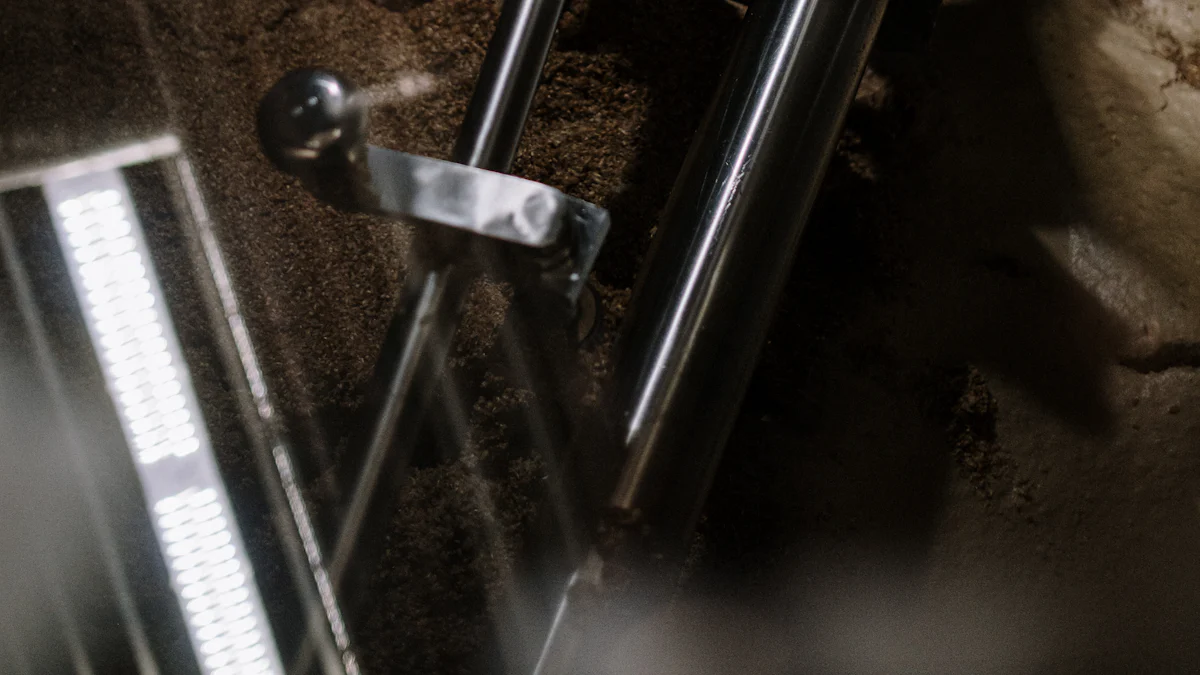
Stainless steel injection molding stands as a transformative process in modern manufacturing. It enables the creation of intricate, high-precision stainless steel components that meet demanding specifications. This method combines the flexibility of plastic injection molding with the strength and durability of metal. Stainless steel, known for its corrosion resistance and mechanical strength, plays a pivotal role in this process. Industries like automotive, medical devices, and aerospace rely on this technique to produce reliable and complex parts efficiently. Its ability to deliver consistent quality and precision makes it indispensable in today’s competitive manufacturing landscape.
What is Stainless Steel Injection Molding?
Stainless steel injection molding, often called Metal Injection Molding (MIM), is a cutting-edge manufacturing process that combines the versatility of plastic injection molding with the strength and durability of metal. This technique allows for producing intricate and high-precision stainless steel components that meet stringent industry standards. By leveraging stainless steel’s unique properties, such as corrosion resistance and mechanical strength, this process has become a cornerstone in industries requiring complex and reliable parts.
Overview of the Process
The stainless steel injection molding process begins with the preparation of a feedstock. This feedstock consists of fine stainless steel powders mixed with a binder material. The mixture is then heated and injected into a mold cavity using specialized machines, such as hydraulic or electric injection molding systems. Once the material cools and solidifies, the molded part undergoes debinding to remove the binder. Finally, the part is sintered at high temperatures to achieve its final density and mechanical properties.
This process enables manufacturers to create components with exceptional dimensional accuracy and intricate geometries. Unlike traditional methods like machining or casting, stainless steel injection molding minimizes material waste and reduces production costs. It also supports the use of various stainless steel grades, including 304, 316, and 420, each offering distinct advantages for specific applications.
Key Components of Stainless Steel Injection Molding
Several critical elements contribute to the success of stainless steel injection molding:
-
Feedstock: The feedstock is a blend of stainless steel powders and binders. The choice of stainless steel grade, such as 17-4 PH or 420, depends on the desired properties of the final product, including hardness, corrosion resistance, and wear resistance.
-
Mold Design: High-quality steel molds ensure precision and durability during the injection process. These molds can withstand high production volumes while maintaining consistent product standards.
-
Injection Molding Machines: Hydraulic, electric, or hybrid machines inject the feedstock into the mold cavity. These machines provide the necessary pressure and temperature control to achieve optimal results.
-
Debinding and Sintering Equipment: Debinding removes the binder material, while sintering fuses the metal particles to create a dense and robust final product. These steps are crucial for achieving the desired mechanical and aesthetic properties.
By integrating these components, stainless steel injection molding delivers unparalleled precision and efficiency. This process has revolutionized the production of small, intricate parts used in industries such as automotive, medical devices, and aerospace.
Benefits of Stainless Steel Injection Molding
Precision and Complexity
I have always admired how stainless steel injection molding achieves unmatched precision. This process allows manufacturers to create intricate geometries that other methods struggle to replicate. The ability to produce small, detailed components with tight tolerances sets it apart. For example, industries like medical devices and aerospace demand parts with exceptional accuracy. Stainless steel injection molding delivers these results consistently.
The process imposes minimal restrictions on part design. Engineers can innovate freely, knowing the technology supports complex shapes and multi-component designs. Unlike traditional machining, which often requires secondary operations, this method produces finished parts in a single step. This efficiency enhances both quality and productivity.
Cost-Effectiveness
Cost-effectiveness remains a significant advantage of stainless steel injection molding. I have noticed how this method reduces material waste compared to machining or casting. The feedstock, a blend of metal powders and binders, ensures optimal material usage. Less waste translates to lower costs, especially for large production runs.
Labor costs also decrease with this process. Automation minimizes manual intervention, streamlining production. Additionally, the need for secondary operations, such as machining or finishing, is rare. These factors make stainless steel injection molding an economical choice for manufacturers aiming to optimize their budgets.
Durability and Strength
Durability and strength define the core benefits of stainless steel injection molding. The sintering process fuses metal particles, creating dense and robust components. I have seen how this results in parts with superior mechanical properties, capable of withstanding high stress and wear.
Stainless steel’s inherent corrosion resistance further enhances its durability. Components produced through this method perform reliably in harsh environments, from automotive engines to medical implants. The ability to tailor mechanical properties by adjusting the sintering process adds another layer of versatility. Manufacturers can meet specific application requirements without compromising quality.
The Process of Stainless Steel Injection Molding
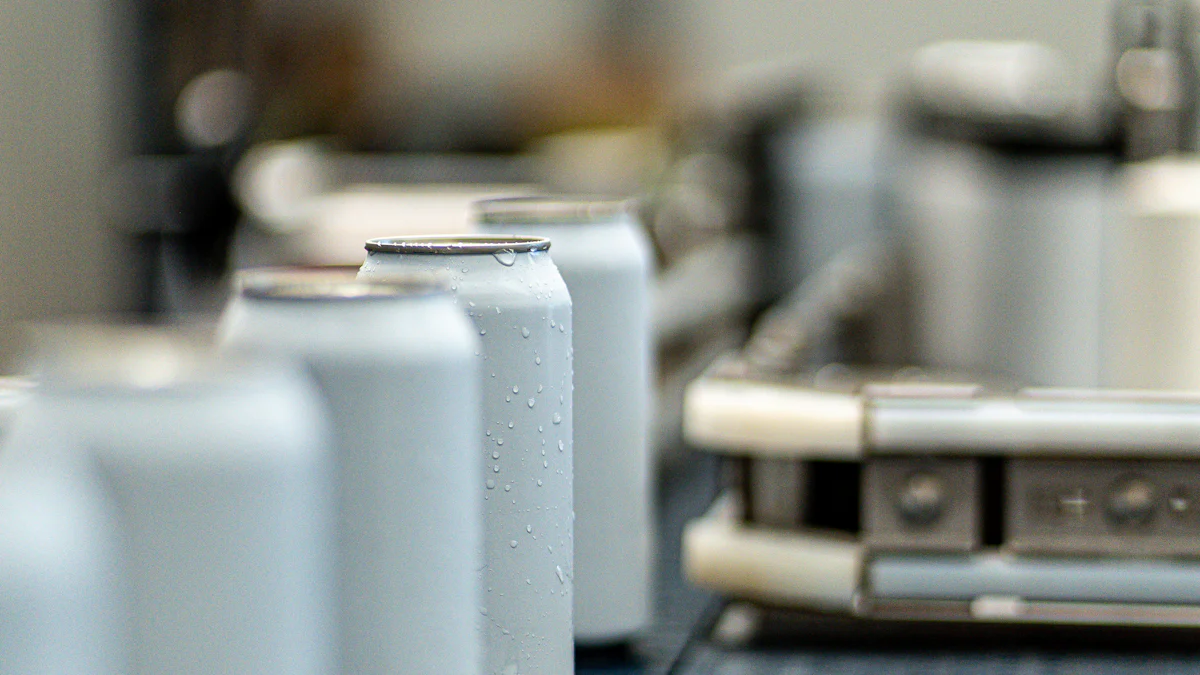
Material Preparation
Material preparation forms the foundation of stainless steel injection molding. I always emphasize the importance of this step because it directly impacts the quality of the final product. The process begins with creating a feedstock, which combines fine stainless steel powders with a binder material. The binder acts as a temporary adhesive, holding the metal particles together during the molding phase.
The selection of stainless steel powders depends on the desired properties of the finished part. For instance, 304 stainless steel offers excellent corrosion resistance, while 17-4 PH provides superior strength and hardness. The powders undergo rigorous screening to ensure uniform particle size, which is critical for achieving consistent results. Once mixed with the binder, the feedstock is granulated into pellets, making it easier to handle during the injection process.
This stage requires precision and expertise. Any inconsistency in the feedstock composition can lead to defects in the molded parts. I have seen how advanced equipment and strict quality control measures ensure the feedstock meets the highest standards.
Injection Molding
Injection molding transforms the prepared feedstock into the desired shape. I find this step fascinating because it combines engineering precision with creative design. The feedstock pellets are fed into an injection molding machine, where they are heated until they reach a semi-liquid state. This molten material is then injected into a custom-designed mold cavity under high pressure.
The mold design plays a crucial role in this phase. It determines the shape, dimensions, and surface finish of the final part. High-quality molds, often made from hardened steel, withstand the intense pressure and temperature of the injection process. The molten feedstock fills every corner of the mold, capturing intricate details and complex geometries.
Once the material cools and solidifies, the mold opens to release the “green” part. This part retains the shape of the final product but lacks its mechanical strength. I always stress the importance of maintaining precise temperature and pressure settings during this stage to avoid defects like warping or incomplete filling.
Debinding and Sintering
Debinding and sintering represent the final steps in stainless steel injection molding. These stages transform the “green” part into a dense, robust metal component. During debinding, the binder material is carefully removed, leaving behind a porous structure known as the “brown” part. This step requires controlled conditions to prevent damage to the delicate structure.
Sintering follows debinding and serves as the most critical phase. The “brown” part is placed in a specialized furnace and heated to temperatures near the melting point of stainless steel. This process causes the metal particles to fuse together, eliminating porosity and achieving the desired density. I have observed how sintering enhances the mechanical properties of the part, such as strength, hardness, and corrosion resistance.
The sintering process also allows for slight adjustments in the part’s dimensions, ensuring exceptional dimensional accuracy. Manufacturers can tailor the mechanical properties by modifying the sintering temperature and duration. This flexibility makes stainless steel injection molding ideal for producing components with specific performance requirements.
“The sintering phase is the final stage in metal injection molding, where the ‘brown’ part is heated in a specialized furnace.” This quote highlights the transformative nature of sintering in creating high-quality metal parts.
By following these steps, stainless steel injection molding delivers components that meet the highest standards of precision, durability, and performance. This process has revolutionized industries by enabling the production of complex parts with unmatched efficiency.
Applications of Stainless Steel Injection Molding
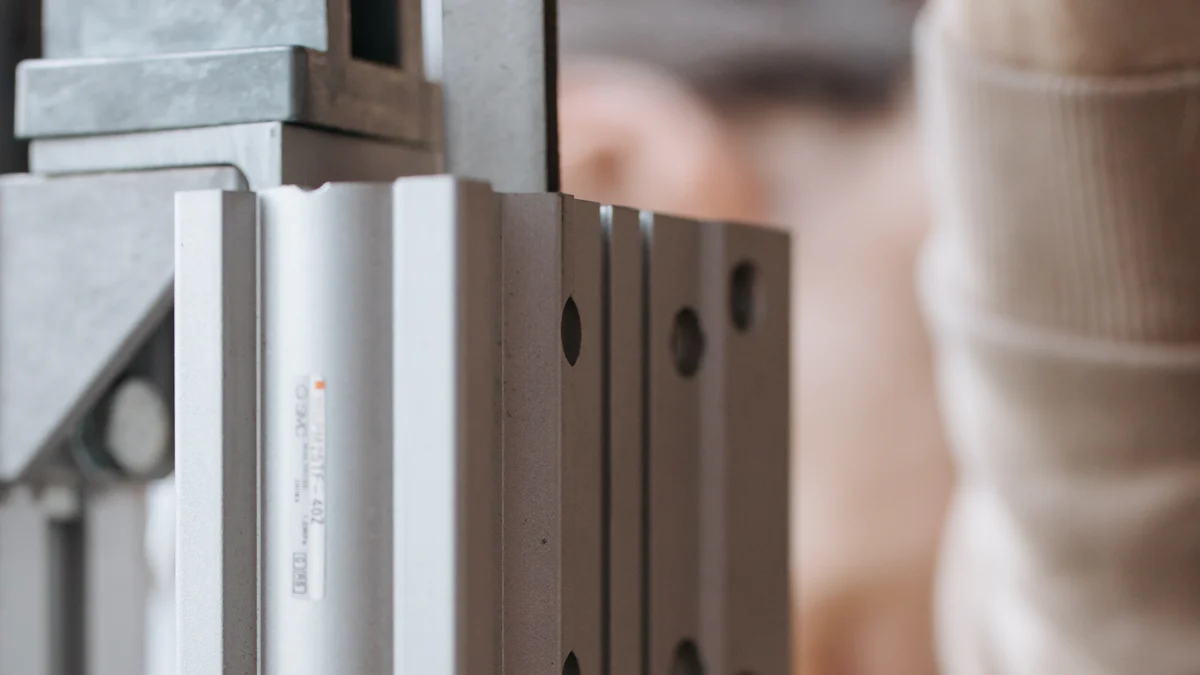
Automotive Industry
The automotive industry relies heavily on stainless steel injection molding to produce high-performance components. I have observed how this process enables the creation of intricate parts that meet the rigorous demands of modern vehicles. For example, manufacturers use this technique to produce components for engines, gearboxes, and turbochargers. These parts require exceptional strength and precision to function effectively under extreme conditions.
Locking mechanisms, steering systems, and electrical systems also benefit from this technology. The ability to create complex geometries with tight tolerances ensures that these components perform reliably. I find it remarkable how stainless steel injection molding reduces material waste while maintaining high production efficiency. This makes it an ideal choice for the automotive sector, where cost-effectiveness and quality are paramount.
Medical Devices
In the medical field, stainless steel injection molding plays a crucial role in producing precision instruments. I have seen how this process delivers surgical tools like scissors and clamps with unmatched accuracy. The use of 420 stainless steel in these applications ensures durability and resistance to wear, which are essential for medical procedures.
The ability to create small, intricate components makes this method invaluable for medical devices. For instance, implants and diagnostic tools often require complex designs that traditional manufacturing methods cannot achieve. Stainless steel injection molding meets these challenges while maintaining strict hygiene and quality standards. This technology has revolutionized the medical industry by enabling the production of reliable and high-precision instruments.
Consumer Electronics
The consumer electronics industry benefits significantly from stainless steel injection molding. I have noticed how this process allows manufacturers to produce high-precision components at scale. Devices like smartphones, laptops, and wearable gadgets require intricate parts that combine functionality with aesthetic appeal. Stainless steel injection molding meets these requirements efficiently.
This method also reduces production costs, making it a preferred choice for electronics manufacturers. The ability to create complex designs without compromising quality ensures that products remain competitive in the market. I find it fascinating how this technology supports innovation in consumer electronics by enabling the development of advanced and compact devices.
Aerospace and Defense
The aerospace and defense sectors demand precision, reliability, and strength in every component. I have seen how stainless steel injection molding meets these stringent requirements with unmatched efficiency. This process enables the production of intricate parts that perform under extreme conditions, such as high temperatures, pressure, and corrosive environments.
In aerospace applications, manufacturers rely on this technology to create components for jet engines, fuel systems, and structural assemblies. The ability to produce lightweight yet durable parts enhances aircraft performance and fuel efficiency. For example, stainless steel grades like 17-4 PH provide the necessary strength and corrosion resistance for critical aerospace components. I find it remarkable how this method ensures consistency and precision, which are essential for maintaining safety standards in aviation.
The defense industry also benefits significantly from stainless steel injection molding. This process supports the production of complex parts for weapons systems, communication devices, and surveillance equipment. The durability and strength of stainless steel ensure that these components withstand harsh environments and demanding operational conditions. I have observed how the ability to produce small, intricate parts with tight tolerances gives defense manufacturers a competitive edge.
“Stainless steel injection molding delivers components that meet the highest standards of precision, durability, and performance.” This statement underscores the transformative impact of this technology on aerospace and defense manufacturing.
By leveraging stainless steel injection molding, these industries achieve cost-effective production without compromising quality. The process minimizes material waste and reduces the need for secondary operations, making it an ideal choice for high-performance applications. I believe this technology will continue to play a pivotal role in advancing aerospace and defense innovations.
Comparison with Other Manufacturing Methods
Stainless Steel Injection Molding vs. Machining
I often compare stainless steel injection molding to machining when evaluating manufacturing methods. Machining involves cutting material from a solid block to create the desired shape. While machining excels in producing low-volume, custom parts, it struggles with efficiency for high-volume production. Stainless steel injection molding, on the other hand, thrives in mass production. It allows manufacturers to produce thousands of identical components with minimal material waste.
Machining generates significant scrap material, especially when working with stainless steel. This waste increases costs and impacts sustainability. In contrast, stainless steel injection molding uses feedstock efficiently, reducing waste to nearly zero. I find this aspect particularly valuable for industries prioritizing cost-effectiveness and environmental responsibility.
Another key difference lies in design flexibility. Machining imposes limitations on complex geometries due to tool access and cutting constraints. Stainless steel injection molding overcomes these challenges by injecting molten feedstock into molds. This process captures intricate details and produces parts with tight tolerances. For example, aerospace and medical industries benefit from the ability to create small, precise components that machining cannot replicate.
The time factor also sets these methods apart. Machining requires multiple steps, including setup, cutting, and finishing. Stainless steel injection molding consolidates these steps into a single process. This efficiency reduces lead times and accelerates production schedules. I have seen how this advantage helps manufacturers meet tight deadlines without compromising quality.
“Stainless steel injection molding minimizes waste and maximizes efficiency, making it ideal for high-volume production.” This statement highlights why I often recommend this method over machining for large-scale projects.
Stainless Steel Injection Molding vs. Casting
Casting and stainless steel injection molding share similarities, as both involve shaping molten material. However, their differences become evident when examining precision, material usage, and application suitability. Casting pours molten metal into molds, which solidifies into the desired shape. While effective for large parts, casting struggles with achieving the fine details and tight tolerances required for smaller components.
Stainless steel injection molding excels in producing intricate parts with exceptional dimensional accuracy. I have observed how this method consistently delivers components with complex geometries, such as those used in consumer electronics and medical devices. Casting, on the other hand, often requires secondary machining to achieve similar precision, increasing production time and costs.
Material properties also differ between these methods. Casting can result in porosity and uneven density, which compromise strength and durability. Stainless steel injection molding eliminates these issues through the sintering process. This step fuses metal particles, creating dense and robust components. For industries like aerospace and defense, where reliability is critical, this advantage makes stainless steel injection molding the preferred choice.
Production efficiency further distinguishes these methods. Casting involves longer cooling times and more labor-intensive processes. Stainless steel injection molding streamlines production with automated systems, reducing labor costs and improving consistency. I find this efficiency particularly beneficial for industries requiring high-volume production without sacrificing quality.
“The sintering process in stainless steel injection molding ensures superior strength and durability compared to casting.” This insight underscores why I advocate for this method in demanding applications.
By comparing stainless steel injection molding to machining and casting, I see how it offers unmatched precision, efficiency, and material utilization. These advantages make it a transformative technology in modern manufacturing.
Stainless steel injection molding has proven itself as a transformative manufacturing method. It combines precision, cost-effectiveness, and durability to produce intricate components with superior mechanical properties. I have seen how its streamlined process reduces material waste and labor costs while supporting complex designs that machining and casting cannot achieve. Industries like automotive, aerospace, and medical devices rely on this technology for its unmatched efficiency and reliability. I encourage manufacturers to explore its potential for creating high-quality parts that meet modern demands.
FAQ
What is stainless steel injection molding?
Stainless steel injection molding, often called Metal Injection Molding (MIM), is a manufacturing process that combines metal powders with binders to create intricate and high-precision components. I have seen how this method allows for the production of small, complex parts with exceptional dimensional accuracy. The process involves molding, debinding, and sintering to achieve the final product’s desired strength and density.
Why is stainless steel preferred in injection molding?
Stainless steel offers unique properties like corrosion resistance, mechanical strength, and durability. I often recommend 420 stainless steel for its high hardness, wear resistance, and excellent corrosion resistance. These qualities make it ideal for applications in industries such as automotive, medical devices, and aerospace. Its ability to maintain dimensional stability under stress further enhances its appeal.
What are the advantages of using 420 stainless steel in MIM?
420 stainless steel provides several benefits in metal injection molding. I have observed its high hardness and wear resistance, which make it suitable for demanding applications. It also offers good corrosion resistance, ensuring durability in harsh environments. Additionally, its dimensional stability during the sintering process ensures consistent quality in the final product.
How does stainless steel injection molding compare to traditional machining?
Stainless steel injection molding excels in producing high-volume, intricate parts with minimal material waste. Unlike machining, which generates significant scrap material, this process uses feedstock efficiently. I have noticed how it supports complex geometries that machining struggles to achieve. It also reduces production time by eliminating secondary operations, making it a cost-effective alternative.
Can stainless steel injection molding produce durable components?
Yes, stainless steel injection molding creates highly durable components. The sintering process fuses metal particles, resulting in dense and robust parts. I have seen how this method produces components capable of withstanding high stress, wear, and corrosive environments. Stainless steel’s inherent properties further enhance the durability of these parts.
What industries benefit the most from stainless steel injection molding?
Several industries rely on stainless steel injection molding for its precision and efficiency. I have observed its widespread use in automotive, medical devices, aerospace, and consumer electronics. For example, the automotive sector uses it for engine components, while the medical field relies on it for surgical tools and implants. Its versatility makes it valuable across various applications.
How does the sintering process improve the final product?
The sintering process plays a critical role in enhancing the final product’s properties. During this phase, the “brown” part is heated to near the melting point of stainless steel, causing the metal particles to fuse. I have seen how this step eliminates porosity, increases density, and improves mechanical strength. It also allows for slight adjustments in dimensions, ensuring exceptional accuracy.
Is stainless steel injection molding environmentally friendly?
Yes, stainless steel injection molding minimizes material waste, making it an environmentally friendly option. The feedstock’s efficient usage reduces scrap compared to traditional methods like machining. I believe this aspect aligns with sustainability goals, especially for industries aiming to reduce their environmental impact.
What are the limitations of stainless steel injection molding?
While stainless steel injection molding offers many advantages, it has some limitations. I have noticed that the initial tooling costs can be high, making it less suitable for low-volume production. The process also requires precise control during debinding and sintering to avoid defects. However, these challenges are outweighed by its benefits in high-volume and complex part production.
How do I determine if stainless steel injection molding is right for my project?
To decide if stainless steel injection molding suits your project, consider factors like part complexity, production volume, and material requirements. I always recommend this method for intricate designs and high-volume production. If your application demands durability, precision, and cost-effectiveness, stainless steel injection molding could be the ideal choice. Consulting with experts can help you evaluate its feasibility for your specific needs.