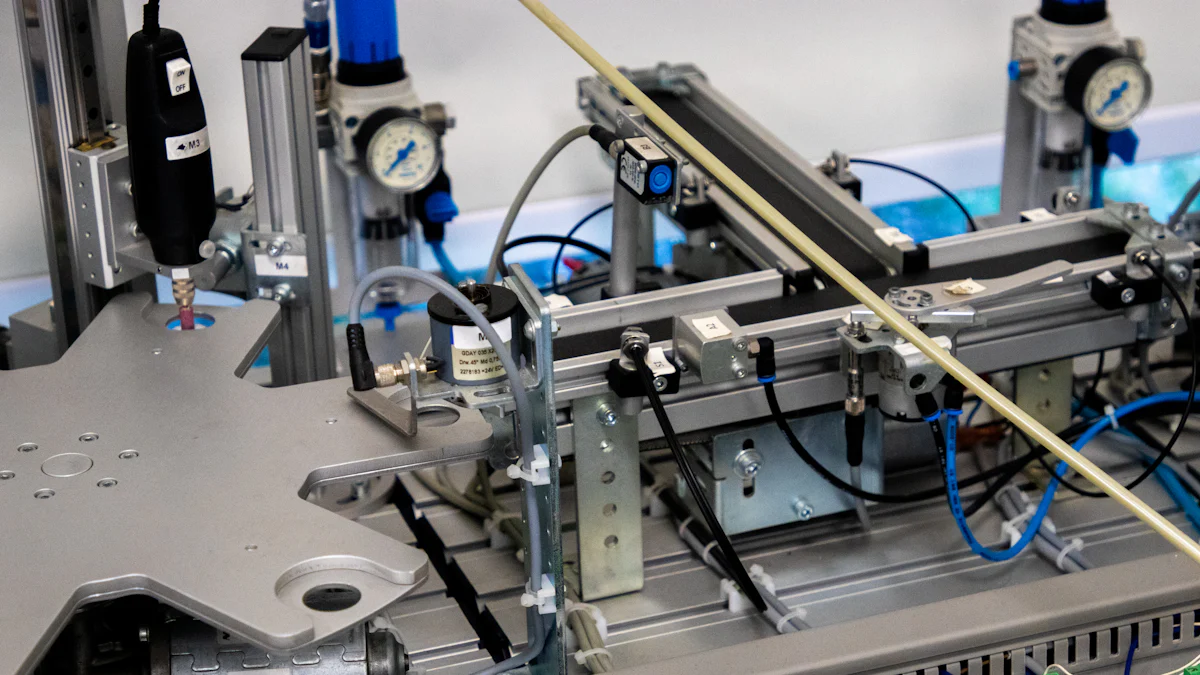
Metal Injection Molding (MIM) design plays a pivotal role in modern manufacturing. It combines the flexibility of plastic injection molding with the strength of metal, offering a cost-effective solution for producing small, intricate parts. You can achieve complex geometries that traditional methods struggle to replicate. Understanding design considerations is crucial for successful MIM implementation. This knowledge ensures that you meet industry requirements and cost targets, making MIM a preferred choice across various sectors. As the MIM market continues to grow, its significance in manufacturing becomes increasingly evident.
Advantages of Metal Injection Molding
Metal Injection Molding (MIM) offers several advantages that make it a preferred choice in modern manufacturing. By understanding these benefits, you can appreciate why MIM is increasingly popular across various industries.
Efficiency in Production
MIM stands out for its production efficiency. You can produce a large number of parts in a shorter time compared to traditional methods like machining or die casting. This efficiency stems from the reduced number of manufacturing steps involved in MIM. By streamlining the process, you not only save time but also cut down on labor costs. The ability to produce high volumes quickly makes MIM an ideal solution for industries requiring mass production of small, intricate components.
Low Waste and Material Utilization
One of the significant benefits of MIM is its low waste generation. Traditional metal forming techniques often result in substantial material waste. In contrast, MIM optimizes material utilization, ensuring minimal waste. You achieve this through precise control over the injection process, which allows for exact material usage. This efficiency not only reduces costs but also aligns with sustainable manufacturing practices by minimizing environmental impact.
Design Flexibility and Complexity
MIM provides unparalleled design flexibility. You can create complex geometries and intricate designs that are challenging to achieve with other manufacturing methods. This flexibility allows for innovative product designs without compromising on strength or performance. The process supports the production of small, high-precision parts, making it suitable for industries like firearms, where precision is crucial. By leveraging M IM, you can push the boundaries of design while maintaining cost-effectiveness and quality.
Key Design Considerations in Metal Injection Molding
When designing for Metal Injection Molding, you must consider several key factors to ensure the success of your project. These considerations help you optimize the manufacturing process and achieve high-quality results.
Gate Positioning
Gate positioning plays a crucial role in the Metal Injection Molding process. You need to strategically locate gates to direct the material flow onto a core pin or cavity wall. This positioning ensures stability throughout the molding process. Proper gate placement minimizes defects and enhances the overall quality of the final product. By focusing on gate positioning, you can prevent issues such as air entrapment and uneven material distribution, which can compromise the integrity of the molded part.
Wall Thickness
Wall thickness is another critical factor in Metal Injection Molding design. You should aim for uniform wall thickness to prevent distortion in the molded parts. Variations in wall thickness can lead to uneven cooling and shrinkage, resulting in defects. By maintaining consistent wall thickness, you ensure that the material flows smoothly and evenly during the injection process. This consistency helps you achieve precise dimensions and enhances the structural integrity of the final product.
Draft Angles
Incorporating draft angles into your design is essential for successful Metal Injection Molding. Draft angles facilitate the removal of parts from the mold without causing damage. You should add draft to component faces to prevent dragging and surface scratches during ejection. Typically, draft angles range from 0.25 to 3 degrees, depending on the complexity of the part. By including appropriate draft angles, you ensure smooth ejection and maintain the quality of the molded parts.
By considering these key design elements, you can optimize the Metal Injection Molding process and produce high-quality components. These considerations help you achieve precision, efficiency, and cost-effectiveness in your manufacturing projects.
Material Selection in Metal Injection Molding
Choosing the right material for Metal Injection Molding (MIM) is crucial. It affects every stage of the process, from molding to the final product’s performance. The material you select will determine the mechanical properties, dimensional stability, and overall quality of the components you produce.
Impact on Performance
The performance of MIM parts heavily depends on the material chosen. Different metals offer varying levels of strength, corrosion resistance, and machinability. For instance, alloy steels and stainless steels are popular choices due to their excellent mechanical properties and resistance to wear and corrosion. These materials can achieve densities close to 98% of their theoretical values, providing strength comparable to wrought products. When selecting a material, consider factors such as the part’s weight, tolerance requirements, and the mechanical stress it will endure. This careful selection ensures that the final product meets the desired performance standards.
Dimensional Stability
Dimensional stability is another critical aspect influenced by material selection. The fine particle size used in MIM feedstock allows for high sintered densities, which contribute to the dimensional accuracy of the parts. Materials like heat-resistant alloys maintain their shape and size even under extreme conditions, making them ideal for applications requiring precise dimensions. You must also consider the material’s shrinkage characteristics during the sintering process. Proper material selection helps minimize dimensional changes, ensuring that the final product retains its intended shape and size.
By understanding the impact of material selection on performance and dimensional stability, you can optimize the Metal Injection Molding process. This knowledge allows you to produce high-quality components that meet industry standards and application requirements.
The Sintering Process and Its Impact on Design
Overview of the Sintering Process
In Metal Injection Molding, the sintering process is a critical phase that transforms the ‘brown’ part into a dense, solid component. You begin by heating the brown part in a specialized furnace. This furnace operates under an inert gas atmosphere to prevent oxidation, ensuring the integrity of the metal. The temperature during sintering is carefully controlled, reaching levels close to the metal’s melting point. This high temperature promotes partial melting and bonding of the metal particles, forming strong metallurgical bonds. As a result, the part achieves its final shape and mechanical properties.
Sintering not only densifies the powder but also enhances the strength and durability of the component. After sintering, you might need to perform additional processes such as heat treatments or surface finishing to meet specific application requirements. These steps ensure that the final product possesses the desired properties and performance characteristics.
Design Adjustments for Sintering
Designing for the sintering process requires careful consideration of several factors. You must account for the shrinkage that occurs during sintering. As the metal particles bond and densify, the part typically shrinks by 15-20%. To compensate for this, you should design the initial green part slightly larger than the desired final dimensions. This adjustment ensures that the final product meets the precise specifications.
Another important consideration is the uniformity of the part’s geometry. You should aim for consistent wall thickness and avoid abrupt changes in cross-section. These design choices help maintain even shrinkage and prevent warping or distortion during sintering. By ensuring uniformity, you enhance the dimensional stability and structural integrity of the final component.
Additionally, you should consider the material’s sintering behavior. Different metals exhibit varying shrinkage rates and bonding characteristics. Understanding these properties allows you to select the appropriate material and design the part accordingly. This knowledge helps you optimize the sintering process and achieve high-quality results.
By making these design adjustments, you can effectively navigate the challenges of the sintering process in Metal Injection Molding. These considerations enable you to produce components that meet industry standards and application requirements.
Applications of Metal Injection Molding
Metal Injection Molding (MIM) has revolutionized various industries by enabling the production of small, intricate parts with high precision. Its ability to create complex geometries and maintain tight tolerances makes it an ideal choice for several applications.
Automotive Industry
In the automotive industry, MIM plays a crucial role in manufacturing lightweight components. You can produce dense, lightweight parts that help meet stringent fuel efficiency and emission standards. By replacing multiple parts with a single MIM component, you reduce weight and improve vehicle performance. This process not only enhances fuel economy but also contributes to the overall sustainability of automotive manufacturing.
Medical Industry
The medical industry benefits significantly from MIM technology. You can create small, complex components required for medical devices with high precision. MIM allows for the production of parts with superior mechanical and physical properties, essential for medical applications. The ability to produce intricate geometries ensures that medical devices meet the stringent requirements for safety and functionality. This precision is vital for components used in surgical instruments and implantable devices.
Firearms and Defense
In the firearms and defense sector, MIM is widely used for producing high-volume components without compromising quality. You can manufacture precise parts such as hammers, triggers, and levers, which are critical for firearm functionality. The process ensures that each component meets the necessary specifications for performance and reliability. By utilizing MIM, you achieve consistent quality across large production runs, essential for the defense industry.
MIM’s versatility and efficiency make it a preferred choice across these industries. Its ability to produce high-quality components with intricate designs and tight tolerances highlights its importance in modern manufacturing.
Agricultural Equipment
Metal Injection Molding (MIM) has become a valuable asset in the agricultural equipment industry. You can leverage MIM to produce small, intricate components that are essential for modern farming machinery. These parts often require high precision and durability, which MIM can provide effectively.
-
Precision and Complexity: Agricultural equipment often demands components with complex geometries and tight tolerances. MIM excels in producing such parts, ensuring that each component fits perfectly within the machinery. This precision enhances the overall performance and reliability of the equipment.
-
Durability and Strength: The agricultural environment is harsh, with equipment exposed to dirt, moisture, and heavy loads. MIM parts offer superior mechanical properties, making them ideal for such conditions. You can rely on MIM to produce components that withstand wear and tear, ensuring longevity and reducing maintenance costs.
-
Cost-Effectiveness: By using MIM, you can replace multiple parts with a single, well-designed component. This consolidation reduces assembly time and costs, making the manufacturing process more efficient. The ability to produce high volumes of parts quickly further contributes to cost-effectiveness, benefiting both manufacturers and end-users.
-
Sustainability: MIM aligns with sustainable manufacturing practices by minimizing material waste. In agriculture, where efficiency and sustainability are crucial, MIM provides an environmentally friendly solution. You can achieve optimal material utilization, reducing the environmental impact of production.
Incorporating MIM into agricultural equipment manufacturing offers numerous advantages. By focusing on precision, durability, cost-effectiveness, and sustainability, you can enhance the quality and performance of farming machinery. This approach not only meets industry demands but also supports the advancement of modern agriculture.
Importance of Quality in Metal Injection Molding Processes
Ensuring quality in Metal Injection Molding (MIM) is crucial for producing reliable and high-performing components. By focusing on quality, you can achieve consistent results that meet industry standards and customer expectations.
Ensuring Consistent Product Quality
To maintain consistent product quality in MIM, you must implement rigorous quality control measures throughout the manufacturing process. Start by selecting high-quality raw materials. The choice of material directly impacts the mechanical properties and durability of the final product. Use precise control over the injection process to ensure uniformity in each batch. This consistency helps prevent defects and ensures that every part meets the required specifications.
Regular inspections and testing are essential. Conduct dimensional checks and mechanical tests to verify that the components meet the desired standards. By identifying and addressing any deviations early, you can minimize waste and reduce the risk of defective products reaching the market.
“Quality is not an act, it is a habit.” – Aristotle
Adopting a culture of quality within your organization fosters continuous improvement. Encourage your team to prioritize quality at every stage, from design to production. This commitment ensures that you consistently deliver high-quality MIM components.
Consulting with Experts for Design Optimization
Consulting with experts in Metal Injection Molding can significantly enhance the quality of your products. These professionals bring valuable insights and experience to the table, helping you optimize your designs for better performance and manufacturability.
Experts can guide you in selecting the right materials and designing components that maximize the benefits of MIM. They can also assist in identifying potential issues early in the design phase, allowing you to make necessary adjustments before production begins. This proactive approach reduces the likelihood of costly errors and rework.
By collaborating with experts, you gain access to the latest advancements in MIM technology. They can introduce you to innovative techniques and tools that improve efficiency and quality. This knowledge enables you to stay competitive in the market and meet the evolving demands of your customers.
Incorporating expert advice into your MIM processes ensures you produce components that meet and exceed industry standards. This focus on quality and continuous improvement positions you for success in the competitive manufacturing world.
Future Trends in Metal Injection Molding
Metal Injection Molding (MIM) continues to evolve, driven by technological advancements and increasing industry adoption. Understanding these trends can help you stay ahead in the competitive manufacturing landscape.
Technological Advancements
-
Enhanced Materials: New materials are being developed for MIM. These materials offer improved mechanical properties and greater resistance to wear and corrosion, allowing you to produce components that meet higher performance standards.
-
Automation and AI Integration: Automation is transforming MIM processes. You can now use AI to optimize production, reducing errors and increasing efficiency. Automated systems streamline operations, allowing you to produce high volumes with consistent quality.
-
Improved Sintering Techniques: New sintering technologies are emerging. These techniques enhance the density and strength of MIM parts. By adopting these methods, you can achieve better dimensional accuracy and reduce post-processing requirements.
-
Sustainability Innovations: The focus on sustainability is growing. You can expect innovations that minimize waste and energy consumption. These eco-friendly practices align with global efforts to reduce environmental impact.
Industry Adoption
-
Wider Application Range: MIM is expanding into new industries. You will find its applications in consumer electronics, aerospace, and more. This growth is due to MIM’s ability to efficiently produce complex, high-precision parts.
-
Increased Demand for Customization: The demand for customized products is rising. MIM offers the flexibility to create tailored components. You can meet specific customer needs without compromising on quality or cost.
-
Collaboration with Experts: Consulting with experts is crucial as MIM becomes more complex. Experts can guide you through the intricacies of the process. They help you optimize designs and select the right materials, ensuring successful outcomes.
-
Global Market Expansion: The global MIM market is expanding. You will see increased adoption in emerging markets. This growth allows you to explore new business avenues and reach a broader customer base.
By keeping abreast of these trends, you can leverage Metal Injection Molding to its full potential. Embracing technological advancements and understanding industry dynamics will position you for success in the evolving manufacturing sector.
Design plays a critical role in the success of Metal Injection Molding. By focusing on design, you can harness the full potential of this efficient manufacturing process. Investing in quality processes and consulting with experts ensures optimal outcomes. This approach not only enhances product quality but also aligns with industry standards. Metal Injection Molding has the potential to revolutionize manufacturing across various industries. Its ability to produce small, complex, high-performance parts makes it a valuable asset in automotive, medical, and aerospace sectors. Embrace MIM to stay competitive and innovative.