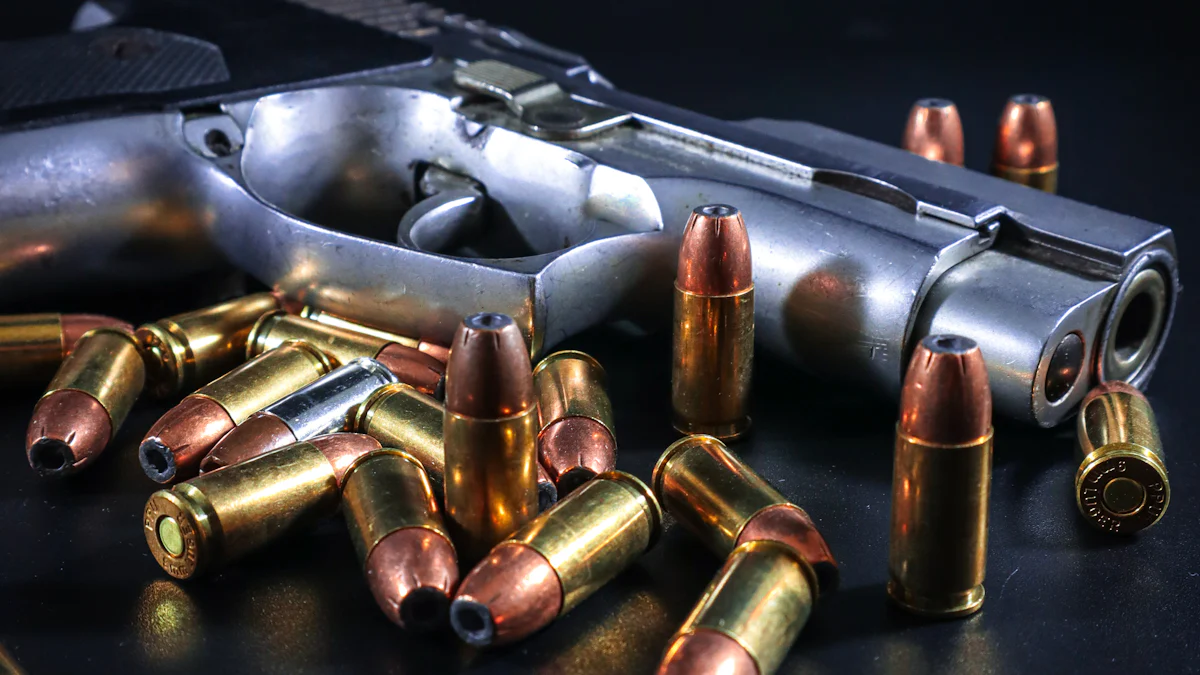
What are MIM gun parts? Metal Injection Molding (MIM) has revolutionized the production of firearm components by combining powdered metallurgy with injection molding to create intricate and precise parts. MIM gun parts, produced through this innovative process, are essential in modern firearms. They are commonly used to manufacture critical components like triggers and safeties with exceptional accuracy. This method not only ensures cost-efficiency but also upholds high-quality standards. By enabling the creation of complex designs at a reduced cost, MIM has become a cornerstone in the firearms industry, addressing the need for affordable and reliable firearms.
Key Takeaways
- MIM gun parts are created using Metal Injection Molding, combining powdered metal with binders to produce precise and intricate firearm components.
- This manufacturing process offers significant cost savings, making MIM parts an attractive option for producing affordable and reliable firearms.
- MIM technology excels in creating complex designs, allowing for the production of critical components like triggers and safeties with tight tolerances.
- While MIM parts are reliable for everyday use, they may not be suitable for high-stress applications, where forged or machined components are preferred.
- Understanding the intended use of your firearm is crucial; MIM parts are ideal for recreational shooting but may fall short in competition settings.
- Choosing firearms with MIM components can provide excellent value, balancing performance and affordability for most users.
What Are MIM Gun Parts?
Definition and Key Characteristics
MIM gun parts are firearm components crafted through the Metal Injection Molding process. This method combines powdered metal with a binding agent to create intricate and precise shapes. These parts stand out for maintaining tight tolerances, ensuring consistent dimensions and reliable performance. Manufacturers often rely on MIM technology to produce critical firearm components like triggers, sears, and ejectors. The precision achieved through this process directly impacts the functionality and reliability of firearms.
One of the defining characteristics of MIM gun parts is their cost-effectiveness. By utilizing high-volume production techniques, manufacturers can significantly reduce costs without compromising quality. This makes MIM parts an attractive option for producing affordable firearms. However, some experts argue that MIM parts may not be suitable for premium or competition-grade firearms, where durability and performance under extreme conditions are paramount.
Overview of the MIM Process
The Metal Injection Molding process involves several key steps that transform raw materials into finished firearm components. Each step plays a crucial role in achieving the desired precision and quality.
Mixing Metal Powders with Binders
The process begins by blending fine metal powders with a binding agent. This mixture, often referred to as “feedstock,” combines the strength of metal with the flexibility of plastic. The binders hold the metal particles together, allowing the material to be shaped during the next stage.
Injection Molding into Precise Shapes
The feedstock is then injected into molds designed to create specific firearm components. This step allows manufacturers to produce complex shapes with remarkable accuracy. For example, intricate designs for triggers or safeties can be achieved without the need for extensive machining. The ability to mold precise shapes reduces material waste and speeds up production.
Sintering to Remove Binders and Solidify the Part
After molding, the parts undergo a sintering process. During this stage, the binders are removed, and the metal particles fuse together under high heat. This step solidifies the part, giving it the strength and durability required for use in firearms. The sintering process also ensures that the final product meets the tight tolerances necessary for proper fit and function.
By following these steps, manufacturers can produce MIM gun parts that meet the demands of modern firearms. The combination of precision, cost-efficiency, and versatility has made MIM technology a cornerstone of the firearms industry.
Applications of MIM Gun Parts in Firearms
Common Firearm Components Made with MIM
Triggers, hammers, and safeties
MIM technology plays a vital role in crafting essential firearm components like triggers, hammers, and safeties. These parts demand precision and consistency to ensure proper functionality. Manufacturers rely on MIM to produce these intricate components with tight tolerances. For example, triggers made through MIM maintain uniform dimensions, which directly impacts the firearm’s performance. Hammers and safeties also benefit from the process, as MIM allows for the creation of complex shapes that traditional machining might struggle to achieve. This precision ensures that these parts fit seamlessly into firearm assemblies, enhancing reliability.
Small internal parts (e.g., sears, ejectors)
Small internal parts, such as sears and ejectors, are another area where MIM excels. These components often require detailed designs and exact measurements to function correctly within the firearm’s mechanism. MIM enables manufacturers to produce these parts efficiently while maintaining high-quality standards. For instance, sears crafted through MIM provide consistent engagement with other components, ensuring smooth operation. Ejectors, which play a critical role in expelling spent cartridges, benefit from the durability and precision offered by MIM. By utilizing this technology, manufacturers can produce small internal parts that meet the rigorous demands of modern firearms.
Examples of Firearms Using MIM Parts
Handguns with MIM components
Many popular handguns incorporate MIM components to enhance performance and reduce production costs. For instance, Smith & Wesson has transitioned numerous small parts in their pistols to MIM production. This shift has allowed them to maintain consistent quality across their product lines. Similarly, Kimber and Wilson Combat utilize MIM parts in their 1911 models, including extractors, sears, and hammers. These brands have demonstrated that MIM components can perform reliably in handguns, even under demanding conditions. I have personally seen how these parts contribute to the overall functionality and affordability of these firearms.
Rifles and shotguns incorporating MIM parts
Rifles and shotguns also benefit from the integration of MIM components. Ruger, for example, incorporates MIM parts into several of their revolvers, such as the SP101 and GP100. These parts include triggers and other small internal components that require precision. Additionally, Smith & Wesson uses MIM technology in their revolvers, ensuring consistent performance across their lineup. By adopting MIM, manufacturers can produce rifles and shotguns with intricate designs and reliable functionality. This approach not only enhances the performance of these firearms but also makes them more accessible to a broader audience.
“MIM manufactures components with tight tolerances and consistent dimensions, guaranteeing accurate fit and functionality in firearm assemblies.” This statement highlights the importance of MIM in creating reliable firearms.
The widespread use of MIM parts in handguns, rifles, and shotguns underscores their significance in the firearms industry. By leveraging this technology, manufacturers can produce high-quality components that meet the needs of both casual users and professionals.
Advantages and Disadvantages of MIM Gun Parts
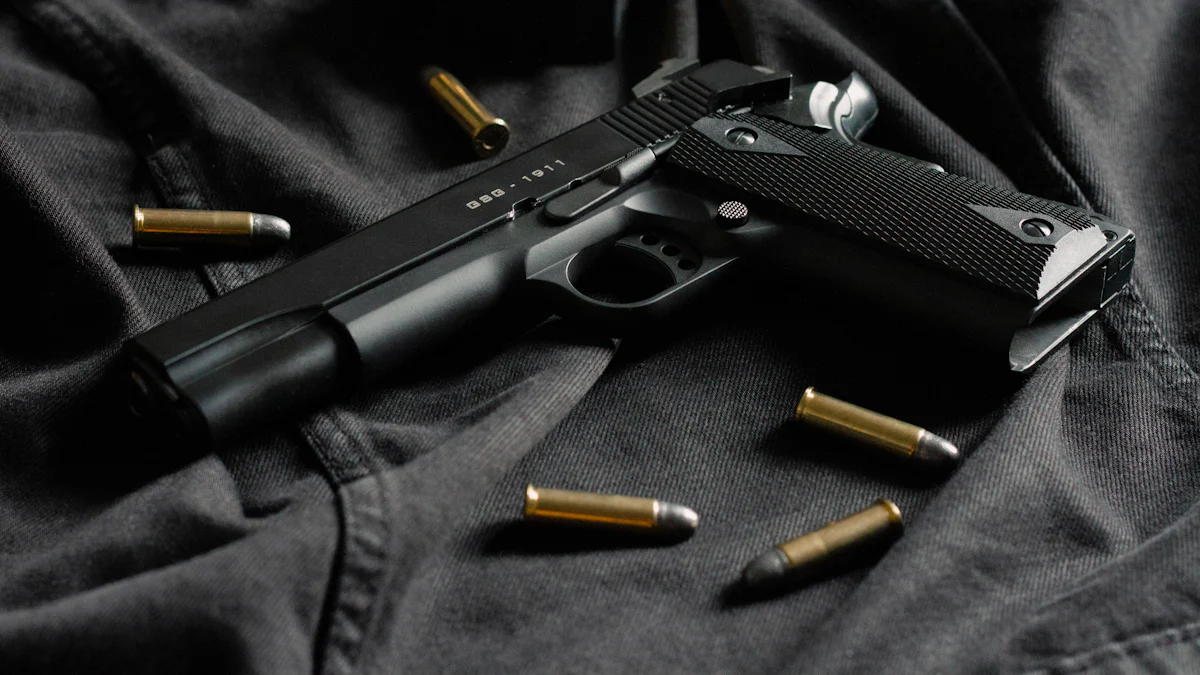
Advantages
Cost-effective for mass production
MIM technology excels in reducing production costs. I’ve observed how manufacturers can produce large quantities of firearm components without sacrificing quality. The process eliminates the need for extensive machining, which lowers labor and material expenses. This efficiency makes MIM parts an ideal choice for affordable firearms. By streamlining production, manufacturers can focus on delivering reliable products at competitive prices.
Ability to create intricate designs
The ability to craft complex shapes sets MIM apart from traditional methods. I’ve seen firsthand how MIM allows for the creation of intricate firearm components that would be challenging or impossible to achieve through machining or forging. For example, small internal parts like sears and ejectors benefit from this precision. The flexibility of MIM ensures that even the most detailed designs meet exact specifications, enhancing the overall functionality of firearms.
Consistent quality and precision
Consistency is critical in firearm manufacturing, and MIM delivers on this front. The process ensures tight tolerances and uniform dimensions across all components. I’ve noticed how this consistency directly impacts the reliability of firearms. Whether it’s a trigger or a safety, MIM parts fit seamlessly into assemblies, reducing the likelihood of malfunctions. This level of precision builds trust among firearm users who demand dependable performance.
Disadvantages
Potential for reduced durability under extreme stress
While MIM parts perform well under normal conditions, they may not match the durability of forged or machined components in extreme scenarios. I’ve encountered discussions where some users expressed concerns about MIM parts failing under high stress. For instance, components subjected to intense pressure or repeated impact might wear out faster than their forged counterparts. This limitation makes MIM less suitable for firearms designed for heavy-duty or competition use.
Limited material options
MIM relies on specific metal powders, which restricts the range of materials available for production. I’ve noticed that this limitation can affect the strength and performance of certain components. For example, while MIM parts are stronger and denser than sintered parts, they don’t reach the strength levels of machined barstock or forged parts. This constraint may influence a manufacturer’s decision when selecting materials for high-performance firearms.
Perception of lower quality among some users
Despite advancements in MIM technology, some firearm enthusiasts still perceive MIM parts as inferior. I’ve heard arguments suggesting that MIM lacks the craftsmanship associated with traditional machining or forging. This perception often stems from early issues with MIM parts, which failed to meet quality standards. Although modern MIM components have improved significantly, overcoming this stigma remains a challenge for manufacturers.
Addressing Concerns About Reliability
Real-world performance of MIM parts
In my experience, real-world performance often dispels doubts about MIM reliability. Many firearms with MIM components function flawlessly in various conditions. For instance, handguns from brands like Kimber and Smith & Wesson incorporate MIM parts and perform reliably. These examples demonstrate that MIM parts can meet the demands of everyday use. By focusing on quality control, manufacturers ensure that MIM components deliver consistent results.
Comparisons to forged and machined parts
When comparing MIM parts to forged and machined components, each method has its strengths. MIM parts excel in creating intricate designs and maintaining cost-efficiency. Forged parts, on the other hand, offer superior strength and durability under extreme stress. Machined parts provide unmatched precision but at a higher cost. I’ve found that the choice between these methods depends on the intended application. For most standard firearms, MIM parts strike a balance between performance and affordability.
“MIM parts are stronger, denser, and capable of complex geometric shapes compared to forged and machined parts.” This insight highlights the unique advantages of MIM technology while acknowledging its limitations.
By addressing these concerns, I believe firearm users can make informed decisions about the suitability of MIM components for their needs. Understanding the trade-offs between cost, precision, and durability helps clarify why MIM has become a cornerstone in modern firearm manufacturing.
Are MIM Gun Parts Reliable?
Factors Influencing Reliability
Quality of Manufacturing Processes
The reliability of MIM gun parts depends heavily on the quality of the manufacturing process. I’ve observed that manufacturers who invest in advanced equipment and strict quality control produce parts with exceptional consistency. For instance, companies like Smith & Wesson and Colt have refined their MIM production techniques over the years. They ensure that each component meets precise specifications, reducing the likelihood of defects.
When manufacturers follow rigorous standards, MIM parts perform reliably in various firearms. However, cutting corners during production can lead to flaws, such as weak points or improper dimensions. This is why I always emphasize the importance of choosing firearms from reputable brands. Their commitment to quality ensures that MIM components function as intended.
Intended Use and Stress Levels
The intended use of a firearm plays a significant role in determining the reliability of its MIM parts. I’ve noticed that MIM components excel in standard applications, such as recreational shooting or self-defense. These scenarios typically involve moderate stress levels, where MIM parts perform without issue.
However, firearms designed for heavy-duty use, such as competition or military applications, may demand components with greater durability. In these cases, forged or machined parts might be more suitable. For example, I’ve seen discussions among firearm enthusiasts about MIM parts potentially wearing out faster under extreme conditions. While this concern holds merit, it’s important to remember that most users won’t subject their firearms to such intense stress.
Industry Perspectives
Opinions from Firearm Manufacturers
Many firearm manufacturers trust MIM technology for producing reliable components. Experts in the firearms industry often highlight the success of brands like Colt and Smith & Wesson in integrating MIM parts into their products. One expert noted, “S&W changed to MIM for their hammers and triggers some time back with a few early issues but refined until they require less fitting and are holding up well.” This statement underscores how advancements in MIM technology have addressed initial challenges, resulting in dependable components.
Manufacturers also appreciate the cost-efficiency and precision of MIM. By adopting this technology, they can produce intricate parts at scale without compromising quality. For instance, I’ve seen how companies like Kimber and Ruger incorporate MIM components into their firearms, demonstrating confidence in the process. Their success stories reinforce the reliability of MIM parts when produced under strict standards.
Feedback from Firearm Users
Feedback from firearm users provides valuable insights into the real-world performance of MIM parts. Many users report positive experiences with firearms that feature MIM components. One individual shared, “If S&W, Colt, etc., trust MIM for high-stress parts like the hammer and trigger, I think I’ll trust it for parts on my Springfield.” This sentiment reflects the growing acceptance of MIM technology among firearm enthusiasts.
However, some users remain skeptical due to past issues with early MIM parts. I’ve encountered comments questioning the durability of MIM components under extreme conditions. While these concerns are valid, it’s important to consider advancements in the technology. Modern MIM parts undergo rigorous testing to ensure they meet the demands of everyday use. By focusing on quality control, manufacturers have addressed many of the reliability concerns associated with MIM.
“MIM manufactures components with tight tolerances and consistent dimensions, guaranteeing accurate fit and functionality in firearm assemblies.” This quote highlights the importance of precision in ensuring the reliability of MIM parts.
In my experience, the reliability of MIM gun parts depends on several factors, including manufacturing quality and intended use. By understanding these variables, firearm users can make informed decisions about the suitability of MIM components for their needs.
MIM gun parts represent a breakthrough in firearm manufacturing. This process combines powdered metallurgy with injection molding to create small, intricate components with precision and efficiency. MIM excels in producing cost-effective parts while maintaining consistent quality. However, it may not match the durability of forged or machined components under extreme conditions.
The advantages of MIM include affordability, intricate design capabilities, and high-volume production. Yet, limitations like material restrictions and durability concerns exist. I believe MIM parts suit most standard applications, offering reliability for everyday use. When choosing firearms, evaluate your specific needs to determine if MIM components align with your expectations.
FAQ
Does it matter if gun parts are MIM?
Yes, it does matter, but only in specific contexts. MIM gun parts perform exceptionally well under normal use conditions. They offer precision and cost-efficiency, making them ideal for most firearms. However, for competition or custom guns that endure extreme stress, forged or machined parts may provide better durability. Choosing the right material depends on your firearm’s intended use.
How can I tell if my gun has MIM parts?
Identifying MIM parts in your firearm can be challenging without detailed knowledge of the manufacturing process. Typically, manufacturers do not explicitly label MIM components. However, you can often spot them by their smooth, uniform appearance and intricate designs. If you’re unsure, consult your firearm’s manual or contact the manufacturer directly. Understanding your firearm’s construction helps you make informed decisions about its maintenance and use.
Are MIM parts reliable for everyday use?
Absolutely. MIM parts excel in standard applications like recreational shooting or self-defense. They maintain tight tolerances and consistent dimensions, ensuring reliable performance. For instance, triggers and hammers made through MIM function seamlessly under normal conditions. Reliability concerns usually arise only in extreme scenarios, such as high-stress competition shooting.
Why do some people criticize MIM parts?
Criticism of MIM parts often stems from misconceptions or early issues with the technology. Some users perceive them as less durable than forged or machined components. Others associate MIM with budget firearms, assuming lower quality. However, advancements in MIM technology have addressed many of these concerns. Modern MIM parts meet high standards of precision and reliability, proving their worth in the firearms industry.
Do all firearm manufacturers use MIM parts?
Not all manufacturers use MIM parts, but many do. Brands like Smith & Wesson, Kimber, and Ruger incorporate MIM components into their firearms. These companies trust MIM for its cost-effectiveness and ability to produce intricate designs. On the other hand, some manufacturers, like Glock, avoid MIM due to their preference for alternative methods. Each brand chooses materials based on their design philosophy and target market.
Are MIM parts suitable for competition firearms?
MIM parts may not be the best choice for competition firearms. Competitive shooters demand components that withstand high round counts and intense stress. Forged or machined parts often outperform MIM in these scenarios. For casual use, MIM parts work perfectly fine, but for competition-level reliability, premium materials are worth the investment.
What advantages does MIM offer over traditional methods?
MIM offers several advantages, including cost-efficiency, the ability to create intricate designs, and reduced assembly requirements. Unlike traditional machining, MIM produces cohesive components with tight tolerances. This precision ensures proper fit and functionality in firearm assemblies. For manufacturers, MIM streamlines production while maintaining high-quality standards.
Can MIM parts fail under extreme conditions?
Yes, MIM parts can fail under extreme conditions, though this is rare in everyday use. Components subjected to intense pressure or repeated impact may wear out faster than forged counterparts. For example, competition firearms often require parts that endure heavy abuse, where MIM might fall short. Understanding your firearm’s purpose helps you determine if MIM parts are suitable.
Are MIM parts more affordable than forged or machined parts?
Yes, MIM parts are generally more affordable. The process eliminates extensive machining, reducing labor and material costs. This affordability makes MIM an attractive option for manufacturers and consumers alike. By choosing MIM, you can enjoy high-quality firearms at a lower price point.
Should I avoid firearms with MIM parts?
Not necessarily. Firearms with MIM parts perform reliably for most users. If you prioritize cost-efficiency and precision, MIM components are an excellent choice. However, if you need a firearm for heavy-duty or competition use, consider models with forged or machined parts. Evaluate your needs and budget to make the best decision for your situation.
Pingback: Does Titanium Rust? - China Custom Titanium Components Manufacturing