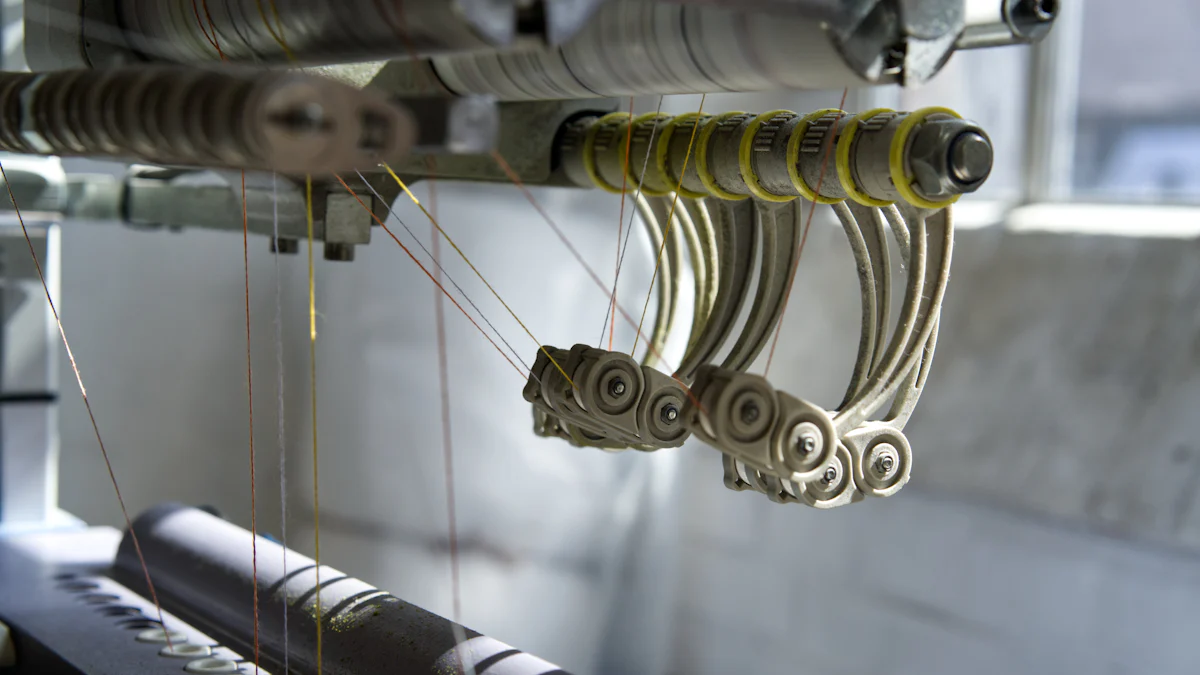
The density of stainless steel represents its mass per unit volume, typically ranging from 7.75 to 8.05 g/cm³. This property is pivotal in material selection across engineering, manufacturing, and design industries. A material’s density directly influences its weight, strength-to-weight ratio, and overall performance. For instance, selecting the right density ensures optimal weight distribution in structural applications or enhances durability in corrosive environments. Understanding this characteristic allows me to make informed decisions that balance functionality, efficiency, and safety in various projects.
Key Takeaways
- Stainless steel density ranges from 7.75 to 8.05 g/cm³, influencing weight, strength, and performance in various applications.
- Accurate density measurement is crucial; use precise weighing and volume determination methods, such as water displacement, to ensure reliable results.
- Higher density often correlates with greater strength, making choosing the right grade for high-stress applications essential.
- Consider environmental conditions when selecting stainless steel; grades like 316 offer enhanced corrosion resistance for harsh settings.
- Density impacts not only the weight of the material but also its performance, especially in dynamic environments where stability is key.
- Understanding the density variations among stainless steel grades helps in selecting the most suitable material for specific project needs.
- A systematic approach to material selection, including defining project goals and consulting standards, minimizes risks and enhances project success.
What Is the Density of Stainless Steel and How Is It Measured?
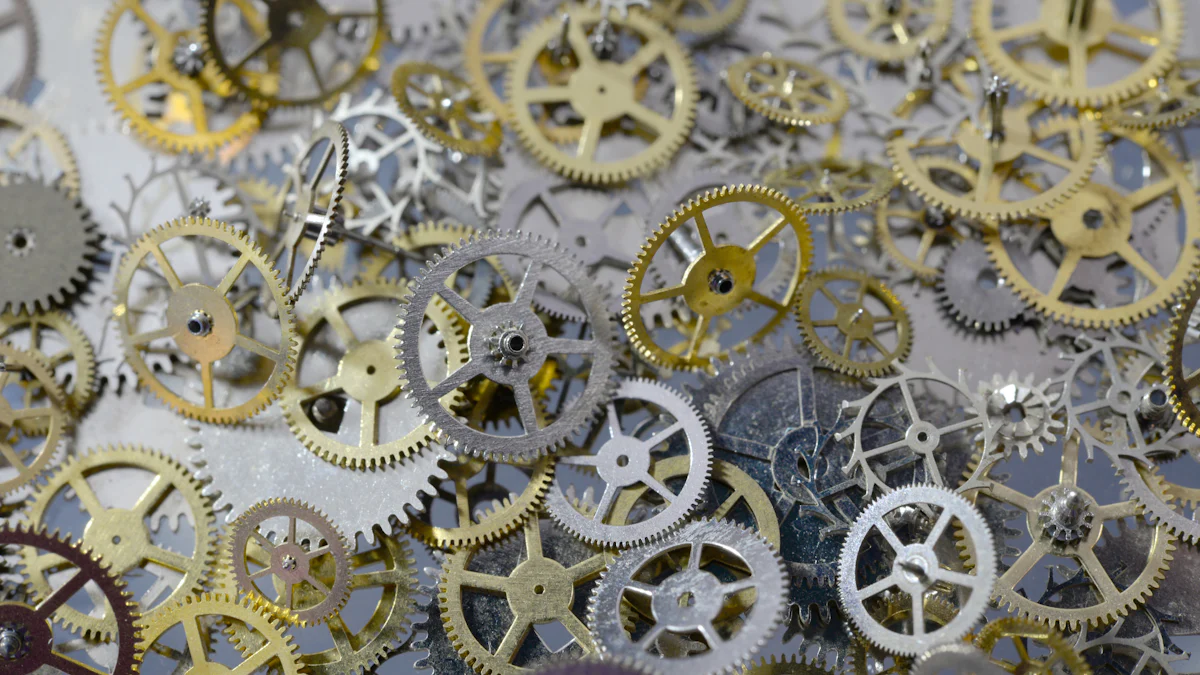
Understanding the density of stainless steel begins with defining what density means and how it is quantified. This knowledge forms the foundation for accurate material selection and ensures optimal performance in various applications.
Definition and Units of Density
Density refers to the mass of a material per unit volume. For stainless steel, this property typically ranges between 7.75 and 8.05 g/cm³. Engineers and designers often use this measurement to calculate weight, assess structural integrity, and predict material behavior under different conditions. The standard unit for density in the metric system is kilograms per cubic meter (kg/m³), but grams per cubic centimeter (g/cm³) is also common in smaller-scale applications.
When I evaluate materials, I rely on these units to compare stainless steel with other metals. For example, aluminum has a much lower density, making it lighter but less durable in certain environments. This comparison highlights why density plays such a critical role in material selection.
Methods for Measuring Stainless Steel Density
Accurate measurement of stainless steel density requires precision and the right tools. I follow a systematic approach to ensure reliable results:
- Weighing the Sample: I use a high-precision balance to measure the mass of the stainless steel sample. Even minor inaccuracies can affect the final calculation.
- Volume Determination: For irregularly shaped samples, I apply the water displacement method. By submerging the sample in water and measuring the displaced volume, I can calculate its density.
- Temperature Control: I maintain a consistent temperature during measurements. Temperature variations can cause expansion or contraction, altering the density value.
“Best practices, such as controlling temperature and using precise equipment, are essential for accurate density measurements.”
These methods ensure that I obtain reliable data, which is crucial for selecting the right material for a project.
Factors Influencing Density Measurements
Several factors can influence the density of stainless steel and the accuracy of its measurement. I always consider these variables to avoid errors:
- Impurities and Inclusions: Non-metallic inclusions or impurities in the alloy can slightly alter the density. For instance, higher levels of carbon or other elements may increase or decrease the overall mass per unit volume.
- Sample Preparation: Proper preparation, including sintering and debinding, ensures uniformity in the sample. Uneven surfaces or voids can skew the results.
- Environmental Conditions: Temperature and humidity can impact both the material and the measuring equipment. I mitigate these effects by conducting tests in controlled environments.
By addressing these factors, I can confidently determine the density of stainless steel and understand its implications for material properties.
How Does the Density of Stainless Steel Impact Material Properties?
Relationship Between Density and Strength
The density of stainless steel directly correlates with its strength. A higher density often indicates a more robust material, capable of withstanding greater stress and load. For example, stainless steel grades like 304 and 316, with densities around 7.93 g/cm³, exhibit excellent tensile strength and durability. I rely on this relationship when selecting materials for high-stress applications, such as structural supports or heavy machinery components.
In contrast, materials with lower densities, such as aluminum or titanium, may lack the same level of strength. While these materials are lighter, they often require additional reinforcement to achieve comparable performance. This trade-off highlights why understanding the density of stainless steel is essential for balancing strength and weight in engineering projects.
Influence of Density on Weight and Performance
The density of stainless steel significantly impacts the weight of a finished product. With an average density of 8.0 g/cm³, stainless steel is heavier than materials like aluminum, which has a density of approximately 2.7 g/cm³. This weight difference plays a critical role in applications where performance depends on weight distribution. For instance, in aerospace or automotive industries, I might opt for lighter materials to improve fuel efficiency. However, in construction or industrial settings, the added weight of stainless steel enhances stability and load-bearing capacity.
I also consider how density affects performance in dynamic environments. Heavier materials like stainless steel provide better vibration damping and resistance to deformation under pressure. This makes it an ideal choice for equipment subjected to repetitive motion or heavy loads. By evaluating these factors, I can ensure that the material aligns with the specific demands of the project.
Role of Density in Durability and Corrosion Resistance
Density influences not only the physical properties of stainless steel but also its durability and resistance to corrosion. Higher-density grades, such as duplex stainless steels, combine strength with enhanced corrosion resistance, making them suitable for harsh environments. For example, I often choose duplex grades with densities ranging from 7.80 to 7.90 g/cm³ for marine or chemical processing applications. These grades resist pitting and cracking, even in highly corrosive conditions.
The alloying elements in stainless steel, such as chromium and nickel, contribute to both its density and its protective oxide layer. This layer prevents rust and extends the material’s lifespan. Lower-density materials, like carbon steel, lack this level of protection, which can lead to faster degradation over time. By prioritizing the density of stainless steel, I ensure long-term durability and reduced maintenance costs for my projects.
“Selecting the right density ensures not only optimal performance but also longevity and reliability in demanding environments.”
Comparing the Density of Stainless Steel Across Grades
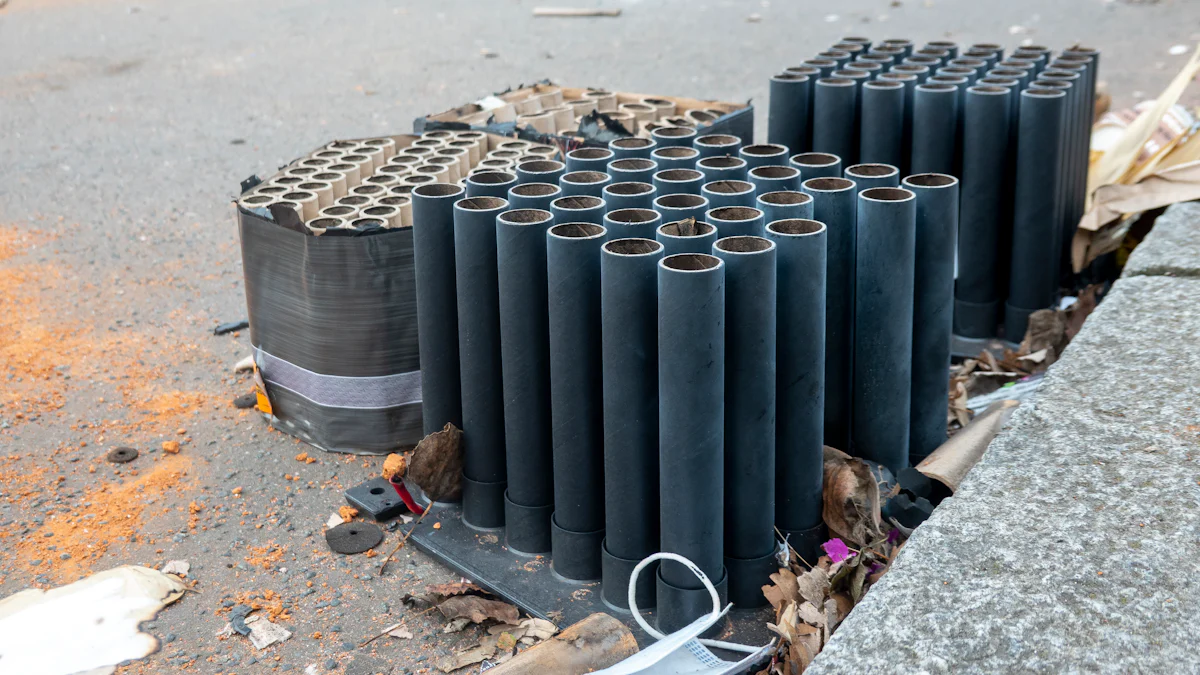
Overview of Stainless Steel Grades
Stainless steel comes in various grades, each tailored for specific applications and environments. I often work with popular grades like 304 and 316, which are widely used due to their versatility and performance. Grade 304, known as the “workhorse” of stainless steel, offers excellent corrosion resistance and is suitable for general-purpose applications. On the other hand, grade 316 contains added molybdenum, enhancing its resistance to pitting and making it ideal for marine or chemical environments.
Other grades, such as duplex stainless steels, combine the best properties of austenitic and ferritic stainless steels. These grades provide higher strength and improved corrosion resistance. Each grade’s unique composition directly influences its density, which plays a critical role in determining its suitability for specific uses.
Density Variations Among Grades
The density of stainless steel varies depending on its grade and alloy composition. For instance, grade 304 has a density of approximately 7.93 g/cm³, while grade 316 is slightly denser at around 7.98 g/cm³. This difference arises from the additional alloying elements, such as molybdenum, in grade 316. Duplex stainless steels, with densities ranging from 7.80 to 7.90 g/cm³, strike a balance between strength and weight.
These variations may seem minor, but they significantly impact material selection. For example, I choose grade 304 for lightweight applications where corrosion resistance is essential but weight must be minimized. In contrast, I prefer grade 316 for projects requiring enhanced durability in harsh environments, even if the material is slightly heavier.
“Understanding the density differences among stainless steel grades helps me select the right material for each project, ensuring optimal performance and efficiency.”
Applications of Grades Based on Density
The density of stainless steel directly influences its applications. I often use grade 304 for kitchen equipment, architectural structures, and automotive components due to its balance of strength, corrosion resistance, and moderate density. Its relatively lower density makes it easier to handle and fabricate without compromising durability.
For more demanding environments, I rely on grade 316. Its slightly higher density, combined with superior corrosion resistance, makes it ideal for marine equipment, chemical processing plants, and medical devices. The added weight enhances stability and durability in these challenging conditions.
Duplex stainless steels, with their intermediate density, excel in structural applications requiring high strength and resistance to stress corrosion cracking. I frequently recommend these grades for bridges, oil rigs, and storage tanks, where both weight and performance are critical factors.
By understanding how density varies across stainless steel grades, I can confidently match the material to the specific needs of each project. This approach ensures that the final product meets performance expectations while maintaining cost-effectiveness.
Selecting the Right Stainless Steel Based on Density
Choosing the right stainless steel for a project requires careful consideration of its density. This property directly impacts weight, performance, and durability, making it a critical factor in material selection. By evaluating key factors and balancing density with other properties, I can ensure the material aligns with the specific demands of the application.
Key Factors in Material Selection
When selecting stainless steel, I focus on several key factors that influence its suitability for a project:
- Application Requirements: I assess the intended use of the material. For structural applications, higher-density grades provide the strength and stability needed to support heavy loads. In contrast, lightweight applications may benefit from lower-density materials to reduce overall weight.
- Environmental Conditions: Corrosive environments demand stainless steel grades with enhanced resistance. For example, grade 316, with its slightly higher density, performs well in marine or chemical settings.
- Cost Considerations: Density affects the weight of the material, which in turn influences transportation and fabrication costs. I weigh these expenses against the benefits of using a specific grade.
- Performance Needs: I evaluate how density impacts the material’s toughness, machinability, and durability. Higher-density grades often offer superior performance in demanding conditions.
By analyzing these factors, I can narrow down the options and select the most appropriate stainless steel for the job.
“Understanding the relationship between density and application requirements ensures optimal material performance and cost-efficiency.”
Balancing Density With Other Properties
Density alone does not determine the suitability of stainless steel. I always balance this property with other material characteristics to achieve the best results:
- Strength and Toughness: Higher-density grades typically exhibit greater strength and toughness. However, I consider whether the added weight aligns with the project’s goals. For example, in aerospace applications, lighter materials may take precedence over strength.
- Corrosion Resistance: Alloying elements like chromium and nickel contribute to both density and corrosion resistance. I prioritize grades with the right balance of these properties for environments prone to rust or chemical exposure.
- Fabrication and Machinability: Denser materials can be more challenging to machine or form. I account for this during the manufacturing process to avoid delays or increased costs.
- Aesthetic and Functional Needs: In architectural projects, I consider how density affects the material’s appearance and functionality. Thicker, denser materials may provide a more robust and polished finish.
Balancing these factors allows me to make informed decisions that optimize both performance and practicality.
Practical Tips for Choosing Stainless Steel
Selecting the right stainless steel grade involves a systematic approach. Here are some practical tips I follow:
- Define Project Goals: I start by identifying the specific requirements of the project, such as load-bearing capacity, environmental exposure, and aesthetic preferences.
- Compare Grades: I review the density and other properties of various stainless steel grades. For instance, I might choose grade 304 for general-purpose applications or grade 316 for harsher environments.
- Consult Standards: I refer to industry standards and guidelines to ensure the material meets safety and performance criteria.
- Test Samples: Whenever possible, I test small samples of the material to evaluate its behavior under real-world conditions.
- Seek Expert Advice: For complex projects, I consult with material scientists or engineers to confirm my selection.
“A methodical approach to material selection minimizes risks and ensures the success of the project.”
By following these steps, I can confidently choose the stainless steel grade that best meets the project’s needs while considering the density of stainless steel as a pivotal factor.
Understanding the density of stainless steel is essential for making informed material selection decisions. This property directly affects strength, weight, and application suitability, making it a cornerstone of engineering and design practices. By evaluating the density of stainless steel alongside other factors like corrosion resistance and machinability, I can ensure optimal performance and durability. Whether designing for aerospace, automotive, or industrial applications, considering density helps achieve the perfect balance between functionality and efficiency. I encourage readers to prioritize density as a key metric in their material selection process for successful project outcomes.
FAQ
What is Stainless Steel Density?
Stainless steel density refers to its mass per unit volume. This property allows me to calculate the weight of the material based on its volume. For example, if I know the density of a specific grade, I can estimate how much a component will weigh before fabrication. This helps in planning and ensures the material meets project requirements.
Why is it important to know stainless steel density?
Knowing the density of stainless steel helps me determine if a particular alloy suits a specific application. For instance, in materials science, density plays a key role in evaluating whether the material can handle the intended load or environmental conditions. It also aids in comparing stainless steel with other metals to find the best fit for a project.
Why is the density of stainless steel crucial for engineers?
Engineers rely on stainless steel density for weight calculations, structural integrity assessments, and material selection. For example, when designing a bridge or a heavy machine, I use density to ensure the material can withstand stress and perform optimally under various conditions. This knowledge minimizes risks and enhances safety.
How does stainless steel density affect material selection?
Density directly impacts weight, strength, and performance. When selecting materials, I consider how the density aligns with the project’s goals. For lightweight applications, I might choose a lower-density material. For heavy-duty projects, higher-density stainless steel provides the necessary strength and durability.
Does stainless steel density vary across grades?
Yes, the density of stainless steel varies depending on its grade and alloy composition. For example, grade 304 has a density of about 7.93 g/cm³, while grade 316 is slightly denser at around 7.98 g/cm³. These differences influence the material’s suitability for specific applications, such as marine or industrial environments.
Can I measure stainless steel density myself?
Yes, you can measure stainless steel density using simple methods. I often weigh the sample using a precision balance and determine its volume through water displacement. Dividing the mass by the volume gives the density. However, maintaining consistent temperature and using accurate tools ensures reliable results.
How does stainless steel density impact weight and performance?
The density of stainless steel affects the weight of the final product. Heavier materials provide better stability and vibration resistance, which I find ideal for industrial equipment. However, lighter materials may improve efficiency in applications like aerospace or automotive industries. Balancing these factors ensures optimal performance.
Yes, density correlates with the alloying elements that enhance corrosion resistance. For example, higher-density grades like 316 contain more chromium and nickel, which form a protective oxide layer. This makes them more durable in harsh environments, such as marine or chemical settings.
How do I choose the right stainless steel grade based on density?
To select the right grade, I first define the project’s requirements, such as load capacity and environmental exposure. Then, I compare the densities of different grades and evaluate their properties. For instance, I might choose grade 304 for general-purpose use or grade 316 for corrosive environments.
What industries benefit most from understanding stainless steel density?
Industries like construction, aerospace, automotive, and manufacturing benefit greatly from understanding stainless steel density. For example, in construction, I use this knowledge to ensure structural stability. In aerospace, it helps optimize weight for fuel efficiency. Each industry relies on density to meet specific performance and safety standards.