About Metal Powder Injection Molding: Process, Uses, Materials, Advantages and Disadvantages.
Metal Injection Molding (MIM) is a metal processing technique that combines powder metallurgy and plastic injection molding technologies. This process utilizes a mixture of metal powder and organic binder to create “feedstock,” which is then used to manufacture complex metal parts through injection molding. Unlike plastic injection molding, MIM requires subsequent debinding and sintering treatments. It is typically used to produce small metal parts ranging from 1-100 grams with high precision, high density, and complex shapes. MIM is widely applied in industries such as electronics, medical, automotive, and aerospace.
This article will use a Q&A format to explain many aspects of MIM for you.
What is Metal Injection Molding?
Metal Injection Molding (MIM), also known as Powder Injection Molding, is a process that uses metal powder feedstock to manufacture complex metal parts during the injection molding process. This technique binds metal powder together using organic binders to form powder metal granules. These granules are then injection molded into the desired part shapes and undergo debinding and sintering treatments to complete the final product.
What is the Purpose of Metal Injection Molding (MIM)?
The main purpose of Metal Injection Molding (MIM) is to efficiently mass-produce small metal parts with complex geometries and high precision. Specifically, it includes:
- Producing Complex-Shaped Parts: MIM technology can create complex, thin-walled, and intricately designed metal parts that are difficult to form using traditional methods.
- Improving Mechanical Properties and Strength: MIM parts generally exhibit superior mechanical properties and strength compared to those produced by CNC machining and casting.
- Efficient Mass Production: MIM is suitable for large-scale production with high material utilization and automation levels, offering low-cost production solutions. For example, electronic products such as mobile phones, computers, and smartwatches typically have production volumes of 500,000 to 2,000,000 pieces. With MIM technology, daily production can reach 50,000 to 100,000 pieces, a level of efficiency that is difficult to achieve with other manufacturing processes.
- Reducing Waste and Improving Material Utilization: The MIM process generates less waste, and most of the waste can be recycled or reused.
MIM technology provides an efficient, precise, and cost-effective solution in manufacturing, and it is widely used in electronics, medical, automotive, aerospace, and defense industries.
How Does Metal Injection Molding (MIM) Work?
The working principle of Metal Injection Molding (MIM) involves converting metal powder feedstock into granules. Under high pressure and temperature, the feedstock is transformed into a molten state using organic binders. The molten metal is then injected into a mold, cooled, and solidified to form preliminary parts. These parts undergo a debinding process to remove the organic binders and are then sintered to achieve the final shape. The main steps are as follows:
- Mixing: Fine metal powder is mixed with a binder (such as wax or plastic) to create a homogeneous mixture known as “feedstock.”
- Injection Molding: The feedstock is heated to a molten state and injected into a mold using an injection molding machine. Once cooled, it forms a “green” part.
- Debinding: The binder is removed from the green part using chemical or thermal methods, leaving behind a porous “brown” part.
- Sintering: The brown part is heated to a temperature near the metal’s melting point, allowing the metal particles to diffuse and densify, ultimately forming a solid metal part.
Powder Injection Molding process
What Materials Can Be Used in MIM?
The Metal Injection Molding (MIM) process can utilize a variety of materials, primarily including the following categories:
Material | Density (g/cm³) | Yield Strength (MPa) | Tensile Strength (MPa) | Elongation (%) | Hardness |
Low-alloy steel | |||||
MIM 4605 HT | 7.55 | 1480 | 1650 | 1 | 43-48 HRC |
MIM 4140 HT | 7.5 | 1200 | 1600 | 5 | 43-48 HRC |
MIM 4340 HT | 7.5 | 1100 | 1200 | 6 | 40-45 HRC |
MIM 2700 | 7.6 | 250 | 400 | 12 | 69 HRB |
MIM 2200 | 7.6 | 125 | 280 | 35 | 45 HRB |
MIM 52100 HT | 7.5 | 1100 | 1500 | 2 | 55-62 HRC |
MIM 8620 | 7.5 | 130 | 320 | 25 | 100 HRB |
MIM 9310 | 7.5 | 350 | 540 | 15 | 375 HV1 |
Stainless steel | |||||
MIM 17-4 PH | 7.6 | 740 | 900 | 6 | 27-32 HRC |
MIM 17-4 PH (H900) | 7.6 | 1100 | 1200 | 4 | 38-42 HRC |
MIM 316L | 7.6 | 180 | 520 | 40 | 67 HRB |
MIM 420 (Heat Treatment) | 7.4 | 1200 | 1370 | – | 44 HRB |
MIM 440 (Heat Treatment) | 7.5 | 1600 | 1250 | 1 | 55 HRC |
MIM 430L | 7.5 | 230 | 410 | 25 | 65 HRB |
Tool Steel | |||||
MIM S7 HT | 7.4 | 1550 | 1750 | 2 | 45-53 HRC |
MIM A2 HT | 7.5 | – | – | – | 55-63 HRC |
MIM M2 HT | 7.9 | – | – | – | 55-65 HRC |
MIM M4 HT | 7.9 | – | – | – | 60-65 HRC |
MIM T15 HT | 8.2 | – | – | – | 60-65 HRC |
Bio-implantable alloys | |||||
MIM F-75 – Hipped | 7.8 | 520 | 1000 | 40 | 25 HRC |
MIM MP35N | 8.3 | 400 | 900 | 10 | 8 HRC |
Titanium Alloy | |||||
MIM Ti-6Al-4V | 4.43 | 800 | 880 | 12 | 350 HV |
Please note that these data may vary depending on the specific composition of the material, heat treatment, and manufacturing processes. When selecting materials for MIM, other factors such as corrosion resistance, magnetism, biocompatibility, etc., also need to be considered.
Can tin metal be used in metal injection molding (MIM)?
Yes, tin metal can be used in MIM, but it is typically used as part of an alloy rather than as pure metal.
Here is some related information:
Tin Alloys: Tin is often alloyed with other metals to improve its properties. For example, bismuth bronze is an alloy primarily composed of copper, tin, and bismuth, which exhibits good machinability and corrosion resistance. This alloy can be manufactured into complex parts using the injection molding process.
Applications of Bismuth Bronze: Bismuth bronze is highly suitable for injection molding complex-shaped parts due to its low melting point and good flowability. Its non-toxic nature and good machinability make it widely used in applications such as pipe fittings, bearings, jewelry, etc.
Other Alloys: Besides bismuth bronze, tin can also be alloyed with other metals like copper, zinc, etc., to form different bronze or brass alloys, which can also be processed using the MIM process.
In summary, although pure tin is not commonly used in the MIM process, tin as an alloy component is widely used in MIM, especially in alloys such as bismuth bronze.
Can tungsten metal be used in metal injection molding?
Yes, Tungsten metal can be used in metal injection molding (MIM).
Tungsten and its alloys have wide applications in the MIM process, primarily due to their high density, high strength, and excellent high-temperature resistance. Here is some related information:
High Density and High Strength: Tungsten alloys have extremely high density and strength, making them suitable for applications requiring high strength and wear resistance, such as radiation shielding and high-temperature furnace components in the aerospace and defense industries.
High-Temperature Resistance: Tungsten’s high melting point and excellent high-temperature performance make it perform well in high-temperature environments, suitable for manufacturing high-temperature furnace components and other high-performance parts.
Application Fields: Tungsten metal injection molded parts are widely used in industries such as aerospace, defense, and medical. For example, tungsten alloys are used to manufacture radiation shielding, high-temperature furnace components, and other high-performance parts.
In summary, tungsten metal and its alloys have important applications in the metal injection molding process, especially in fields requiring high density, high strength, and high-temperature resistance.
What is the density of metal injection molded parts?
The density of metal injection molded (MIM) parts is usually close to the theoretical density of their raw materials. Specifically, the density of MIM parts can reach 95% to 99% of the theoretical density of the raw materials. Here is some relevant information:
High density: The MIM process is able to produce high-density metal parts, with a density usually between 95% and 99% of the theoretical density of the raw materials. This means that the density of MIM parts is very close to parts produced by traditional manufacturing methods such as forging or casting.
Material influence: The density of different metal materials varies. For example, materials such as stainless steel, iron-based alloys, titanium alloys, and tungsten alloys vary in density in the MIM process, but can all reach a high percentage of their theoretical density.
Sintering process: Sintering is a key step in the MIM process. High-temperature treatment allows metal powder particles to diffuse and bond with each other, thereby improving the density and mechanical properties of the part.
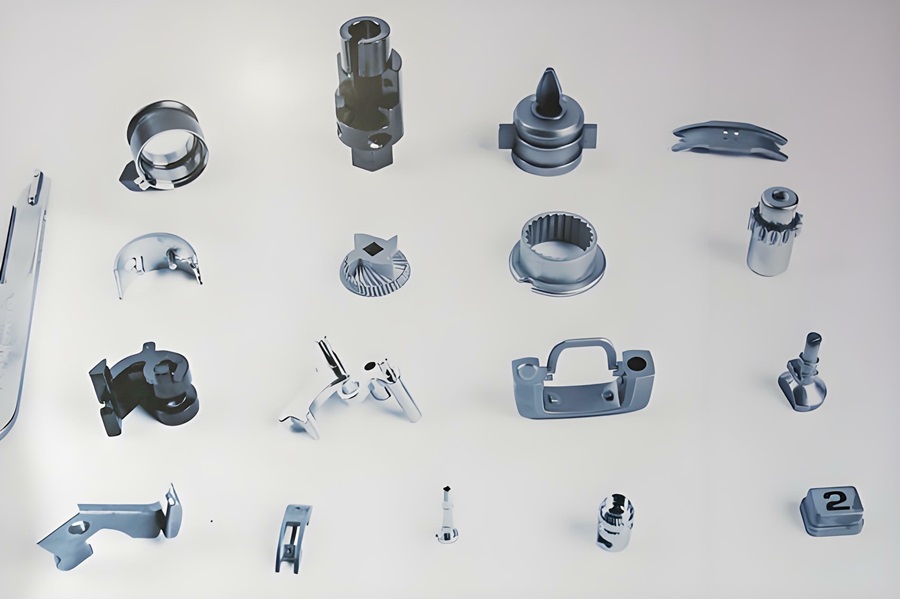
How long does it take to mass produce metal injection molded products?
The entire production cycle of metal injection molding (MIM) usually takes a few weeks to a few months, depending on the complexity of the part and the production batch. The main production steps and the time required are outlined as follows:
Mold making: It usually takes 4-5 weeks to make a metal mold.
Injection molding: The raw material is injected into the mold and cooled to form a “green” part. This step takes a shorter time, mainly depending on the production batch.
Debinding: The binder in the green body is removed by chemical or thermal treatment. The time is usually about one day.
Sintering: The debinded “brown body” is heated to a high temperature close to the melting point of the metal and sintered. The sintering time is longer, generally taking 10-12 hours.
Surface treatment (optional):
Surface treatment such as polishing, electroplating, blackening, etc. is carried out according to needs, and the time varies depending on the process.
Therefore, for large-scale MIM production using metal molds, it usually takes about 6-8 weeks from mold making to the final product.
What is the quality of metal injection molding products?
Metal injection molding can produce high-quality products. This process can manufacture fine parts with complex geometries and precise tolerances. The metal powder particles are extremely small, typically ranging from 0.5-20 μm. This reduces the number of inclusions and lowers the final porosity during high-pressure and high-temperature processes, resulting in high-quality parts.
What are the advantages of Metal Injection Molding?
Metal Injection Molding (MIM) technology has several significant advantages, making it widely used in multiple industries. Here are the main advantages of MIM:
- Capability for Complex Structure Formation MIM technology can mold highly complex structural parts, which is difficult to achieve with traditional metal processing methods. Through injection molding, the material can completely fill the mold cavity, ensuring the complex shape and fine structure of the parts.
- High Density and Excellent Performance The density of MIM parts can usually reach over 96% of the theoretical density of the raw material, significantly higher than the 85% of traditional pressed products. This high density gives MIM parts excellent mechanical properties and microstructure uniformity.
- High Production Efficiency MIM technology is suitable for mass production, enabling automated and large-scale production. The lifespan of metal molds is comparable to that of engineering plastic injection molds, suitable for batch production of parts.
- High Material Utilization Rate MIM process can significantly save raw materials, theoretically achieving a utilization rate of 100%. Compared with traditional metal processing methods, MIM reduces material waste and improves economy.
- Wide Material Applicability MIM technology is suitable for a variety of metal materials, including iron-based, low-alloy steel, stainless steel, titanium alloy, hard alloy, etc. This makes MIM widely used in electronics, automotive, medical and other fields.
- High Precision and Excellent Surface Quality The dimensional tolerance of MIM parts can reach ±0.5%, and certain features can even reach ±0.3%. In addition, MIM parts have high surface finish, suitable for further surface treatment.
- Environmental Protection and Economy MIM technology uses metal materials accurately during the production process, avoiding material waste, and achieving a utilization rate of close to 100% of raw materials. This not only saves resources but also reduces production costs.
- Suitable for Small Parts MIM technology is particularly suitable for the production of small parts weighing between 0.1 and 250 grams, which are often difficult to manufacture through traditional methods.
- High Strength and Corrosion Resistance MIM parts have high strength and corrosion resistance, suitable for applications requiring high performance and durability.
Therefore, Metal Injection Molding technology, with its ability to form complex structures, high density and excellent performance, high production efficiency, high material utilization rate, wide material applicability, high precision and excellent surface quality, environmental protection, and economy, has become an important process technology in modern manufacturing.
What are the advantages of Metal Injection Molding?
Metal Injection Molding (MIM) technology has several significant advantages, making it widely used in multiple industries. Here are the main advantages of MIM:
- Capability for Complex Structure Formation MIM technology can mold highly complex structural parts, which is difficult to achieve with traditional metal processing methods. Through injection molding, the material can completely fill the mold cavity, ensuring the complex shape and fine structure of the parts.
- High Density and Excellent Performance The density of MIM parts can usually reach over 96% of the theoretical density of the raw material, significantly higher than the 85% of traditional pressed products. This high density gives MIM parts excellent mechanical properties and microstructure uniformity.
- High Production Efficiency MIM technology is suitable for mass production, enabling automated and large-scale production. The lifespan of metal molds is comparable to that of engineering plastic injection molds, suitable for batch production of parts.
- High Material Utilization Rate MIM process can significantly save raw materials, theoretically achieving a utilization rate of 100%. Compared with traditional metal processing methods, MIM reduces material waste and improves economy.
- Wide Material Applicability MIM technology is suitable for a variety of metal materials, including iron-based, low-alloy steel, stainless steel, titanium alloy, hard alloy, etc. This makes MIM widely used in electronics, automotive, medical and other fields.
- High Precision and Excellent Surface Quality The dimensional tolerance of MIM parts can reach ±0.5%, and certain features can even reach ±0.3%. In addition, MIM parts have high surface finish, suitable for further surface treatment.
- Environmental Protection and Economy MIM technology uses metal materials accurately during the production process, avoiding material waste, and achieving a utilization rate of close to 100% of raw materials. This not only saves resources but also reduces production costs.
- Suitable for Small Parts MIM technology is particularly suitable for the production of small parts weighing between 0.1 and 250 grams, which are often difficult to manufacture through traditional methods.
- High Strength and Corrosion Resistance MIM parts have high strength and corrosion resistance, suitable for applications requiring high performance and durability.
Therefore, Metal Injection Molding technology, with its ability to form complex structures, high density and excellent performance, high production efficiency, high material utilization rate, wide material applicability, high precision and excellent surface quality, environmental protection, and economy, has become an important process technology in modern manufacturing.
What are the disadvantages of metal injection molding?
While Metal Injection Molding (MIM) has many advantages, it also has some disadvantages and challenges. Here are some of the main drawbacks of the MIM process:
- Complex Process: MIM involves multiple steps, including powder selection, mixing, injection molding, debinding, and sintering, each requiring strict control. Any issues in any of these steps can affect the quality of the final product.
- High Mold Cost: MIM requires the use of precision molds, and the design and manufacturing costs of these molds can be high, especially for complex-shaped parts. This makes MIM more suitable for large-scale production to amortize the mold cost.
- Material Selection Limitations: While MIM can use a variety of metal materials, not all metals are suitable for the MIM process. Some high-melting-point or difficult-to-sinter materials may not be suitable for MIM.
- Difficulty in Defect Control: Common defects in the MIM process include underfilling, weld lines, gas pores, and deformation. These defects typically manifest after debinding and sintering and require strict control of process parameters during production to avoid.
- Long Debinding and Sintering Times: Debinding and sintering are time-consuming steps in the MIM process. Debinding requires a gradual temperature increase to avoid cracking, while sintering needs to be done at high temperatures for a long time to ensure part density and mechanical properties.
- Size and Shape Limitations: While MIM is suitable for producing small complex parts, it may not be suitable for very large parts or parts with extremely complex shapes. Additionally, the dimensional accuracy and shape complexity of MIM parts are also limited by mold design and manufacturing technology.
- Post-processing Requirements: MIM parts may require further post-processing such as heat treatment, machining, or surface treatment to meet final performance requirements. This adds to the complexity and cost of production.
- Environmental and Health Risks: Some binders and solvents used in the MIM process may pose potential risks to the environment and the health of operators, requiring appropriate safety measures and environmental protection measures.
Therefore, the complex process of metal injection molding, high mold costs, material selection limitations, difficulty in defect control, long debinding and sintering times, size and shape limitations, post-processing requirements, and environmental and health risks need to be considered and overcome in practical applications.
What are the applications of metal injection molding?
Metal Injection Molding (MIM) technology has a wide range of applications across multiple industries and fields. Here are some main application areas and specific examples:
- Electronics Consumer Electronics: such as phone casings, miniature motor parts, sensors, phone switches, miniature USB interfaces, etc. Computers and peripherals: such as printer accessories, magnetic cores, drive components, etc.
- Automotive Manufacturing Power transmission parts: such as turbocharger components, fuel injector parts, sensor components, etc. Safety systems: such as airbag sensor embeds, car locks, clutch inner rings, etc.
- Medical Equipment Orthodontic brackets: used for dental braces, mainly using 316L stainless steel. Surgical instruments: such as scissors, forceps, disposable surgical tools, etc., with high strength and corrosion resistance. Implants: such as knee implant parts, interventional therapy stents, etc., mainly using titanium alloy. Hearing aid sound tubes: complex shapes with high surface finish.
- Industrial and Tools Tools: such as gun drills, drill bits, power tools, hand tools, wrenches, milling heads, nozzles, etc. Mechanical parts: such as industrial metal parts, spinning machines, sewing machines, office machinery, etc., for small complex parts.
- Household Appliances Small parts: such as watch cases, bracelets, electric toothbrushes, scissors, fans, golf club heads, imitation jewelry, etc.
- Military Weapons Weapon components: such as missile tails, firearms, bullets, detonator parts, etc.
- Other Applications Electronic packaging: such as electronic packaging housings of tungsten-copper alloys, oxygen-free copper, stainless steel, etc. MIM technology is widely used in these fields due to its ability to produce high-density, high-precision, complex-shaped metal parts, meeting the modern industry’s demand for small, complex, high-performance parts.
Can I use Metal Injection Molding for prototyping?
Metal Injection Molding (MIM), while offering significant advantages in mass-producing complex metal parts, is not typically suitable for prototype design. Here are the main reasons:
- High Mold Cost: MIM requires the use of precision molds, which are costly to design and manufacture. For prototype design, only a small number of parts are usually needed, making it difficult to amortize the high mold cost and resulting in overall high costs.
- Complex Process: MIM involves multiple steps, including powder selection, blending, injection molding, debinding, and sintering, each requiring strict control. Any issues in any of these steps can affect the quality of the final product. This complexity makes MIM unsuitable for rapid iteration and design adjustments.
- Long Production Cycle: The production cycle of MIM is long, especially in mold making and sintering steps. Mold making typically takes several weeks, and the sintering process also takes a long time. For prototype design that requires quick feedback and iteration, the time cost is too high.
- Unsuitable for Small Batch Production: MIM is more suitable for mass production to amortize mold and process costs. For prototype design, only a small number of parts are usually needed, and the economics and efficiency of MIM are not evident.
- Alternative Methods Are More Advantageous: For prototype design, methods like 3D printing and CNC machining are more suitable. These methods have lower initial costs, shorter production cycles, and higher design flexibility, allowing for rapid production and adjustment of prototype parts.
In summary, due to high mold costs, complex process, long production cycles, and unsuitability for small batch production, MIM is not suitable for prototype design. Instead, methods like 3D printing and CNC machining are more suitable for the prototype design stage.
What MIM metal products can JH MIM provide?
JH MIM offers a wide range of metal products using Metal Injection Molding (MIM) technology. Here are some of the MIM metal products they provide:
- Stainless Steel: Such as 316L, 17-4PH, etc., known for their excellent corrosion resistance and mechanical properties.
- Iron-based Alloys: Commonly used in applications requiring high strength and wear resistance.
- Tungsten Alloys: Featuring high density and high melting points, suitable for high-temperature and high-strength applications.
- Hard Alloys: Such as tungsten carbide, ideal for cutting tools and wear-resistant parts.
- Fine Ceramics: Used in special application areas, offering high hardness and high-temperature resistance.
- Titanium and Its Alloys: Known for high strength, low density, and good biocompatibility, often used in medical and aerospace fields.
These materials make JH MIM’s products suitable for various industries, including aerospace, medical, automotive, industrial, consumer electronics, and jewelry and fashion sectors.
How can JH MIM meet your metal injection molding needs?
At JH MIM, we understand that meeting your metal injection molding (MIM) needs requires more than just state-of-the-art equipment and advanced technology. It requires a partnership built on trust, communication, and a commitment to quality. This is why we strive to provide not only excellent products but also a seamless and responsive customer experience.
Why Choose JH MIM for Your MIM Needs?
Rich Experience: With nearly 20 years of experience in the MIM industry, we have honed our processes and technologies to provide high-precision, complex parts for various industries, including automotive, consumer electronics, medical, and defense.
Advanced Facilities: Our facility spans over 18,000 square meters and is equipped with cutting-edge MIM equipment, including material mixing workshops, injection molding facilities, sintering workshops, and surface treatment workshops. This comprehensive setup allows us to control every aspect of production, ensuring the highest quality standards.
Diverse Material Selection: We offer a variety of materials for the MIM process, including MIM-4605, MIM-304, MIM-316L, MIM-17-4PH, and MIM-420. These materials are suitable for various applications, from industrial structural parts to medical and electronic device components.
Quality Assurance: Our commitment to quality is reflected in our ISO 9001 and IATF 16949 certifications. We maintain stringent quality control standards and use advanced testing technologies to ensure that each component meets your specifications.
Global Reach: With over 10 years of export experience, we have established strong partnerships with customers in North America, South America, Europe, and the Middle East. Our global reach ensures that we can meet your needs no matter where you are.
Low MOQ and Competitive Pricing: We understand the challenges of high MOQs in the industry. This is why we offer a minimum order quantity as low as 2,000 pieces, making it easier for you to manage costs and inventory. Our pricing is also at least 10% lower than industry averages, providing you with cost-effective solutions.
Our Process:
Design and Prototyping: Our team of expert engineers will work closely with you to design and prototype your parts. Using advanced design software and rapid prototyping technologies, we can quickly bring your ideas to life.
Tooling and Mold Making: We have our own tooling and mold-making facilities, allowing us to strictly control the quality and timeline of your project. Our in-house capabilities ensure that we can produce precise molds according to your specifications.
Production: Once the molds are ready, we begin the MIM process. This involves mixing metal powders with a binder to create feedstock, injecting the feedstock into molds, and then debinding and sintering the parts to achieve the final product. Our state-of-the-art equipment ensures high precision and consistency in every batch.
Finishing and Quality Control: After sintering, parts may undergo additional finishing processes such as machining, heat treatment, or surface treatment to meet your exact requirements. Our quality control team performs rigorous inspections at every stage to ensure that each part meets your specifications.
Delivery and Support: We pride ourselves on our fast and reliable service. From initial consultation to final delivery, our team is here to support you. We offer flexible shipping options to ensure that your parts arrive on time, every time.
How much does injection molding cost?
The cost of metal injection molding (MIM) is influenced by various factors, including material cost, mold cost, equipment cost, part complexity, and production volume. Here is a detailed analysis of these cost factors:
1. Material Cost
Material Types: The cost varies significantly across different metal materials, such as stainless steel, nickel alloys, and titanium alloys.
Material Usage: The design and size of the parts determine the amount of material needed. Larger parts require more material, thereby increasing the cost.
2. Mold Cost
Mold Design Complexity: Complex mold designs require more time and technology to manufacture, which increases the mold cost.
Mold Manufacturing Methods: Common mold manufacturing methods include CNC machining, 3D printing, and electrical discharge machining (EDM). Each method has different costs and suitability.
Mold Materials: Molds are typically made of steel or aluminum. Steel molds are more durable but also more expensive.
3. Equipment Cost
Equipment Type: The cost of MIM equipment depends on its type and complexity. Specialized industrial injection molding equipment can range from $50,000 to $200,000.
Maintenance and Operation Costs: The maintenance and operation of the equipment require skilled technicians, adding to the operational costs.
4. Part Complexity
Design Complexity: Complex part designs necessitate more intricate molds and additional production steps, increasing the cost.
Surface Treatment: High-quality surface treatments (such as mirror polishing) require more time and labor, increasing the cost.
5. Production Volume
Low-Volume Production: Low-volume production (100 to several thousand pieces) typically uses 3D printed molds, which are cheaper but result in higher cost per part.
Medium-Volume Production: Medium-volume production (several thousand to tens of thousands of pieces) usually employs pre-hardened steel or aluminum molds, resulting in moderate costs.
High-Volume Production: High-volume production (hundreds of thousands of pieces) requires high-quality steel molds, with high initial costs but lower cost per part.
Cost Estimate Examples
The following are examples of cost estimates for different production volumes
Production Volume | Mold Cost | Material Cost (per piece) | Total Material Cost | Labor Cost (per piece) | Processing Cost (per piece) | Cost per Piece |
2,000 pieces | $5000 | $0.5 | $50 | $0.2 | $0.8 | $4 |
10,000 pieces | $5000 | $0.5 | $2,500 | $0.1 | $0.6 | $1.7 |
100,000
pieces |
$5000 | $0.5 | $50,000 | $0.05 | $0.4 | $1 |
How to reduce MIM costs
Simplify design: reduce unnecessary design complexity and surface treatment.
Choose the right material: use lower-cost materials such as ABS or polypropylene.
Optimize production volume: increase production volume to spread mold and equipment costs.
Use insert molds: insert molds and overmolding technology can save costs.
In summary, the cost of metal injection molding is affected by many factors. By optimizing the design, selecting the right material and production volume, the cost can be effectively reduced.
How precise is metal injection molding?
Metal injection molding (MIM) is capable of producing high-precision metal parts, with its accuracy reflected in the following aspects:
Dimensional Tolerance
The dimensional tolerance of MIM parts typically reaches ±0.3%, with some feature dimensions achieving tolerances as tight as ±0.1%. This high precision is mainly due to the use of high-precision molds and strict control of process parameters such as temperature and pressure.
Surface Roughness
MIM-produced parts generally have excellent surface quality, with surface roughness reaching Ra 0.5μm or better. This means that MIM parts often meet the requirements of many applications without the need for further surface treatment.
Complex Geometries
The MIM process can produce metal parts with complex shapes and fine structures, which are difficult to achieve with traditional metalworking methods. The flexibility in MIM mold design allows for the manufacturing of various complex geometries.
Comparison with Other Processes
- Compared to traditional powder metallurgy pressing processes, MIM parts have higher density (up to 95%-99% of the theoretical density of the raw material) and superior dimensional accuracy and surface quality.
- Compared to die casting, MIM can produce smaller, more intricate parts and can utilize a broader range of metal materials.
How popular is Metal Injection Molding?
Market Size
- Global Metal Injection Molding Market in 2023: The market size was $4.4 billion, and it is projected to reach $11.8 billion by 2036, with a compound annual growth rate (CAGR) of approximately 8.1%.
- Global Metal Injection Molding Market in 2022: The market size was $2.94 billion, and it is expected to reach $4.6 billion by 2028, with a CAGR of 7.65%.
- Global Metal Injection Molding Market in 2022: The market size was $4.12 billion, and it is projected to reach $8.02 billion by 2030, with a CAGR of approximately 8.68%.
Growth Trends
- Global Market: The metal injection molding market is expected to continue growing in the coming years, driven mainly by technological advancements, increased demand from the automotive industry, and the trend towards miniaturization of electronic products.
- Regional Markets: The Asia-Pacific region is expected to become the largest market, primarily due to rapid industrialization and expansion of the automotive industry in the region. Significant growth is also expected in the North American and European markets.
Based on the data, the growth curve of the global metal injection molding market can be visualized as follows:
Below is a graphical representation of the growth curve:
The metal injection molding market is experiencing significant growth, driven by the increasing demand from various industries such as automotive, electronics, and healthcare. The market is expected to grow at a strong compound annual growth rate, reaching $11.8 billion by 2036. This growth is attributed to technological advancements, the proliferation of electric vehicles, and the rising demand for miniature and complex components across various applications.
What is the future of metal injection molding?
Based on gathered information, Metal Injection Molding (MIM) has vast application prospects and continuous growth potential in the future. Here are some key points:
Continued Market Growth
- The global MIM market is expected to maintain a compound annual growth rate of 8-11%.
- The global MIM market was approximately $4.4 billion in 2023 and is projected to reach $11.8 billion by 2036.
- The Asia-Pacific region is seen as the fastest-growing regional market, mainly benefiting from industrialization and expansion in the automotive industry.
Technological Innovation Driving Application Expansion
- Development of new materials enables MIM to produce larger and more complex parts, expanding its application range.
- Integration with advanced manufacturing technologies such as 3D printing brings new design and production capabilities to MIM.
- Advancements in simulation and digital tools help optimize MIM processes, improving production efficiency and product quality.
Continuous Expansion of Application Areas
- The automotive industry’s demand for small, complex, high-strength parts continues to grow, making it a key application area for MIM.
- Industries requiring high-precision, high-performance parts such as medical devices and aerospace are also important application directions for MIM.
- Emerging fields such as consumer electronics, renewable energy, etc., also have new demands for MIM parts.
Sustainable Development as a Key Driver
- The MIM process has high material utilization and low energy consumption, conducive to achieving sustainable manufacturing.
- Developing environmentally friendly materials such as biodegradable binders promotes the transformation of MIM towards “green manufacturing”.
Overall, with its unique advantages, Metal Injection Molding is expected to maintain a strong development momentum in the future, continuously expand its market share in existing application areas, and also expand into more emerging industries, becoming an indispensable key process technology in the manufacturing industry.
How does Metal Injection Molding differ from Plastic Injection Molding?
Metal Injection Molding (MIM) and Plastic Injection Molding have many similarities in process and application, but there are also significant differences. Here are the main differences between the two:
Material
Metal Injection Molding (MIM): A mixture of metal powder and binder is used as the raw material. Commonly used metals include stainless steel, iron, titanium and other alloys.
Plastic Injection Molding: Thermoplastics (such as polypropylene, polyethylene, ABS, etc.) are used as the raw material.
Process steps
Metal Injection Molding (MIM):
Compounding: Mix metal powder with binder to form the “raw material”.
Injection Molding: Heat the raw material and inject it into the mold to form the “green blank”.
Debinding: Remove most of the binder, leaving a porous “brown blank”.
Sintering: Sintering at high temperature to remove the remaining binder and densify the metal particles to form the final part.
Plastic Injection Molding:
Feeding: Add plastic particles to the hopper.
Plasticizing: Melt the plastic by heating and screw rotation.
Injection: Molten plastic is injected into the mold to form a part.
Cooling and Ejection: After cooling, the mold is opened and the finished product is taken out.
Temperature and Pressure
Metal Injection Molding (MIM): The temperature is low during injection molding (about 200°C), but high temperature is required for sintering (usually between 1350°C and 1400°C).
Plastic Injection Molding: The temperature is low during injection molding (usually between 200°C and 300°C), and no subsequent high-temperature treatment is required.
Post-processing
Metal Injection Molding (MIM): Degreasing and sintering steps are required, and sometimes further heat treatment or machining is required.
Plastic Injection Molding: Usually only simple cooling and demolding are required, and sometimes flash removal or surface treatment is required. .
Plastic Injection Molding: Suitable for manufacturing a variety of plastic parts, widely used in consumer goods, automobiles, electronics, medical equipment and other fields.
Cost and Production Volume
Metal Injection Molding (MIM): The initial mold cost is high, but it is suitable for mass production of complex parts with low unit cost.
Plastic injection molding: The mold cost is relatively low, suitable for mass production, and the unit cost is also low.
In summary, metal injection molding and plastic injection molding have significant differences in materials, process steps, temperature and pressure, post-processing, application, cost and production volume. For details, please refer to the following table:
Characteristics | Metal Injection Molding (MIM) | Plastic Injection Molding (PIM) |
Material | Mixture of metal powders and binders (e.g., stainless steel, iron, titanium, etc.) | Thermoplastic plastics (e.g., polypropylene, polyethylene, ABS, etc.) |
Process Steps | Mixing, injection molding, debinding, sintering | Feeding, plasticizing, injection, cooling and demoulding |
Temperature and pressure | Injection molding has a low temperature (about 200°C), sintering requires high temperature (1350°C to 1400°C) | Injection molding has a low temperature (200°C to 300°C), no subsequent high temperature treatment is required |
Post-processing | Requires debinding and sintering steps, sometimes further heat treatment or machining | Usually only requires simple cooling and demoulding, sometimes flash removal or surface treatment |
Applications | Suitable for manufacturing small metal parts with complex shapes and high strength, widely used in medical, aerospace, automotive, electronics and other fields | Suitable for manufacturing various plastic parts, widely used in consumer goods, automobiles, electronics, medical equipment and other fields |
Cost and Production Volume | Initial tooling costs are high, but suitable for mass production of complex parts with low unit costs | Tooling costs are relatively low, suitable for mass production with low unit costs |
What is the difference between PM and MIM?
Powder Metallurgy (PM) and Metal Injection Molding (MIM) are two different metal forming processes. Here are their main differences:
Characteristics | Powder Metallurgy (PM)) | Metal Injection Molding (MIM) |
Process Steps | Powder preparation, mixing, pressing, sintering | Feedstock mixing, injection molding, debinding, sintering |
Material Form | Metal powder | Metal powder mixed with binders |
Forming Method | Pressing | Injection molding |
Part Complexity | Suitable for simple shapes | Suitable for complex geometries |
Dimensional | Accuracy Generally lower | High precision (±0.3%) |
Surface Quality | Requires post-processing | High surface finish |
Production Batch Size | Suitable for medium to small batch production | Suitable for large batch production |
Material Utilization | Relatively high | Extremely high |
Application Fields | Automotive parts, tools, mechanical parts | Medical devices, electronic products, automotive parts, aerospace |
Cost | Lower mold cost, suitable for small batch production | Higher mold cost, suitable for large batch production |
Production Cycle | Short | Longer, especially for mold making and sintering steps |
Explanation:
- Process Steps Powder Metallurgy (PM): Includes powder preparation, mixing, pressing, and sintering. Metal powders are pressed and then sintered at high temperatures to obtain dense metal parts. Metal Injection Molding (MIM): Includes feedstock mixing, injection molding, debinding, and sintering. Metal powders mixed with binders are injected into molds to form “green” parts, which are then rebound and sintered to obtain the final parts.
- Material Form Powder Metallurgy (PM): Uses pure metal powders or alloy powders. Metal Injection Molding (MIM): Uses a mixture of metal powders and binders, with the binders typically being thermoplastic polymers or wax.
- Forming Method Powder Metallurgy (PM): Formed by pressing, suitable for simple-shaped parts. Metal Injection Molding (MIM): Formed by injection molding, suitable for parts with complex geometries.
- Part Complexity Powder Metallurgy (PM): Suitable for producing parts with relatively simple shapes. Metal Injection Molding (MIM): Can produce parts with complex shapes and fine structures.
- Dimensional Accuracy Powder Metallurgy (PM): Generally lower dimensional accuracy, requiring post-processing. Metal Injection Molding (MIM): High dimensional accuracy, typically up to ±0.3%.
- Surface Quality Powder Metallurgy (PM): Generally average surface quality, requiring post-processing. Metal Injection Molding (MIM): High surface finish, usually requiring no further treatment.
- Production Batch Size Powder Metallurgy (PM): Suitable for medium to small batch production. Metal Injection Molding (MIM): Suitable for large batch production, especially for products with annual output exceeding 50,000 pieces.
- Material Utilization Powder Metallurgy (PM): Relatively high material utilization. Metal Injection Molding (MIM): Extremely high material utilization, with almost no waste.
- Application Fields Powder Metallurgy (PM): Widely used in automotive parts, tools, mechanical parts, etc. Metal Injection Molding (MIM): Widely used in medical devices, electronic products, automotive parts, aerospace, etc.
- Cost Powder Metallurgy (PM): Lower mold cost, suitable for small batch production. Metal Injection Molding (MIM): Higher mold cost, suitable for large batch production.
- Production Cycle Powder Metallurgy (PM): Shorter production cycle. Metal Injection Molding (MIM): Longer production cycle, especially for mold making and sintering steps. In conclusion, Powder Metallurgy (PM) and Metal Injection Molding (MIM) have their own advantages and disadvantages, suitable for different applications. PM is suitable for producing parts with relatively simple shapes, with low cost and suitable for medium to small batch production; while MIM is suitable for producing parts with complex shapes and high precision, suitable for large batch production.
What is the difference between Metal Injection Molding and Die Casting?
Metal injection molding (MIM) and die casting are two common metal forming processes, each with its own unique advantages and application scope. The following are their main differences:
Characteristics | Metal Injection Molding (MIM) | Die Casting |
Materials | Applicable to both ferrous and non-ferrous metals, such as stainless steel, titanium alloys, nickel alloys, etc. | Primarily applicable to non-ferrous metals, such as aluminum, zinc, magnesium, etc. |
Process Steps | Mixing, injection molding, debinding, sintering | Mold design, metal preparation, injection, casting, post-processing |
Complexity | Capable of producing small, complex geometric parts | Suitable for producing larger, simpler parts |
Dimensional Accuracy | High accuracy, typically up to ±0.3% | High accuracy, but often requires subsequent finishing |
Surface Quality | High surface finish, usually does not require further processing | Moderate surface quality, may require finishing |
Production Batch Size | Suitable for large-scale production | Suitable for medium to large-scale production |
Mold Lifespan | Shorter mold lifespan, typically 150,000 to 300,000 shots | Longer mold lifespan, typically over 1,000,000 shots |
Material Utilization | High material utilization, almost no waste | Relatively high material utilization, but some waste |
Cost | Higher initial mold cost, suitable for large-scale production | Lower initial mold cost, suitable for medium to large-scale production |
Post-Processing | Requires multiple steps such as debinding and sintering | Requires deburring and surface treatment |
Applications | Medical devices, electronics, automotive parts, aerospace, etc. | Automotive, electronics, appliances, aerospace, etc. |
- Materials Metal Injection Molding (MIM): Suitable for a variety of metal materials, including stainless steel, titanium alloys, nickel alloys, etc. These materials are mixed with binders in powder form, suitable for manufacturing complex parts. Die Casting: Mainly suitable for non-ferrous metals such as aluminum, zinc, magnesium, etc. These materials are melted at high temperatures and injected into molds, suitable for manufacturing larger parts.
- Process Steps Metal Injection Molding (MIM): Includes steps such as mixing, injection molding, debinding, and sintering. Each step needs to be precisely controlled to ensure the quality of the final parts. Die Casting: Includes steps such as mold design, metal preparation, injection, casting, and post-processing. The process is relatively simple but requires high temperature and pressure.
- Complexity of Parts Metal Injection Molding (MIM): Able to produce small, complex geometric shapes, suitable for high precision and complex designs. Die Casting: Suitable for producing larger, simpler parts with lower complexity.
- Dimensional Accuracy Metal Injection Molding (MIM): High dimensional accuracy, typically up to ±0.3%, suitable for parts with high precision requirements. Die Casting: High accuracy, but usually requires subsequent finishing to meet final dimensional requirements.
- Surface Quality Metal Injection Molding (MIM): High surface finish, usually does not require further processing. Die Casting: Moderate surface quality, may require finishing and surface treatment.
- Production Batch Size Metal Injection Molding (MIM): Suitable for large-scale production, especially for products with annual production exceeding 50,000 units. Die Casting: Suitable for medium to large-scale production, with fast production speed.
- Mold Lifespan Metal Injection Molding (MIM): Shorter mold lifespan, typically 150,000 to 300,000 shots. Die Casting: Longer mold lifespan, typically over 1,000,000 shots.
- Material Utilization Metal Injection Molding (MIM): High material utilization, almost no waste. Die Casting: Relatively high material utilization, but there is some waste.
- Cost Metal Injection Molding (MIM): Higher initial mold cost, but suitable for large-scale production with lower unit cost. Die Casting: Lower initial mold cost, suitable for medium to large-scale production.
- Post-Processing Metal Injection Molding (MIM): Requires multiple steps such as debinding and sintering. Die Casting: Requires deburring and surface treatment.
- Applications Metal Injection Molding (MIM): Widely used in medical devices, electronic products, automotive parts, aerospace, etc. Die Casting: Widely used in automotive, electronics, appliances, aerospace, etc.
In conclusion, Metal Injection Molding (MIM) and Die Casting have their own advantages and disadvantages, suitable for different application scenarios. MIM is suitable for producing small, complex, high-precision parts, while Die Casting is suitable for producing larger, simpler parts. The choice of process depends on the specific requirements of the parts, production batch size, and cost considerations.
Summary
Metal injection molding (MIM) technology plays an important role in modern manufacturing, mainly due to its ability to efficiently and economically produce small metal parts with complex shapes and high performance. Although the MIM process involves multiple complex steps and the initial mold cost is high, its high material utilization, high production efficiency and excellent product quality give it significant advantages in mass production. In the future, with the continuous advancement of technology and the development of new materials, the application scope of MIM will be further expanded, and the market size is expected to continue to grow, especially in high-demand fields such as automobiles, medical and electronics.