Sintered Gears
The sintered gear with higher strength can be made of copper-permeated sintered steel with a density of 90 ~ 95% theoretical value, low connectivity porosity, and smooth operation. Sintered gears with higher oil content are required to enhance self-lubrication and wear resistance.
The performance of the sintered gear is closely related to the powder metallurgy process, and the performance of the gear produced by different processes and technical routes is very different, and the development of powder metallurgy technology promotes the improvement of the performance of the sintered gear and the stability of the size. The technologies developed in recent years such as warm forming, high-speed forming, sintering hardening, high-temperature sintering, melting, and gear surface densification are expected to achieve high density, low cost, and high precision gear production at the same time.
Sintered gears vs machined
As an important part of the transmission system, the gear is generally made by mechanical processing. However, with the development of the automobile industry, the requirements for gear and other parts are getting higher and higher, and it is difficult to meet the requirements in terms of cost, delivery date, and noise; Powder metallurgy is a technology that can manufacture complex shaped parts, which can save material, energy, labor, high quality, suitable for mass production, and can meet the requirements of the automotive industry for parts.
Through the use of high-performance powder forming, sintering, and special post-processing, the powder metallurgy process has been able to produce gears with densities exceeding 7.5g/cm3. The use of these technologies has successfully replaced parts machined or machined by other methods. The success of the powder metallurgy process has made it possible for mechanical engineers to design high-performance and lower-cost parts. At present, the gear parts used in automobiles are synchronizer gear hubs, clutch gear hubs, and so on.
Benefits of Sintered Gears
Sintered gears offer several compelling advantages, making them ideal for a variety of applications:
- High Precision: Sintered gears enable the production of intricately shaped components with tight tolerances, providing design flexibility for both custom applications and mass production. This is challenging and often cost-prohibitive with traditional machining methods.
- Cost-Efficiency: Powder metallurgy generates minimal waste, with material utilization exceeding 95%. The process eliminates the need for secondary operations like hobbing and grinding, reducing both production time and costs.
- Outstanding Mechanical Properties: The ability to combine different metals allows sintered gears to exhibit excellent mechanical properties such as high tensile strength, durability, and load-bearing capacity. Their smooth and quiet operation makes them suitable for demanding applications.
- Design Flexibility: The additive nature of powder metallurgy enables the creation of complex geometries that would be impossible to achieve with traditional machining, offering significant design freedom.
- Environmentally Sound: Sintered gears are produced with minimal waste and lower energy usage, making powder metallurgy an environmentally friendly and economical process compared to traditional machining or casting.
These advantages make sintered gears a highly effective choice for industries requiring precision, performance, and sustainability.
- Sintered gear materials
Materials
property |
Copper impregnated steel | Nickel steel | Low alloy steel | |||
13Cu-0.8C-Fe | 2Ni-0.5C-1.5Cu-Fe | 0.4Mn-0.5Ni-0.6Mo-0.5C-Fe | ||||
Since 871C quenching and tem | Sintered | Since 871C quenching and tem | Sintered | Since 871C quenching and tem | Sintered | |
Ddensity (g/cm) | 7.3 | 7.3 | 6.8 | 6.8 | 6.7 | 6.8 |
Ultimate tensile strength(kgf/mm) | 80.5 | 59.5 | 66.5 | 36 | 78.4 | 35 |
Tensile yield strength, residual deformation 0.2%(kgf/mm) | 74.9 | 40.5 | 56 | 28 | 72.1 | 29 |
Elongation(%) | 0.5 | 3.0 | 0.8 | 1.5 | 0.6 | 1.0 |
Apparent hardness | HRC 38 | HRB89 | HRC 24 | HRB65 | HRC 29 | HRB60 |
Particle hardness | HRC58 | N/D | HRC 40 | N/D | HRC 44 | N/D |
Impact strength (Charlton value, no notch)(kgf.m) | 0.87 | 1.4 | 1.38 | 1.0 | 1.24 | 0.9 |
Stainless Steel Sintered Gears
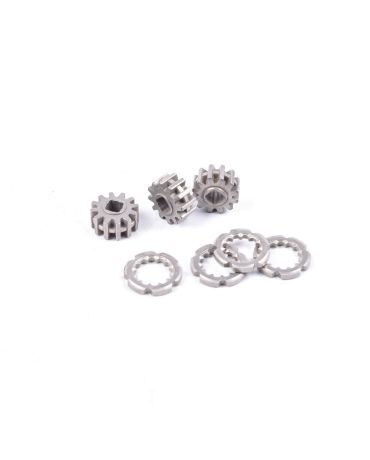

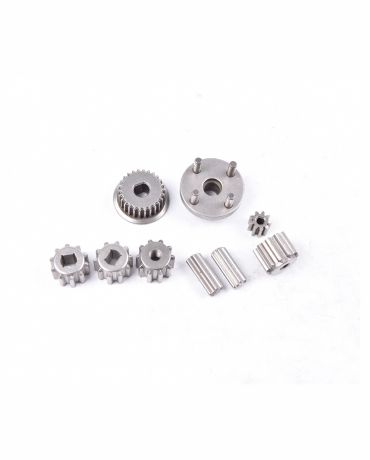
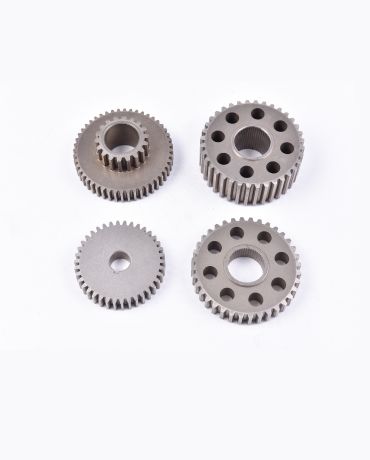
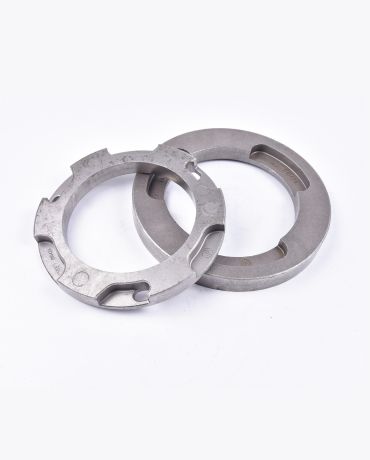
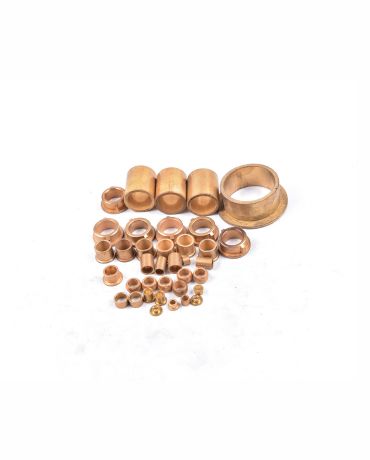
Yes, this is a routine operation for most companies before inquiring.
We have metal 3D printing equipment and can provide sample 3D printing.
3D drawings allow engineers to better understand the structure of the product, and 2D documents can provide more information, including materials, tolerances, surface treatment, etc. More detailed information is conducive to more accurate quotation by engineers.
In the case of detailed inquiry drawings and information, it usually only takes 2-3 days for us to give you a detailed quotation, including the product price and mold price.
After confirming the order, we usually take 5-7 days to prepare the DFM report of the product. After confirmation, we spend 25 days to complete the mold, and provide T1 samples to customers for testing in the following 10-15 days.
If there is a problem with the test, we will re-sample it for free based on the feedback and provide a suitable sample.
MIM products MOQ 2000 PCS
CNC products MOQ 2000 PCS
Alu die casting, MOQ 2000 PCS
PM product MOQ 5000 PCS
Typically, the lead time for processing and submitting samples is 30 days. However, according to the order quantity and special requirements of customers, we can extend or shorten the delivery cycle accordingly.
1-year product warranty
World-class testing equipment
30+QC Workers
Key sizes 100% checking before shipment
ISO9001+IATF16949
Usually T/T is used as the payment method
Mold: 50% deposit, 50% payment after confirming the sample.
Bulk production: 30% deposit, 30% see bill of lading Copy, pay 70% balance.