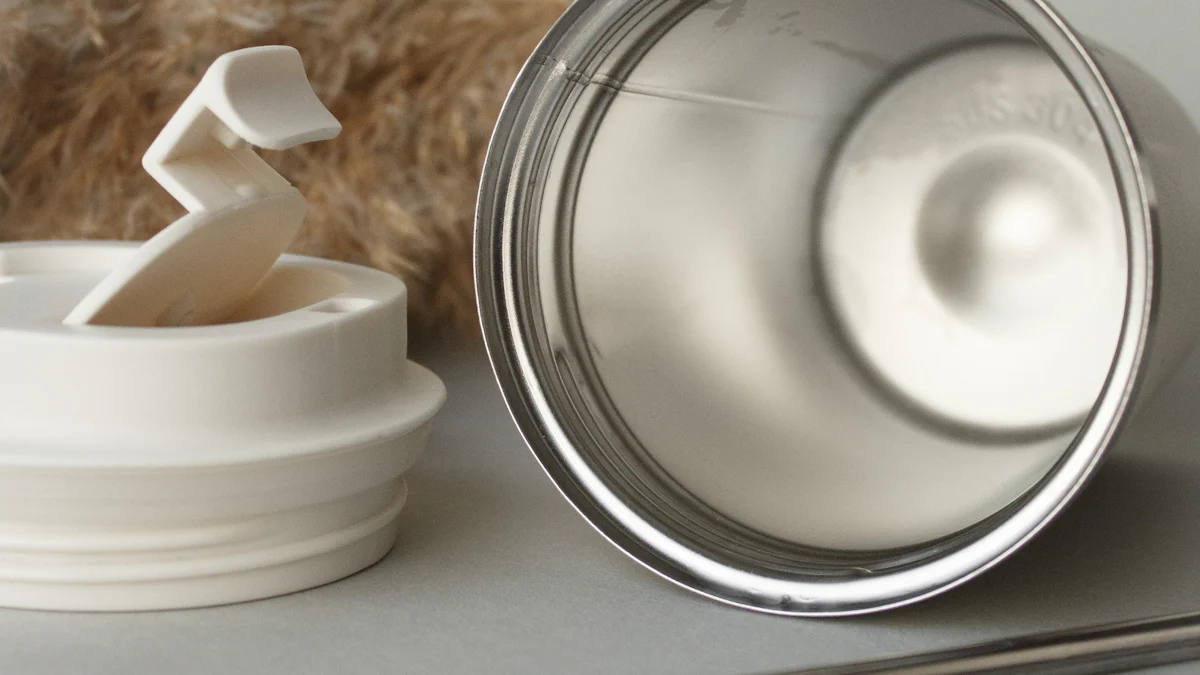
Stainless steel grades explained classify this versatile alloy based on its composition and performance. Each grade offers unique properties, making it suitable for specific uses. For example, industries like mechanical engineering consumed 28.6% of global stainless steel in 2022, while electrical machinery accounted for 8%. These grades ensure the material meets diverse demands, from corrosion resistance in chemical plants to strength in vehicle exhaust systems. Selecting the right grade directly impacts durability, efficiency, and cost-effectiveness. Understanding these classifications empowers professionals to make informed decisions tailored to their applications.
Key Takeaways
- Stainless steel grades are classified based on their composition and performance, impacting their suitability for various applications.
- Understanding the unique properties of each grade, such as corrosion resistance and strength, is crucial for making informed material choices.
- Austenitic grades like 304 and 316 are ideal for environments exposed to moisture and chemicals, while ferritic grades like 430 are more cost-effective for decorative uses.
- Selecting the right stainless steel grade can enhance durability, efficiency, and cost-effectiveness in both industrial and consumer applications.
- Factors to consider when choosing a grade include corrosion resistance, strength requirements, cost, and fabrication needs.
- Consulting industry standards and seeking expert advice can help ensure compliance and optimal performance in your projects.
- Regular maintenance of stainless steel is essential to preserve its protective properties and extend its lifespan.
What are stainless steel grades, and why are they important?
Definition and characteristics of stainless steel
Stainless steel is an alloy made primarily of iron, with chromium as its defining element. Chromium, at a minimum of 10%, gives stainless steel its corrosion-resistant properties. This material resists rust and staining, making it ideal for environments exposed to moisture or chemicals. Other elements like nickel, molybdenum, and carbon enhance its strength, durability, and resistance to extreme conditions.
The unique characteristics of stainless steel come from its composition. For instance, the addition of nickel improves corrosion resistance and ductility, while molybdenum increases resistance to pitting in chloride-rich environments. These properties make stainless steel versatile, suitable for industries ranging from construction to medical equipment. Its ability to maintain structural integrity under stress ensures reliability in demanding applications.
The role of grades in identifying composition and performance
Grades serve as a classification system to differentiate types of stainless steel based on their composition and performance. Each grade has a specific combination of elements tailored to meet particular requirements. For example, grade 304 contains 18% chromium and 8% nickel, offering excellent corrosion resistance and weldability. On the other hand, grade 316 includes molybdenum, which enhances its resistance to harsh chemicals and saltwater environments.
By understanding grades, professionals can identify the right material for their projects. Grades act as a guide, ensuring that the selected stainless steel meets the mechanical and environmental demands of the application. This system simplifies decision-making, reducing the risk of material failure and ensuring long-term success.
Importance of grades in industrial and consumer applications
Stainless steel grades play a critical role in both industrial and consumer applications. In industries like chemical processing, selecting the correct grade ensures resistance to corrosive substances, extending the lifespan of equipment. For example, grade 316 is often used in marine environments due to its superior resistance to saltwater corrosion. In contrast, grade 430, with lower nickel content, is more cost-effective and suitable for decorative purposes.
In consumer products, grades determine the performance and durability of items like kitchen appliances, cutlery, and automotive components. Choosing the wrong grade can lead to premature wear, increased maintenance costs, or even safety hazards. By understanding stainless steel grades, manufacturers and consumers alike can make informed decisions, balancing performance, aesthetics, and budget.
“Selecting the right stainless steel grade is crucial for optimal performance and long-term success in metal fabrication projects.” This principle highlights the importance of understanding grades to ensure durability, versatility, and cost-effectiveness in every application.
Types of stainless steel grades explained
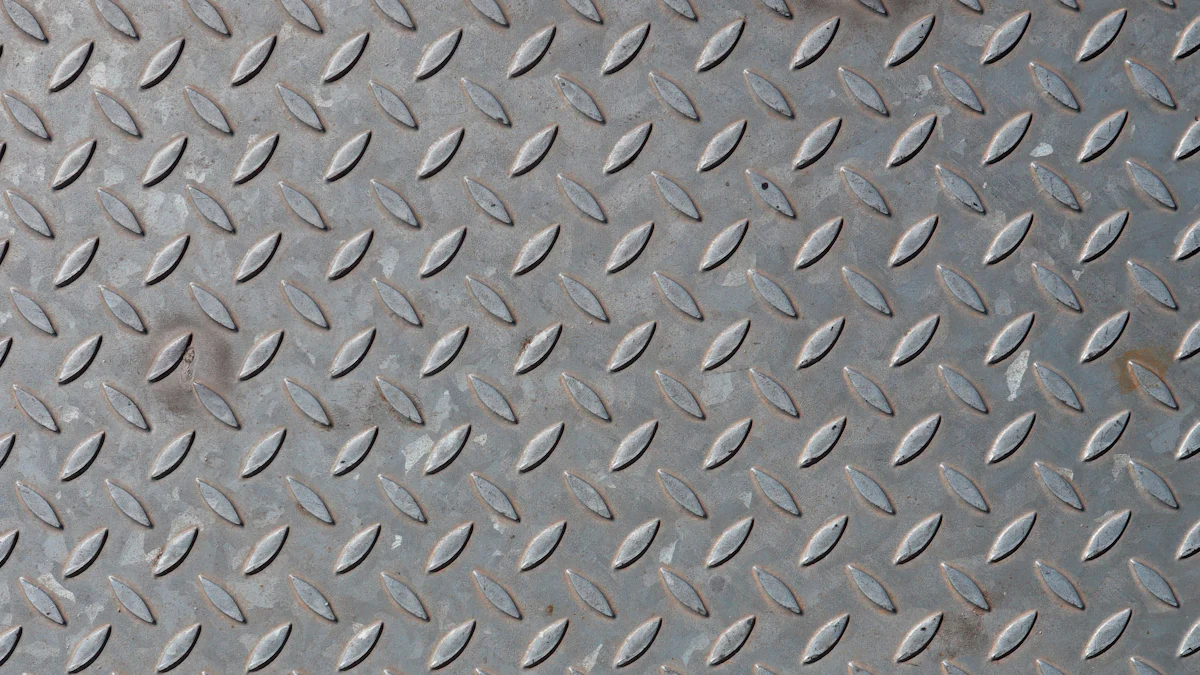
Stainless steel grades explained include several types, each with unique properties and applications. Understanding these types helps in selecting the right material for specific needs. Below, I will break down the three primary types: austenitic, ferritic, and martensitic stainless steels.
Austenitic stainless steel
Austenitic stainless steel stands out as the most widely used type. Its composition typically includes high levels of chromium (16-26%) and nickel (6-22%), which provide excellent corrosion resistance. This type also remains non-magnetic and highly ductile, making it easy to form and weld. The 300 series, including grades like 304 and 316, falls under this category.
Austenitic stainless steel performs exceptionally well in environments exposed to moisture, chemicals, or extreme temperatures. For instance, grade 304, often referred to as “18/8” stainless steel, contains 18% chromium and 8% nickel. It offers versatility and durability, making it ideal for kitchen equipment, medical devices, and architectural applications. Grade 316, with added molybdenum, provides enhanced resistance to chloride-rich environments, such as marine settings.
“Austenitic stainless steel combines superior corrosion resistance with excellent formability, making it a top choice for demanding applications.”
Ferritic stainless steel
Ferritic stainless steel features a ferrite microstructure, similar to carbon steel. It contains 10.5-27% chromium and little to no nickel, which makes it more affordable than austenitic grades. This type is magnetic and offers good corrosion resistance, particularly against stress corrosion cracking. However, it lacks the strength and ductility of austenitic stainless steel.
Ferritic stainless steel works well in less demanding environments. For example, grade 430 is commonly used in decorative applications, such as automotive trim and kitchen appliances, due to its cost-effectiveness and aesthetic appeal. While it may not match the corrosion resistance of austenitic grades, it performs adequately in mild environments and offers better resistance to nitric acid.
“Ferritic stainless steel provides a balance of affordability and corrosion resistance, making it suitable for decorative and less demanding industrial uses.”
Martensitic stainless steel
Martensitic stainless steel distinguishes itself with its high carbon content, which allows it to be hardened and strengthened through heat treatment. It typically contains 11.5-18% chromium and varying amounts of carbon. This type is magnetic and offers excellent wear resistance, hardness, and tensile strength. However, it has lower corrosion resistance compared to austenitic and ferritic grades.
Martensitic stainless steel finds applications where strength and durability are critical. For instance, it is commonly used in cutlery, surgical instruments, and turbine blades. Grades like 410 and 420 exemplify this type, offering a range of mechanical properties depending on the heat treatment applied. While it may not excel in highly corrosive environments, its robustness makes it indispensable in specific industries.
“Martensitic stainless steel delivers unmatched hardness and strength, making it ideal for tools and components requiring high durability.”
Duplex stainless steel
Duplex stainless steel combines the best qualities of austenitic and ferritic stainless steels. Its microstructure consists of approximately equal parts austenite and ferrite, which gives it a unique balance of strength and corrosion resistance. This type typically contains 19-28% chromium, 4.5-8% nickel, and small amounts of molybdenum, nitrogen, and other elements. The dual-phase structure enhances its mechanical properties, making it stronger than both austenitic and ferritic grades.
Duplex stainless steel excels in environments where high strength and resistance to stress corrosion cracking are essential. For example, industries like chemical processing, oil and gas, and marine engineering rely on this material for its durability in harsh conditions. It performs well in chloride-rich environments, such as seawater, where other grades might fail. Additionally, its lower nickel content makes it more cost-effective than austenitic stainless steel.
“Duplex stainless steel offers a remarkable combination of strength, corrosion resistance, and cost-efficiency, making it a preferred choice for demanding industrial applications.”
Despite its advantages, duplex stainless steel requires careful handling during fabrication. Its unique composition demands precise welding techniques to maintain its properties. However, when used correctly, it delivers exceptional performance and longevity, even in the most challenging environments.
Precipitation hardening stainless steel
Precipitation hardening stainless steel, often abbreviated as PH stainless steel, stands out for its ability to achieve high strength through heat treatment. This type contains chromium, nickel, and additional elements like copper and aluminum, which enable the precipitation hardening process. The heat treatment forms fine particles within the metal, significantly increasing its strength without compromising corrosion resistance.
PH stainless steel is ideal for applications requiring both high strength and moderate corrosion resistance. For instance, aerospace, automotive, and defense industries use this material for components like gears, shafts, and fasteners. Grades such as 17-4 PH (also known as grade 630) are particularly popular due to their excellent mechanical properties and ease of fabrication.
“Precipitation hardening stainless steel combines strength and corrosion resistance, making it indispensable for high-performance applications.”
This type of stainless steel offers versatility in design and manufacturing. Its ability to undergo heat treatment after fabrication allows engineers to optimize its properties for specific applications. However, it may not match the corrosion resistance of austenitic or duplex grades, so it is best suited for environments with moderate exposure to corrosive elements.
Common stainless steel grades explained
Understanding specific stainless steel grades helps in selecting the right material for various applications. Each grade offers unique properties tailored to meet different performance requirements. Below, I will explain three of the most commonly used grades: 304, 316, and 430.
304 stainless steel
Grade 304 stands as the most widely used stainless steel grade. It contains 18% chromium and 8% nickel, which provide excellent corrosion resistance and durability. This composition makes it suitable for a wide range of applications, from kitchen equipment to industrial machinery. Its non-magnetic nature and ease of fabrication further enhance its versatility.
304 stainless steel performs exceptionally well in environments exposed to moisture or mild chemicals. For example, it is commonly used in food processing equipment, sinks, and medical devices. Its ability to resist rust and staining ensures long-term reliability, even under frequent use. Additionally, its weldability and formability make it a preferred choice for complex designs.
“304 stainless steel, often referred to as ’18/8,’ combines durability with corrosion resistance, making it a staple in both industrial and consumer applications.”
316 stainless steel
Grade 316 takes the properties of 304 stainless steel a step further by adding molybdenum to its composition. This addition enhances its resistance to pitting and crevice corrosion, especially in chloride-rich environments. With 16% chromium, 10% nickel, and 2-3% molybdenum, 316 stainless steel excels in harsh conditions where other grades might fail.
Marine environments, chemical processing plants, and pharmaceutical industries often rely on 316 stainless steel. For instance, it is used in boat fittings, chemical storage tanks, and surgical instruments. Its superior corrosion resistance ensures longevity and performance in demanding applications. While it may cost more than 304, its enhanced properties justify the investment for critical uses.
“316 stainless steel offers unmatched resistance to harsh chemicals and saltwater, making it indispensable for marine and industrial applications.”
430 stainless steel
Grade 430 provides a cost-effective alternative to austenitic grades like 304 and 316. It belongs to the ferritic family, containing 16-18% chromium and little to no nickel. This composition makes it magnetic and less expensive while still offering good corrosion resistance in mild environments.
430 stainless steel is ideal for decorative and low-stress applications. For example, it is commonly used in automotive trim, kitchen appliances, and interior architectural elements. While it lacks the strength and corrosion resistance of higher grades, it performs well in environments with minimal exposure to moisture or chemicals. Its affordability and aesthetic appeal make it a popular choice for non-critical uses.
“430 stainless steel balances cost and performance, making it a practical option for decorative and light-duty applications.”
By understanding these common grades, professionals can make informed decisions based on their specific needs. Whether prioritizing corrosion resistance, strength, or cost, each grade offers distinct advantages tailored to different applications.
Comparing stainless steel grades
When choosing between stainless steel grades, understanding their differences ensures the right material for the job. Let’s compare two common pairs: 304 vs. 316 and 304 vs. 430. Each comparison highlights unique properties, applications, and performance.
304 vs. 316 stainless steel
304 and 316 stainless steels belong to the austenitic family, but their compositions set them apart. Grade 304 contains 18% chromium and 8% nickel, while grade 316 adds 2-3% molybdenum. This addition enhances 316’s resistance to pitting and crevice corrosion, especially in chloride-rich environments.
304 stainless steel works well in general-purpose applications. Industries like automotive rely on it for parts such as radiators, exhaust systems, and engine components. Its excellent corrosion resistance and ease of fabrication make it a versatile choice. However, in highly corrosive settings, 304 may fall short.
316 stainless steel excels in harsher conditions. Marine environments, chemical processing plants, and medical equipment often demand its superior corrosion resistance. For example, offshore structures and boat fittings benefit from 316’s ability to withstand saltwater exposure. Although 316 costs more than 304, its durability in extreme environments justifies the investment.
“Choose 304 for versatility and affordability. Opt for 316 when facing harsh chemicals or marine conditions.”
304 vs. 430 stainless steel
304 and 430 stainless steels differ significantly in composition and performance. Grade 304, an austenitic stainless steel, contains chromium and nickel, offering excellent corrosion resistance and non-magnetic properties. In contrast, grade 430, a ferritic stainless steel, contains chromium but little to no nickel, making it magnetic and more affordable.
304 stainless steel suits demanding applications. Its resistance to rust and staining makes it ideal for food processing equipment, medical devices, and industrial machinery. The non-magnetic nature of 304 also proves advantageous in specific technical applications.
430 stainless steel serves decorative and low-stress purposes. Automotive trim, kitchen appliances, and interior design elements often use this grade. While it lacks the strength and corrosion resistance of 304, it performs well in mild environments. Its cost-effectiveness and aesthetic appeal make it a practical choice for non-critical uses.
“304 stainless steel offers superior performance and versatility. 430 provides an economical option for decorative or light-duty applications.”
By comparing these grades, I can see how each fits specific needs. Whether prioritizing corrosion resistance, strength, or cost, understanding these differences ensures informed decisions.
How to choose the right stainless steel grade
Choosing the right stainless steel grade requires a clear understanding of your specific needs and the material’s properties. Each grade offers unique advantages, so selecting the most suitable one ensures optimal performance, durability, and cost-efficiency. Below, I will outline the key factors to consider and provide practical tips to guide your decision-making process.
Factors to consider
When selecting a stainless steel grade, I always start by evaluating the application’s requirements. Here are the primary factors to consider:
-
Corrosion Resistance
The environment plays a significant role in determining the required corrosion resistance. For example:- Grade 304 works well in general-purpose applications with mild exposure to moisture or chemicals.
- Grade 316, with its molybdenum content, offers superior resistance to harsh chemicals and saltwater, making it ideal for marine or industrial environments.
- Grade 430 provides adequate resistance in mild environments but may not perform well in highly corrosive conditions.
-
Strength and Durability
Applications requiring high strength or wear resistance demand specific grades. For instance:- Martensitic grades, like 410, excel in tools and components needing hardness and tensile strength.
- Duplex stainless steel combines strength with excellent corrosion resistance, making it suitable for demanding industrial uses.
-
Cost Considerations
Budget constraints often influence material selection. Austenitic grades like 304 and 316 tend to cost more due to their nickel content. Ferritic grades, such as 430, offer a more affordable alternative for decorative or low-stress applications. -
Magnetic Properties
If magnetic properties matter, ferritic grades like 430 are magnetic, while austenitic grades like 304 and 316 are non-magnetic. This distinction can be critical in certain technical or industrial applications. -
Fabrication and Welding Requirements
Some grades are easier to weld and form than others. For example:- Austenitic grades, such as 304 and 316, are highly ductile and easy to fabricate.
- Duplex stainless steel requires precise welding techniques to maintain its properties.
-
Aesthetic Appeal
For decorative purposes, the finish and appearance of the stainless steel matter. Grades like 430 are popular for their shiny finish and cost-effectiveness in aesthetic applications.
“Understanding the environment, application, and budget ensures the right stainless steel grade for every project.”
Practical tips for decision-making
To simplify the selection process, I recommend following these practical tips:
-
Define the Application’s Priorities
Start by listing the key requirements of your project. For example, if corrosion resistance is critical, focus on grades like 316. If cost is a priority, consider ferritic options like 430. -
Compare Grades Based on Performance
Use comparative data to evaluate grades. For instance:- 304 vs. 316: Choose 304 for general use and affordability. Opt for 316 in harsh environments like marine or chemical settings.
- 304 vs. 430: Select 304 for superior corrosion resistance and versatility. Use 430 for decorative or light-duty applications.
-
Consult Industry Standards
Refer to industry standards and specifications to ensure compliance with safety and performance requirements. For example, the SAE grade system provides valuable insights into the composition and properties of each grade. -
Test Material Samples
When in doubt, request samples of different grades and test them under actual working conditions. This approach helps confirm the material’s suitability for your application. -
Seek Expert Advice
Consult with material specialists or suppliers for guidance. Their expertise can help you navigate complex decisions and avoid costly mistakes.
By following these steps, I ensure that the chosen stainless steel grade aligns with the project’s demands. This approach minimizes risks, enhances performance, and optimizes costs.
“The right stainless steel grade balances performance, durability, and budget, ensuring long-term success in any application.”
Stainless steel grades explained the importance of understanding material properties for diverse applications. Each grade, like 304, 316, or 430, offers unique benefits tailored to specific needs. I always emphasize evaluating factors such as environment, mechanical stresses, and fabrication processes when selecting a grade. For example, 316 excels in marine settings, while 430 suits decorative uses. By knowing these distinctions, I ensure optimal performance and cost-efficiency. Choosing the right grade not only enhances durability but also guarantees long-term success in any project.
FAQ
What makes stainless steel resistant to corrosion?
Stainless steel resists corrosion due to its chromium content. Chromium reacts with oxygen in the air to form a thin, protective oxide layer on the surface. This layer prevents rust and staining. Even if the surface gets scratched, the oxide layer regenerates, maintaining its corrosion resistance. I always recommend choosing grades with higher chromium levels for environments with harsh conditions.
How do I decide between 304 and 316 stainless steel?
The choice depends on your application. Grade 304 works well for general-purpose uses, such as kitchen equipment or industrial machinery. It offers excellent corrosion resistance and durability. Grade 316, with added molybdenum, provides superior resistance to saltwater and harsh chemicals. For marine environments or chemical processing, I suggest opting for 316. If cost is a concern and the environment is less demanding, 304 is a reliable choice.
Is stainless steel magnetic?
Not all stainless steel grades are magnetic. Austenitic grades, like 304 and 316, are generally non-magnetic due to their high nickel content. Ferritic grades, such as 430, are magnetic because of their ferrite microstructure. Martensitic grades, like 410, are also magnetic and offer high strength. If magnetic properties matter for your project, I recommend selecting ferritic or martensitic stainless steel.
Can stainless steel rust?
While stainless steel resists rust better than other metals, it can still corrode under certain conditions. Exposure to chloride-rich environments, such as seawater, can cause pitting or crevice corrosion in lower grades like 304. Grades like 316, with added molybdenum, resist these conditions better. Proper maintenance, such as regular cleaning, helps prevent rust and extends the material’s lifespan.
What is the difference between ferritic and austenitic stainless steel?
Ferritic stainless steel contains little to no nickel, making it more affordable and magnetic. It offers good corrosion resistance but lacks the strength and ductility of austenitic grades. Austenitic stainless steel, like 304 and 316, contains higher levels of nickel and chromium. This composition provides excellent corrosion resistance, non-magnetic properties, and high ductility. I recommend ferritic grades for decorative or low-stress applications and austenitic grades for demanding environments.
Why is 304 stainless steel called “18/8”?
The term “18/8” refers to the composition of grade 304 stainless steel. It contains 18% chromium and 8% nickel. This combination provides excellent corrosion resistance and durability. The nickname highlights its balanced properties, making it one of the most versatile and widely used stainless steel grades.
How do I maintain stainless steel to ensure longevity?
Maintaining stainless steel involves regular cleaning to remove dirt, grease, and contaminants. Use mild soap and water or specialized stainless steel cleaners. Avoid abrasive materials that can scratch the surface. For environments with high chloride exposure, I recommend rinsing the surface frequently to prevent pitting. Proper maintenance preserves the protective oxide layer and ensures long-term performance.
What is duplex stainless steel, and when should I use it?
Duplex stainless steel combines the properties of austenitic and ferritic grades. It offers high strength, excellent corrosion resistance, and resistance to stress corrosion cracking. Its dual-phase structure makes it suitable for demanding environments, such as chemical processing, oil and gas, and marine engineering. I suggest using duplex stainless steel when both strength and corrosion resistance are critical.
Are there cost-effective alternatives to austenitic stainless steel?
Yes, ferritic stainless steel, like grade 430, provides a cost-effective alternative. It contains little to no nickel, reducing its price while still offering good corrosion resistance in mild environments. For decorative or low-stress applications, I recommend considering ferritic grades. However, for demanding conditions, investing in austenitic grades like 304 or 316 ensures better performance.
How do I choose the right stainless steel grade for my project?
Choosing the right grade requires evaluating your project’s specific needs. Consider factors like corrosion resistance, strength, cost, and fabrication requirements. For general-purpose use, grade 304 works well. For harsh environments, grade 316 offers superior performance. If budget is a priority, ferritic grades like 430 provide an economical option. I always advise consulting with material specialists or testing samples to ensure the best fit for your application.
“Understanding the environment, application, and budget ensures the right stainless steel grade for every project.”