Metal Injection Molding vs Machining: Which Saves More in 2025?
Production budgets rise or fall based on manufacturing costs. The choice between metal injection molding and machining plays a big role in this equation. These proven methods create metal parts differently, and their costs can vary based on what you’re making and how many parts you need.
Metal injection molding creates precise components without wasting much material. Machining stands out as a match for intricate geometries that need perfect accuracy. Manufacturers need to understand these differences to make budget-friendly decisions, whether they’re running high-volume production lines or crafting specialized parts.
A detailed look at both methods shows how they affect the bottom line in 2025. The analysis covers material costs, production speed, energy use, and ways to cut waste. This helps manufacturers pick the process that gives them the best value for their specific needs.
MIM part
Material and Design Flexibility
Material selection and design capabilities are vital differentiators between metal injection molding (MIM) and machining processes. These factors shape production decisions and final component quality.
Material Selection Range
Metal injection molding shows impressive versatility in material options. The process works with metals and alloys of all types, including stainless steels, low alloy steels, copper alloys, titanium alloys, nickel alloys, and tungsten alloys. MIM technology lets manufacturers customize material compositions based on customer needs, which creates tailored solutions for unique applications.
Machining works with solid metal blocks and keeps material integrity throughout the process. While both methods handle similar materials, MIM offers extra benefits through its powder metallurgy approach. The sintering process in MIM reaches density levels between 96% and 99%, and can hit 100% density with Hot Isostatic Press (HIP) treatment.
Design Complexity Possibilities
These manufacturing methods have very different design capabilities:
- Geometric Features
- MIM creates intricate shapes and sophisticated geometries easily
- Machining has limits due to tool accessibility needs
- Internal features challenge machining but work well with MIM
Each process has its own strengths in handling specific design elements. MIM really shines when producing thin-wall features and adding both exterior and interior threads. It also combines multiple components into single, complex pieces without affecting structural integrity.
Machining struggles with internal geometries because cutting tools need enough working space. Complex designs take longer to machine, which drives up production costs. MIM production times stay consistent no matter how complex the part is, making it a great choice for intricate components.
Surface finish quality varies between these methods too. MIM components can achieve surface roughness as low as 0.2 µm, which often eliminates the need for extra finishing work. This makes MIM perfect for parts that need precise surface specifications right out of production.
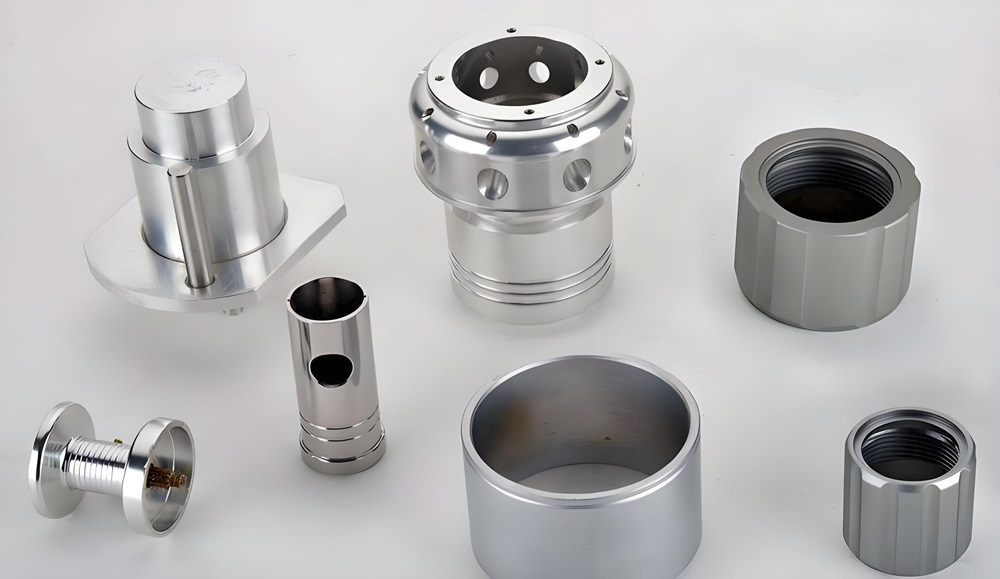
Time-to-Market Comparison
Time factors shape manufacturing decisions. Metal injection molding and machining each offer unique advantages when it comes to production timelines.
Production Setup Duration
The original setup requirements show marked differences between these processes. MIM needs significant upfront preparation. We focused on mold creation and material feedstock preparation. Complex part designs need intricate mold cavities that require careful planning. A 5-year old MIM setup aids consistent, high-volume production runs.
Manufacturing Speed Analysis
Production speeds show notable differences between these methods. Component complexity directly affects machining operation duration – intricate designs take longer to machine. High-volume output usually requires investment in additional CNC machines.
MIM shows remarkable consistency in cycle times. Production speeds stay similar whatever the part complexity. This happens because multiple components get molded simultaneously through cavity technology. MIM excels at automated production and enables large-quantity manufacturing while maintaining consistent quality standards.
Quality Control Time Requirements
Each method takes a distinct approach to quality assurance. Machining needs individual part inspection since each component undergoes separate processing. High tolerance specifications usually need substantial manual oversight that can extend production timelines.
Metal injection molding streamlines quality control through:
- Multiple cavity technology enabling consistent dimensional accuracy
- Automated production reducing variation between parts
- Surface finish specifications reaching 0.2 µm without secondary operations
MIM’s overall time efficiency becomes clear in high-volume scenarios. The original mold investments represent significant upfront costs. Rapid production cycles and minimal secondary operations balance these early investments. Machining retains advantages in lower-volume production. Tool accessibility and precise control support tighter tolerances despite longer per-part production times.
Environmental and Efficiency Factors
Efficiency metrics show clear differences between metal injection molding and machining processes in how they affect the environment and manage resources.
Energy Consumption Metrics
Metal injection molding is more energy efficient because it combines manufacturing steps. The process uses a single molding tool to create multiple components at once, which optimizes power usage for each part. Machining operations just need constant energy input while removing material, and complex parts need even more power.
Waste Generation Statistics
These manufacturing methods handle materials very differently. Machining creates a lot of waste by cutting away metal from raw workpieces. This cutting process leaves behind scrap material that needs recycling or extra processing.
Metal injection molding wastes less material by producing parts that are almost their final shape. The process achieves these material efficiency rates:
- 94-98% density in standard operations
- Up to 100% density with Hot Isostatic Press treatment
- Minimal material loss during production
Resource Utilization Rate
Both methods use resources differently. Metal injection molding makes better use of resources through:
Automated production systems cut down on labor compared to machining’s hands-on processes. The process also combines multiple components into single parts and removes the need for assembly steps. It eliminates secondary operations too, which saves more resources.
Machining faces several resource challenges:
- Multiple tool requirements for different features
- Extended processing times for complex geometries
- Additional equipment needs for high-volume production
The difference in resource efficiency becomes clear when producing large volumes. Metal injection molding keeps steady resource usage rates no matter the production size. Machining needs more equipment and workers as production increases. The automated nature of MIM processes also gives precise control over material flow and processing, which ensures the best use of resources during production.
Future Technology Impact
Technology advances continue to shape how manufacturing processes grow and adapt. Metal injection molding and machining must meet tomorrow’s production needs.
Automation Potential
Metal injection molding shows excellent automation capabilities through its integrated production approach. The process naturally blends with automated systems for several reasons:
- Multiple cavity technology creates consistent parts
- Single tool molding cuts equipment complexity
- Standardized cycle times lead to predictable schedules
Machining operations face different automation challenges. Each component needs separate processing steps, which makes automation more complex. Both methods still push toward better automated solutions.
Smart Manufacturing Integration
Smart manufacturing principles highlight key differences between these processes. Metal injection molding adapts well to smart manufacturing through:
- Process Control Optimization
- Automated material flow management
- Live quality monitoring systems
- Precise temperature and pressure control
- Production Efficiency Enhancement
- Fewer secondary operations needed
- Consistent cycle times at all complexity levels
- High-volume output without extra equipment
Machining processes show different smart manufacturing traits. Multiple operation steps make digital integration more complex. Advanced tool control systems and precise dimensional accuracy still benefit machining greatly.
Each technology brings unique strengths to future manufacturing. Metal injection molding excels at automated, high-volume production and keeps quality standards consistent with minimal human input. Machining operations focus on better tool control and precision through smart system integration.
Both processes improve as technology advances. Metal injection molding now includes automated quality control systems that achieve surface roughness values of 0.2 µm without human intervention. Machining operations have better tool management and process monitoring abilities.
Manufacturing technology keeps moving forward, and these methods adapt in different ways. Metal injection molding shows great promise for automated, high-volume work. Machining keeps its edge in specialized, precision-focused tasks. Manufacturers can plan better production strategies by understanding these technological paths.
Comparison Table
Aspect | Metal Injection Molding (MIM) | Machining |
---|---|---|
Material Selection | Broad range includes stainless steels, low alloy steels, copper alloys, titanium alloys, nickel alloys, tungsten alloys | Uses solid metal blocks |
Material Density | 96-99% (reaches 100% with HIP treatment) | Not mentioned |
Design Complexity | Creates intricate shapes and complex geometries | Tools limit access and design options |
Surface Finish | Achieves finish as low as 0.2 µm | Not mentioned |
Production Setup | Needs extensive preparation and mold creation | Requires minimal setup |
Production Speed | Maintains steady cycle times whatever the part complexity | Complexity affects production time |
Volume Capability | Best suits high-volume production | Works better for lower volumes |
Quality Control | Multiple cavity technology simplifies inspection | Each part needs inspection |
Waste Generation | Near-net-shape production creates minimal waste | Removes material extensively causing waste |
Energy Efficiency | United manufacturing process improves efficiency | Needs constant energy input that grows with complexity |
Automation Potential | Offers superior automation with united production | Faces automation limitations |
Smart Manufacturing | Adapts easily to smart manufacturing systems | Needs complex digital system integration |
Conclusion
MIM and machining each offer unique benefits that influence manufacturing choices in 2025. A detailed comparison reveals several differences that impact economical solutions and production efficiency.
MIM excels at handling complex geometries and works best to produce high-volume parts with intricate features. Machining delivers excellent precision but shows limitations as tools requirements increase and production times extend for complex components.
Production cycles stay consistent with MIM despite higher setup costs upfront. Machining works better for lower-volume specialized parts, though production speeds change substantially based on complexity. The process also shows better environmental performance by generating minimal waste and using resources efficiently. Machining struggles with material waste and consumes more energy.
Smart manufacturing and automation capabilities make MIM a strong choice for high-volume production. Machining still proves valuable for specialized tasks that need precise dimensional control. The right choice between MIM and machining depends on project needs, production volumes, and long-term costs. Companies should assess these elements carefully before selecting their manufacturing process.