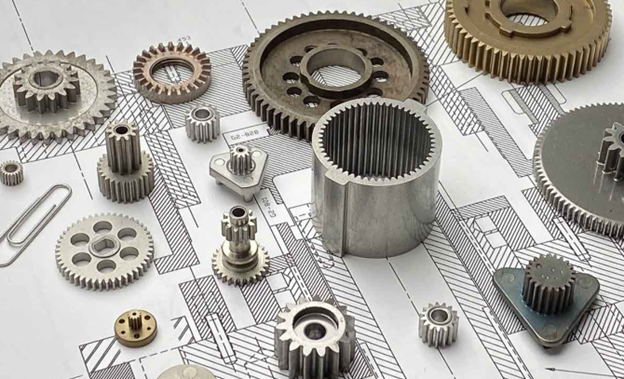
Why powder metallurgy is a green manufacturing technology? Powder metallurgy is recognized as a green manufacturing technology because it emphasizes sustainability and resource efficiency. It minimizes waste during production, ensuring high material utilization with virtually no scrap left behind. The process incorporates energy-efficient methods like sintering, which significantly reduces environmental impact. By adopting powder metallurgy, industries can align with eco-friendly practices and contribute to a cleaner, more sustainable future. Its ability to support green manufacturing principles makes it an excellent choice for reducing carbon footprints.
Key Takeaways
- Powder metallurgy minimizes waste by utilizing nearly all raw materials and recycling surplus powders, making it a highly sustainable manufacturing option.
- The process achieves near-net shape production, significantly reducing the need for additional machining and conserving both materials and energy.
- By consuming less energy than traditional methods, powder metallurgy lowers operational costs and reduces carbon emissions by up to 30%.
- Customizable materials in powder metallurgy allow for tailored alloys that meet specific performance requirements, enhancing product functionality.
- Adopting powder metallurgy supports a circular economy by emphasizing the recycling and reusing of materials throughout the production lifecycle.
- The streamlined production process of powder metallurgy not only improves efficiency but also contributes to long-term cost savings for businesses.
- Choosing powder metallurgy aligns industries with eco-friendly practices, promoting a cleaner and more sustainable future.
Understanding Why Powder Metallurgy is a Green Manufacturing Technology
The Powder Metallurgy Process
Key steps: blending, compacting, and sintering
Powder metallurgy relies on three essential steps: blending, compacting, and sintering. In the blending stage, you mix metal powders to achieve the desired composition. Compacting follows, where you press the powder into a specific shape using high pressure. Finally, sintering heats the compacted material below its melting point to bond the particles together. This process ensures precision and consistency in the final product.
The method generates minimal waste. Unlike traditional manufacturing, which often produces excess scrap, powder metallurgy uses nearly all the raw material. Any leftover powder can be collected and reused, making the process highly sustainable. Recycling plays a significant role in reducing resource consumption and environmental impact.
Minimal waste generation and material recycling
Powder metallurgy stands out for its ability to minimize waste. You can achieve near-net shape production, which means the part requires little to no additional machining. This reduces the amount of material discarded during manufacturing. Furthermore, surplus metal powders are not wasted. Instead, they are recycled back into the production cycle, ensuring maximum material efficiency.
By adopting this process, you contribute to a greener manufacturing approach. The emphasis on recycling and waste reduction aligns with sustainable practices, making powder metallurgy an eco-friendly choice.
Efficiency and Resource Conservation
High material utilization rates
High material utilization rates make powder metallurgy a practical solution for industries aiming to reduce their environmental footprint.
This high utilization rate makes powder metallurgy a practical solution for industries aiming to reduce their environmental footprint. It supports the principles of green manufacturing by ensuring that resources are used responsibly and effectively.
Reduced need for secondary machining
The near-net shape capability of powder metallurgy minimizes the need for secondary machining. You can produce complex parts with precise dimensions directly from the process. This eliminates additional steps like cutting or grinding, which consume more energy and generate waste.
By reducing secondary machining, you save time and resources. The streamlined process enhances efficiency while lowering operational costs. This approach not only benefits manufacturers but also supports sustainability by conserving energy and reducing waste.
Environmental and Cost Benefits of Powder Metallurgy
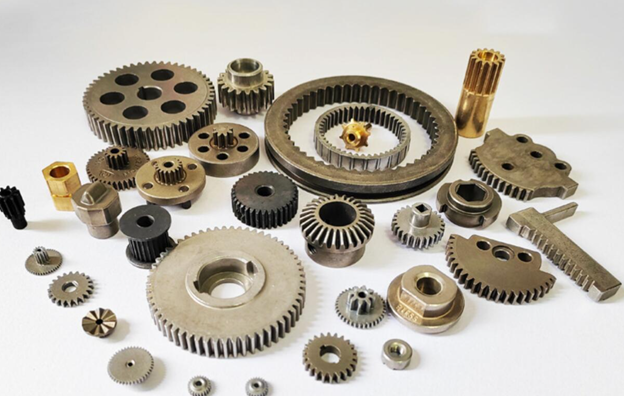
Waste Reduction and Recycling
Near-net shape production minimizes material waste
Powder metallurgy enables near-net shape production, which means you can create parts that closely match the final desired shape. This approach minimizes the need for additional machining or finishing, reducing material waste significantly. Unlike traditional manufacturing methods that often leave behind large amounts of scrap, powder metallurgy ensures that almost all the raw material is used effectively. This high level of efficiency makes it a sustainable choice for industries aiming to reduce their environmental impact.
Reuse of surplus metal powders
One of the standout features of powder metallurgy is its ability to reuse surplus metal powders. Any leftover material from the production process can be collected and reintegrated into future manufacturing cycles. This recycling capability not only conserves resources but also reduces the demand for virgin materials. By adopting this practice, you contribute to a circular economy where materials are reused rather than discarded, further supporting the principles of green manufacturing.
Energy Efficiency and Carbon Footprint
Lower energy consumption compared to traditional methods
Powder metallurgy consumes less energy compared to conventional manufacturing techniques. The process eliminates energy-intensive steps like melting and casting, which are common in traditional methods. Sintering, a key step in powder metallurgy, requires lower temperatures and shorter processing times. This energy efficiency helps you save on operational costs while reducing the overall environmental burden.
Significant reduction in CO2 emissions
By using powder metallurgy, you can achieve a significant reduction in CO2 emissions. Studies show that this process can lower carbon emissions by up to 30% compared to traditional manufacturing methods. The reduced energy consumption and minimal waste generation both contribute to this environmental benefit. Choosing powder metallurgy allows you to align with global efforts to combat climate change and promote sustainable practices.
Cost-Effectiveness
Savings from reduced material and energy use
Powder metallurgy offers substantial cost savings by optimizing material and energy use. The near-net shape production minimizes waste, ensuring that you get the most out of your raw materials. Additionally, the energy-efficient nature of the process lowers utility expenses. These savings make powder metallurgy an economically viable option for businesses looking to improve their bottom line while adopting eco-friendly practices.
Lower operational costs
The streamlined process of powder metallurgy reduces the need for secondary operations like machining or finishing. This not only saves time but also cuts down on labor and equipment costs. By simplifying the production workflow, you can achieve lower operational expenses without compromising on the quality of the final product. Powder metallurgy proves to be a cost-effective solution that supports both financial and environmental goals.
Precision, Flexibility, and Long-Term Sustainability
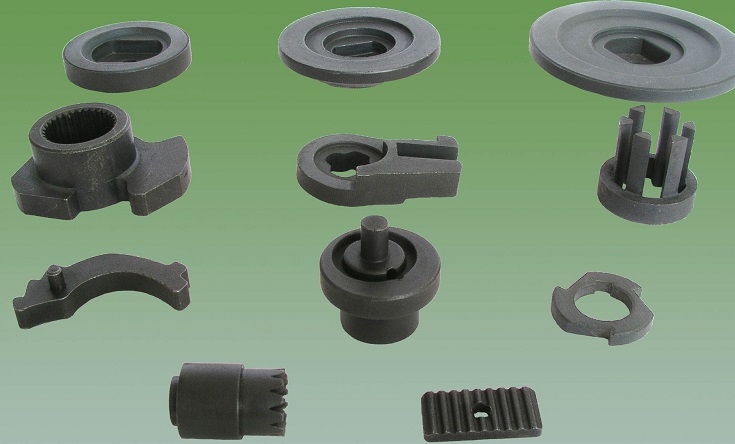
Near-Net Shape Design
Achieving complex geometries with minimal waste
Powder metallurgy allows you to create intricate and complex geometries with remarkable precision. The process molds metal powders into near-net shapes, meaning the parts produced closely resemble the final design. This eliminates the need for excessive material removal, which reduces waste significantly. You can achieve detailed designs without compromising material efficiency, making this method ideal for industries that demand precision.
The ability to produce complex shapes directly from the process also enhances sustainability. By minimizing waste, you contribute to a greener manufacturing approach. This aligns with the principles of eco-friendly production and supports efforts to reduce environmental impact.
Reducing the need for extensive machining
With powder metallurgy, you can reduce or even eliminate the need for extensive machining. The near-net shape capability ensures that parts require minimal finishing. This saves time and resources while lowering energy consumption. Traditional manufacturing often involves multiple machining steps, which generate waste and increase costs. Powder metallurgy simplifies the process, making it more efficient and sustainable.
By adopting this approach, you streamline production and conserve resources. The reduced reliance on machining not only benefits the environment but also improves operational efficiency.
Tailored Alloys and Material Optimization
Customizing materials for specific applications
Powder metallurgy gives you the flexibility to customize materials for specific applications. You can blend different metal powders to create tailored alloys that meet unique performance requirements. This customization ensures that the final product delivers optimal functionality. Whether you need high strength, corrosion resistance, or thermal conductivity, powder metallurgy allows you to achieve the desired properties.
This level of material control enhances the versatility of the process. You can produce components that are perfectly suited to their intended use, reducing the need for additional modifications. This not only saves resources but also supports sustainable manufacturing practices.
Enhancing product performance while conserving resources
The ability to optimize materials directly impacts product performance. Powder metallurgy enables you to enhance the durability and efficiency of components while conserving resources. By using only the necessary materials, you avoid overproduction and minimize waste. This approach ensures that you achieve high-quality results without unnecessary resource consumption.
Material optimization also contributes to cost savings. You can reduce expenses by using fewer raw materials and streamlining production. This makes powder metallurgy a practical choice for industries focused on sustainability and efficiency.
Supporting a Circular Economy
Recycling and reusing materials across the product lifecycle
Powder metallurgy plays a vital role in supporting a circular economy. The process emphasizes recycling and reusing materials throughout the product lifecycle. Any surplus metal powders generated during production can be collected and reintegrated into future manufacturing cycles. This reduces the need for virgin materials and promotes resource conservation.
By adopting this practice, you contribute to a sustainable manufacturing ecosystem. Recycling materials not only minimizes waste but also lowers the environmental impact of production. This aligns with global efforts to create a more circular and sustainable economy.
Reducing environmental impact through sustainable practices
Sustainable practices are at the core of powder metallurgy. The process generates minimal waste, conserves energy, and reduces carbon emissions. By reusing materials and optimizing production, you can significantly lower the environmental footprint of manufacturing. This makes powder metallurgy an excellent example of green technology.
Choosing powder metallurgy allows you to align with eco-friendly initiatives. The focus on sustainability ensures that you meet environmental standards while maintaining high-quality production. This approach supports long-term goals for a cleaner and more sustainable future.
Powder metallurgy sets a benchmark for green manufacturing. You reduce waste by utilizing nearly all raw materials and recycling surplus powders. The energy-efficient process conserves resources while lowering carbon emissions. Its precision ensures high-quality components with minimal environmental impact. By adopting this technology, you align with sustainable practices and achieve cost savings. Powder metallurgy empowers industries to embrace eco-friendly solutions and contribute to a greener future. It answers the question, “Why powder metallurgy is a green manufacturing technology?” with its unmatched sustainability and efficiency.
FAQ
What is powder metallurgy?
Powder metallurgy is a manufacturing process that uses powdered metals to create components. You blend, compact, and sinter the powders to form solid parts. This method allows you to produce precise and durable components with minimal waste.
Why is powder metallurgy considered eco-friendly?
Powder metallurgy minimizes waste by using nearly all raw materials. Any leftover powders can be recycled. The process also consumes less energy compared to traditional methods, reducing carbon emissions and supporting sustainable practices.
How does powder metallurgy reduce material waste?
Powder metallurgy achieves near-net shape production. This means the parts you create closely match the final design, requiring little to no additional machining. This reduces material waste significantly. Surplus powders are also reused, further conserving resources.
Is powder metallurgy energy-efficient?
Yes, powder metallurgy is highly energy-efficient. The sintering process operates at lower temperatures and shorter durations compared to traditional methods like casting. This reduces energy consumption and lowers operational costs.
Can powder metallurgy help reduce CO2 emissions?
Absolutely. Studies show that powder metallurgy can reduce CO2 emissions by up to 30% compared to conventional manufacturing techniques. The energy-efficient process and minimal waste generation contribute to this significant reduction.
What industries benefit from powder metallurgy?
Many industries benefit from powder metallurgy, including automotive, aerospace, medical, and electronics. You can use this process to create complex, high-performance components tailored to specific applications.
Can you customize materials in powder metallurgy?
Yes, powder metallurgy allows you to blend different metal powders to create customized alloys. This flexibility lets you meet specific performance requirements, such as strength, corrosion resistance, or thermal conductivity.
How does powder metallurgy support a circular economy?
Powder metallurgy supports a circular economy by emphasizing recycling and reusing materials. Surplus powders from production are reintegrated into future cycles. This reduces the need for virgin materials and promotes resource conservation.
Is powder metallurgy cost-effective?
Yes, powder metallurgy is cost-effective. The process minimizes material waste and energy use, which lowers production costs. The reduced need for secondary machining also saves time and labor expenses.
What makes powder metallurgy suitable for green manufacturing?
Powder metallurgy aligns with green manufacturing principles by reducing waste, conserving energy, and lowering carbon emissions. Its precision and efficiency ensure high-quality production with minimal environmental impact. This makes it an ideal choice for sustainable manufacturing.