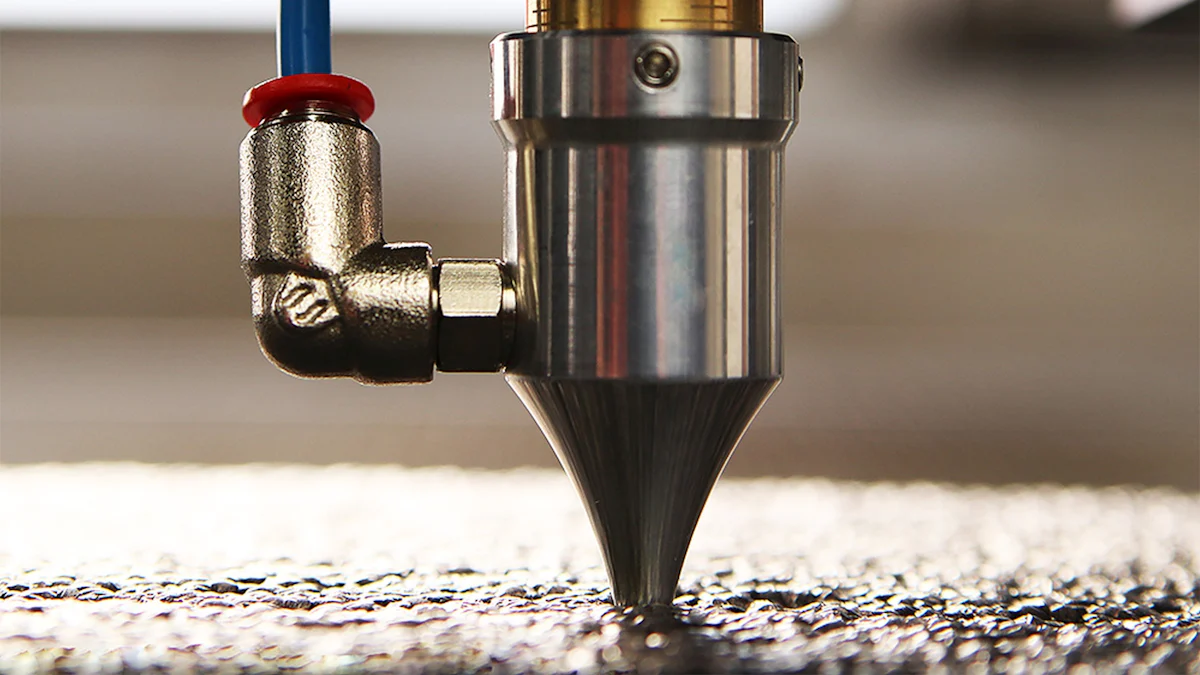
Understanding the differences between sintered steel and stainless steel is crucial for making informed decisions in various industries. Sintered steel, with its unique manufacturing process, offers flexibility in design and application. It has seen significant growth, especially in the automotive sector, due to the shift toward lightweight materials. The market size is projected to grow from
15.84billionin2023∗to∗15.84 billion in 2023* to *
16.68 billion in 2024. Meanwhile, stainless steel remains a staple for its corrosion resistance and durability. Knowing when to use each material can greatly impact the efficiency and success of your projects.Key Takeaways
- Sintered steel is ideal for complex designs due to its unique powder metallurgy process, allowing for intricate shapes and precise dimensions.
- Stainless steel offers superior corrosion resistance, making it the preferred choice for applications in harsh environments like construction and marine industries.
- The manufacturing process of sintered steel is more material-efficient, reducing waste and potentially lowering costs in large-scale production.
- While sintered steel provides design flexibility, stainless steel is known for its strength and durability, making it suitable for demanding applications.
- Understanding the specific requirements of your project is crucial in choosing between sintered steel and stainless steel to maximize efficiency and performance.
- Investing in sintered steel may involve higher initial costs, but its long-term benefits in design and material efficiency can lead to significant savings.
- Different grades of stainless steel, such as 316L, can be tailored for specific applications, enhancing performance in areas like heat and corrosion resistance.
Properties of Sintered Steel vs Stainless Steel
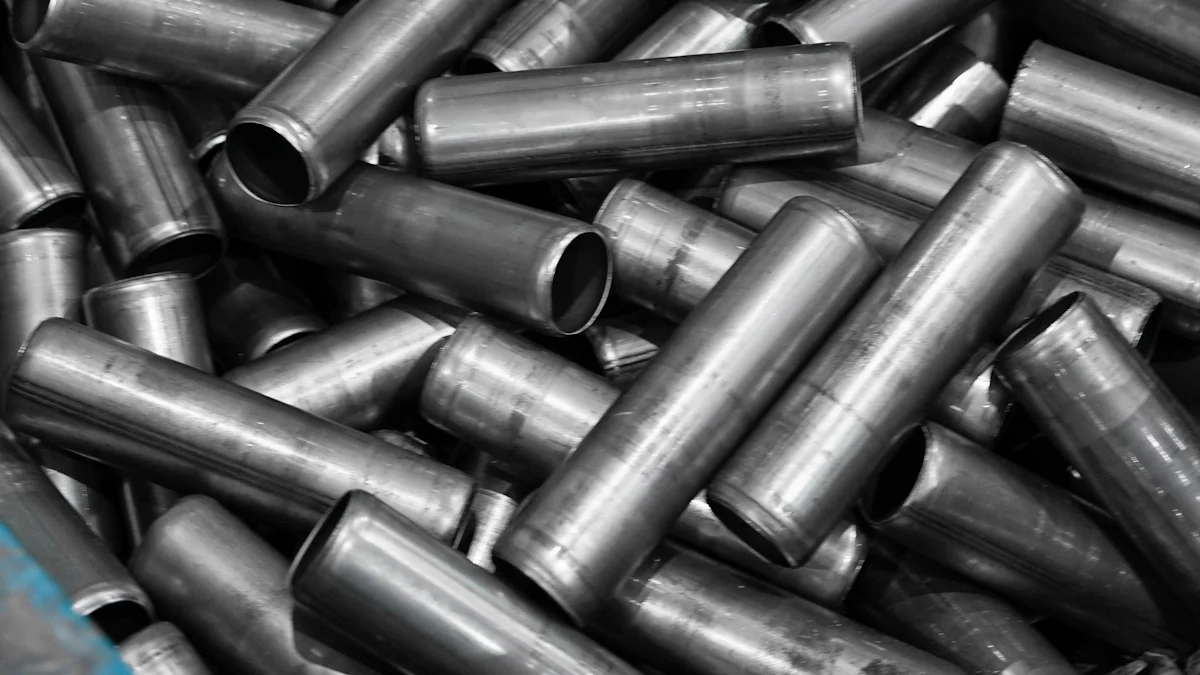
Composition and Structure
When I examine the composition and structure of sintered steel vs stainless steel, I notice distinct differences. Sintered steel results from a process called powder metallurgy. This involves compacting powdered metal and heating it below its melting point. The particles bond together, forming a solid piece. This method allows for intricate designs and shapes, making it ideal for complex components like gears and splines.
In contrast, stainless steel is an alloy primarily composed of iron, chromium, and nickel. The addition of chromium provides its renowned corrosion resistance. Manufacturers produce stainless steel through traditional methods like casting and finishing. This results in a uniform and dense structure, which contributes to its strength and durability.
Mechanical and Corrosion Resistance
The mechanical properties and corrosion resistance of sintered steel vs stainless steel also differ significantly. Sintered steel offers flexibility in design but may not match the strength of traditionally manufactured metals. However, high-temperature sintering can enhance its tensile strength and fatigue resistance. This makes it suitable for applications where weight reduction is crucial, such as in the automotive industry.
Stainless steel, on the other hand, excels in environments requiring high corrosion resistance. Its ability to withstand harsh conditions makes it a preferred choice in industries like construction and consumer goods. Different types of stainless steel, such as 316L, offer varying levels of heat and corrosion resistance. This versatility allows it to be used in a wide range of applications, from kitchen appliances to architectural structures.
Manufacturing Processes
Sintered Steel: Powder Metallurgy and Sintering
In my exploration of sintered steel manufacturing, I find the process both fascinating and efficient. The journey begins with powder metallurgy, where manufacturers compact powdered metal into a desired shape. This step allows for precise control over the component’s dimensions and properties. After compaction, the material undergoes sintering. During this phase, the compacted powder heats below its melting point, causing the particles to bond at a molecular level. This process enhances the material’s strength and integrity.
The sintering environment plays a crucial role in determining the final properties of the steel. Factors such as sintering temperature and atmosphere significantly influence the densification and mechanical properties of the finished product. For instance, a higher sintering temperature can improve tensile strength and corrosion resistance. This flexibility makes sintered steel an attractive option for industries requiring intricate designs and close tolerances.
Stainless Steel: Alloying, Casting, and Finishing
Stainless steel manufacturing follows a more traditional route. The process starts with alloying, where iron combines with chromium, nickel, and other elements. This combination gives stainless steel its renowned corrosion resistance and durability. Once the alloy is prepared, it undergoes casting. In this stage, the molten metal pours into molds to form the desired shape. Casting ensures a uniform and dense structure, contributing to the material’s strength.
After casting, the steel undergoes finishing processes. These include annealing, pickling, and polishing, which enhance the material’s surface quality and mechanical properties. The finishing steps ensure that stainless steel meets the high standards required for various applications, from kitchen appliances to architectural structures. The combination of alloying, casting, and finishing results in a versatile material that excels in demanding environments.
Advantages and Disadvantages
Sintered Steel
When I consider the advantages of sintered steel, its flexibility in design stands out. The powder metallurgy process allows for the creation of complex shapes and intricate designs, which is particularly beneficial in industries like automotive and aerospace. This capability to produce components with precise dimensions and close tolerances can lead to significant cost savings in manufacturing.
-
Design Flexibility: Sintered steel offers the ability to create complex geometries that traditional manufacturing methods might struggle with. This makes it ideal for producing parts like gears and splines.
-
Material Efficiency: The process minimizes waste, as it uses only the necessary amount of material to create the part. This efficiency can lead to cost savings, especially in large-scale production.
-
Enhanced Properties: By adjusting the sintering conditions, manufacturers can enhance properties such as tensile strength and corrosion resistance. This adaptability makes sintered steel suitable for various applications.
However, sintered steel also has its disadvantages. The initial capital cost for setting up powder metallurgy can be high, which might deter smaller manufacturers. Additionally, while sintered steel can achieve good mechanical properties, it may not always match the strength and durability of traditionally manufactured metals. This limitation can restrict its use in applications requiring extreme strength or wear resistance.
Stainless Steel
Stainless steel’s advantages lie in its renowned corrosion resistance and durability. Its composition, primarily of iron, chromium, and nickel, provides excellent resistance to rust and staining, making it a preferred choice in environments exposed to moisture and chemicals.
-
Corrosion Resistance: Stainless steel excels in resisting corrosion, which makes it ideal for use in harsh environments. This property ensures longevity and reduces maintenance costs.
-
Strength and Durability: The uniform and dense structure of stainless steel contributes to its high mechanical strength. This makes it suitable for demanding applications, such as in construction and heavy machinery.
-
Versatility: With various grades available, stainless steel can be tailored to meet specific requirements. For instance, 316L stainless steel is preferred for high-pressure applications due to its enhanced strength and durability.
Despite these advantages, stainless steel has its drawbacks. The cost of raw materials and the energy-intensive manufacturing process can make it more expensive than other materials. Additionally, while it offers excellent corrosion resistance, it may not provide the same level of design flexibility as sintered steel.
Applications in Various Industries
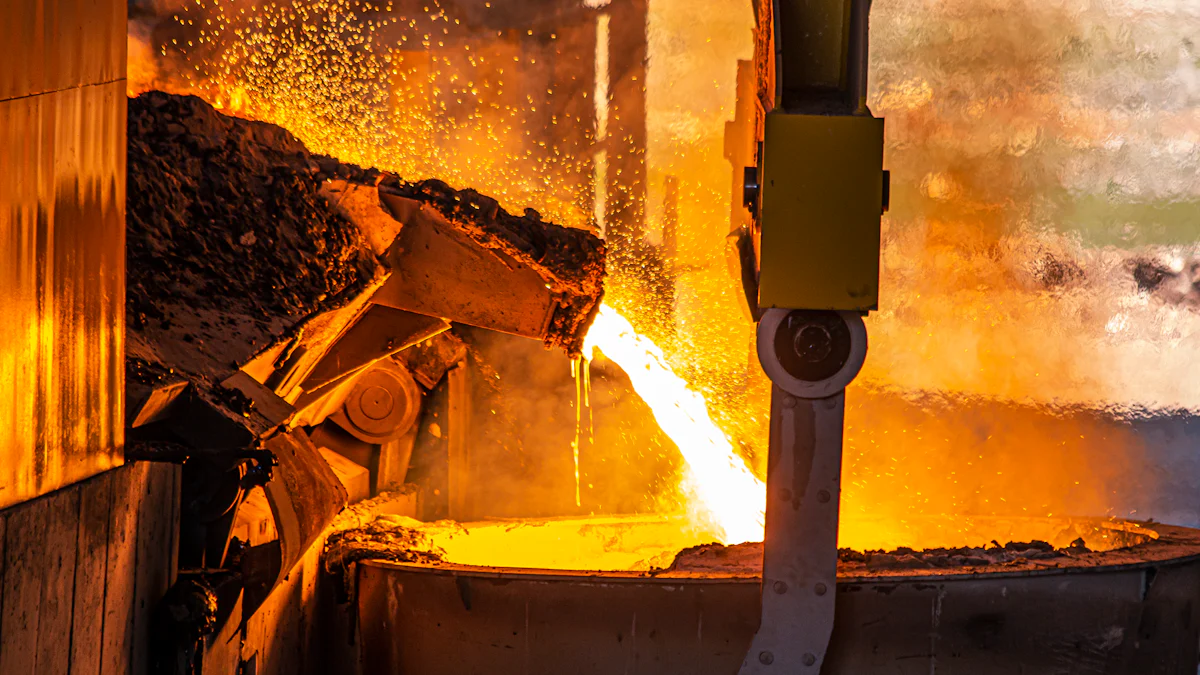
Automotive Industry
In the automotive industry, I see sintered steel playing a pivotal role. Its ability to form complex shapes with precise dimensional control makes it ideal for manufacturing components like gears and bearings. These parts require high strength and wear resistance, which sintered steel provides efficiently. The automotive sector benefits from the material’s lightweight nature, contributing to fuel efficiency and reduced emissions. Sintered stainless steel also finds applications in exhaust systems and fuel injectors, where corrosion resistance is crucial.
Construction and Architecture
When I look at construction and architecture, stainless steel stands out for its durability and aesthetic appeal. Its corrosion resistance ensures longevity in structures exposed to the elements. Stainless steel is often used in building facades, railings, and structural components. In contrast, sintered steel offers advantages in specific applications like fasteners and connectors, where its strength and dimensional stability are beneficial. The ability to incorporate various alloying elements allows for tailored properties, making sintered steel a versatile choice in construction projects.
Consumer Goods
In the realm of consumer goods, both sintered steel and stainless steel have their niches. Stainless steel’s non-porous surface and resistance to bacterial growth make it a preferred material for kitchen appliances and cookware. Its sleek appearance adds a modern touch to household items. On the other hand, sintered steel’s cost-effectiveness and material efficiency make it suitable for producing small, intricate components in electronics and home appliances. The flexibility in design and high material utilization of sintered steel provide manufacturers with the ability to innovate and create unique products.
In comparing sintered steel vs stainless steel, I find distinct advantages and limitations for each. Sintered steel excels in design flexibility and material efficiency, making it ideal for complex components in industries like automotive and aerospace. However, its initial setup costs can be high. Stainless steel, particularly grades like 316L, offers unmatched corrosion resistance and durability, suitable for harsh environments such as marine or chemical processing. For applications requiring intricate designs, sintered steel is preferable. In contrast, stainless steel is the go-to choice for environments demanding high corrosion resistance and strength.
FAQ
What are the advantages of using sintered stainless steel for parts?
Sintered stainless steel offers several advantages. It provides material and labor efficiency, which can lead to cost savings. The process allows for flexibility in design, enabling the creation of complex shapes with close tolerances. This results in components with desirable material properties and often reduces the need for multiple assemblies.
How does the corrosion resistance of sintered steel compare to stainless steel?
Stainless steel generally excels in corrosion resistance due to its chromium content. Sintered steel, while offering some corrosion resistance, may not match the levels provided by stainless steel, especially in environments with high chloride concentrations. However, high-temperature sintering can enhance the corrosion resistance of sintered steel.
Can sintered steel match the strength of traditionally manufactured metals?
Sintered steel can achieve good mechanical properties, but it may not always match the strength of traditionally manufactured metals. High-temperature sintering can improve tensile strength and fatigue resistance, making it suitable for applications where weight reduction is crucial.
What industries benefit most from using sintered steel?
Industries like automotive and aerospace benefit significantly from sintered steel. Its ability to form complex shapes with precise dimensional control makes it ideal for manufacturing components like gears and bearings. The material’s lightweight nature contributes to fuel efficiency and reduced emissions in the automotive sector.
Why is stainless steel preferred in construction and architecture?
Stainless steel is preferred in construction and architecture due to its durability and aesthetic appeal. Its corrosion resistance ensures longevity in structures exposed to the elements. Stainless steel is often used in building facades, railings, and structural components.
How does the cost of sintered steel compare to stainless steel?
The initial capital cost for setting up powder metallurgy for sintered steel can be high, which might deter smaller manufacturers. Stainless steel, on the other hand, can be more expensive due to the cost of raw materials and the energy-intensive manufacturing process.
What are the environmental impacts of using sintered steel?
Sintered steel manufacturing minimizes waste by using only the necessary amount of material to create the part. This efficiency can lead to cost savings and reduced environmental impact, especially in large-scale production.
Are there specific grades of stainless steel that offer better performance?
Yes, different grades of stainless steel offer varying levels of performance. For instance, 316L stainless steel is preferred for high-pressure applications due to its enhanced strength and durability. This versatility allows stainless steel to be tailored to meet specific requirements.
Can sintered steel be used in consumer goods?
Yes, sintered steel’s cost-effectiveness and material efficiency make it suitable for producing small, intricate components in electronics and home appliances. Its flexibility in design and high material utilization provide manufacturers with the ability to innovate and create unique products.
What factors influence the choice between sintered steel and stainless steel?
The choice between sintered steel and stainless steel depends on the specific application requirements. Sintered steel excels in design flexibility and material efficiency, making it ideal for complex components. Stainless steel offers unmatched corrosion resistance and durability, suitable for harsh environments.