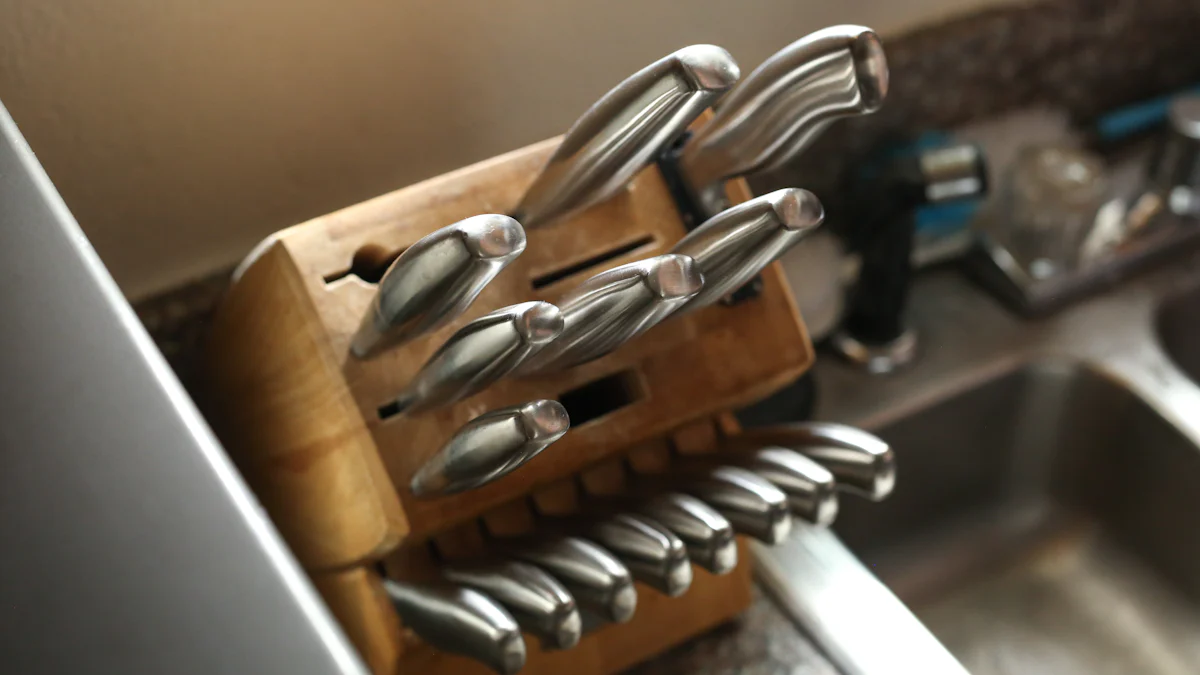
The difference between 304 and 304L stainless steel primarily lies in their carbon content. Grade 304 contains a maximum of 0.08% carbon, while 304L has a reduced carbon content of 0.03%. This seemingly minor variation significantly impacts their performance. The lower carbon in 304L minimizes the risk of carbide precipitation during welding, enhancing its corrosion resistance. This makes 304L particularly suitable for applications requiring welding, where maintaining structural integrity and resisting corrosion are crucial. Understanding these differences helps in selecting the right material for specific industrial needs.
Key Takeaways
- 304 and 304L stainless steel differ primarily in carbon content, with 304L having a lower carbon percentage, enhancing its corrosion resistance.
- The lower carbon content in 304L minimizes the risk of carbide precipitation during welding, making it ideal for applications requiring welding.
- While 304 offers greater strength and hardness, 304L provides better ductility, allowing for easier shaping and forming without cracking.
- 304L’s enhanced weldability means it often does not require post-weld heat treatment, simplifying the welding process and reducing costs.
- Choosing between 304 and 304L should be based on specific application needs, particularly regarding corrosion resistance and structural integrity.
- Both grades are widely used in various industries, with 304L being preferred in chemical processing and applications exposed to corrosive environments.
- Consider long-term costs, as 304L’s durability and lower maintenance needs can lead to lower lifecycle costs despite its higher initial price.
Chemical Composition
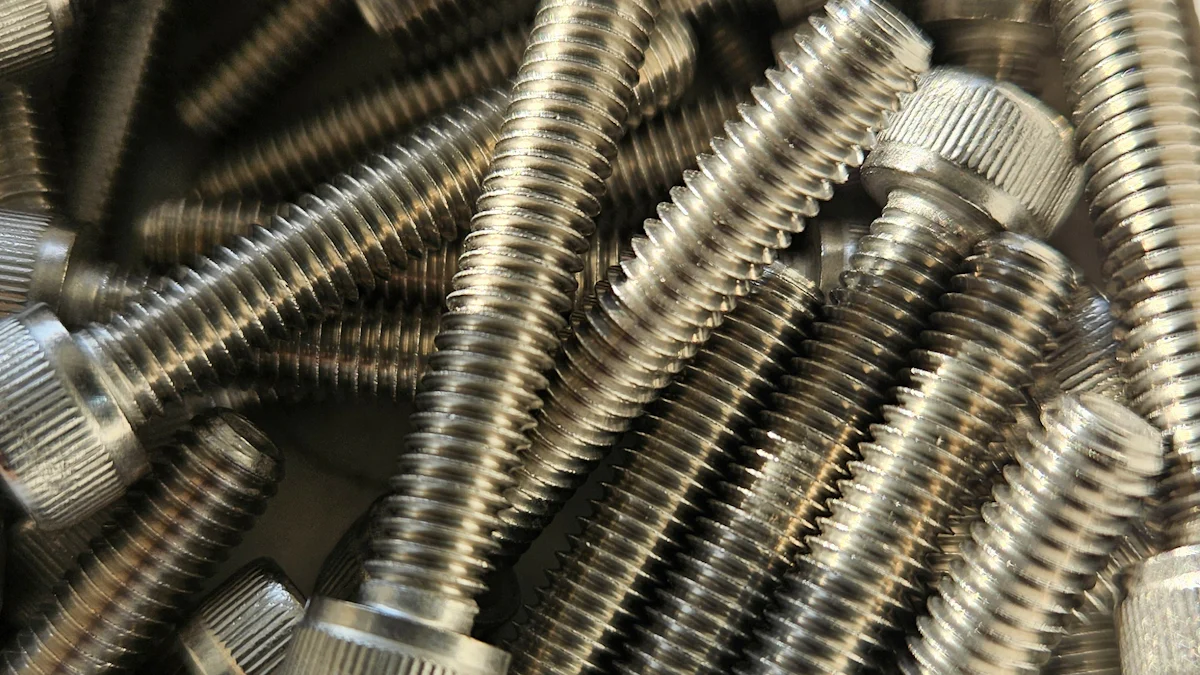
Understanding the chemical composition of stainless steel grades is crucial for selecting the right material for specific applications. The difference between 304 and 304L stainless steel primarily lies in their carbon content, which significantly influences their properties.
Carbon Content
The carbon content in stainless steel affects its performance in various environments. In grade 304, the maximum carbon content is 0.08%. In contrast, grade 304L has a reduced carbon content of 0.03%. This lower carbon content in 304L plays a pivotal role in its enhanced characteristics.
Impact on Corrosion Resistance
The carbon content directly impacts corrosion resistance. In high-temperature environments, carbon can combine with chromium to form chromium carbides. This process, known as sensitization, reduces the chromium available to form the protective oxide layer, compromising corrosion resistance. The lower carbon content in 304L minimizes this risk, making it more suitable for applications where corrosion resistance is critical, especially after welding.
Impact on Mechanical Properties
Carbon content also affects the mechanical properties of stainless steel. Higher carbon levels generally increase strength and hardness. However, they can reduce ductility. Grade 304, with its higher carbon content, offers greater strength compared to 304L. On the other hand, 304L, with its lower carbon content, provides better ductility, making it easier to form and shape without cracking.
Other Alloying Elements
Besides carbon, other alloying elements contribute to the properties of stainless steel. These elements include chromium, nickel, and trace elements, each playing a unique role in defining the characteristics of the steel.
Chromium and Nickel Content
Both 304 and 304L stainless steels contain similar amounts of chromium and nickel. Chromium, typically around 18-20%, provides corrosion resistance by forming a passive oxide layer on the surface. Nickel, usually about 8-10%, enhances the steel’s toughness and ductility. These elements remain consistent between the two grades, ensuring that both offer excellent corrosion resistance and mechanical properties.
Trace Elements
Trace elements, such as manganese, silicon, and phosphorus, are present in small quantities in both 304 and 304L. These elements can influence the steel’s machinability, weldability, and overall performance. While their concentrations are generally low, they contribute to the subtle differences in behavior between the two grades.
By understanding these chemical compositions, I can better appreciate the difference between 304 and 304L stainless steel. This knowledge aids in selecting the appropriate grade for specific industrial needs, ensuring optimal performance and longevity.
Mechanical Properties
Understanding the mechanical properties of stainless steel is crucial for selecting the right material for specific applications. The difference between 304 and 304L stainless steel extends beyond chemical composition to include variations in mechanical properties, which influence their performance in different environments.
Strength and Hardness
Strength and hardness are vital characteristics that determine how a material withstands forces without deforming.
Tensile Strength
Tensile strength measures the maximum stress a material can endure while being stretched or pulled before breaking. In general, grade 304 stainless steel exhibits higher tensile strength compared to 304L due to its higher carbon content. This increased strength makes 304 suitable for applications requiring robust structural integrity. However, the lower carbon content in 304L does not significantly compromise its tensile strength, maintaining adequate performance for many applications.
Yield Strength
Yield strength indicates the stress at which a material begins to deform plastically. Grade 304 typically offers higher yield strength than 304L, providing greater resistance to deformation under load. This property is particularly beneficial in applications where maintaining shape under stress is essential. Despite this, 304L still provides sufficient yield strength for many uses, especially where welding is involved, as its lower carbon content reduces the risk of sensitization.
Ductility and Toughness
Ductility and toughness describe a material’s ability to deform without breaking and absorb energy before fracturing, respectively.
Elongation
Elongation measures how much a material can stretch before breaking. The lower carbon content in 304L enhances its ductility, allowing it to elongate more than 304. This property makes 304L easier to form and shape, which is advantageous in manufacturing processes requiring intricate designs or complex shapes.
Impact Resistance
Impact resistance refers to a material’s ability to withstand sudden forces or shocks without fracturing. Both 304 and 304L stainless steels offer excellent impact resistance, thanks to their austenitic structure. However, the enhanced ductility of 304L can provide a slight edge in absorbing impact energy, making it a preferred choice in applications where sudden forces are a concern.
Weldability
Understanding the weldability of stainless steel is crucial for selecting the right material for applications involving welding. The difference between 304 and 304L stainless steel significantly impacts their performance in welded conditions.
Welding Techniques
When it comes to welding techniques, both 304 and 304L stainless steels offer excellent properties. However, the choice of grade can influence the suitability for different welding methods.
Suitability for Different Welding Methods
Grade 304L stands out due to its improved weldability. Its lower carbon content reduces the risk of carbide precipitation during welding. This makes it less prone to weld decay, ensuring structural integrity. I find 304L particularly suitable for applications requiring welding, as it minimizes the risk of cracking and preserves corrosion resistance. In contrast, 304 may require more careful control of welding parameters to avoid sensitization.
Post-Weld Heat Treatment
Post-weld heat treatment is often unnecessary for 304L when welding thin sections. This advantage simplifies the welding process and reduces costs. However, for thicker sections or when using 304, post-weld annealing might be necessary to restore corrosion resistance and mechanical properties. By understanding these requirements, I can make informed decisions about the need for additional treatments after welding.
Effects of Welding on Properties
Welding can alter the properties of stainless steel, affecting its performance in various environments. The effects of welding on 304 and 304L stainless steels differ due to their carbon content.
Sensitization and Corrosion
Sensitization occurs when chromium carbides form at grain boundaries during welding, reducing corrosion resistance. Grade 304L, with its lower carbon content, minimizes this risk. It maintains excellent corrosion resistance even after welding. In contrast, 304 is more susceptible to sensitization, especially in high-temperature environments. This makes 304L a preferred choice for applications where corrosion resistance is critical.
Mechanical Integrity
Welding can also impact the mechanical integrity of stainless steel. Both 304 and 304L offer good mechanical properties, but 304L’s enhanced weldability ensures better performance in welded conditions. Its lower carbon content reduces the risk of cracking and maintains ductility. This makes 304L ideal for applications where maintaining mechanical integrity after welding is essential.
By understanding these aspects of weldability, I can better appreciate the differences between 304 and 304L stainless steel. This knowledge aids in selecting the appropriate grade for specific welding applications, ensuring optimal performance and longevity.
Applications
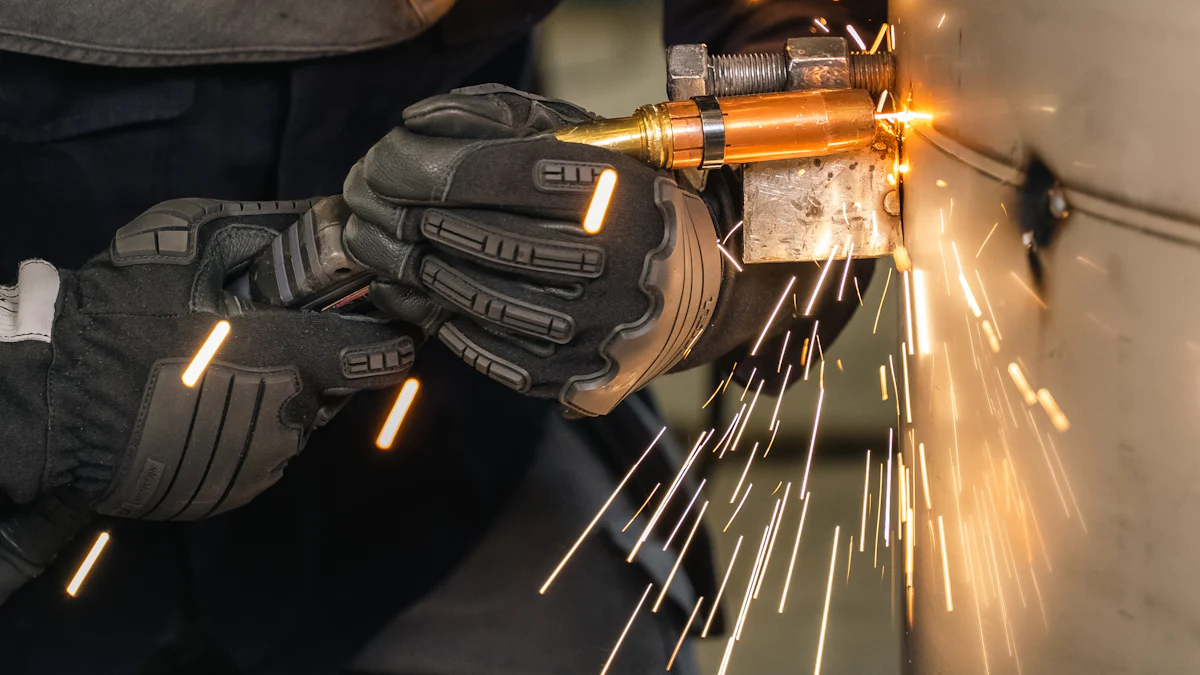
Understanding the applications of 304 and 304L stainless steel helps in selecting the right material for specific needs. Each grade offers unique advantages that make them suitable for various industries.
Common Uses of 304 Stainless Steel
304 stainless steel is a versatile material widely used across different sectors due to its excellent corrosion resistance and mechanical properties.
Industrial Applications
In industrial settings, 304 stainless steel finds extensive use. It serves as a key component in plate heat exchangers, which are crucial for efficient thermal management in chemical processing and power generation. The material’s robustness makes it ideal for auto parts and ship components, where durability is paramount. Additionally, its resistance to corrosion ensures longevity in harsh environments, making it a preferred choice for building materials and agricultural equipment.
Consumer Products
304 stainless steel also plays a significant role in consumer products. Its aesthetic appeal and resistance to rust make it suitable for household goods like kitchen appliances and utensils. The material’s non-reactive nature ensures safety in food contact applications, enhancing its desirability in the food industry. Furthermore, its ease of fabrication allows manufacturers to create intricate designs, catering to diverse consumer preferences.
Common Uses of 304L Stainless Steel
304L stainless steel offers distinct advantages, particularly in applications requiring welding or exposure to corrosive environments.
Chemical Processing
In chemical processing, 304L stainless steel stands out due to its enhanced corrosion resistance. The lower carbon content minimizes the risk of sensitization, ensuring the material maintains its integrity even after welding. This property makes it suitable for chemical containers and equipment exposed to aggressive substances. Its ability to withstand corrosive environments ensures reliability and safety in chemical plants.
Construction and Architecture
The construction and architecture sectors benefit from 304L stainless steel’s properties. Its formability allows for the creation of complex architectural designs, while its corrosion resistance ensures durability in outdoor applications. The material’s aesthetic appeal adds value to architectural trim and decorative elements. Moreover, its structural integrity makes it a reliable choice for construction materials, providing strength and longevity in various building projects.
By understanding the difference between 304 and 304L stainless steel, I can make informed decisions about their applications. Each grade offers unique benefits that cater to specific industrial and consumer needs, ensuring optimal performance and longevity.
Cost Implications
Understanding the cost implications of choosing between 304 and 304L stainless steel is crucial for making informed decisions. Each grade presents unique financial considerations that can impact both initial and long-term expenses.
Material Costs
When evaluating material costs, I consider both price differences and availability. These factors play a significant role in determining the overall expense of using either grade.
Price Differences
The price of 304L stainless steel tends to be slightly higher than that of 304 stainless steel. This difference arises from the enhanced weldability and lower carbon content of 304L, which require more precise manufacturing processes. The additional steps involved in producing 304L contribute to its increased cost. Despite this, the investment in 304L can be justified by its superior performance in applications requiring welding and corrosion resistance.
Availability
Availability can influence material costs as well. Both 304 and 304L stainless steels are widely available, but regional demand and supply chain factors can affect their accessibility. In some cases, the higher demand for 304L in industries like chemical processing and food production may lead to fluctuations in its availability. I find it essential to consider these factors when planning projects to ensure timely procurement and avoid potential delays.
Long-term Cost Considerations
Beyond initial material costs, I must also evaluate long-term cost considerations. These include maintenance, durability, and lifecycle costs, which can significantly impact the total cost of ownership.
Maintenance and Durability
Maintenance and durability are critical factors in assessing long-term costs. 304L stainless steel offers enhanced corrosion resistance, reducing the need for frequent maintenance and repairs. Its lower carbon content minimizes the risk of carbide precipitation during welding, ensuring structural integrity over time. This durability translates into lower maintenance costs, making 304L a cost-effective choice for applications exposed to harsh environments.
Lifecycle Costs
Lifecycle costs encompass the total expenses associated with a material throughout its lifespan. While 304 stainless steel may have a lower initial cost, the potential for increased maintenance and reduced corrosion resistance can lead to higher lifecycle costs. In contrast, the superior performance of 304L in welded and corrosive conditions can result in lower overall expenses. By considering these factors, I can make informed decisions that align with budgetary constraints and project requirements.
In conclusion, the difference between 304 and 304L stainless steel lies primarily in their carbon content. This distinction affects their corrosion resistance and mechanical properties. 304L, with its lower carbon content, offers enhanced weldability and corrosion resistance, making it ideal for applications involving welding or exposure to corrosive environments. When choosing between these grades, I consider the specific requirements of the application. For projects demanding superior corrosion resistance and structural integrity, 304L often emerges as the preferred choice. Understanding these differences ensures optimal material selection for diverse industrial needs.
FAQ
What is 304L stainless steel?
304L stainless steel is a variant of the widely used 304 stainless steel, known for its lower carbon content. This reduction in carbon enhances its corrosion resistance, especially after welding. It finds applications in industries like chemical processing, medical equipment, food processing, and marine equipment due to its excellent weldability and corrosion resistance.
What is the difference between 304 and 304L stainless steel?
The primary difference between 304 and 304L stainless steel lies in their carbon content. 304L has a lower carbon content (less than 0.03%) compared to 304 (up to 0.08%). This difference provides 304L with better corrosion resistance after welding, making it suitable for applications where welding is required.
Why would anyone want to use 304L if it is weaker than standard 304 stainless steel?
Despite being slightly weaker than 304, 304L offers significant advantages in specific applications. Its lower carbon content reduces the risk of sensitization during welding, enhancing its corrosion resistance. This makes 304L ideal for environments where welding is necessary and corrosion resistance is critical.
What are the key properties of 304L stainless steel?
304L stainless steel boasts several key properties, including high corrosion resistance, excellent formability, and weldability. It also offers great low-temperature properties and responds well to hardening by cold working. These attributes, combined with its affordable cost, make it a popular choice for various industrial applications.
Can 304L stainless steel be used in food processing?
Yes, 304L stainless steel is suitable for food processing applications. Its corrosion resistance and non-reactive nature make it safe for contact with food. Additionally, its excellent formability allows for the creation of intricate designs, catering to the diverse needs of the food industry.
Is 304L stainless steel more expensive than 304?
Generally, 304L stainless steel is slightly more expensive than 304 due to its enhanced properties and lower carbon content. The additional manufacturing processes required to achieve these characteristics contribute to the increased cost. However, the investment in 304L can be justified by its superior performance in specific applications.
How does the lower carbon content in 304L affect its performance?
The lower carbon content in 304L stainless steel minimizes the risk of carbide precipitation during welding. This reduction enhances its corrosion resistance, particularly in welded conditions. As a result, 304L maintains its structural integrity and resists corrosion more effectively than 304 in certain environments.
What industries commonly use 304L stainless steel?
Industries such as chemical processing, medical equipment manufacturing, food processing, and marine equipment commonly use 304L stainless steel. Its excellent weldability and corrosion resistance make it ideal for applications requiring these properties.
Does 304L stainless steel require post-weld heat treatment?
In most cases, 304L stainless steel does not require post-weld heat treatment, especially for thin sections. Its lower carbon content reduces the risk of sensitization, eliminating the need for additional treatments. However, for thicker sections, post-weld annealing might be necessary to restore corrosion resistance and mechanical properties.
How does 304L stainless steel perform in high-temperature environments?
304L stainless steel performs well in high-temperature environments, thanks to its excellent oxidation resistance. Its lower carbon content reduces the risk of sensitization, maintaining its corrosion resistance even at elevated temperatures. This makes it suitable for applications exposed to high heat.