MIM 440C(austenitic grade)
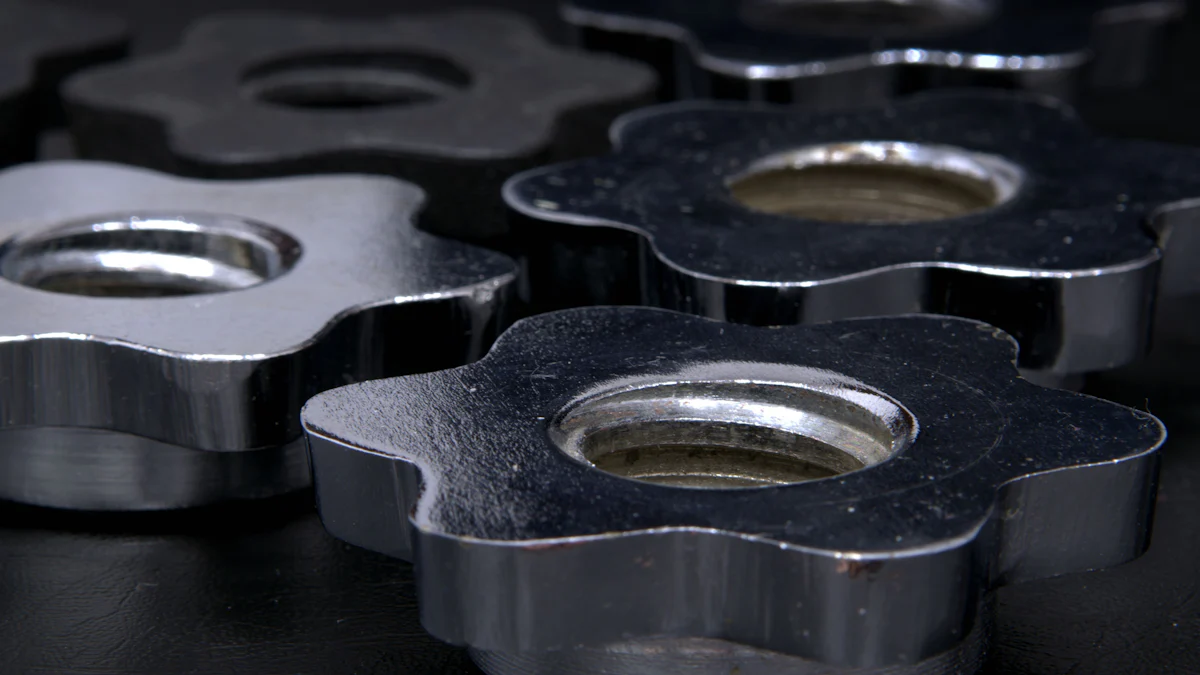
I find 440C Stainless Steel to be an exceptional choice for crafting swords. Its high hardness, reaching up to 60 HRC, ensures a sharp edge that lasts. This steel’s moderate corrosion resistance makes it suitable for various environments, while its wear resistance guarantees durability. These properties make 440C Stainless Steel a popular option for not only swords but also kitchen knives and cutting tools. Its ability to maintain sharpness and resist rust at an affordable price highlights its versatility and reliability in demanding applications.
Composition of 440C Stainless Steel
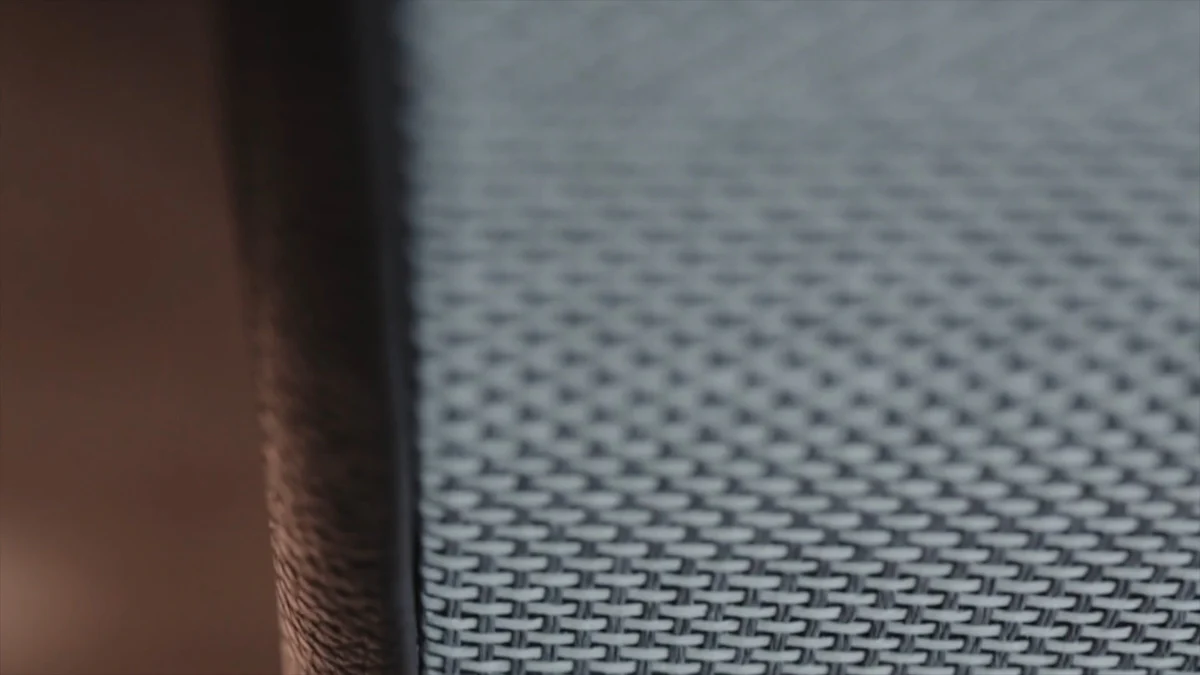
Chemical Composition
Understanding the chemical composition of 440C Stainless Steel is crucial for appreciating its unique properties. This steel stands out due to its high carbon and chromium content, which contribute significantly to its performance.
Carbon Content
The carbon content in 440C Stainless Steel is approximately 1.2%. This high carbon level is a key factor in achieving the steel’s exceptional hardness and wear resistance. The presence of carbon allows the steel to be heat-treated to attain a Rockwell hardness of up to 60 HRC, making it one of the hardest stainless steels available. This hardness is particularly beneficial for applications requiring sharp edges and durability, such as in cutlery and industrial tools.
Chromium and Other Elements
Chromium is another vital component, comprising about 16-18% of the steel’s composition. This element provides the steel with its stainless properties, enhancing its corrosion resistance. Chromium forms a passive layer on the steel surface, protecting it from rust and oxidation. Additionally, 440C Stainless Steel contains small amounts of molybdenum, which further improves its wear resistance and edge retention. These elements together make 440C a versatile choice for environments where both hardness and corrosion resistance are required.
Comparison with 1095 Carbon Steel
When comparing 440C Stainless Steel to 1095 Carbon Steel, several differences in composition and implications for use become apparent.
Differences in Composition
1095 Carbon Steel is a high-carbon steel with approximately 0.95% carbon content, but it lacks the chromium found in 440C. This absence of chromium means that 1095 does not possess the same level of corrosion resistance as 440C. While 1095 can achieve high hardness levels, it is more prone to rust and requires more maintenance to prevent corrosion.
Implications for Use
The differences in composition between these two steels lead to distinct applications. 440C Stainless Steel, with its superior corrosion resistance and hardness, is ideal for environments where moisture and wear are concerns, such as in kitchen knives and surgical instruments. On the other hand, 1095 Carbon Steel, known for its toughness and ease of sharpening, is often preferred for applications like outdoor knives and swords, where impact resistance is more critical than corrosion resistance.
Hardness and Toughness
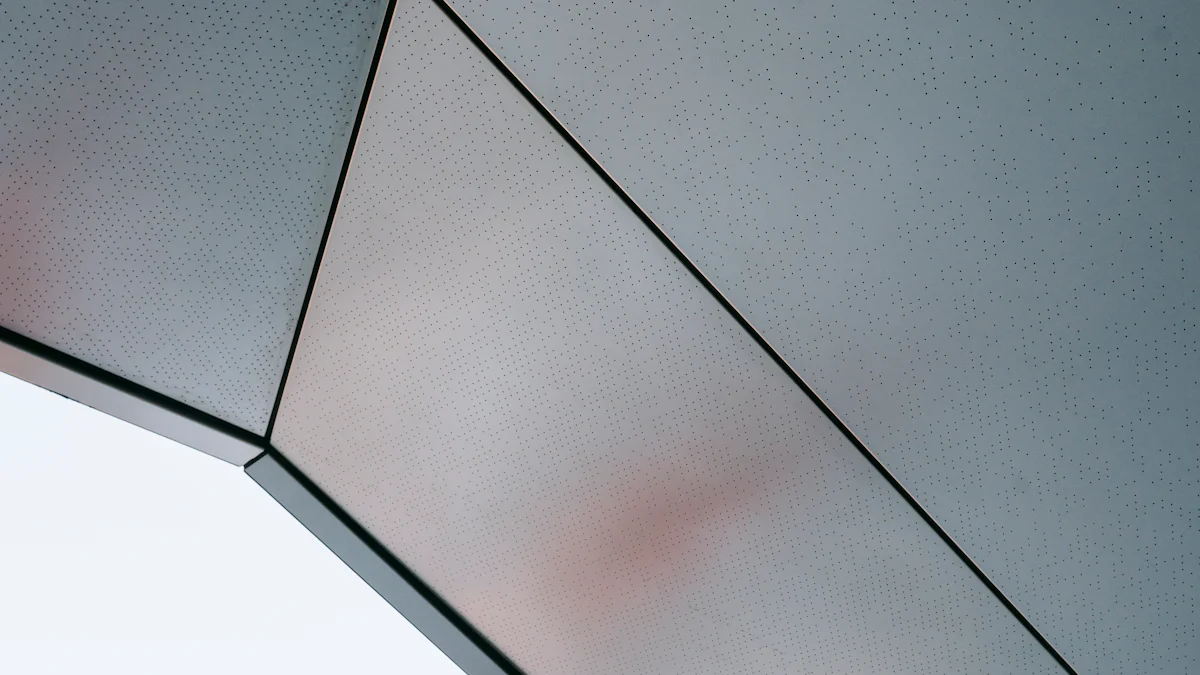
Hardness Levels
Rockwell Hardness Scale
When I evaluate the hardness of 440C Stainless Steel, I often refer to the Rockwell Hardness Scale. This scale measures the resistance of a material to indentation, providing a clear indication of its hardness. 440C Stainless Steel can achieve a remarkable hardness level of up to 60 HRC. This high hardness results from its unique composition, particularly its high carbon and chromium content. Such hardness makes it an excellent choice for applications requiring sharp edges and durability, like precision bearings and cutting tools.
Impact on Durability
The hardness of 440C Stainless Steel significantly impacts its durability. In my experience, materials with higher hardness levels tend to offer better wear resistance. This means that tools and components made from 440C can withstand prolonged use without significant wear. However, it’s essential to balance hardness with other properties, as excessive hardness can sometimes lead to brittleness. Despite this, 440C remains a popular choice for applications where maintaining a sharp edge is crucial.
Toughness Considerations
Resistance to Impact
While 440C Stainless Steel boasts impressive hardness, I find its toughness to be a critical factor in its performance. Toughness refers to a material’s ability to absorb energy and resist fracture. Although 440C is not as tough as some other steels, it still offers reasonable resistance to impact. This makes it suitable for applications where both hardness and moderate toughness are required. However, for high-impact applications, one might consider alternatives that offer greater toughness.
Comparison with 1095 Carbon Steel
Comparing 440C Stainless Steel with 1095 Carbon Steel reveals distinct differences in toughness. 1095 Carbon Steel is renowned for its toughness and ease of sharpening. It excels in applications where impact resistance is more critical than corrosion resistance. On the other hand, 440C provides superior hardness and corrosion resistance, making it ideal for environments where these properties are prioritized. Each steel has its strengths, and the choice between them depends on the specific requirements of the application.
Brittleness and Corrosion Resistance
Brittleness Factors
Effects of High Carbon Content
In my experience, the high carbon content in 440C Stainless Steel significantly contributes to its brittleness. This steel contains approximately 1.2% carbon, which enhances its hardness and wear resistance. However, this high carbon level can also make the steel more susceptible to cracking under stress. The increased brittleness means that while 440C can maintain a sharp edge, it may not withstand heavy impacts as well as some other steels.
Suitability for High-Impact Applications
When considering 440C Stainless Steel for high-impact applications, I often weigh its brittleness against its other properties. While its hardness and wear resistance are impressive, the brittleness can limit its use in situations where the material might experience sudden or severe impacts. For applications requiring both high hardness and impact resistance, I might explore alternative materials that offer a better balance between these properties.
Corrosion Resistance
Role of Chromium
Chromium plays a crucial role in the corrosion resistance of 440C Stainless Steel. With a chromium content of about 16-18%, this steel forms a protective layer on its surface, which helps prevent rust and oxidation. This passive layer is essential for maintaining the steel’s integrity in various environments. In my work, I have found that this corrosion resistance makes 440C an excellent choice for tools and components exposed to moisture or corrosive substances.
Comparison with Other Stainless Steels
When comparing 440C Stainless Steel to other stainless steels, such as grade 304, I notice that 440C offers superior hardness and wear resistance. However, its corrosion resistance is moderate compared to some other stainless steels. Despite this, 440C remains highly corrosion-resistant, making it suitable for many demanding applications. Its ability to resist corrosion by air, fresh water, and weak acids ensures consistent performance even in challenging environments.
Edge Retention and Sharpness
Edge Retention Capabilities
Longevity of Sharpness
In my experience, 440C Stainless Steel excels in edge retention due to its high hardness. This steel maintains a sharp edge for extended periods, making it ideal for applications where consistent performance is crucial. The high carbon content contributes significantly to this longevity, allowing tools and blades to remain effective without frequent sharpening. I have found that this property makes 440C a preferred choice for professionals who require reliable cutting tools.
Maintenance Requirements
While 440C Stainless Steel offers impressive edge retention, it still requires proper maintenance to maximize its lifespan. Regular cleaning and occasional honing help preserve the sharpness and prevent any potential corrosion. I recommend using a fine-grit sharpening stone to maintain the edge, as this method complements the steel’s properties. By adhering to a routine maintenance schedule, users can ensure that their 440C tools continue to perform at their best.
Sharpness Potential
Ease of Sharpening
Despite its high hardness, I find 440C Stainless Steel relatively easy to sharpen. The steel’s composition allows for efficient sharpening without excessive wear on the sharpening tools. This ease of sharpening ensures that even after prolonged use, the blade can be restored to its original sharpness with minimal effort. For those who value both performance and convenience, 440C offers a balanced solution.
Comparison with 1095 Carbon Steel
When comparing 440C Stainless Steel to 1095 Carbon Steel, distinct differences in sharpening emerge. 1095 Carbon Steel, known for its toughness, sharpens more easily than 440C. However, 440C provides superior edge retention, reducing the frequency of sharpening required. In my opinion, the choice between these steels depends on the specific needs of the user. For those prioritizing long-lasting sharpness, 440C stands out as a robust option.
In my experience, 440C Stainless Steel stands out for its high hardness, excellent edge retention, and moderate corrosion resistance. These properties make it a top choice for crafting swords and other cutting tools. I recommend 440C for applications where maintaining a sharp edge is crucial. Its balance of hardness and wear resistance ensures durability, though its brittleness requires careful consideration in high-impact scenarios. Overall, 440C Stainless Steel offers a reliable option for those seeking performance and longevity in demanding environments.
FAQ
What are the applications of 440C stainless steel?
440C stainless steel finds its use in a wide range of applications due to its exceptional properties. I often see it used in manufacturing precision tools like medical scalpels, scissors, and surgical instruments. It also serves well in producing high-quality cutting tools, ball bearings, valve components, and even razor blades. Its high hardness and wear resistance make it ideal for these demanding applications.
What are the properties of 440C steel?
In my experience, 440C steel stands out for its remarkable hardness and corrosion resistance. It achieves a hardness level of up to 60 HRC after heat treatment, which is among the highest for stainless steels. This steel also offers excellent wear resistance and strength, making it suitable for various industrial applications. Its ability to resist corrosion by air, fresh water, and weak acids further enhances its appeal.
How does 440C stainless steel resist corrosion?
The high chromium content in 440C stainless steel significantly boosts its corrosion resistance. This element forms a protective layer on the steel’s surface, preventing rust and oxidation. I find that this property reduces the maintenance required for tools made from 440C, making it a practical choice for environments where moisture exposure is a concern.
What is the hardness level of 440C stainless steel?
440C stainless steel can be hardened to an impressive 60 HRC. This high hardness level contributes to its excellent edge retention and wear resistance. In my work, I have found that this makes 440C a preferred material for applications requiring sharp, durable edges, such as in knives and cutting tools.
What are the specific qualities of 440C stainless steel?
440C stainless steel is renowned for its high corrosion resistance, reliability, and exceptional hardness. It contains approximately 1% carbon, 17% chromium, and 1% molybdenum, which contribute to its excellent edge retention and wear resistance. These qualities make it a favored choice for fine, handcrafted knife blades and other precision instruments.
How does 440C stainless steel compare to other stainless steels in terms of corrosion resistance?
Compared to other grades like 440A and 440B, 440C stainless steel offers superior corrosion resistance. This makes it more suitable for applications where both hardness and corrosion resistance are critical. I often recommend 440C for environments that demand high performance and durability.
What are the traits of Stainless Steel Grade 440C?
Stainless Steel Grade 440C demonstrates high strength, moderate corrosion resistance, and good hardness. Its wear resistance makes it ideal for cutting instrumentation, surgical blades, knife blades, ball bearings, valves, and measuring instruments. I find these traits make 440C a versatile and reliable material for various demanding applications.
What makes 440C stainless steel suitable for high-impact applications?
While 440C stainless steel offers impressive hardness and wear resistance, its brittleness can limit its use in high-impact applications. However, its moderate toughness still allows it to perform well in situations where both hardness and some level of impact resistance are required. For applications demanding higher impact resistance, I might consider alternative materials with better toughness.
How does 440C stainless steel maintain its sharpness?
The high carbon content in 440C stainless steel contributes to its excellent edge retention. This steel maintains a sharp edge for extended periods, reducing the need for frequent sharpening. I find this property particularly beneficial for professionals who rely on consistent cutting performance in their tools.
Is 440C stainless steel easy to sharpen?
Despite its high hardness, I find 440C stainless steel relatively easy to sharpen. Its composition allows for efficient sharpening without excessive wear on the sharpening tools. This ease of sharpening ensures that blades made from 440C can be restored to their original sharpness with minimal effort, making it a convenient choice for users who value both performance and ease of maintenance.
Chemical Content
- 440C
- 304
- 316L
- 420
- 17-4PH
440C | C | Si | S | P | Mn | Cr | Ni |
w.t/% | 0.95-1.20 | ≤1.00 | ≤0.03 | ≤0.035 | ≤1.0 | 16.0-18.0 | ≤0.60 |
304 | C | Si | S | P | Mn | Cr | Ni | Fe |
w.t/% | ≤0.03 | ≤1.00 | ≤0.03 | ≤0.03 | ≤2.0 | 18.0-20.0 | 8.0-11.0 | Bal |
316L | C | Si | S | P | Mn | Cr | Ni | Mo | N |
w.t/% | 0.03 | 0.75 | 0.03 | 0.045 | 2 | 16-18 | 10-14 | 2-3 | 0.1 |
420 | C | Si | S | P | Mn | Cr | Ni |
w.t/% | 0.16-0.25 | ≤1.00 | ≤0.03 | ≤0.04 | ≤1.0 | 12.0-14.0 | ≤0.75 |
17-4PH | C | Si | S | P | Mn | Cr | Ni | Nb+Ta |
w.t/% | ≤0.07 | ≤1.00 | ≤0.03 | ≤0.04 | ≤1.0 | 15.5-17.5 | 3.0-5.0 | 0.15-0.45 |