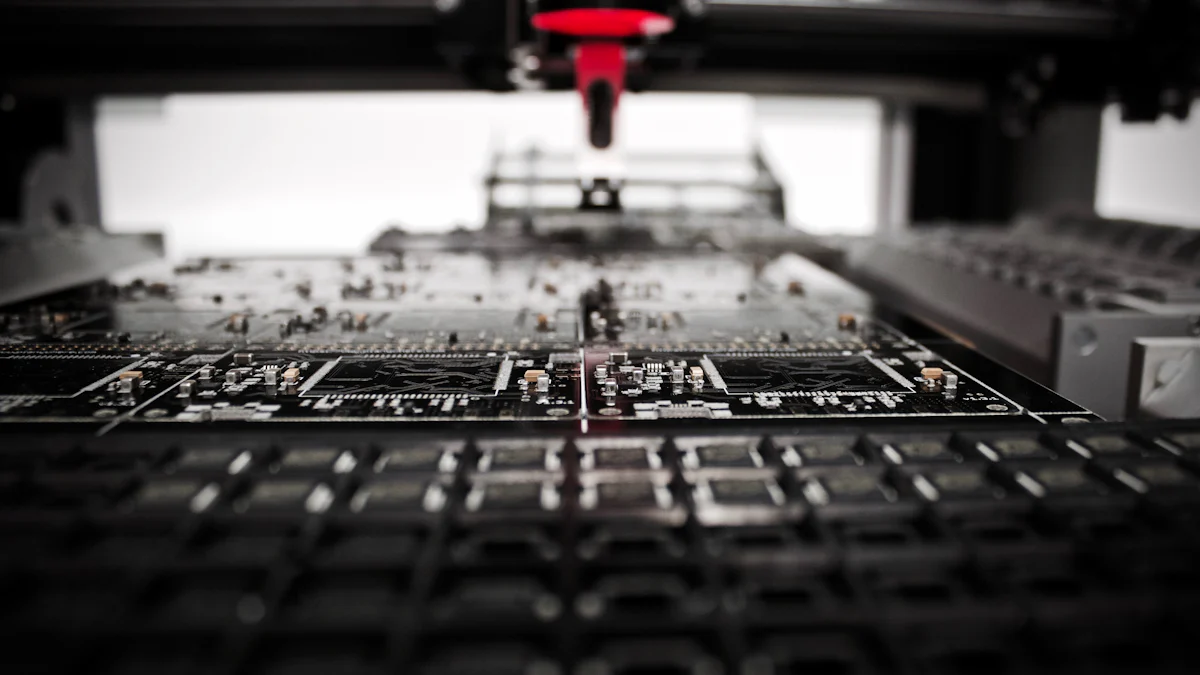
Design plays a pivotal role in the success of the MIM Process. It determines how efficiently components are produced and directly influences their quality. A well-thought-out design minimizes manufacturing challenges and ensures precision in the final product. Collaboration with experienced MIM vendors during the design phase enhances manufacturability. Their expertise helps identify potential issues early, saving time and resources. Designers must approach the process clearly understanding material behavior and production constraints to achieve optimal results.
Key Takeaways
- Effective design is crucial for successful MIM manufacturing, influencing efficiency and product quality.
- Collaboration with experienced MIM vendors during the design phase can help identify potential issues early, saving time and resources.
- Maintaining uniform wall thickness prevents defects and ensures structural integrity in MIM components.
- Proper placement of gating and injection points is vital for achieving high-quality parts with minimal defects.
- Incorporating draft angles in designs facilitates smooth ejection from molds, preserving dimensional accuracy.
- Selecting the right materials is key to optimizing performance and manufacturability in MIM components.
- Designers should prioritize eco-friendly practices, as MIM allows for material reuse, promoting sustainability.
Overview of the MIM Process
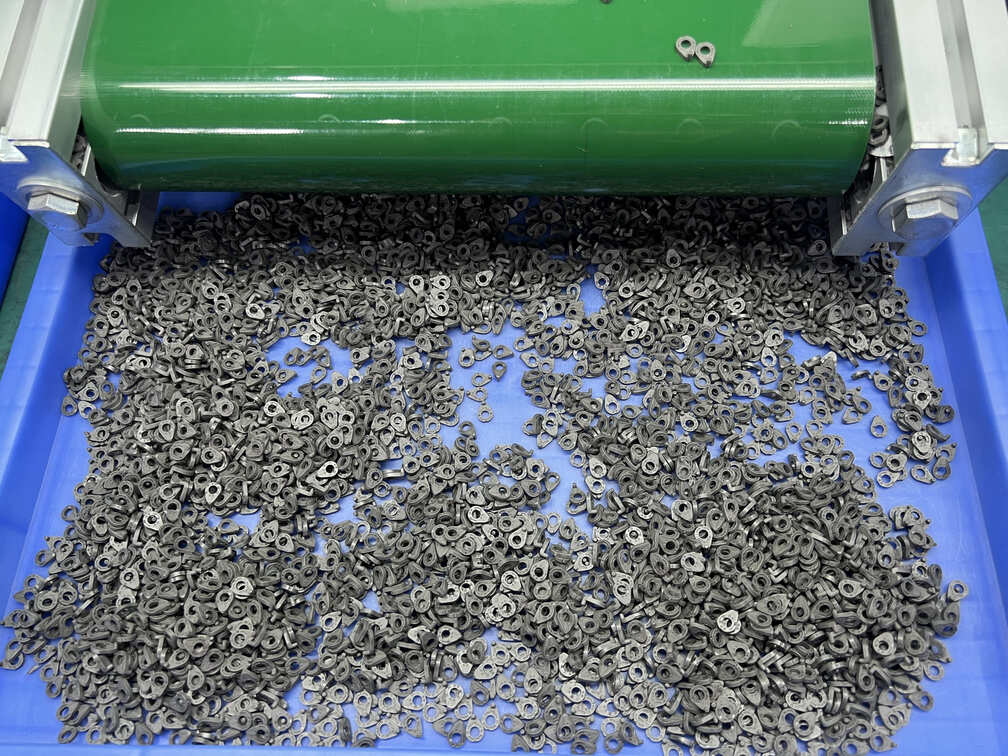
What is the MIM Process?
The Metal Injection Molding (MIM) process combines the versatility of plastic injection molding with the strength and durability of metal.
This process allows manufacturers to produce intricate shapes with exceptional precision. It bridges the gap between traditional machining and casting methods, offering a cost-effective solution for complex geometries. The MIM process is particularly suited for small to medium-sized components that require tight tolerances and high performance.
Advantages of the MIM Process
The MIM process offers several advantages that make it a preferred choice for manufacturing complex metal parts:
- Design Flexibility: MIM enables the production of intricate designs that would be challenging or impossible with conventional methods.
- Material Efficiency: The process minimizes material waste, as excess feedstock can often be reused.
- Cost-Effectiveness: For high-volume production, MIM reduces costs by eliminating the need for extensive machining or secondary operations.
- High Precision: The process achieves tight tolerances and consistent quality across batches.
- Wide Material Selection: MIM supports a variety of metals, including stainless steel, titanium, and nickel-based alloys, catering to diverse application needs.
These benefits make the MIM process an attractive option for industries seeking to balance complexity, performance, and cost.
Applications of the MIM Process
Industries benefiting from MIM (e.g., automotive, medical, aerospace)
The MIM process serves a wide range of industries due to its ability to produce high-quality components with complex geometries.
- Automotive: Manufacturers use MIM to create precision parts such as gears, turbocharger components, and fuel injector nozzles.
- Medical: The medical sector relies on MIM for surgical instruments, orthodontic brackets, and implantable devices.
- Aerospace: Aerospace companies benefit from MIM’s ability to produce lightweight yet durable components, including fasteners and structural parts.
These industries leverage the unique capabilities of MIM to meet stringent performance and reliability standards.
Types of components best suited for MIM
Certain types of components are particularly well-suited for the MIM process:
- Small and Complex Parts: MIM excels at producing small components with intricate details, such as connectors and microgears.
- High-Performance Components: Parts requiring superior mechanical properties, such as strength and wear resistance, are ideal candidates.
- Precision Parts: Components with tight dimensional tolerances, such as housings and brackets, benefit from MIM’s accuracy.
The process is most effective for parts that combine complexity, precision, and high production volumes.
Key Design Principles for the MIM Process
Uniform Wall Thickness
Maintaining uniform wall thickness is a fundamental principle in the MIM process. Consistent wall thickness ensures even material flow during injection, reducing the risk of defects such as warping or sink marks. Uneven walls can lead to variations in cooling rates, which may compromise the structural integrity of the component. Designers should aim for a balanced design that avoids abrupt changes in thickness. Gradual transitions between sections help maintain part stability and improve manufacturability.
Thin walls can reduce material usage and shorten cycle times, but they must remain within the limits of the MIM process to prevent breakage during sintering. Thick walls, on the other hand, may increase shrinkage and extend sintering times. Striking the right balance between thickness and functionality is essential for achieving optimal results.
Gating and Injection Points
The placement of gating and injection points significantly impacts the quality of MIM components. Properly positioned gates ensure smooth material flow into the mold cavity, minimizing the risk of voids or incomplete fills. Designers must consider the geometry of the part and the flow characteristics of the feedstock when determining gate locations.
Centralized gates often work well for symmetrical parts, while edge gates may suit asymmetrical designs. Multiple gates may be necessary for larger or more complex components to ensure uniform filling. However, excessive gating can leave visible marks on the finished part, so careful planning is required to balance functionality and aesthetics.
Gate size also plays a critical role. Oversized gates may lead to material wastage, while undersized gates can restrict flow and cause defects. Collaborating with MIM vendors during the design phase helps optimize gate placement and size, ensuring high-quality results.
Ejection and Parting Lines
Ejection and parting lines are unavoidable in the MIM process, but thoughtful design can minimize their impact. Ejection lines form where the mold ejector pins push the part out of the cavity, while parting lines occur at the junction of mold halves. Both features can affect the appearance and functionality of the final component.
Designers should position ejection and parting lines in non-critical areas whenever possible. Placing these lines on flat or less visible surfaces reduces their prominence and simplifies post-processing. Avoiding sharp edges near ejection points prevents damage during removal, ensuring the part retains its intended shape.
The draft angle also influences ejection efficiency. Including a slight taper on vertical surfaces allows parts to release smoothly from the mold, reducing the risk of deformation. Proper planning of ejection and parting lines enhances both the manufacturability and aesthetic appeal of MIM components.
Guidelines for Dimensions, Tolerances, and Material Choices
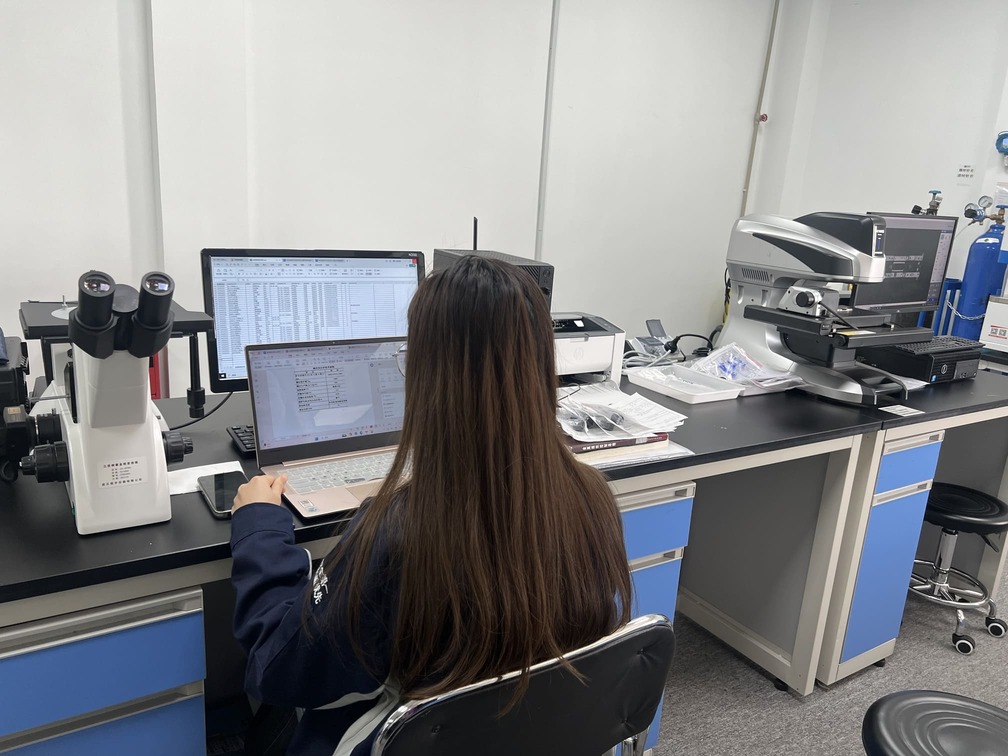
Dimensional Considerations
Dimensional accuracy plays a critical role in the success of components produced through the MIM Process. Designers must account for shrinkage during sintering, which typically ranges from 15% to 20%. This predictable reduction in size requires precise scaling of the mold cavity to ensure the final part meets the desired specifications. Failure to consider this factor can result in parts that deviate from required tolerances.
Tight tolerances are achievable with MIM, but they demand careful planning.
Flat surfaces and uniform dimensions help reduce distortion during sintering. Incorporating large flat areas or common planes across multiple components minimizes warping and ensures consistency. For complex geometries, designers should prioritize symmetry to maintain structural integrity and simplify the molding process.
Material Selection
Material selection significantly influences the performance and manufacturability of MIM components. The MIM Process supports a wide range of materials, including stainless steel, titanium, and nickel-based alloys. Each material offers unique properties that cater to specific applications. For example, stainless steel provides excellent corrosion resistance, while titanium delivers high strength-to-weight ratios.
When selecting materials, designers must consider factors such as mechanical properties, thermal behavior, and compatibility with the intended application. Components subjected to high stress or extreme temperatures require materials with superior strength and thermal stability. For medical or aerospace applications, biocompatibility and lightweight characteristics may take precedence.
Material flow characteristics also impact the molding process. Feedstock with poor flowability can lead to defects such as voids or incomplete fills. Collaborating with MIM vendors ensures the chosen material aligns with the design requirements and manufacturing constraints. Vendors can provide insights into material behavior during injection, debinding, and sintering, helping designers make informed decisions.
Recycling and sustainability should also factor into material selection. Many MIM materials allow for the reuse of excess feedstock, reducing waste and promoting cost efficiency. Designers who prioritize eco-friendly practices can leverage this advantage to align with industry trends and environmental standards.
Practical Tips for Optimizing MIM Design
Avoiding Sharp Corners
Sharp corners in MIM designs often lead to stress concentrations, which can weaken the final component. During the MIM process, sharp edges may also hinder material flow, resulting in defects such as voids or incomplete fills. Designers should replace sharp corners with rounded edges or fillets to improve structural integrity and manufacturability.
Rounded edges promote smoother material flow during injection, reducing the likelihood of defects. They also enhance the durability of the part by distributing stress more evenly. For internal corners, a minimum radius should be maintained to prevent cracking during sintering. Collaborating with MIM vendors can help determine the optimal radius for specific materials and applications.
Maintaining Draft Angles
Draft angles play a crucial role in ensuring the smooth ejection of parts from the mold. Without an adequate draft, components may stick to the mold cavity, leading to deformation or damage during removal. Designers should incorporate a slight taper on vertical surfaces to facilitate ejection and maintain the part’s dimensional accuracy.
The recommended draft angle varies depending on the material and the complexity of the design. For most MIM components, a draft angle of 1 to 2 degrees is sufficient. However, deeper cavities or intricate geometries may require larger angles. Including draft angles not only simplifies the molding process but also reduces wear on the mold, extending its lifespan.
Selecting Appropriate Injection Points
Injection points determine how the feedstock enters the mold cavity during the MIM process. Proper placement of these points ensures uniform material flow, minimizing the risk of defects such as weld lines or air traps. Designers must consider the geometry of the part and the flow characteristics of the feedstock when selecting injection points.
Centralized injection points work well for symmetrical designs, while multiple points may be necessary for larger or more complex components. However, excessive injection points can leave visible marks on the finished part, so careful planning is essential. Collaborating with MIM vendors allows designers to optimize injection point placement, balancing functionality and aesthetics.
Injection point size also impacts the quality of the final component. Oversized points may lead to material wastage, while undersized points can restrict flow and cause incomplete fills. Designers should work closely with vendors to determine the ideal size and location for injection points, ensuring high-quality results.
Thoughtful design remains a cornerstone of success in the MIM Process. It directly influences manufacturability, efficiency, and the quality of final components. Designers who collaborate with experienced MIM vendors gain valuable insights into material behavior and production constraints. This partnership helps identify potential challenges early, ensuring smoother manufacturing workflows. By leveraging the unique capabilities of the MIM Process, designers can create intricate, precise components that meet demanding industry standards. A strategic approach to design unlocks the full potential of this innovative manufacturing method.
FAQ
What is the typical size range for MIM components?
MIM components are generally small to medium in size, with weights ranging from 0.1 grams to 100 grams. The process excels at producing intricate parts that fit within these dimensions. Larger components may require alternative manufacturing methods due to limitations in material flow and sintering.
How does the MIM process handle complex geometries?
The MIM process is well-suited for creating complex geometries. It uses advanced mold designs and feedstock injection techniques to achieve intricate shapes. Features such as undercuts, thin walls, and fine details can be incorporated with precision. Designers should collaborate with MIM vendors to ensure the feasibility of highly complex designs.
What materials are commonly used in MIM manufacturing?
MIM supports a wide range of materials, including stainless steel, titanium, nickel-based alloys, and cobalt-chromium. Each material offers unique properties, such as corrosion resistance, high strength, or biocompatibility. The choice of material depends on the application requirements and performance criteria.
How does shrinkage during sintering affect the final part?
Shrinkage during sintering typically ranges from 15% to 20%. This size reduction occurs as metal particles fuse, increasing density. Designers must account for this predictable shrinkage when scaling the mold cavity. Accurate calculations ensure the final part meets dimensional specifications.
Can MIM components achieve tight tolerances?
Yes, MIM components can achieve tight tolerances, often within ±0.3% of the nominal dimensions. However, achieving such precision requires careful planning and collaboration with MIM vendors. Overly tight tolerances may increase production costs and rejection rates, so designers should balance precision with manufacturability.
What industries benefit most from MIM technology?
Industries such as automotive, medical, aerospace, and consumer electronics benefit significantly from MIM technology. Automotive manufacturers use it for gears and fuel injector nozzles. The medical field relies on MIM for surgical instruments and implants. Aerospace companies produce lightweight, durable components, while electronics manufacturers create intricate connectors and housings.
Are there limitations to the MIM process?
While MIM offers many advantages, it has limitations. The process is less suitable for very large components or parts requiring extreme thickness variations. High tooling costs may also make it less economical for low-volume production. Additionally, certain materials with poor flow characteristics may not perform well in MIM.
How does MIM compare to traditional machining?
MIM provides greater design flexibility and cost efficiency for high-volume production compared to traditional machining. It eliminates the need for extensive secondary operations and reduces material waste. However, machining may still be preferred for low-volume production or parts requiring extremely tight tolerances.
What role do MIM vendors play in the design process?
MIM vendors provide critical expertise during the design phase. They help optimize part geometry, material selection, and mold design to ensure manufacturability. Their insights into the MIM process help identify potential challenges early, saving time and resources. Collaboration with vendors enhances the overall success of the project.
Is MIM an environmentally friendly manufacturing method?
MIM promotes sustainability by minimizing material waste. Excess feedstock can often be reused, reducing environmental impact. Additionally, the process supports the use of recyclable materials. Designers who prioritize eco-friendly practices can leverage MIM to align with industry trends and environmental standards.