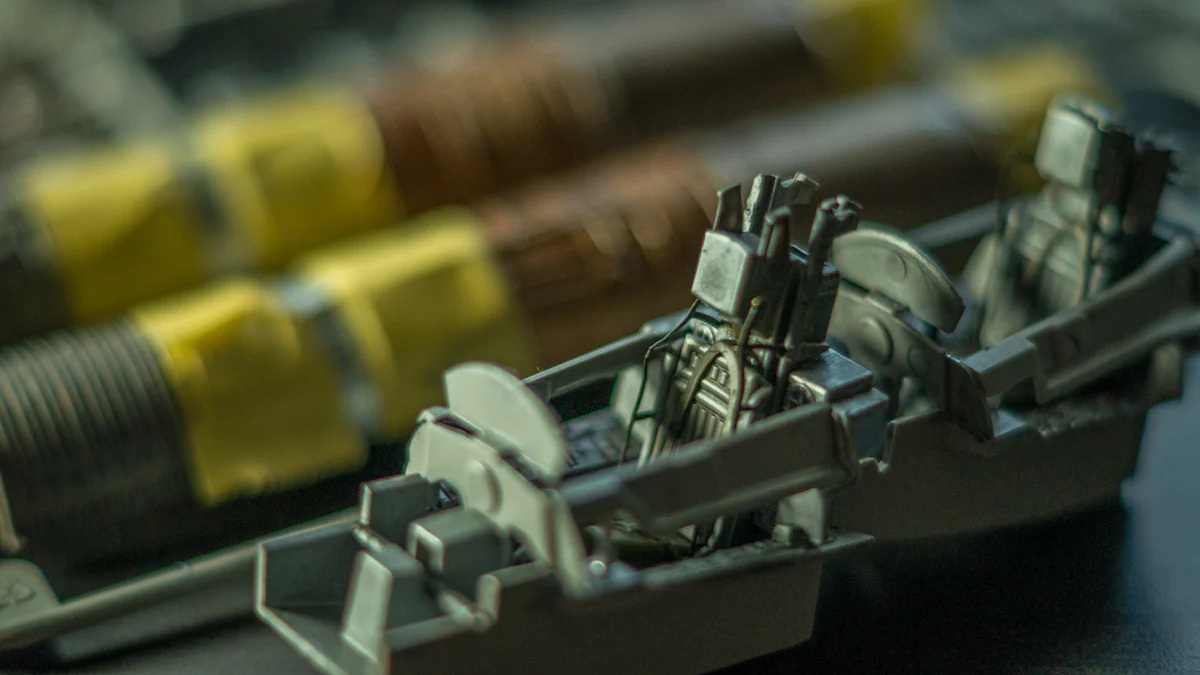
Transitioning from machining to MIM for precision and cost savings offers significant advantages. Metal Injection Molding (MIM) excels in producing complex components with high accuracy, often achieving 95% to 98% of theoretical density at a lower cost than machined parts. This process minimizes material waste and reduces tooling expenses, making it a cost-effective choice for high-volume production. Industries increasingly adopt MIM for its ability to create intricate designs without the need for post-machining operations, optimizing both material usage and production efficiency.
Key Takeaways
- MIM offers significant cost savings and precision, making it ideal for high-volume production of complex parts.
- The MIM process minimizes material waste, enhancing both cost-effectiveness and environmental sustainability.
- Early collaboration in the design phase is crucial for optimizing components for MIM, ensuring they meet performance requirements.
- MIM allows for intricate designs and features that traditional machining cannot achieve, providing greater design flexibility.
- While initial setup costs for MIM can be high, the process becomes more economical with increased production volumes.
- MIM’s ability to produce high-strength components with minimal secondary operations leads to faster time-to-market.
- Choosing MIM over traditional machining depends on part complexity, production volume, and specific application needs.
Understanding the MIM Process
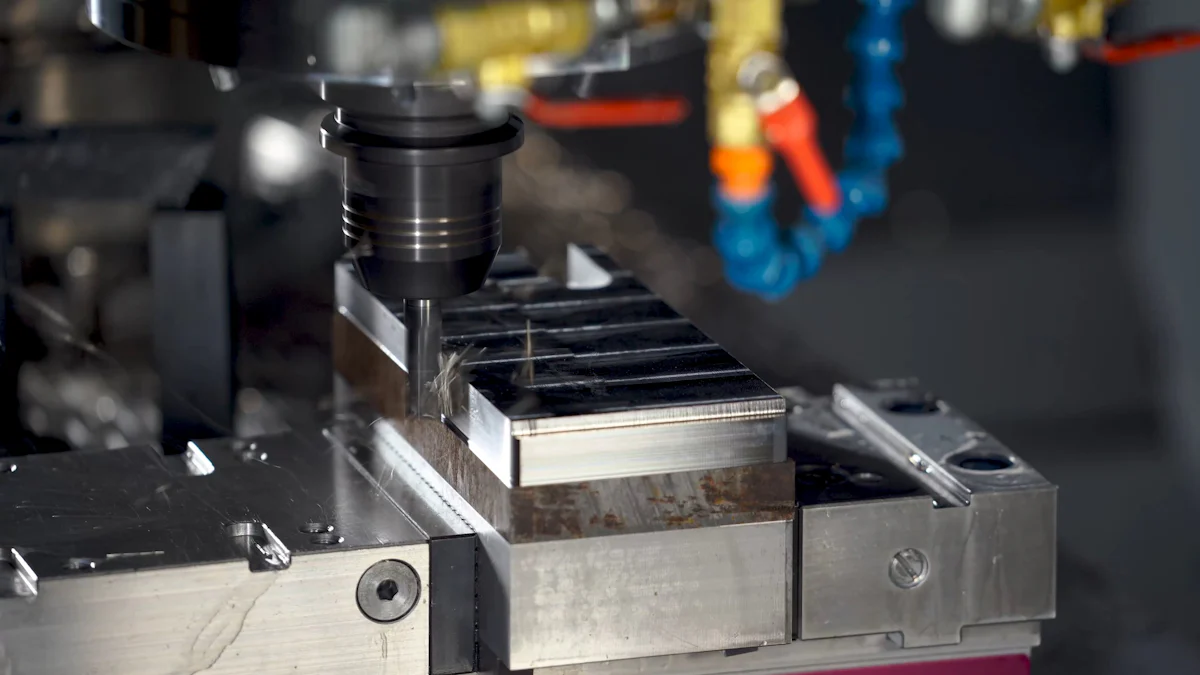
What is Metal Injection Molding?
Metal Injection Molding (MIM) combines the design flexibility of plastic injection molding with the strength and integrity of metal. This innovative process allows for the production of small, complex parts that would be challenging or costly to create using traditional methods like machining or casting. MIM uses a mixture of powdered metal and a polymer binder to form a feedstock, which is then injected into a mold. This technique enables the creation of intricate geometries and features, such as threads and cavities, that are difficult to achieve with other manufacturing processes.
Key Steps in the MIM Process
The MIM process involves several critical steps to transform raw materials into finished components:
-
Feedstock Preparation: The process begins by mixing fine metal powders with a thermoplastic binder to create a homogeneous feedstock. This mixture is granulated into pellets suitable for injection molding.
-
Injection Molding: The feedstock is heated and injected into a mold cavity, forming a “green part” that retains the shape of the final component but is not yet fully dense.
-
Debinding: The binder is removed from the green part through a thermal or solvent process, leaving behind a porous structure known as the “brown part.”
-
Sintering: The brown part undergoes sintering, where it is heated to a temperature below the melting point of the metal. This step fuses the metal particles, resulting in a dense, solid metal part with excellent mechanical properties.
-
Finishing: Depending on the application, additional finishing processes such as machining, coating, or heat treatment may be applied to achieve the desired specifications.
Advantages of MIM in Manufacturing
MIM offers several advantages over traditional manufacturing methods, making it an attractive option for industries requiring precision and cost savings:
-
Complex Geometries: MIM excels at producing parts with intricate designs and tight tolerances, which are often impossible or expensive to achieve with conventional machining.
-
Material Efficiency: The near net-shape capability of MIM minimizes material waste, reducing costs and environmental impact.
-
High Volume Production: MIM is ideal for high-volume manufacturing, providing consistent quality and repeatability across large production runs.
-
Cost-Effectiveness: While the initial setup costs for MIM can be high, the process becomes more economical with increased production volumes, offering significant savings compared to traditional methods.
By transitioning from machining to MIM for precision and cost savings, manufacturers can benefit from these advantages, enhancing both product quality and production efficiency.
Comparing MIM and Traditional Machining

When considering manufacturing methods, Metal Injection Molding (MIM) and traditional machining offer distinct advantages and limitations. Understanding these differences helps in choosing the right process for specific applications.
Volume Production Capabilities
MIM shines in high-volume production scenarios. It efficiently produces small, intricate parts with complex geometries. This method excels in creating components that would be challenging or costly to machine. MIM’s ability to produce parts in large quantities without compromising quality makes it ideal for industries requiring mass production. In contrast, traditional machining is more suited for smaller production runs or when producing larger parts with simpler designs. Machining provides excellent control and flexibility, but it becomes less cost-effective as production volumes increase.
Material and Properties Considerations
MIM offers a wide range of material options, allowing for the creation of parts with excellent mechanical properties. The process achieves high density and consistency, making it suitable for applications demanding precision and strength. MIM can handle various materials, including stainless steel, titanium, and other alloys, providing versatility in manufacturing. On the other hand, traditional machining offers more control over the material properties during the manufacturing process. It is often preferred for applications where specific material characteristics are critical, especially for larger components.
Design Complexity and Flexibility
One of MIM’s standout features is its ability to produce highly complex parts with intricate designs. The process allows for significant design freedom, enabling the creation of components with features like undercuts, threads, and thin walls. This capability reduces the need for secondary operations, saving time and costs. Traditional machining, while offering precision and control, may struggle with complex geometries. It is better suited for simpler designs or when modifications are needed during production. Machining provides flexibility in prototyping and small-scale production, where design changes are frequent.
When MIM is More Advantageous
High Volume Production Scenarios
In high-volume production scenarios, Metal Injection Molding (MIM) stands out as a superior choice. I find that MIM efficiently produces small, intricate parts with complex geometries. This capability makes it ideal for industries requiring mass production. Unlike traditional machining, which becomes less cost-effective as production volumes increase, MIM maintains consistent quality and repeatability across large production runs. The process minimizes material waste and lowers tooling costs, making it a more economical option for high-volume manufacturing. By transitioning from machining to MIM for precision and cost savings, manufacturers can achieve significant advantages in both efficiency and cost-effectiveness.
Cost-Efficiency in Manufacturing
MIM offers unparalleled cost-efficiency in manufacturing. I have observed that the process excels in producing highly complex and precise parts with excellent mechanical properties. MIM reduces the need for costly secondary operations, such as machining, which further enhances cost savings. While the initial setup costs for MIM can be high, the process becomes more economical with increased production volumes. This makes MIM a competitive alternative for manufacturers seeking to optimize their production costs. By leveraging MIM’s capabilities, companies can produce complex and high-precision metal components at a fraction of the cost compared to traditional methods.
Design Flexibility and Innovation
The design flexibility and innovation offered by MIM are unmatched. I appreciate how MIM allows for significant design freedom, enabling the creation of components with features like undercuts, threads, and thin walls. This capability reduces the need for secondary operations, saving time and costs. MIM’s ability to produce intricately shaped parts and small precision components with complicated design geometry makes it more advantageous than machining for certain applications. The process supports innovation by allowing designers to explore new possibilities without the constraints of traditional manufacturing methods. By embracing MIM, manufacturers can push the boundaries of design and achieve greater product differentiation.
Importance of Early Collaboration in Design
Optimizing Design for MIM
I have found that early collaboration in the design phase is crucial for optimizing components for Metal Injection Molding (MIM). By engaging with design engineers from the outset, we can ensure that the parts meet the necessary form-fit-function requirements. This proactive approach allows us to address potential challenges before they become costly issues.
In my experience, early collaboration helps in selecting the right materials and designing for manufacturability. We can tailor the design to leverage MIM’s strengths, such as its ability to produce complex geometries. This ensures that the final product not only meets performance criteria but also benefits from the cost efficiencies inherent in the MIM process.
Collaborative Design Process Benefits
The benefits of a collaborative design process extend beyond mere optimization. When I work closely with other engineers and stakeholders, we create a synergy that enhances innovation and efficiency. This collaboration fosters a deeper understanding of the project goals and constraints, leading to more informed decision-making.
-
Enhanced Innovation: By pooling our expertise, we can explore creative solutions that might not emerge in isolation. This collective brainstorming often leads to innovative designs that push the boundaries of what’s possible with MIM.
-
Improved Efficiency: Early collaboration streamlines the development process. We can identify and mitigate risks early, reducing the likelihood of costly redesigns or production delays.
-
Cost Savings: By aligning the design with MIM capabilities from the start, we minimize the need for secondary operations. This alignment translates into significant cost savings and a faster time-to-market.
“Collaboration early in the development cycle can ensure a component produced through metal injection molding meets the form-fit-function requirements,” as noted by engineers with expertise in both MIM and machining processes.
Transitioning from machining to MIM for precision and cost savings offers numerous advantages. MIM excels in producing small, intricate parts with complex geometries that traditional machining struggles to achieve. This process not only enhances design freedom but also consolidates parts, reducing assembly needs. The ability to produce high-strength components with minimal material waste makes MIM a cost-effective choice for high-volume production. By embracing MIM, manufacturers can achieve superior precision and significant cost savings, making it an ideal solution for industries seeking efficiency and innovation.
FAQ
What is Metal Injection Molding (MIM)?
Metal Injection Molding (MIM) combines the flexibility of plastic injection molding with the strength of metal. This process allows for the production of small, complex parts that are challenging to create using traditional methods like machining or casting. MIM uses a mixture of powdered metal and a polymer binder to form a feedstock, which is then injected into a mold.
How does MIM compare to other manufacturing techniques?
MIM excels in producing high-volume, complex metal components that fit in the palm of your hand. It is suitable for many common alloys and unique alloys developed for specific applications. For simple geometries, other techniques like press-sinter, turn parts, and stamping might be more cost-effective. However, when it comes to high-volume machining of complex geometries or applications requiring high mechanical properties, MIM stands out as the most cost-effective option.
Are you looking to manufacture metal parts but confused between MIM and machining?
Choosing between MIM and machining depends on factors like part complexity, production volume, material selection, and cost. MIM is ideal for creating complex, small, and intricate parts. Machining suits larger parts or those with simple geometries. Ultimately, the choice hinges on the specific needs of the application, and manufacturers should evaluate both methods carefully.
What are the key advantages of using MIM?
MIM offers several advantages, including the ability to produce parts with intricate designs and tight tolerances. It minimizes material waste and is ideal for high-volume manufacturing, providing consistent quality across large production runs. While initial setup costs can be high, MIM becomes more economical with increased production volumes.
Can MIM handle different materials?
Yes, MIM can handle a wide range of materials, including stainless steel, titanium, and other alloys. This versatility makes it suitable for applications demanding precision and strength. The process achieves high density and consistency, making it a reliable choice for various industries.
What is the importance of early collaboration in MIM design?
Early collaboration in the design phase is crucial for optimizing components for MIM. Engaging with design engineers from the outset ensures that parts meet necessary form-fit-function requirements. This proactive approach helps address potential challenges before they become costly issues, enhancing both innovation and efficiency.
How does MIM support design flexibility and innovation?
MIM allows for significant design freedom, enabling the creation of components with features like undercuts, threads, and thin walls. This capability reduces the need for secondary operations, saving time and costs. By embracing MIM, manufacturers can push the boundaries of design and achieve greater product differentiation.
Is MIM suitable for high-volume production scenarios?
Absolutely. MIM shines in high-volume production scenarios, efficiently producing small, intricate parts with complex geometries. Unlike traditional machining, which becomes less cost-effective as production volumes increase, MIM maintains consistent quality and repeatability across large production runs.
What are the cost-efficiency benefits of MIM?
MIM offers unparalleled cost-efficiency in manufacturing. It reduces the need for costly secondary operations, such as machining, which further enhances cost savings. While the initial setup costs for MIM can be high, the process becomes more economical with increased production volumes, making it a competitive alternative for manufacturers.
How does MIM contribute to environmental sustainability?
MIM’s near net-shape capability minimizes material waste, reducing costs and environmental impact. By optimizing material usage and production efficiency, MIM supports sustainable manufacturing practices, making it an environmentally friendly choice for high-volume production.