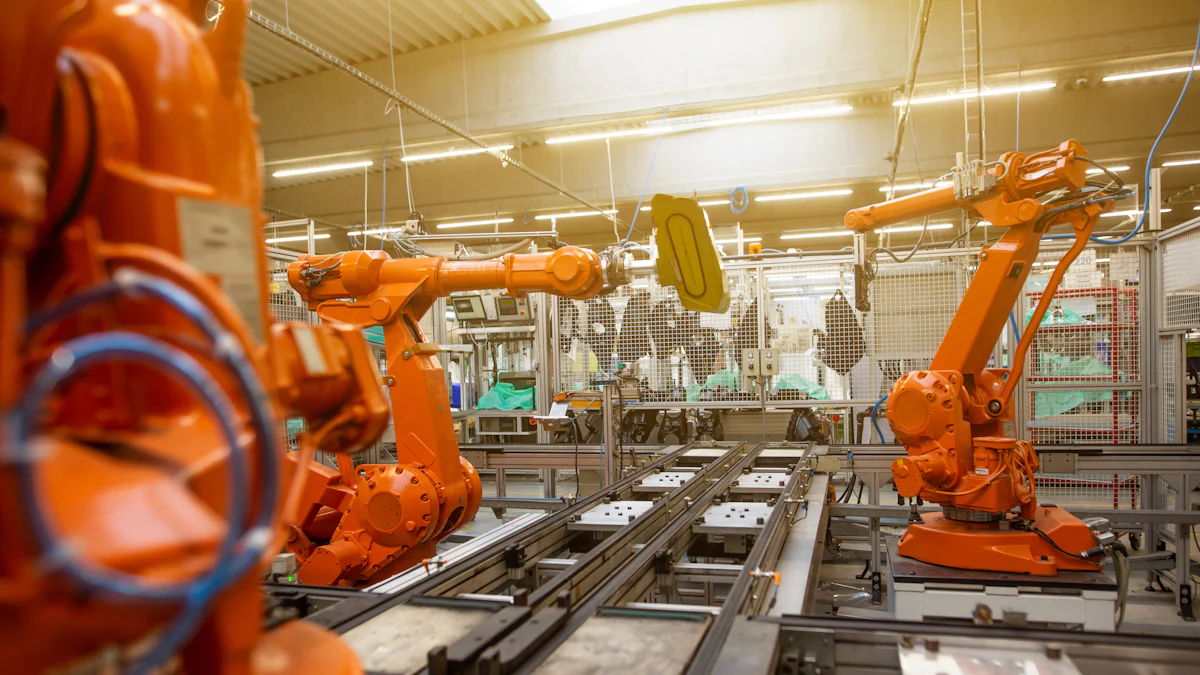
In the world of manufacturing, understanding the nuances of metal injection molding vs plastic injection molding is crucial. These two processes differ significantly in materials, methods, and applications. Metal injection molding (MIM) uses a blend of powdered metal and binder, allowing for the creation of intricate metal parts. In contrast, plastic injection molding employs plastic pellets to produce a wide range of products. The choice between these methods impacts industries like automotive, aerospace, and consumer electronics. As MIM continues to grow, with projections reaching $8.02 billion by 2030, its cost-effectiveness and scalability attract more businesses.
Key Takeaways
- Metal injection molding (MIM) is ideal for producing complex, high-strength metal parts, making it suitable for industries like automotive and aerospace.
- Plastic injection molding excels in high-volume production, offering faster cycle times and lower costs, which benefits consumer goods and electronics.
- MIM involves additional steps like debinding and sintering, resulting in longer production times than the straightforward plastic injection molding process.
- Choosing between MIM and plastic injection molding depends on your application’s specific needs, such as strength, weight, and production volume.
- Understanding the material costs and tooling investments is crucial, as MIM typically requires higher initial costs due to the precision needed for metal parts.
- Both processes have unique advantages: MIM offers superior mechanical properties, while plastic injection molding provides flexibility and efficiency in production.
- Evaluating the performance requirements of your product can guide you in selecting the most appropriate molding method for your manufacturing needs.
Overview of Metal Injection Molding
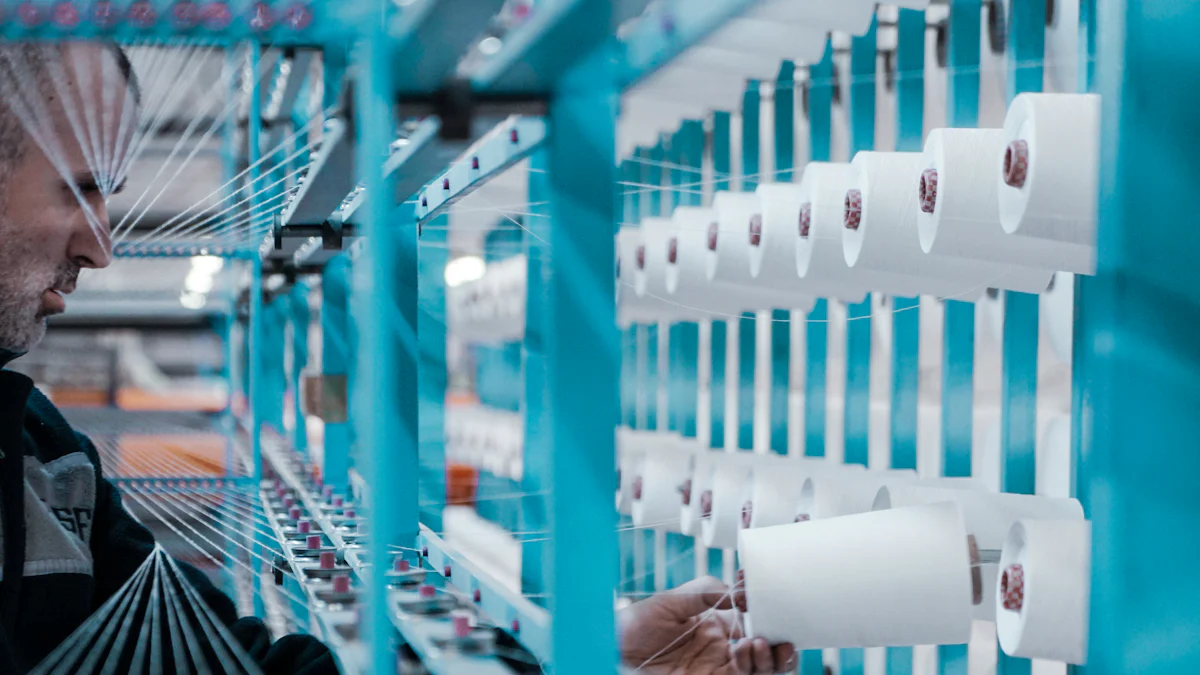
In the realm of manufacturing, Metal Injection Molding (MIM) stands out as a sophisticated process that merges the principles of plastic injection molding with the robust properties of metals. This technique allows for the production of highly complex, small to medium-sized metal components with precision and efficiency.
Process Description
Materials Used
I find that the materials used in metal injection molding are quite diverse. The process primarily involves a blend of finely powdered metals and polymer binders. This mixture forms a feedstock, which is crucial for the molding process. The choice of metal powders can vary, including stainless steel, titanium, and other alloys, depending on the desired properties of the final product.
Steps Involved
The steps involved in metal injection molding are intricate yet fascinating. Initially, the metal powders and binders are mixed to create a homogeneous feedstock. This feedstock is then granulated into pellets, which are injected into a mold under high pressure. Once the part is molded, it undergoes a debinding process to remove the binders. Finally, the part is sintered at high temperatures to achieve its final density and mechanical properties. This sequence ensures that the parts produced are dense, high-quality, and exhibit excellent surface finishes.
Common Applications
Industries Utilizing Metal Injection Molding
Metal injection molding finds its application across various industries due to its ability to produce intricate parts with tight tolerances. I have observed its significant use in the automotive industry, where it helps in manufacturing components like gears and turbocharger parts. The aerospace sector also benefits from MIM, utilizing it for producing lightweight yet strong components. Additionally, the medical field employs this process for creating surgical instruments and implants.
Types of Products Manufactured
The types of products manufactured through metal injection molding are diverse and impressive. This process excels in producing small, intricate parts with complex geometries. Products such as electronic connectors, firearm components, and dental brackets are commonly manufactured using MIM. The ability to produce parts with thin walls and detailed features makes it a preferred choice for many manufacturers.
Overview of Plastic Injection Molding
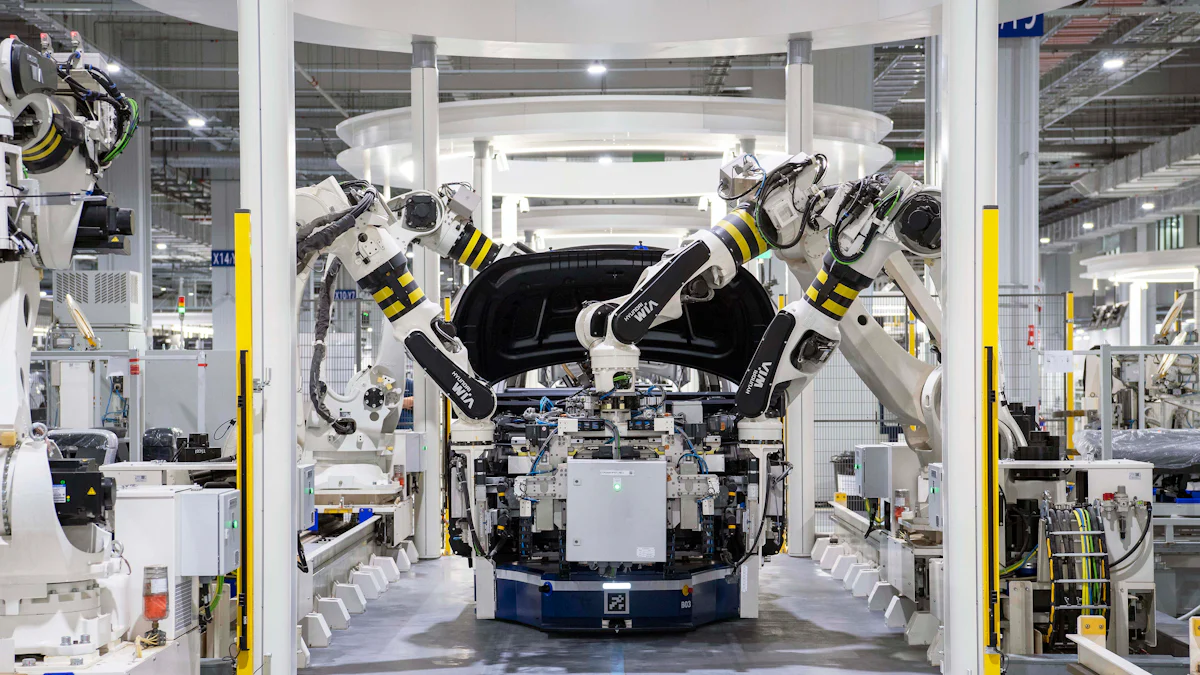
In the manufacturing landscape, Plastic Injection Molding emerges as a versatile and efficient process. It allows for the creation of a wide array of plastic products, ranging from simple to complex shapes. This method stands out due to its ability to produce high volumes of parts with consistent quality.
Process Description
Materials Used
I find that the materials used in plastic injection molding are primarily thermoplastics. These include common polymers such as polyethylene, ABS, nylon, polypropylene, and TPU. Each material offers unique properties, making it suitable for different applications. For instance, ABS is known for its strength and toughness, while polypropylene provides excellent chemical resistance.
Steps Involved
The steps involved in plastic injection molding are straightforward yet effective. Initially, the chosen plastic material is melted into a liquid state. This molten plastic is then injected into a mold cavity under high pressure. The mold defines the shape of the final product. Once the plastic cools and solidifies, the mold opens, and the finished part is ejected. This cycle repeats, allowing for rapid production of identical parts.
Common Applications
Industries Utilizing Plastic Injection Molding
Plastic injection molding finds its place in numerous industries due to its adaptability and efficiency. I have observed its extensive use in the automotive industry for producing dashboards and interior components. The electronics sector also benefits, using this process to manufacture housings for devices. Additionally, the consumer goods industry relies on it for creating household items and packaging solutions.
Types of Products Manufactured
The types of products manufactured through plastic injection molding are diverse and impressive. This process excels in producing items with intricate shapes and detailed features. Common products include plastic housings for electrical components, car dashboards, and home appliances. The ability to create parts with thin walls and complex geometries makes it a preferred choice for many manufacturers.
Comparative Analysis
Process Differences
Complexity and Precision
In my experience, metal injection molding (MIM) offers a remarkable ability to produce parts with complex geometries and tight tolerances. This process excels in creating intricate metal components that require high precision. The combination of powdered metal and binders allows for the consolidation of multiple components into a single part, reducing assembly time and enhancing structural integrity. On the other hand, plastic injection molding is well-suited for intricate shapes but does not match the precision level of MIM. It provides flexibility in mold design, which is beneficial for producing a wide range of products.
Production Speed
When it comes to production speed, plastic injection molding takes the lead. The process is efficient for high-volume production, offering shorter lead times compared to metal injection molding. The rapid cycle times in plastic molding make it ideal for industries that demand quick turnaround times. In contrast, MIM involves additional steps like debinding and sintering, which can extend the production timeline. However, the high-quality surface finish and mechanical properties achieved through MIM often justify the longer production process.
Material Considerations
Strength and Durability
From my observations, metal injection molding provides superior strength and durability compared to plastic injection molding. The metal components produced through MIM exhibit excellent mechanical properties, making them suitable for applications requiring high strength and wear resistance. This advantage is particularly evident in industries like automotive and aerospace, where durability is crucial. Plastic injection molding, while offering a broad range of material options, cannot match the inherent strength of metal parts. However, it remains a viable choice for applications where flexibility and lightweight properties are more important.
Flexibility and Weight
Plastic injection molding shines in terms of flexibility and weight. The process allows for the creation of lightweight parts, which is advantageous in industries such as consumer electronics and automotive. The variety of thermoplastics available provides options for achieving specific characteristics like chemical resistance or impact strength. Metal injection molding, while offering robust components, results in heavier parts. This weight factor can be a limitation in applications where minimizing mass is essential.
Advantages and Disadvantages
Metal Injection Molding Pros and Cons
Pros:
- High precision and tight tolerances
- Excellent mechanical properties
- Ability to produce complex geometries
Cons:
- Longer production times
- Higher initial investment due to tooling and sintering processes
Plastic Injection Molding Pros and Cons
Pros:
- Efficient for high-volume production
- Shorter lead times
- Flexibility in material selection and mold design
Cons:
- Lower strength and durability compared to metal
- Limited to applications where lightweight properties are prioritized
Cost Considerations
When evaluating metal injection molding (MIM) and plastic injection molding, cost plays a crucial role. I have found that understanding the financial implications of each process helps in making informed decisions.
Initial Investment
Tooling Costs
Tooling costs can significantly impact the initial investment in both metal and plastic injection molding. In my experience, metal injection molding requires more expensive tooling due to the need for high precision and durability. The molds must withstand the high pressures and temperatures involved in the process. Conversely, plastic injection molding typically involves lower tooling costs. The materials used for plastic molds are often less costly, making it a more accessible option for businesses with budget constraints.
Material Costs
Material costs also vary between the two processes. Metal injection molding uses a blend of powdered metals and binders, which can be more expensive than the thermoplastics used in plastic injection molding. The choice of metal powders, such as stainless steel or titanium, further influences the cost. Plastic materials, like polyethylene or polypropylene, generally offer a more economical solution. However, the specific application and required properties of the final product will dictate the most cost-effective material choice.
Production Costs
Volume and Scale
Production costs are heavily influenced by the volume and scale of manufacturing. Plastic injection molding excels in high-volume production, offering economies of scale that reduce the cost per unit. The rapid cycle times and ability to produce large quantities efficiently make it ideal for mass production. Metal injection molding, while capable of producing intricate parts, may incur higher costs for smaller production runs. The additional steps involved, such as debinding and sintering, contribute to these costs.
Efficiency and Waste
Efficiency and waste management are critical factors in production costs. Plastic injection molding is known for its efficiency, with minimal material waste due to the recyclability of thermoplastics. The process allows for the reuse of excess material, reducing overall waste. Metal injection molding, on the other hand, involves more complex steps that can lead to higher waste levels. The removal of binders and the sintering process may result in material loss, impacting the overall cost-efficiency of the method.
In this exploration of metal injection molding vs plastic injection molding, I have highlighted the distinct advantages and limitations of each process. Metal injection molding excels in producing complex, high-strength components, while plastic injection molding offers efficiency and flexibility for high-volume production. When choosing between these methods, consider the specific needs of your application. For intricate metal parts, MIM provides precision and durability. For lightweight, cost-effective solutions, plastic injection molding is ideal. Understanding the performance of materials like aluminum and steel in molds can further guide your decision-making process.
FAQ
What are the differences between metal injection molding and die casting?
Metal injection molding (MIM) and die casting serve different purposes in manufacturing. MIM excels in producing small, intricate metal parts with high precision. It combines powdered metal with a binder to create complex shapes. Die casting, on the other hand, involves forcing molten metal into a mold under high pressure. This method is ideal for larger parts with simpler geometries. Both processes are widely used across industries, and some manufacturers even employ both methods to meet diverse production needs.
How does plastic injection molding compare to die casting in terms of cost-effectiveness?
Plastic injection molding is generally more cost-effective than die casting, especially for mass production. The process allows for the rapid creation of large quantities of identical parts, reducing the cost per unit. Die casting, while efficient for certain applications, often involves higher material and tooling costs. For projects focused on budget efficiency, plastic injection molding offers a more economical solution.
What are the future prospects of metal injection molding?
Metal injection molding holds promising potential for the future. As technology advances, MIM continues to expand its applications across various industries. Its ability to produce high-quality, complex metal parts makes it an attractive option for sectors like automotive, aerospace, and medical devices. With ongoing innovations, the market for metal injection molding is expected to grow, offering new opportunities for manufacturers.
What are the similarities and differences between metal injection molding and plastic injection molding?
Both metal and plastic injection molding share a similar injection stage. They involve injecting a plasticized raw material or feedstock into a mold cavity at high pressure. However, the key difference lies in the post-processing. Metal injection molding requires additional steps like debinding and sintering to achieve the final product’s density and mechanical properties. Plastic injection molding, in contrast, involves cooling and solidifying the molten plastic, making it a faster process overall.
How should I choose between plastic injection molding and die casting based on part functionality?
When deciding between plastic injection molding and die casting, consider the part’s functionality. Evaluate the specific requirements of the part, such as strength, weight, and complexity. Compare the pros and cons of each method in relation to these needs. For lightweight and flexible parts, plastic injection molding may be more suitable. For parts requiring high strength and durability, die casting could be the better choice. Analyzing the part’s functionality simplifies the selection process.