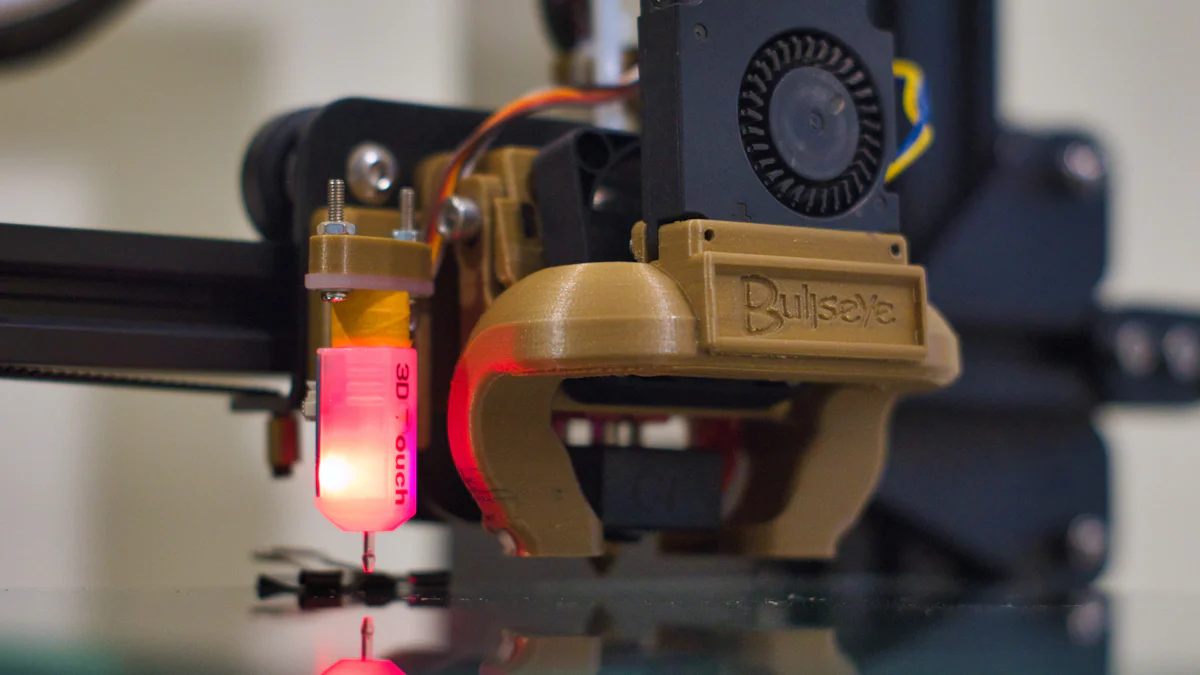
In the world of manufacturing, choosing between Metal Injection Molding vs Metal Binder Jetting can significantly impact production efficiency and cost. Metal Injection Molding (MIM) excels in high-volume production, offering labor savings through automation. It is ideal for complex, small components. On the other hand, Metal Binder Jetting (MBJ) shines with its ability to economically produce large, intricate parts without molds. The decision hinges on factors like part design and production quantity. Understanding these differences helps manufacturers select the most suitable process for their needs.
Key Takeaways
- Metal Injection Molding (MIM) is ideal for high-volume production of small, complex parts, making it a go-to choice for industries like automotive and consumer electronics.
- Metal Binder Jetting (MBJ) offers unmatched design flexibility, allowing for the creation of intricate geometries without the need for molds, which is perfect for rapid prototyping.
- Consider initial investment costs: MIM requires higher upfront costs due to tooling, while MBJ has lower initial costs, making it suitable for smaller production runs.
- Evaluate the mechanical properties needed for your parts: MIM typically produces stronger components, while MBJ excels in design intricacy but may require additional finishing.
- Understand your production speed needs: MIM is efficient for large batches once tooling is set, whereas MBJ allows for quicker transitions from design to production.
- Both processes offer a variety of metal options, but MIM is better for high-strength applications, while MBJ can work with hard materials without melting.
- Choosing between MIM and MBJ depends on your specific production needs, including part complexity, volume, and material requirements.
Overview of Metal Injection Molding
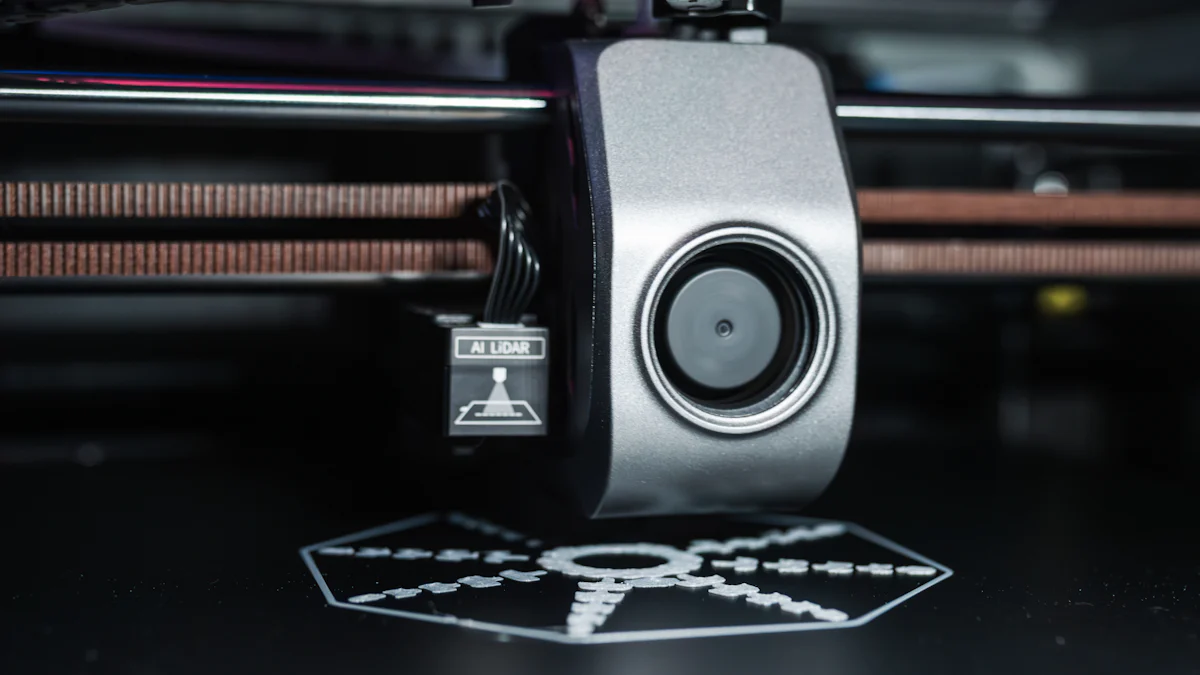
Process Description
Metal Injection Molding (MIM) stands as a unique manufacturing process that merges the precision of plastic injection molding with the robustness of metalworking. I find this combination fascinating because it allows for the creation of small, complex-shaped metal components with outstanding mechanical properties.
Materials and Binder Composition
In MIM, finely powdered metal is mixed with a binder to create a feedstock. This mixture is crucial as it determines the quality and characteristics of the final product. The binder acts as a temporary vehicle to hold the metal powder together during the initial stages of the process. I appreciate how this step ensures that the metal particles are uniformly distributed, which is essential for achieving the desired material properties.
Molding and Sintering Steps
The feedstock is injected into a mold cavity under high pressure, forming what we call ‘green parts.’ These parts undergo debinding to remove the binder, followed by sintering. Sintering involves heating the parts to a temperature below the melting point of the metal, which helps achieve full density and mechanical strength. This step fascinates me because it transforms the fragile green parts into robust metal components.
Advantages
MIM offers several advantages that make it a preferred choice in various industries.
High Volume Production
One of the most significant benefits of MIM is its capability for high-volume production. This process is highly repeatable, making it ideal for manufacturing large quantities of parts efficiently. I often see this advantage leveraged in industries like automotive and consumer electronics, where consistent quality and volume are paramount.
Complex Geometries
MIM excels in producing parts with complex geometries that would be challenging or impossible to achieve with traditional machining methods. The ability to create intricate shapes without compromising on strength or quality is something I find particularly impressive about this process.
Limitations
Despite its advantages, MIM does have some limitations that need consideration.
Initial Tooling Costs
The initial tooling costs for MIM can be high, which might deter some manufacturers from adopting this process for low-volume production. However, I believe that the long-term benefits often outweigh these initial expenses, especially for large-scale operations.
Material Limitations
While MIM offers a variety of material options, there are still some limitations in terms of the types of metals that can be used. Not all metals are suitable for this process, which can restrict its application in certain scenarios. I think it’s essential for manufacturers to carefully evaluate their material requirements before choosing MIM.
Overview of Metal Binder Jetting
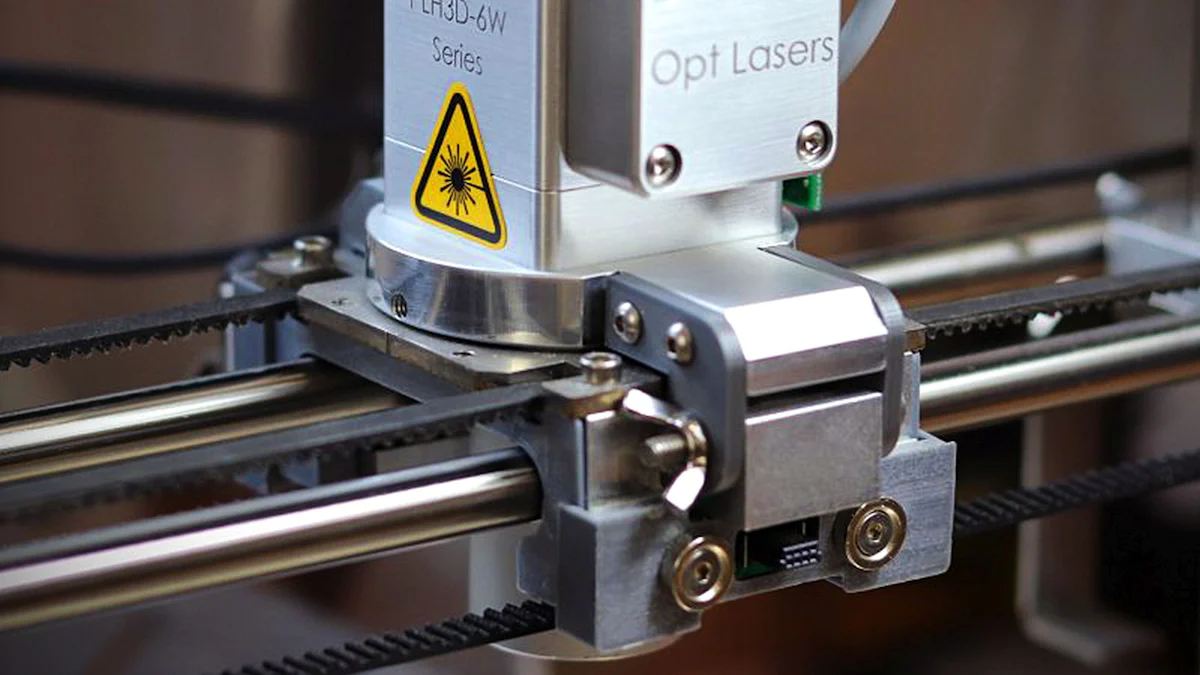
Process Description
Metal Binder Jetting represents a fascinating advancement in additive manufacturing. This process involves applying a liquid binder onto a thin layer of metal powder particles using inkjet print heads. I find this method intriguing because it constructs parts layer by layer, following a digital design file as a blueprint. The absence of melting in this process allows for the use of hard materials, which can be processed economically to produce large, complex components.
Layer-by-Layer Construction
In Metal Binder Jetting, each layer of powder receives a precise application of binder, which bonds the particles together. This step repeats until the entire part is formed. I appreciate how this technique allows for the creation of intricate designs without the constraints of traditional manufacturing methods. The ability to nest multiple parts in a single build further enhances its efficiency, making it ideal for batch production.
Post-Processing Requirements
Once the green parts are formed, they undergo debinding and sintering. Debinding removes the binder, while sintering consolidates the powder into a solid mass. This post-processing is crucial for achieving the desired mechanical properties and dimensional accuracy. I find the transformation from fragile green parts to robust metal components particularly impressive.
Advantages
Metal Binder Jetting offers several compelling advantages that make it a valuable choice for certain applications.
Design Flexibility
One of the standout features of this process is its unparalleled design flexibility. The ability to create complex geometries without the need for molds opens up new possibilities for designers and engineers. I believe this flexibility is a game-changer for industries that require customized or intricate parts.
No Need for Tooling
Another significant advantage is the elimination of tooling requirements. This aspect reduces initial costs and shortens lead times, making it an attractive option for prototyping and small-scale production. I see this as a major benefit for companies looking to innovate quickly and efficiently.
Limitations
Despite its advantages, Metal Binder Jetting does have some limitations that warrant consideration.
Surface Finish Quality
The surface finish quality of parts produced through this process may not match that of other manufacturing methods. I often notice that additional finishing processes, such as polishing or machining, are necessary to achieve the desired surface texture. This requirement can add time and cost to the production process.
Mechanical Properties
While Metal Binder Jetting excels in design flexibility, the mechanical properties of the final parts may not always meet the standards of traditionally manufactured components. I think it’s important for manufacturers to carefully evaluate the performance requirements of their parts before choosing this process.
Comparative Analysis
In the realm of manufacturing, understanding the nuances between Metal Injection Molding vs Metal Binder Jetting can guide decision-making. Each method offers distinct advantages and challenges, which I find fascinating to explore.
Cost Considerations
Initial Investment
When considering initial investment, Metal Injection Molding (MIM) often requires a higher upfront cost due to the need for specialized molds and tooling. This investment can be substantial, especially for complex designs. However, I believe that this cost can be justified for large-scale production runs where the per-part cost decreases significantly over time. In contrast, Metal Binder Jetting (MBJ) typically involves lower initial costs. The absence of tooling requirements makes it an attractive option for companies looking to minimize upfront expenses. This aspect appeals to me as it allows for more flexibility in experimenting with different designs without committing to costly molds.
Production Costs
Production costs also vary between these two methods. MIM excels in high-volume production, offering cost-effective solutions for manufacturing large quantities of parts. The repeatability and efficiency of this process make it ideal for industries like automotive and consumer electronics. On the other hand, MBJ shines in smaller production runs. Its ability to produce intricate parts without the need for molds reduces material waste and labor costs. I find this particularly beneficial for prototyping and small-batch production, where cost efficiency is crucial.
Design Flexibility
Complexity of Parts
Design flexibility is a key differentiator between these processes. MIM allows for the creation of complex geometries, but it does have limitations due to the constraints of mold design. I often see this as a challenge when trying to push the boundaries of part complexity. In contrast, MBJ offers unparalleled design freedom. The layer-by-layer construction method enables the production of intricate shapes that would be difficult or impossible to achieve with traditional methods. This flexibility excites me as it opens up new possibilities for innovative designs.
Customization Options
Customization is another area where MBJ excels. The ability to quickly modify digital designs without the need for new molds allows for rapid prototyping and customization. I appreciate how this capability supports industries that require tailored solutions, such as aerospace and medical devices. MIM, while offering some degree of customization, often involves longer lead times and higher costs for design changes due to the need for new tooling.
Production Speed
Time to Market
Production speed plays a critical role in determining the time to market. MIM, with its efficient high-volume production capabilities, can deliver large quantities of parts quickly once the tooling is in place. This speed is advantageous for industries with high demand and tight deadlines. However, the initial setup time for tooling can delay the start of production. In contrast, MBJ offers faster turnaround times for initial production runs. The absence of tooling requirements allows for quicker transitions from design to production, which I find beneficial for companies looking to bring new products to market rapidly.
Batch Sizes
Batch sizes also influence production speed. MIM is well-suited for large batch sizes, where the cost per part decreases as the volume increases. This efficiency makes it ideal for mass production. On the other hand, MBJ is more flexible with batch sizes, accommodating both small and large runs. This adaptability appeals to me as it allows manufacturers to respond quickly to changing market demands without the constraints of minimum order quantities.
Material Options
Variety of Metals
In the realm of manufacturing, the choice of materials plays a pivotal role in determining the success of a production process. I find that both Metal Injection Molding (MIM) and Metal Binder Jetting (MBJ) offer a diverse range of metal options, each catering to specific needs and applications.
-
Metal Injection Molding (MIM): This process typically utilizes a variety of metals, including stainless steel, titanium, and copper. These metals are chosen for their excellent mechanical properties and ability to withstand high temperatures. I appreciate how MIM allows for the use of these robust materials, making it ideal for industries that demand high-strength components, such as automotive and aerospace.
-
Metal Binder Jetting (MBJ): MBJ also offers a wide selection of metals, including stainless steel, bronze, and nickel-based alloys. What excites me about MBJ is its ability to work with hard materials without the need for melting, which opens up possibilities for creating intricate designs with metals that might be challenging to process using traditional methods.
The variety of metals available in both processes provides manufacturers with the flexibility to choose the most suitable material for their specific application, ensuring optimal performance and durability.
Material Properties
Understanding the material properties is crucial when selecting a manufacturing process. I find that both MIM and MBJ offer unique advantages in terms of material characteristics.
-
Metal Injection Molding (MIM): MIM excels in producing parts with superior mechanical properties. The sintering process used in MIM results in high-density components with excellent strength and durability. I often see this advantage leveraged in industries where precision and reliability are paramount. The ability to achieve near-full density in MIM parts ensures that they can withstand demanding operational conditions.
-
Metal Binder Jetting (MBJ): While MBJ offers unparalleled design flexibility, the mechanical properties of the final parts may not always match those produced by MIM. However, I believe that MBJ’s ability to create complex geometries without compromising on material integrity makes it a valuable choice for applications where design intricacy is more critical than mechanical strength.
Applications and Use Cases
Metal Injection Molding Applications
Metal Injection Molding (MIM) finds its niche in industries that demand precision and durability. I have observed its significant impact in the following sectors:
Automotive Industry
The automotive industry benefits greatly from MIM’s ability to produce small, complex components with excellent mechanical properties. MIM creates durable and fatigue-resistant parts, which are crucial for automotive applications. Components such as gears, turbocharger rotors, and fuel injector nozzles often rely on MIM for their production. The process supports a wide range of materials, including stainless steel and titanium, ensuring that these parts can withstand the demanding conditions of automotive environments.
Consumer Electronics
In consumer electronics, MIM excels in manufacturing intricate parts that require high precision and strength. I find it fascinating how MIM can produce components like connectors, housings, and brackets with exceptional surface finish and dimensional accuracy. The ability to use various metal alloys allows manufacturers to tailor the material properties to meet specific performance requirements. This versatility makes MIM an ideal choice for producing high-quality electronic components.
Metal Binder Jetting Applications
Metal Binder Jetting (MBJ) offers unique advantages in applications where design flexibility and rapid prototyping are essential. I have seen its effectiveness in the following areas:
Prototyping
MBJ shines in the realm of prototyping due to its ability to quickly produce complex geometries without the need for molds. This process allows designers to experiment with different designs and iterate rapidly. I appreciate how MBJ enables the creation of prototypes that closely resemble the final product, providing valuable insights into the design’s functionality and aesthetics. The reduced lead times and lower costs associated with MBJ make it an attractive option for companies looking to innovate swiftly.
Aerospace Components
The aerospace industry leverages MBJ for its capacity to produce lightweight, intricate components. I find it remarkable how MBJ can create parts with complex internal structures that would be challenging to achieve with traditional methods. This capability is particularly beneficial for aerospace applications, where weight reduction and design optimization are critical. Components such as brackets, ducts, and heat exchangers often utilize MBJ to achieve the desired balance between performance and weight.
In comparing Metal Injection Molding vs Metal Binder Jetting, I find distinct differences and similarities that guide manufacturing decisions. MIM excels in producing small, intricate parts with high precision and strength, making it ideal for industries like automotive and aerospace. Its ability to handle high volumes efficiently is unmatched. Conversely, MBJ offers unparalleled design flexibility and rapid prototyping capabilities, which I see as beneficial for industries requiring customization and quick market entry. Ultimately, the choice between these processes depends on specific production needs, such as volume, complexity, and material requirements.
FAQ
What are the main differences between Metal Injection Molding and Metal Binder Jetting?
Metal Injection Molding (MIM) and Metal Binder Jetting (MBJ) differ primarily in their processes and applications. MIM combines metal powder with a binder to form a feedstock, which is then molded and sintered to create dense, strong parts. MBJ, on the other hand, uses a liquid binder to bond metal powder layer by layer, allowing for greater design flexibility but often requiring additional post-processing. The choice between these methods depends on factors like part complexity and production volume.
How do I decide which manufacturing process to use?
Choosing the right manufacturing process involves considering several factors. I recommend evaluating the design complexity of the part and the production volume required. MIM is ideal for high-volume production of small, intricate parts, while MBJ excels in producing complex geometries without molds, making it suitable for prototyping and small-batch production.
What are the cost implications of each method?
The cost implications vary significantly between MIM and MBJ. MIM typically requires a higher initial investment due to tooling costs, but it becomes cost-effective for large-scale production. MBJ has lower upfront costs since it doesn’t require molds, making it more economical for smaller production runs or prototyping.
Can both processes handle the same materials?
Both MIM and MBJ offer a range of metal options, but they have different material capabilities. MIM commonly uses metals like stainless steel and titanium, known for their strength and durability. MBJ also works with various metals, including bronze and nickel-based alloys, but its ability to process hard materials without melting offers unique design possibilities.
How do the mechanical properties of parts compare?
Parts produced by MIM generally exhibit superior mechanical properties due to the high-density achieved during sintering. This makes them suitable for applications requiring strength and durability. MBJ parts, while offering design flexibility, may not always match the mechanical strength of MIM parts, making them more suitable for applications where design intricacy is prioritized.
What industries benefit most from each process?
MIM finds extensive use in industries like automotive and consumer electronics, where precision and high-volume production are crucial. MBJ, with its rapid prototyping capabilities and design flexibility, benefits industries such as aerospace and medical devices, where customization and quick market entry are essential.
How does production speed differ between the two methods?
Production speed varies between MIM and MBJ. MIM offers efficient high-volume production once tooling is in place, making it ideal for industries with high demand. MBJ provides faster turnaround times for initial production runs due to the absence of tooling requirements, which is beneficial for companies looking to bring new products to market quickly.
Are there any limitations to consider with each process?
Yes, each process has its limitations. MIM involves high initial tooling costs and material restrictions, which can limit its application. MBJ may require additional finishing processes to achieve desired surface quality and may not always meet the mechanical property standards of traditionally manufactured components.
What role does technology selection play in manufacturing?
Selecting the right technology is crucial in optimizing production processes. Advanced technologies like MIM and MBJ have revolutionized manufacturing, allowing for innovative solutions tailored to specific needs. Understanding the nuances of each method helps unlock their full potential and ensures efficient production.
How do design complexity and production volume influence the choice of process?
Design complexity and production volume are key factors in selecting a manufacturing method. MIM excels in producing small, complex parts efficiently in large quantities. MBJ offers unparalleled design flexibility, making it ideal for intricate designs and smaller production runs. Evaluating these factors helps manufacturers choose the most suitable process for their needs.