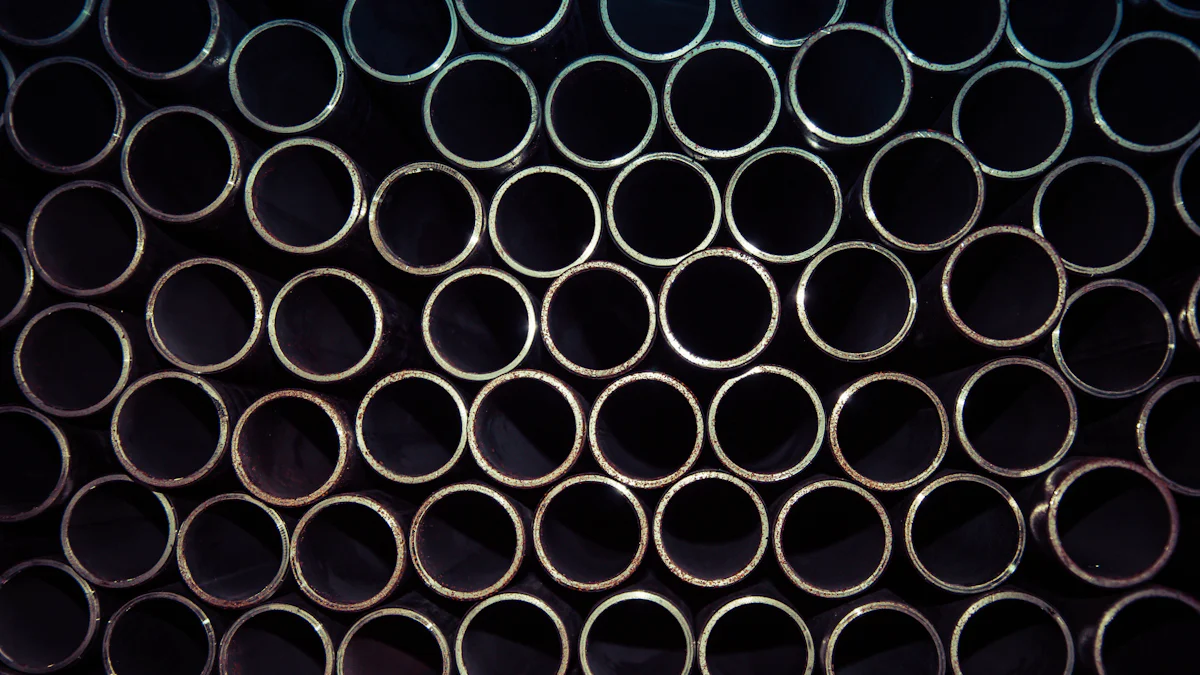
The difference between SS316 and SS316L primarily lies in their carbon content. SS316 contains a maximum of 0.08% carbon, while SS316L, the low-carbon variant, has a maximum of 0.03%. This reduction in carbon content significantly impacts the material’s properties. For instance, SS316L offers enhanced corrosion resistance, making it ideal for environments where welding is necessary. The lower carbon content minimizes the risk of carbide precipitation during welding, which can lead to corrosion. Thus, SS316L is often preferred in applications requiring superior weldability and corrosion resistance.
Key Takeaways
- SS316L has a lower carbon content (0.03%) compared to SS316 (0.08%), enhancing its corrosion resistance and weldability.
- The reduced carbon in SS316L minimizes the risk of carbide precipitation during welding, making it ideal for applications requiring extensive welding.
- SS316 is preferred for applications where strength is critical, while SS316L is better suited for environments with high corrosion risks, such as pharmaceuticals and food processing.
- Both SS316 and SS316L contain molybdenum, but SS316L often has slightly higher levels, improving its resistance to pitting and chemical corrosion.
- While SS316L may have a higher initial cost, its long-term durability and reduced maintenance needs can lead to significant cost savings over time.
- When choosing between SS316 and SS316L, consider the specific application requirements, including environmental conditions and welding needs.
Composition Differences
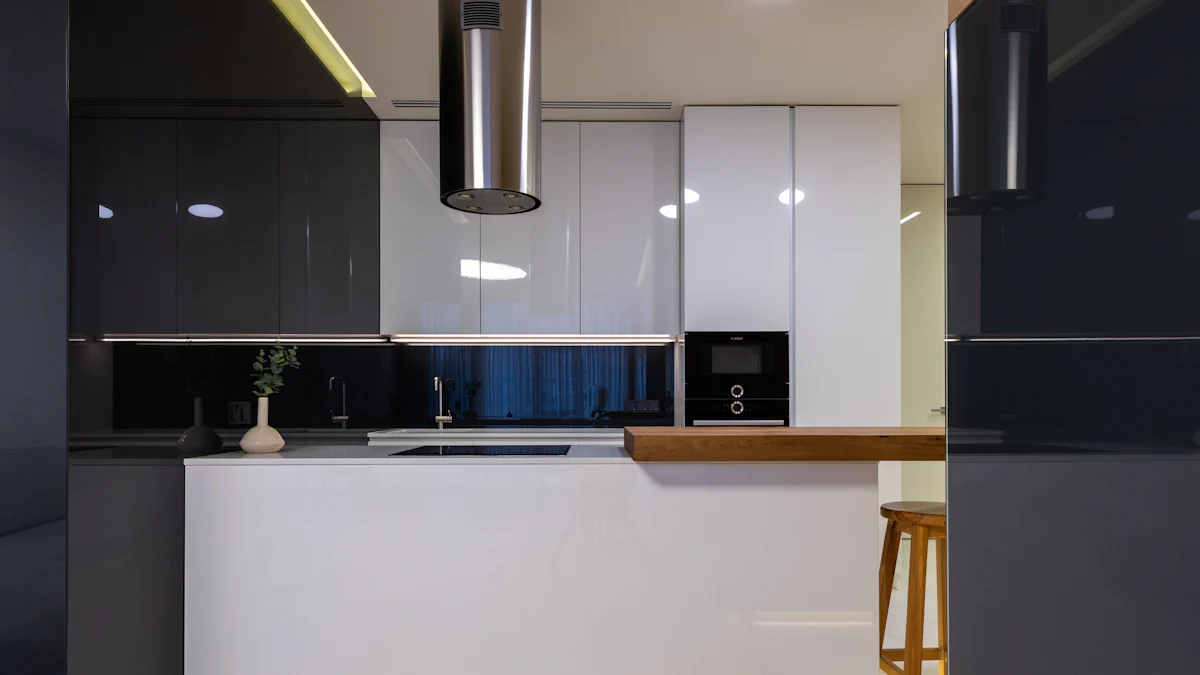
Chemical Composition of SS316
Carbon Content
In SS316, the carbon content reaches a maximum of 0.08%. This level of carbon contributes to the material’s strength and hardness. However, it also poses a risk during welding, as higher carbon levels can lead to carbide precipitation. This phenomenon can reduce corrosion resistance, especially in environments where chloride exposure is common.
Other Alloying Elements
SS316 is an austenitic chromium-nickel stainless steel. It contains molybdenum, which enhances its general corrosion resistance. This element significantly improves the steel’s ability to resist pitting in chloride ion solutions. The presence of nickel and chromium further strengthens its resistance to acids and chlorides, making it suitable for marine environments and high-temperature applications.
Chemical Composition of SS316L
Reduced Carbon Content
The primary difference between SS316 and SS316L lies in the carbon content. SS316L features a reduced carbon content, with a maximum of 0.03%. This lower carbon level minimizes the risk of carbide precipitation during welding. As a result, SS316L maintains its corrosion resistance even after welding, making it ideal for applications requiring extensive welding.
Impact on Alloying Elements
Despite the lower carbon content, SS316L retains similar levels of chromium, nickel, and molybdenum as SS316. These elements ensure that SS316L offers excellent strength, high ductility, and good thermal properties. The molybdenum content, slightly higher in SS316L, enhances its resistance to pitting and chemical corrosion. This makes SS316L suitable for food-safe applications, medical instruments, and environments where superior corrosion resistance is essential.
Properties Comparison
Corrosion Resistance
Performance in Various Environments
I have observed that SS316L exhibits superior corrosion resistance compared to SS316. This advantage becomes particularly evident in environments rich in chlorides, such as marine settings. The lower carbon content in SS316L reduces the risk of intergranular corrosion, which often occurs in high-temperature applications. This makes SS316L a preferred choice for industries that demand high corrosion resistance, such as chemical processing and pharmaceuticals.
Impact of Carbon Content
The difference between SS316 and SS316L primarily lies in their carbon content. SS316L’s reduced carbon level enhances its ability to resist corrosion. During welding, SS316L maintains its structural integrity without requiring post-weld heat treatment. This characteristic minimizes the risk of carbide precipitation, which can compromise corrosion resistance. Therefore, SS316L is often chosen for applications where welding is frequent and corrosion resistance is critical.
Strength and Durability
Mechanical Properties
Both SS316 and SS316L offer excellent mechanical properties, but I find that SS316 provides slightly higher strength due to its higher carbon content. This makes SS316 suitable for applications where strength is a priority. However, SS316L compensates for its lower carbon content with enhanced ductility and toughness, making it versatile for various industrial uses.
Effect of Carbon Reduction
The reduction in carbon content in SS316L does not significantly impact its overall strength. Instead, it improves the material’s durability by enhancing its resistance to stress-corrosion cracking. This makes SS316L an ideal choice for environments where both strength and corrosion resistance are required, such as in the construction of pressure vessels and piping systems.
Weldability
Ease of Welding
From my experience, SS316L offers better weldability than SS316. The lower carbon content in SS316L reduces the risk of carbide precipitation during welding. This allows for easier and more efficient welding processes without the need for additional heat treatments. As a result, SS316L is often used in industries where welding is a frequent requirement.
Risk of Carbide Precipitation
Carbide precipitation poses a significant risk during the welding of stainless steels. In SS316, the higher carbon content increases this risk, potentially leading to reduced corrosion resistance. However, SS316L’s lower carbon content minimizes this risk, ensuring that the material retains its corrosion-resistant properties even after welding. This makes SS316L a reliable choice for applications involving extensive welding, such as in the fabrication of tanks and vessels.
Applications
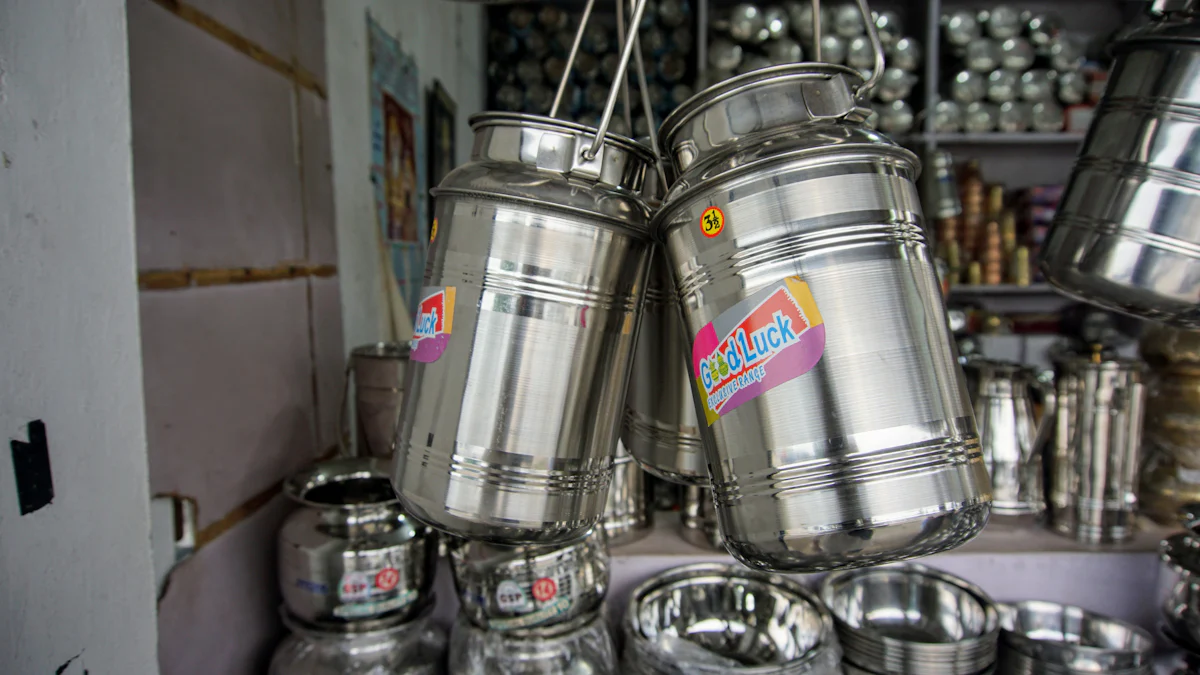
Typical Uses for SS316
Marine Environments
I often recommend SS316 for marine environments due to its excellent resistance to chloride attack. This stainless steel grade withstands the harsh conditions of saltwater, making it ideal for constructing marine equipment and structures. Its ability to resist corrosion from chlorides ensures longevity and reliability in maritime applications. Whether it’s for shipbuilding or offshore platforms, SS316 proves to be a robust choice.
Chemical Processing
In chemical processing, SS316 stands out for its durability and resistance to various acids. The presence of molybdenum enhances its ability to withstand corrosive substances, making it suitable for manufacturing chemical processing equipment. I find that SS316 is often used in reactors, tanks, and piping systems where exposure to harsh chemicals is frequent. Its strength and corrosion resistance make it a preferred material in this industry.
Typical Uses for SS316L
Pharmaceutical Equipment
For pharmaceutical applications, SS316L is my go-to choice. Its low carbon content minimizes the risk of carbide precipitation, ensuring that the material maintains its integrity during welding. This property is crucial in pharmaceutical equipment, where hygiene and sterility are paramount. SS316L‘s resistance to corrosion and ability to withstand sterilization processes make it ideal for manufacturing medical instruments and pharmaceutical machinery.
Food Processing
In the food processing industry, SS316L excels due to its superior corrosion resistance and biocompatibility. The reduced carbon content prevents contamination, making it safe for food contact. I often see SS316L used in food processing machinery, where it ensures cleanliness and durability. Its ability to resist corrosion from food acids and cleaning agents makes it a reliable choice for maintaining hygiene standards.
Cost Considerations
Price Differences
Material Costs
When I compare the costs of SS316 and SS316L, I find that the price difference is generally marginal. SS316L tends to be slightly more expensive due to its lower carbon content and the additional processing steps required to achieve this. The manufacturing process for SS316L involves more stringent controls to ensure the reduced carbon levels, which can contribute to its higher cost. However, this slight increase in price is often justified by the enhanced corrosion resistance that SS316L offers.
Long-term Cost Implications
In my experience, the long-term cost implications of choosing between SS316 and SS316L can be significant. While SS316L may have a higher initial cost, its superior corrosion resistance can lead to cost savings over time. In environments where corrosion is a major concern, the durability of SS316L can reduce maintenance and replacement costs. This makes it a cost-effective choice for applications that demand longevity and reliability.
Factors Influencing Material Choice
Application Requirements
The choice between SS316 and SS316L often depends on the specific requirements of the application. For projects involving extensive welding, I recommend SS316L due to its lower carbon content, which minimizes the risk of carbide precipitation. This characteristic makes SS316L ideal for applications where post-weld heat treatment is not feasible. On the other hand, if the application prioritizes strength over weldability, SS316 might be more suitable.
Budget Constraints
Budget constraints also play a crucial role in material selection. While SS316L offers enhanced properties, its slightly higher cost might not always align with budget limitations. In such cases, I advise evaluating the long-term benefits of SS316L against the immediate cost savings of SS316. For projects with tight budgets, SS316 can be a viable option if the application does not involve harsh corrosive environments or extensive welding.
The difference between SS316 and SS316L primarily revolves around their carbon content, which significantly influences their properties and applications. SS316, with its higher carbon content, offers increased strength and general corrosion resistance, making it suitable for environments where chloride attack is prevalent. On the other hand, SS316L, with its lower carbon content, excels in welding applications and provides superior corrosion resistance, especially in high-chloride and high-temperature environments. This makes SS316L the preferred choice for industries requiring extensive welding and maximum corrosion resistance, such as pharmaceuticals and food processing.
FAQ
What is the difference between SS316 and SS316L?
The primary difference lies in their carbon content. SS316L has a lower carbon content than SS316. This reduction enhances its molding capacity and minimizes the risk of carbide precipitation during welding. As a result, SS316L offers better resistance against corrosive environments and is less prone to intergranular corrosion.
Why is SS316L preferred for welding applications?
I prefer SS316L for welding because its lower carbon content reduces the risk of carbide precipitation. This ensures that the material maintains its corrosion resistance after welding. It eliminates the need for post-weld heat treatment, making it more efficient for projects requiring extensive welding.
How does the molybdenum content affect SS316 and SS316L?
Both SS316 and SS316L contain molybdenum, which enhances their corrosion resistance. However, SS316L often has slightly higher molybdenum content. This increases its ability to resist pitting and chemical corrosion, making it suitable for harsh environments.
Are there any cost differences between SS316 and SS316L?
The cost difference between SS316 and SS316L is generally marginal. SS316L might be slightly more expensive due to its lower carbon content and additional processing requirements. However, its enhanced corrosion resistance can lead to long-term cost savings in maintenance and replacement.
In which industries is SS316 commonly used?
I often see SS316 used in marine environments and chemical processing industries. Its excellent resistance to chloride attack and various acids makes it ideal for constructing marine equipment and chemical processing equipment.
What makes SS316L suitable for pharmaceutical and food processing applications?
SS316L’s low carbon content minimizes the risk of contamination, making it safe for food contact and pharmaceutical use. Its superior corrosion resistance and ability to withstand sterilization processes make it ideal for manufacturing medical instruments and food processing machinery.
Can SS316L be used in high-temperature environments?
Yes, SS316L performs well in high-temperature environments. Its reduced carbon content minimizes the risk of intergranular corrosion, which can occur at elevated temperatures. This makes it suitable for applications requiring both heat resistance and corrosion resistance.
How do I decide between using SS316 and SS316L for my project?
When deciding between SS316 and SS316L, consider the specific requirements of your application. If your project involves extensive welding, I recommend SS316L due to its lower carbon content. For applications prioritizing strength, SS316 might be more suitable. Evaluate the environmental conditions and budget constraints to make an informed choice.
Does SS316L require any special maintenance?
SS316L requires minimal maintenance due to its superior corrosion resistance. Regular cleaning and inspection can help maintain its appearance and performance. In environments with high chloride exposure, additional protective measures might be necessary to ensure longevity.
Is there a significant difference in strength between SS316 and SS316L?
SS316 offers slightly higher strength due to its higher carbon content. However, SS316L compensates with enhanced ductility and toughness. Both materials provide excellent mechanical properties, but the choice depends on the specific strength requirements of your application.