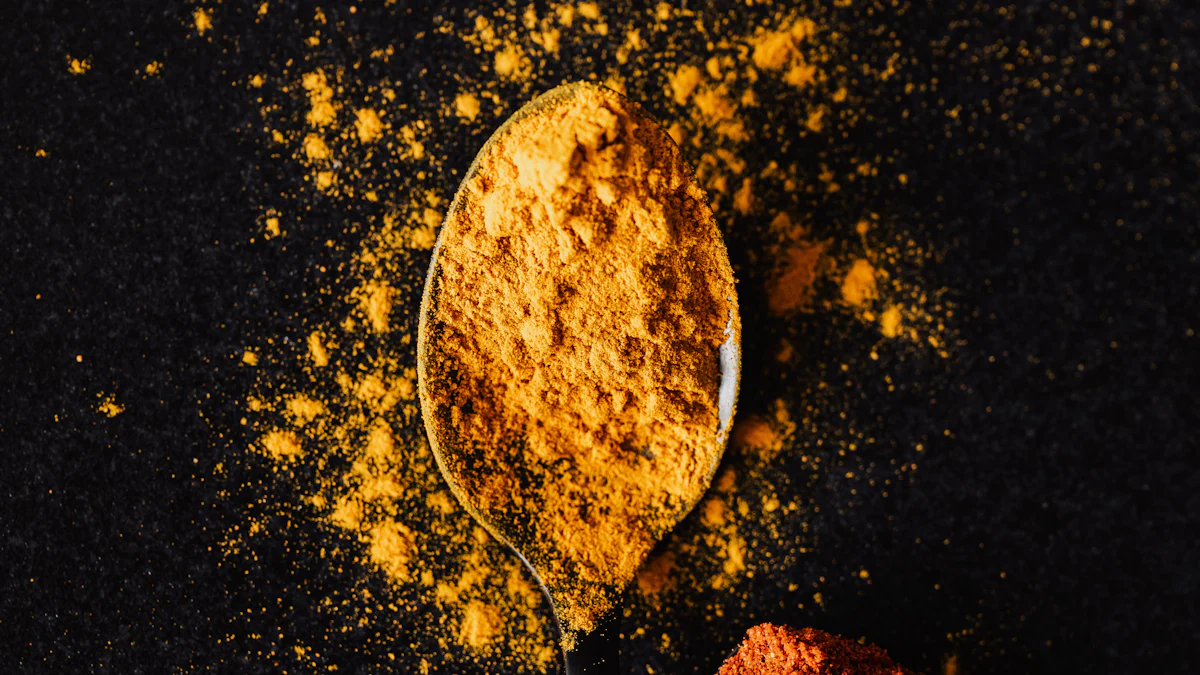
Atomization in powder metallurgy transforms molten metal into fine particles, creating high-quality metal powders. This process plays a pivotal role in modern manufacturing. It reduces machining by enabling near-net shape fabrication, minimizes waste by reusing scrap metal, and enhances energy efficiency. Additionally, atomized powders exhibit superior properties like increased strength and improved ductility due to rapid solidification.
Key Takeaways
- Atomization transforms molten metal into fine particles, producing high-quality powders essential for modern manufacturing, reducing waste, and enhancing energy efficiency.
- The process allows for precise control over powder properties, enabling the creation of custom alloys tailored to specific applications in industries like automotive and aerospace.
- Different atomization methods, such as gas and water atomization, offer unique advantages and limitations, making it crucial to choose the right technique based on application needs.
Overview of Powder Metallurgy
What is Powder Metallurgy
Powder metallurgy (PM) is a manufacturing process that uses metal powders to create components with precise dimensions and unique properties. It begins with the production of fine metal powders, which are then mixed, compacted, and sintered to form solid parts. This method eliminates the need for extensive machining and reduces material waste, making it an efficient and sustainable approach.
Historically, powder metallurgy has roots in ancient practices. The Incas, for example, crafted jewelry using powdered metals. However, the field truly advanced during the 19th and 20th centuries, with innovations that shaped modern techniques. Organizations like the Metal Powder Industries Federation have played a pivotal role in promoting PM and addressing misconceptions about its capabilities.
Role of Atomization in Powder Metallurgy
Atomization in powder metallurgy is a cornerstone of the powder production stage. It transforms molten metal into fine particles, which serve as the foundation for creating high-quality PM components. This process offers several advantages. The rapid solidification during atomization produces powders with a uniform grain structure, enhancing their strength and ductility. Additionally, the small, spherical particles have a high surface area, which improves their compactibility and sintering performance.
I’ve found that atomization also allows for precise control over the chemical composition of powders. This makes it possible to produce custom alloys tailored to specific applications. Whether it’s for automotive, aerospace, or additive manufacturing, atomized powders deliver superior mechanical properties and performance. By integrating atomization into powder metallurgy, manufacturers can achieve consistent quality and meet the demands of modern industries.
Atomization in Powder Metallurgy
Definition and Purpose
Atomization in powder metallurgy refers to the process of breaking down molten metal into fine particles to produce metal powders. I see this as a critical step in creating powders with consistent quality and properties. The purpose of atomization is to generate powders with specific characteristics, such as uniform particle size, spherical shape, and controlled chemical composition. These properties are essential for achieving high performance in powder metallurgy applications.
The scientific principles behind atomization play a significant role in determining the quality of the powders. For instance:
- The surface tension of the molten metal helps form spherical droplets during atomization.
- The viscosity and temperature of the liquid metal influence the particle size and shape. Higher temperatures reduce viscosity, leading to finer powders.
- The type of atomizing medium, such as nitrogen or argon, affects cooling rates and oxidation levels.
By understanding these principles, I can see how manufacturers optimize the process to meet specific requirements.
How the Process Works
The atomization process involves three key stages:
- Preheating: The metal is heated above its melting point to ensure it becomes fully liquid.
- Atomization: The molten metal is forced through a nozzle into a high-velocity gas stream. This breaks the liquid into fine droplets.
- Solidification: The droplets cool rapidly as they travel through the atomizing medium, forming solid spherical particles. These particles are then collected for further processing.
The process parameters, such as gas flow rate, pressure, and the type of atomizing medium, directly impact the final powder quality. For example, higher gas pressure produces finer powders, while lower metal flow rates result in more uniform particles. I find this level of control invaluable for tailoring powders to specific applications.
Types of Atomization
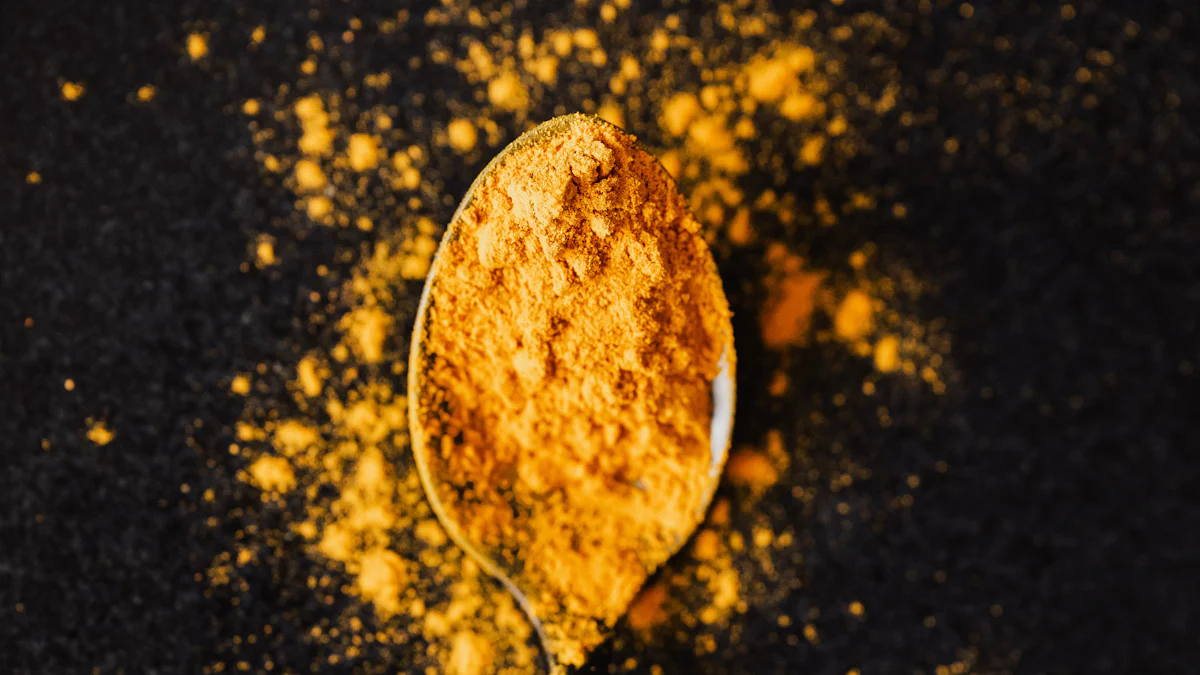
Gas Atomization
Gas atomization stands out as one of the most versatile methods in powder production. It uses high-velocity gas jets, such as nitrogen or argon, to break molten metal into fine droplets. These droplets solidify into spherical particles, which are ideal for applications requiring uniformity. I find this method particularly effective for producing powders with controlled particle size distribution and minimal contamination.
Compared to other techniques, gas atomization offers several advantages:
- Spherical particle shape ensures better flowability and packing density.
- Narrow particle size distribution enhances sintering performance.
- Low contamination levels improve the quality of the final product.
- It supports a wide range of alloy compositions, making it highly adaptable.
However, this method has limitations. The equipment cost is high, and controlling particle size can be challenging. Despite these drawbacks, its ability to produce superior powders makes it indispensable in industries like aerospace and additive manufacturing.
Advantages | Limitations |
---|---|
Superior Powder Characteristics | High Equipment Cost |
Enhanced Material Performance | Oxidation of Powders |
Wider Alloy Range | Powder Agglomeration |
High Production Rate | Challenges in Particle Size Control |
Reduced Contamination |
Water Atomization
Water atomization offers a cost-effective alternative for producing metal powders. It uses high-pressure water jets to disintegrate molten metal, resulting in rapid cooling and solidification. This process creates irregularly shaped particles, which I find advantageous for applications requiring strong mechanical interlocking.
Key features of water atomization include:
- Lower production costs compared to gas atomization.
- Irregular particle shapes due to higher cooling rates.
- Higher oxygen content in the powders, which may limit their use in some applications.
- High green strength after pressing, making it suitable for structural components.
While water atomization lacks the precision of gas atomization, its affordability and efficiency make it a popular choice for large-scale production.
Centrifugal Atomization
Centrifugal atomization employs centrifugal force to transform molten metal into fine droplets. The metal is typically poured onto a rapidly spinning disk or cup, which flings the liquid outward. The droplets solidify into powders with controlled particle sizes and high cleanliness.
This method excels in producing high-quality powders for demanding applications. I often recommend it for industries requiring minimal contamination and high material yield. Its ability to produce powders with consistent properties makes it a reliable choice for specialized manufacturing processes.
Ultrasonic Atomization
Ultrasonic atomization uses high-frequency sound waves to break molten metal into fine droplets. This technique is unique because it achieves extremely fine particle sizes and uniform distributions. I find it particularly useful for applications requiring precision, such as electronics and medical devices.
Although ultrasonic atomization is less common due to its lower production rates, its ability to produce powders with exceptional quality makes it invaluable for niche applications.
Advantages of Atomization
Uniform Particle Size
Atomization ensures a uniform particle size distribution, which is critical for achieving consistent material properties. During the process, molten metal transforms into droplets that solidify into powder. This method eliminates impurities and produces powders with predictable characteristics. I’ve observed that this uniformity reduces variability in manufacturing, leading to reliable and high-performing components.
The ability to control particle size also enhances the flowability of powders. Spherical particles, for instance, pack more efficiently and sinter more uniformly. This results in denser and stronger final products. Whether it’s for aerospace or medical applications, uniform particle size plays a pivotal role in meeting stringent quality standards.
Control Over Powder Properties
Atomization allows precise control over the properties of metal powders. By adjusting process parameters like gas pressure, temperature, and atomizing medium, manufacturers can tailor powders to specific needs. I find this level of customization invaluable for industries requiring specialized materials.
For example, controlling particle size distribution leads to a narrower and more consistent range of sizes. This consistency translates into products with predictable mechanical and thermal properties. Additionally, the rapid cooling during atomization enhances powder purity and minimizes oxidation. These factors contribute to powders with superior performance and reliability.
Cost-Effectiveness
Atomization in powder metallurgy offers a cost-effective solution for producing high-quality powders. The process minimizes material waste by converting molten metal directly into powder. This efficiency reduces the need for extensive machining and lowers production costs.
I’ve noticed that atomization also supports large-scale production, making it suitable for industries with high-volume demands. Techniques like water atomization, for instance, provide an affordable option for creating powders with strong mechanical properties. By optimizing the process, manufacturers can achieve a balance between quality and cost, ensuring competitive pricing for their products.
Applications of Atomized Powders
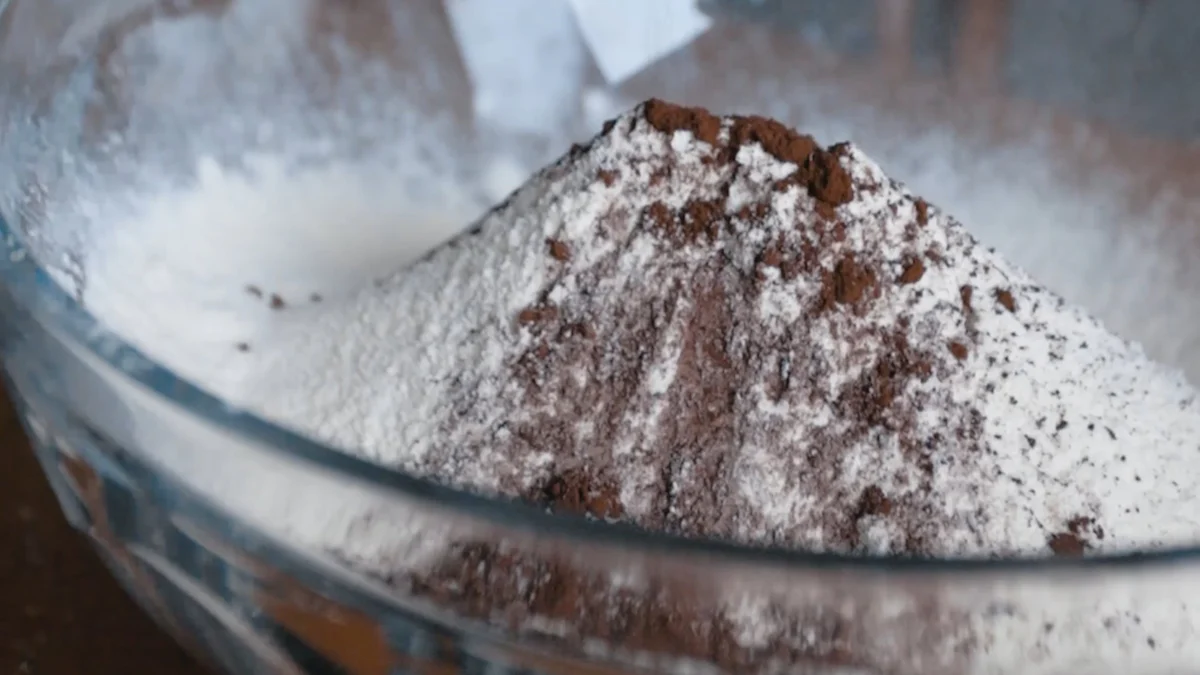
Automotive and Aerospace
Atomized powders play a vital role in the automotive and aerospace industries. These powders enable the production of lightweight yet high-strength components, which are essential for improving performance and efficiency. In the automotive sector, I’ve seen how metal powders contribute to lightweighting, enhancing fuel efficiency, and reducing emissions. For example, they are used to manufacture high-strength engine components that withstand extreme conditions.
In aerospace, atomized powders are indispensable for creating advanced materials like titanium alloys. These materials are used in turbine blades and structural parts, where strength and weight reduction are critical. The ability to produce intricate designs with minimal waste makes atomized powders a preferred choice for these industries.
Industry | Application |
---|---|
Automotive | Lightweight, high-strength engine components |
Aerospace | Turbine blades and structural parts made of titanium |
Additive Manufacturing
Additive manufacturing, or 3D printing, relies heavily on atomized powders. These powders are engineered for various printing processes, enabling the creation of intricate and complex designs. I’ve observed how their spherical shape and uniform particle size, especially those produced through gas atomization, make them ideal for this technology.
The demand for lightweight and complex parts continues to grow, driving advancements in additive manufacturing. Atomized powders provide superior material properties, ensuring precision and reliability in customized parts. Industries like aerospace and healthcare benefit significantly from these powders, as they enable the fabrication of high-performance components with exceptional accuracy.
Electronics and Medical Devices
In electronics, atomized powders are essential for manufacturing conductive inks, pastes, and coatings. These materials are critical for producing printed circuit boards, sensors, and other electronic components. I’ve noticed how their fine particle size and purity ensure optimal conductivity and performance.
In the medical field, atomized powders are used to create biocompatible implants, surgical instruments, and dental prosthetics. Their ability to meet stringent quality standards makes them invaluable for applications requiring precision and reliability. Whether it’s for electronics or medical devices, atomized powders continue to drive innovation and improve product performance.
Atomization in powder metallurgy has revolutionized the production of metal powders, enabling advancements across industries. Its ability to produce high-purity powders with controlled particle sizes ensures superior performance in applications like aerospace, automotive, and medical devices.
Atomization drives energy efficiency, reduces waste, and supports intricate designs in additive manufacturing. It also enhances powder purity, minimizing defects in critical components.
Emerging trends, such as AI-driven optimization and sustainable practices, promise to refine atomization further. These innovations will continue to shape modern manufacturing, ensuring precision, efficiency, and environmental responsibility.
FAQ
What is the main advantage of atomization in powder metallurgy?
Atomization produces powders with uniform particle sizes and controlled properties. This ensures consistent quality, making it ideal for industries requiring precision and high-performance materials.
How does gas atomization differ from water atomization?
Gas atomization creates spherical particles with low contamination, while water atomization produces irregular shapes at a lower cost. Each method suits different applications and budget constraints.
Can atomized powders be recycled?
Yes, atomized powders can be reused in manufacturing processes. This reduces waste and supports sustainable practices, making powder metallurgy an environmentally friendly option.
💡 Tip: Choose the atomization method based on your application’s requirements for particle shape, size, and cost efficiency.