Overview: How Metal Injection molding Service works?
The Basics of Metal Injection Molding Services
Metal powder injection molding is one of the most commonly used manufacturing processes for making metal parts. Because the powder injection molding process has the characteristics of high precision, repeatability, high product stability, low cost, and fast speed, it is widely used in the manufacture of various products and parts. The products serve electronic products, household appliances, mechanical equipment, medical equipment, the military industry, the aerospace industry, etc.
How MIM Metal Injection Molding Works?
Clamping: The two sides of the mim mold are combined and closed.
Injection: The powder material is fed into the machine through the feed port and pushed to the mold under pressure
Melt: The molten material in a fluid state is then injected into the mold
Cooling: The material in the mold, cools and solidifies into the shape of the part.
Ejection: After the part has cooled, it is ejected from the mold.
Sintering process
Degreasing
Degreasing methods are divided into degreasing solvent degreasing + thermal degreasing and degreasing siphon – thermal degreasing two ways, the adhesive in the green product is separated from the product.
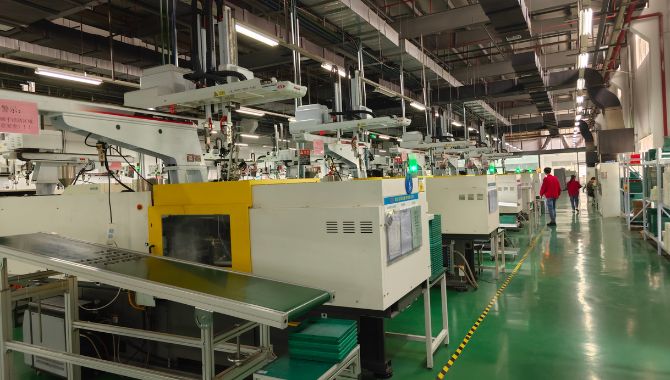
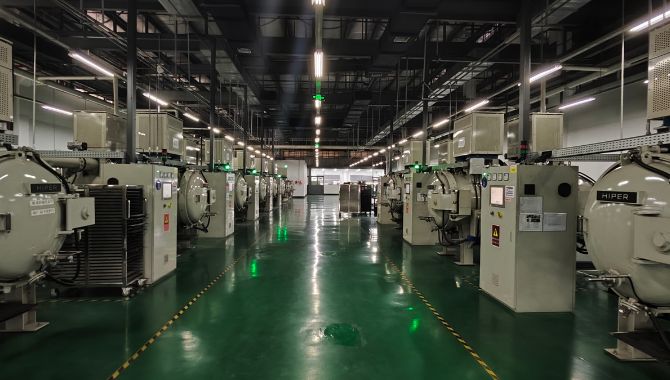
MIM Sintering
through the vacuum sintering furnace, the product is sintered and hardened, and the pores formed after shrinking and degreasing are formed to form the final product.
Shaping
some stainless steel materials (such as SUS 316L,17-4PH steel,420 stainless steel, and so on), are prone to deformation after the sintering process, and it is necessary to correct the deformed part by shaping.
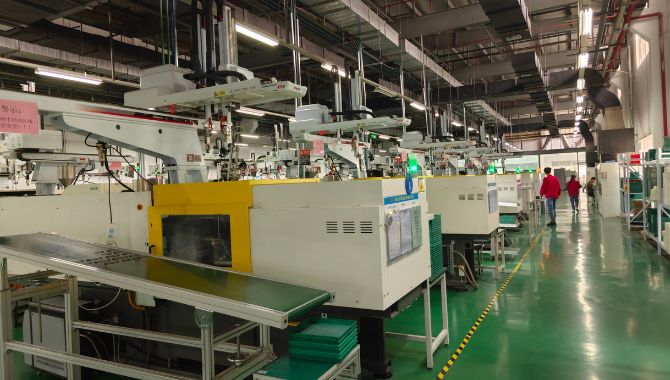
Advantages and Disadvantages of Metal Injection Molding Services
Advantages of injection molding
Material:
We offer many powder metal materials available:
Stainless steel: SUS 304L , Stainless steel 316L,420ss ,steel 440,sus630,17.4ph
iron:4605 steel
titanium:TC21 TC17 TC18
ceramics: zirconia, Aluminium oxide
High-precision and high-density
Compared with the traditional powder metallurgy process, it can provide products with higher density, better product physical properties, smaller tolerances, and higher precision.
low cost
Due to marginal benefits, the cost of producing more than 5,000 pieces of products is much lower than the cost of CNC-processed products,
Stability
Because the industry is produced through molds, it has a high degree of consistency and can ensure the stability of product batches.
Quick
Rapid prototyping, tooling ready in 25-30 days, parts shipped in 25-30 days
Surface Quality
The injection mold is precision CNC milled and polished to give the part an excellent surface. It can reach a roughness of Ra0.3.
The disadvantage of injection molding
Structural constraints
Some products with special structures are difficult to be integrally formed by injection molding.
High cost in small batches
Since the MIM process needs to produce MIM molds first, the cost is too high for the production of small batch products (quantity less than 1000 pieces).
JH MIM, metal powder injection molding service provider from Ningbo, China “To to The Best Worthy One-stop PM and MIM Manufacturer”
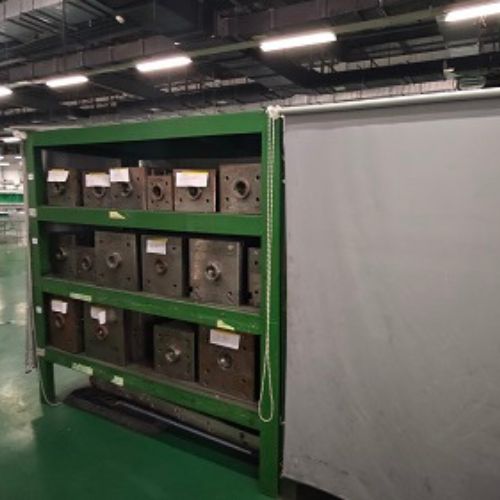
We are a metal injection molding China supplier, based in Ningbo City, China, providing you with full support through our two mim manufacturing factories. From traditional powder metallurgy to molding injection molding, One-stop service from concept and product design to prototyping and mold making to mass production.
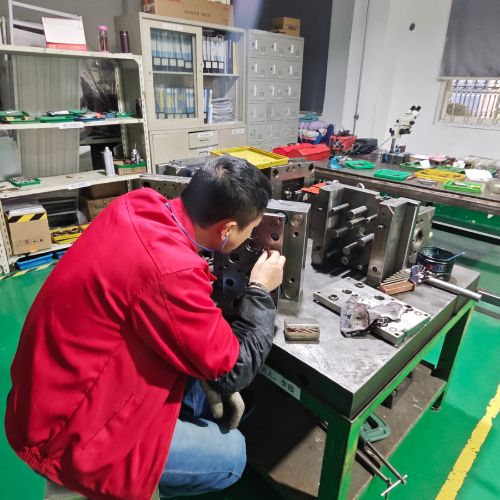
- We have a manufacturing facility of over 18.000 square meters with 18 advanced injection molding machines in two manufacturing sites in the UK
- 6 degreasing furnaces, 8 vacuum sintering furnaces
- Mould for molding workshop, self-production of molds, care, maintenance, repair and overhaul of existing molds
- Customer-customized automatic testing equipment (applicable to products with an annual purchase of more than 500.000 pieces)
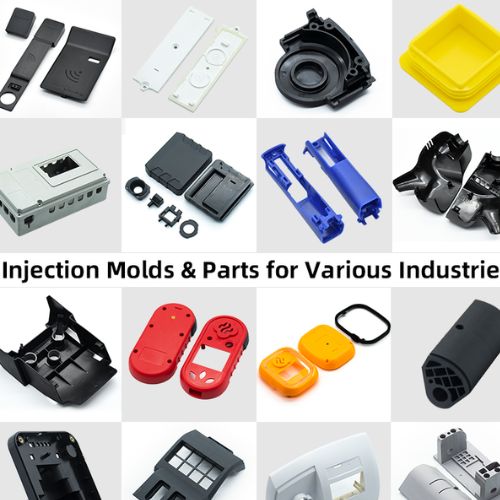
Design to Production in as little as 5 days We understand the importance of minimizing lead times (lead time compression) in order to get your product to market as quickly as possible. Learn more about how we
Why choose JH MIM?
JH MIM, with more than 12 years of MIM experience, has gained long-term trust from trusted partners in the United States, Europe and China. This ensures that we supply the highest quality MIM parts at competitive prices.
Our clients value our ISO 9001 /IATF 16949 certification, which demonstrates our commitment to high-quality service.
24 hours to get a quote
3-5 days to provide a professional DFM report
30-40 days to complete the mold and provide T1 samples
30-35 days to complete mass production
Please email us directly.
24 hours to provide quotations.
Iron, stainless steel, aluminum, titanium, ceramics, etc.
1000 pcs, much smaller than other suppliers.