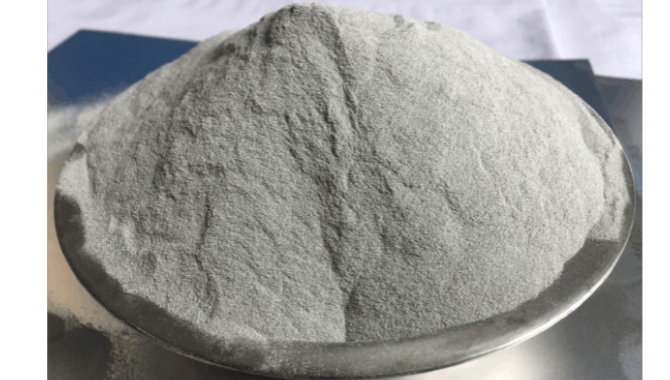
Metal Powder
Can metal be injection molded? Absolutely, it can, thanks to a process known as Metal Injection Molding (MIM). This advanced method combines fine metal powders with a binder to create detailed and precise metal components. MIM is widely utilized in industries like aerospace, medical devices, and automotive manufacturing, where high-quality parts are essential. Its capability to produce complex geometries with exceptional precision makes it an ideal solution for manufacturing strong and dependable metal products.
Key Takeaways
- Metal Injection Molding (MIM) combines fine metal powders with a binder to create precise and complex metal components, making it ideal for industries like aerospace and medical devices.
- MIM allows for the production of intricate geometries and high-density parts, achieving up to 98% of the density of wrought metals, which enhances strength and durability.
- The MIM process involves key steps: material preparation, injection molding, binder removal, and sintering, each critical for ensuring the final product meets quality standards.
- While MIM is cost-effective for high-volume production, it has limitations such as size constraints and the need for precise mold design to account for shrinkage during sintering.
- Alternatives to MIM, like ColdMetalFusion and Freeform Injection Molding, offer unique benefits such as design flexibility and reduced mold costs, catering to different manufacturing needs.
- Choosing the right manufacturing method depends on factors like production volume, part complexity, and budget, so evaluate your project requirements carefully.
Can metal be injection molded through Metal Injection Molding (MIM)?
What is Metal Injection Molding?
Metal Injection Molding (MIM) is a manufacturing process that combines the precision of plastic injection molding with the strength of metal injection molding.
This process allows you to produce intricate and complex metal parts that would be difficult or expensive to create using traditional methods. MIM is especially useful for applications requiring small, detailed components with tight tolerances. Industries like aerospace, medical devices, and automotive manufacturing rely on MIM to produce high-quality parts efficiently.
Materials used in MIM
The materials used in Metal Injection Molding play a crucial role in determining the final product’s properties. You can use a wide range of metals in this process, depending on the application and performance requirements. Common materials include:
- Stainless Steel: Ideal for parts requiring corrosion resistance and strength.
- Titanium: Perfect for lightweight components with excellent strength-to-weight ratios.
- Copper: Suitable for parts needing high thermal or electrical conductivity.
- Nickel Alloys: Great for applications requiring heat resistance and durability.
- Low-Alloy Steels: Used for components that need wear resistance and toughness.
These materials are typically available in powder form, which ensures uniformity and consistency during the molding process. The choice of material depends on the specific needs of your project, such as mechanical properties, environmental conditions, and cost considerations.
By understanding the materials and the MIM process, you can see how metal can indeed be injection molded to create precise and durable components. This innovative technique opens up possibilities for producing parts that meet the demands of modern industries.
How does the Metal Injection Molding (MIM) process work?
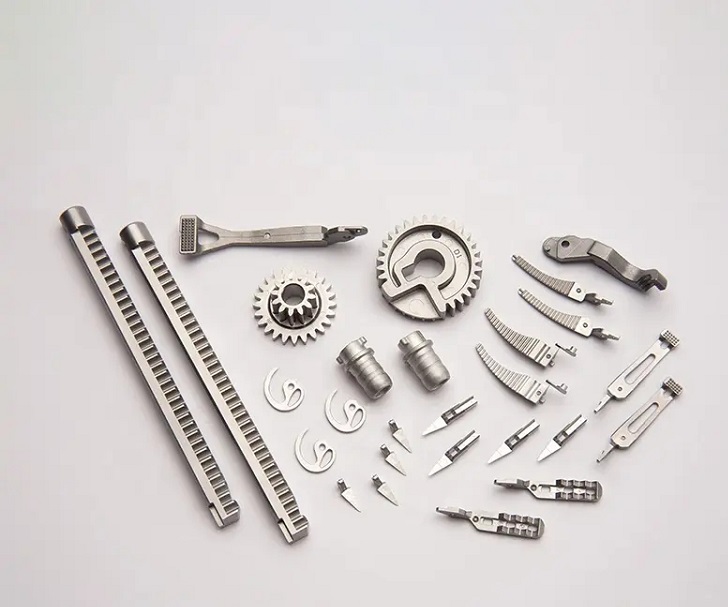
Metal injection molding parts
Metal Injection Molding (MIM) involves several precise steps to transform metal powders into high-quality components. Each stage plays a critical role in ensuring the final product meets your expectations for strength, precision, and durability. Let’s break down the process.
Material preparation
The first step in MIM is preparing the feedstock. You mix fine metal powders with a thermoplastic binder to create a uniform blend. The binder acts as a temporary holding agent, allowing the metal powder to flow during molding. This mixture is then granulated into small pellets, making it easier to handle and feed into the injection molding machine.
The quality of the feedstock directly impacts the final product. Consistency in the metal powder’s particle size and the binder’s composition ensures smooth processing and reliable results. By carefully controlling this step, you set the foundation for producing parts with excellent mechanical properties.
Injection molding
Once the feedstock is ready, you inject it into a mold using an injection molding machine. The machine heats the feedstock until it becomes pliable, then forces it into a mold cavity shaped like the desired part. After cooling, the molded part, known as a “green part,” solidifies and takes on the shape of the mold.
This stage allows you to create intricate geometries and complex designs that would be challenging with traditional manufacturing methods. The precision of the mold ensures that the green part closely resembles the final product, minimizing the need for additional machining or finishing.
Binder removal
After molding, the next step is removing the binder from the green part. This process, called debinding, eliminates the thermoplastic material while leaving the metal powder intact. You can achieve this through chemical, thermal, or solvent-based methods, depending on the binder used.
Debinding is a delicate process. Removing the binder too quickly can damage the part, while incomplete removal can affect the sintering stage. Proper debinding ensures the part remains intact and ready for the next step in the MIM process.
By following these steps, you can see how MIM transforms raw materials into precise and durable components. This process answers the question, “Can metal be injection molded?” with a resounding yes, showcasing its ability to produce high-quality metal parts efficiently.
Sintering
Sintering is the final and most critical step in the Metal Injection Molding (MIM) process. During this stage, you heat the debound part to a temperature just below the metal’s melting point. This high-temperature treatment causes the metal particles to bond together, resulting in a dense and solid structure.
The sintering process enhances the mechanical properties of the part. It increases its strength, hardness, and durability while reducing porosity.
Sintering typically occurs in a controlled atmosphere to prevent oxidation or contamination. For example, you might use an inert gas like argon or a vacuum environment to maintain the metal’s purity. The heating rate, temperature, and duration are carefully monitored to achieve optimal results. These factors depend on the type of metal used and the desired properties of the finished part.
This step transforms the fragile “brown part” into a robust and functional metal component. The sintered part often achieves up to 98% of the density of wrought metal, making it comparable in strength and performance. After sintering, you may perform additional finishing processes, such as machining or surface treatments, to meet specific application requirements.
By understanding the sintering process, you can see how Metal Injection Molding answers the question, “Can metal be injection molded?” This step ensures that the final product meets the high standards of quality and precision demanded by industries like aerospace, medical devices, and automotive manufacturing.
What are the advantages and limitations of MIM?
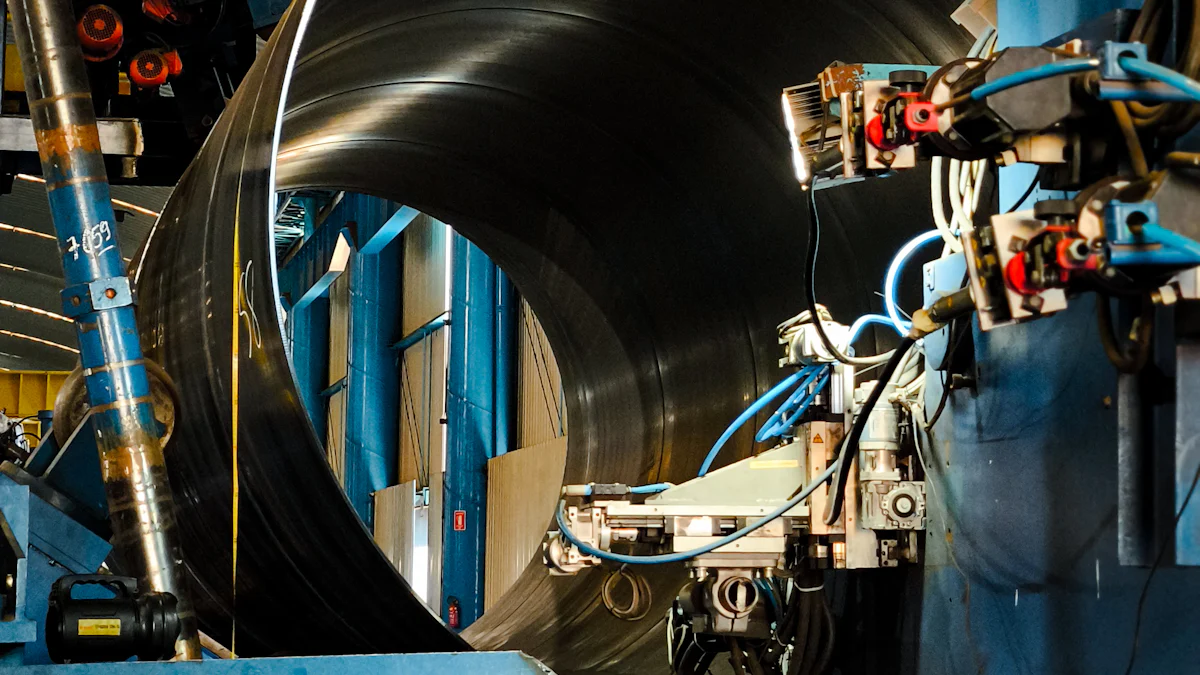
Metal Injection Molding (MIM) offers unique benefits and some challenges. Understanding these aspects helps you decide if this process suits your manufacturing needs.
Advantages of MIM
MIM provides several advantages that make it a preferred choice for producing metal parts:
MIM is ideal for high-volume production. Once you create the mold, you can produce thousands of identical parts efficiently, saving time and resources. Advantages of powder metallurgy often proves more economical than machining or casting.
MIM allows you to create intricate shapes and detailed designs. Traditional methods often struggle with such complexity, but MIM excels in producing parts with tight tolerances and fine features.
-
Material Efficiency
This process minimizes material waste. The use of metal powders ensures that most of the raw material becomes part of the final product, reducing costs and environmental impact. -
High Strength and Density
MIM parts achieve up to 98% of the density of wrought metals. This results in components with excellent mechanical properties, making them strong and durable for demanding applications. -
Scalability
MIM is ideal for high-volume production. Once you create the mold, you can produce thousands of identical parts efficiently, saving time and resources. -
Versatility in Materials
You can choose from a wide range of metals, including stainless steel, titanium, and nickel alloys. This flexibility allows you to tailor the material properties to meet specific requirements. -
Cost-Effectiveness
For complex parts, MIM often proves more economical than machining or casting. The reduced need for secondary operations further lowers production costs.
Limitations of MIM
While MIM offers many benefits, it also has some limitations you should consider:
MIM works best for small to medium-sized parts. Large components may face challenges due to shrinkage during sintering, which can affect dimensional accuracy.
MIM works best for small to medium-sized parts. Large components may face challenges due to shrinkage during sintering, which can affect dimensional accuracy.
-
Initial Investment
The upfront cost of creating molds and preparing feedstock can be high. For low-volume production, this may not be cost-effective. -
Shrinkage and Tolerances
Parts shrink during sintering, which requires precise mold design to compensate. Achieving tight tolerances for certain applications may demand additional finishing steps. -
Binder Removal Challenges
The debinding process must be carefully controlled. Improper binder removal can lead to defects or compromised mechanical properties in the final product. -
Limited Material Options for Some Applications
Although MIM supports various metals, not all materials are suitable. High-melting-point metals or those with specific properties may require alternative manufacturing methods.
By weighing these advantages and limitations, you can determine whether MIM aligns with your project goals. The process answers the question, “Can metal be injection molded?” by offering a reliable way to produce high-quality metal parts, provided the application fits within its capabilities.
Are there alternative methods to Metal Injection Molding (MIM)?
While Metal Injection Molding (MIM) is a powerful technique for producing complex metal parts, you might explore other methods depending on your project needs. These alternatives offer unique advantages and can sometimes address the limitations of MIM. Let’s take a closer look at three popular options.
ColdMetalFusion
ColdMetalFusion combines 3D printing with traditional sintering techniques to create metal parts. This method uses a powder-based approach, where you print the desired shape layer by layer. After printing, the part undergoes sintering to achieve its final density and strength.
Why consider ColdMetalFusion?
- Design Flexibility: You can create highly intricate designs without the need for molds.
- Cost Efficiency for Prototypes: This method works well for low-volume production or prototyping, as it eliminates the upfront cost of mold creation.
- Material Versatility: ColdMetalFusion supports a wide range of metals, including stainless steel and titanium.
However, this method may not be ideal for high-volume production due to slower processing times compared to MIM. If you prioritize customization and precision over speed, ColdMetalFusion could be a great choice.
Freeform Injection Molding
Freeform Injection Molding (FIM) is another innovative alternative. This process uses a flexible mold that adapts to the shape of the part, allowing you to produce complex geometries without the need for rigid molds. The material is injected into the mold, and once solidified, the mold is removed.
What makes Freeform Injection Molding unique?
- Reduced Mold Costs: Flexible molds are less expensive to produce than traditional rigid molds.
- Quick Iterations: You can easily modify the mold design, making it suitable for rapid prototyping.
- Complex Shapes: FIM excels at creating parts with intricate details and undercuts.
Despite its benefits, FIM may not achieve the same level of precision or strength as MIM. It works best for applications where speed and flexibility outweigh the need for extreme durability.
Additive Manufacturing (3D Printing)
Additive manufacturing, commonly known as 3D printing, has revolutionized how you can create metal parts. This method builds parts layer by layer using metal powders or filaments. Technologies like Direct Metal Laser Sintering (DMLS) and Electron Beam Melting (EBM) fall under this category.
Why choose additive manufacturing?
- No Tooling Required: You can skip the mold-making process entirely, saving time and money.
- Customization: Each part can have a unique design, making it ideal for one-off or highly specialized components.
- Short Lead Times: You can produce parts quickly, especially for small batches or prototypes.
However, additive manufacturing often struggles with scalability. Producing large quantities of parts can become time-consuming and costly. Additionally, the surface finish may require post-processing to meet specific quality standards.
Pro Tip: When deciding between these methods, consider factors like production volume, part complexity, and budget. Each technique has strengths that cater to different manufacturing needs.
By exploring these alternatives, you expand your options for creating high-quality metal parts. Whether you choose ColdMetalFusion, Freeform Injection Molding, or additive manufacturing, understanding their capabilities helps you select the best method for your project.
Metal can be injection molded through the Metal Injection Molding (MIM) process. This method excels at producing complex and high-precision parts, making it a valuable solution for industries requiring intricate designs.
FAQ
What types of metals can you use in Metal Injection Molding (MIM)?
You can use a variety of metals in MIM, depending on the application. Common options include stainless steel, titanium, copper, nickel alloys, and low-alloy steels. Each metal offers unique properties. For example, stainless steel provides corrosion resistance, while titanium delivers a high strength-to-weight ratio.
How small can MIM parts be?
MIM excels at producing small and intricate parts. You can create components as small as a few millimeters in size. This makes MIM ideal for industries like medical devices and electronics, where precision and miniaturization are critical.
Is MIM suitable for high-volume production?
Yes, MIM works well for high-volume production. Once you create the mold, you can produce thousands of identical parts efficiently. This scalability makes MIM a cost-effective solution for manufacturing large quantities of complex components.
Can MIM parts match the strength of traditionally manufactured metal parts?
MIM parts achieve up to 98% of the density of wrought metals. This high density ensures excellent mechanical properties, including strength and durability. In many cases, MIM parts perform just as well as those made through traditional methods like machining or casting.
What industries benefit the most from MIM?
Industries that require complex, high-precision metal parts benefit the most from MIM. These include aerospace, automotive, medical devices, electronics, and consumer goods. MIM’s ability to produce intricate designs with tight tolerances makes it a valuable manufacturing method for these sectors.
How does MIM compare to 3D printing for metal parts?
MIM and 3D printing both offer unique advantages. MIM is better for high-volume production and parts requiring high density and strength. 3D printing excels at creating prototypes or custom designs without the need for molds. Your choice depends on factors like production volume, part complexity, and material requirements.
Are there size limitations for MIM parts?
MIM works best for small to medium-sized parts. Large components may face challenges due to shrinkage during sintering, which can affect dimensional accuracy. If your project involves larger parts, you might need to explore alternative manufacturing methods.
What is the typical lead time for MIM production?
The lead time for MIM production depends on factors like mold creation and production volume. Creating the mold usually takes several weeks. Once the mold is ready, you can produce parts quickly. For high-volume orders, MIM offers significant time savings compared to traditional methods.
Can you use MIM for prototyping?
MIM is not the most cost-effective option for prototyping due to the upfront cost of mold creation. However, if your prototype requires the same material properties and precision as the final product, MIM can be a viable choice. For faster and cheaper prototyping, consider alternatives like 3D printing.
What post-processing steps are needed for MIM parts?
MIM parts often require minimal post-processing. After sintering, you may need to perform finishing steps like machining, polishing, or surface treatments to meet specific application requirements. These steps enhance the part’s appearance, functionality, or durability.