Powder Metallurgy Applications in Motorcycles have become a game-changer in motorcycle manufacturing. You benefit from its ability to produce components close to their final shape, which enhances production efficiency and reduces costs. This process minimizes material waste and eliminates the need for extensive machining. By enabling lightweight, high-precision parts, Powder Metallurgy Applications in Motorcycles improve performance and fuel efficiency, making it indispensable in modern motorcycles.
Key Takeaways
- Powder metallurgy helps make motorcycles better by creating light, strong parts. These parts improve how motorcycles work and save fuel.
- This method cuts down on wasted materials and lowers costs. It shapes parts almost perfectly, making it eco-friendly for makers.
- Parts like brake pads and valve guides last longer and need less care. They are tough and can lubricate themselves, saving time and money.
Benefits of Powder Metallurgy in Motorcycles
Cost-Effectiveness and Waste Reduction
Powder metallurgy offers significant cost savings in motorcycle manufacturing. You can produce components close to their final shape, reducing the need for extensive machining. This process minimizes material waste and optimizes production efficiency.
- Powder metallurgy allows for net-shape or near-net-shape forming, efficiently using nearly all material input.
- Unlike traditional methods that remove excess material, powder metallurgy uses only the required amount, reducing waste.
- By compressing metal powders into precise forms, this method can utilize up to 90% less material than conventional machining.
These advantages make powder metallurgy a sustainable and cost-effective solution for motorcycle manufacturers.
Lightweight and High-Strength Components
Motorcycle performance depends on lightweight yet durable components. Powder metallurgy enables you to achieve this balance by producing high-strength parts with reduced weight. Here are some examples of components made using this technology:
Component Type | Description |
---|---|
Shock Absorber Pistons | Complex internal structures with high wear resistance for improved damping performance. |
Driven Gear | Transmits power from the engine to other gears in the transmission system. |
Motorcycle Valve Guide | Ensures proper alignment of the valve stem for smooth operation. |
Motorbike Camshaft Governor | Regulates engine speed by controlling the camshaft. |
Motorcycle Clutch Friction Plate | Engages and disengages the clutch to transmit power from the engine to the transmission. |
Sintered Brake Pads | Essential for the braking system, contributing to safe motorcycling. |
Intake and Exhaust Valve Seats | Designed to withstand high temperatures, enhancing durability in engine applications. |
These components demonstrate how powder metallurgy enhances motorcycle performance while maintaining structural integrity.
Enhanced Durability and Self-Lubrication
Durability is critical for motorcycle components exposed to heavy loads and extreme conditions. Powder metallurgy ensures high strength and wear resistance, which are essential for long-lasting performance. The sintering process compresses and fuses metal powders, creating robust parts that withstand demanding environments.
Self-lubrication further improves performance by reducing friction and wear. Powder metal components are impregnated with oil, creating a self-lubricating effect. This feature eliminates the need for additional lubrication, extends the service life of components, and reduces maintenance frequency. You benefit from smoother operation and lower long-term costs.
Powder Metallurgy Components in Motorcycles
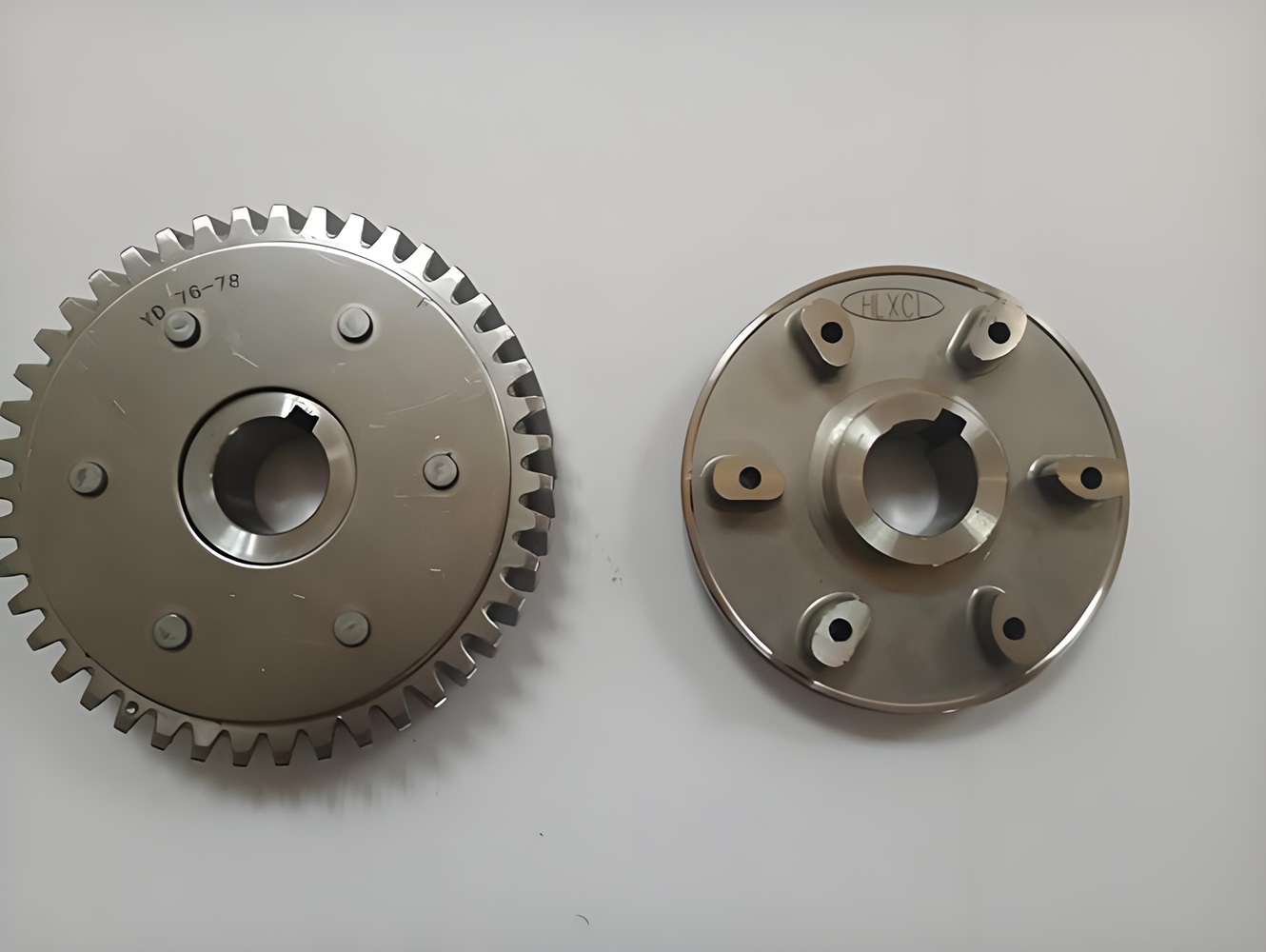
Engine Components (Valve Guides, Camshaft Governors, Oil Pump Rotors)
Powder metallurgy plays a vital role in manufacturing engine components, ensuring high strength and precision. You can find several key parts made using this technology:
- Motorcycle Valve Guide: Aligns the valve stem for smooth operation and reduces wear by transferring heat efficiently.
- Motorbike Camshaft Governor: Regulates engine speed with exceptional precision, ensuring safe and reliable performance.
- Oil Pump Rotors: Circulate oil throughout the engine, reducing friction and preventing overheating.
These components enhance engine efficiency by enduring heavy loads and extreme conditions. The precision manufacturing process allows intricate geometries, improving reliability and reducing production costs.
Transmission System (Driven Gears, Shift Drum Segments)
Transmission components benefit significantly from powder metallurgy. Driven gears and shift drum segments are prime examples:
Feature | Powder Metallurgy | Traditional Methods (Casting/Machining) |
---|---|---|
Design Flexibility | Allows for complex shapes and intricate features | Limited by draft angles and wall thickness |
Material Utilization | Superior with minimal waste | Generates more waste |
Tooling Costs | Generally lower overall costs | Requires significant investment in dies |
Batch-to-Batch Consistency | High consistency due to controlled processes | Varies significantly |
Driven gears transfer power efficiently, while shift drum segments ensure smooth gear engagement. These components offer superior wear resistance and reduced noise, enhancing the overall transmission system.
Shock Absorber Parts (Pistons, Valves)
Shock absorber pistons and valves, manufactured using powder metallurgy, improve ride quality. Pistons feature complex internal structures that enhance damping performance, while valves control hydraulic oil flow for stability. High-precision surfaces reduce friction, ensuring smoother handling and greater comfort during rides.
Brake and Clutch Components (Brake Pads, Clutch Friction Plates)
Powder metallurgy enhances safety and performance in braking and clutch systems. Sintered brake pads provide:
- High Durability: Ideal for high-performance motorcycles.
- Good Heat Dissipation: Prevents brake failure during heavy braking.
- Excellent Stopping Power: Performs well in wet and dry conditions.
Clutch friction plates, made from high-friction composite materials, withstand extreme temperatures and wear, ensuring reliable power transmission.
Timing System Components (Timing Pulleys, Sprockets)
Timing system components like timing pulleys and camshaft sprockets rely on powder metallurgy for precision and durability. Timing pulleys synchronize the camshaft and crankshaft, while camshaft sprockets control valve timing. These components ensure reliable engine operation under high stress.
Real-World Applications and Industry Trends
Examples of Motorcycles Using Powder Metallurgy Components
Powder metallurgy has revolutionized motorcycle manufacturing, with several well-known models benefiting from its advanced components. You can find examples like:
- Honda CG125: This model incorporates powder metallurgy valve guides, ensuring smooth valve operation and enhanced durability.
- Honda CD70: Known for its reliability, this motorcycle uses powder metallurgy components to improve engine efficiency and reduce wear.
These motorcycles demonstrate how powder metallurgy enhances performance, durability, and cost-effectiveness. By integrating this technology, manufacturers achieve high-precision parts that withstand demanding conditions, ensuring a superior riding experience.
Innovations in Powder Metallurgy for Motorcycle Manufacturing
Recent advancements in powder metallurgy continue to shape the future of motorcycle production. Manufacturers are leveraging this technology to improve efficiency, performance, and sustainability. Key innovations include:
- Efficiency: Powder metallurgy has significantly increased the production speed of components like gear hubs, reducing manufacturing time.
- Performance: Parts produced through this method exhibit enhanced strength, wear resistance, and precision, ensuring optimal motorcycle performance.
- Cost-effectiveness: By producing components close to their final shape, powder metallurgy minimizes material waste and reduces overall production costs.
Additionally, this technology champions sustainability by reducing dependence on virgin materials and promoting a closed-loop system. The sintering process generates minimal waste and consumes less energy, making it an environmentally friendly choice. As the industry adopts these innovations, you can expect motorcycles to become more efficient, durable, and eco-friendly.
Powder metallurgy revolutionizes motorcycle manufacturing by delivering high-precision, lightweight, and durable components. Its ability to reduce waste and enhance efficiency makes it a sustainable choice.
🚀 Tip: By adopting powder metallurgy, you can improve performance, cut costs, and contribute to eco-friendly practices. Explore its potential for your motorcycle projects today!
FAQ
What is powder metallurgy, and why is it important in motorcycles?
Powder metallurgy is a manufacturing process that compresses metal powders into precise shapes. It improves motorcycle performance by creating lightweight, durable, and cost-effective components.
Can powder metallurgy components handle extreme conditions?
Yes, powder metallurgy components withstand heavy loads, high temperatures, and wear. Their durability ensures reliable performance in demanding environments like engines and braking systems.
How does powder metallurgy contribute to sustainability?
Powder metallurgy minimizes material waste and energy consumption. Its near-net-shape production reduces scrap, making it an eco-friendly choice for motorcycle manufacturing. 🌱
💡 Tip: Consider powder metallurgy for your projects to enhance efficiency and sustainability!