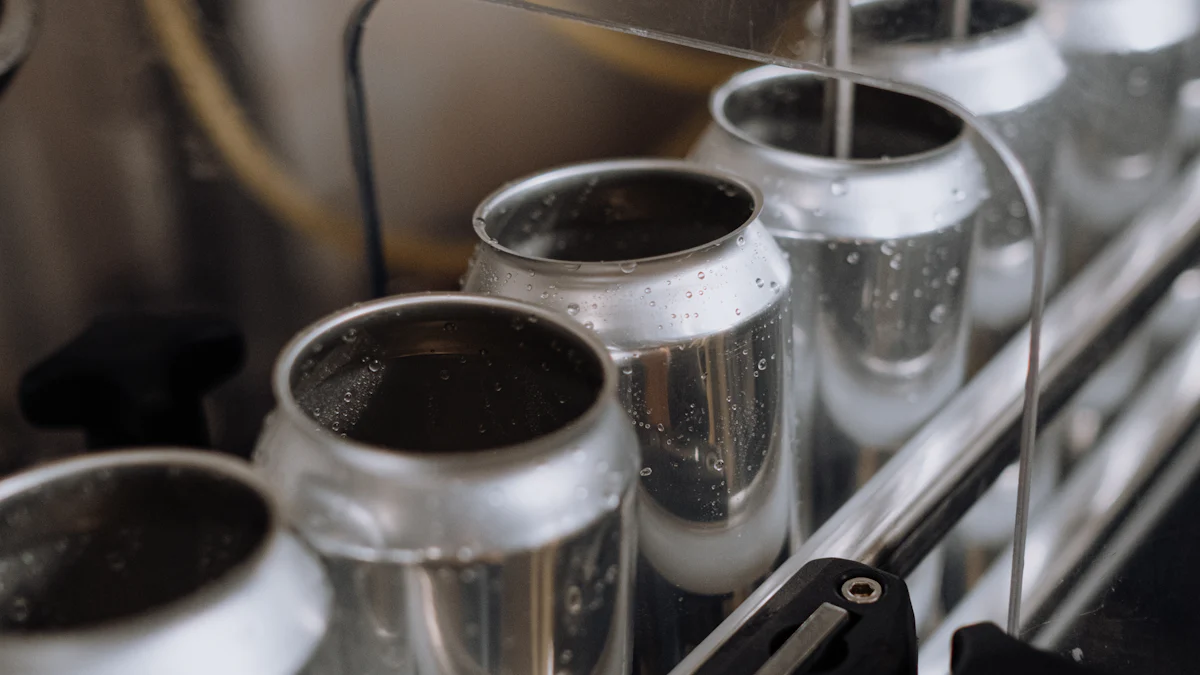
Gas atomization plays a vital role in creating high-quality metal powders. This process ensures the production of powders with precise properties, making them indispensable in modern manufacturing. You rely on these powders for their purity, sphericity, and controlled size, which are essential in advanced technologies. Metal-powders-gas-atomization supports industries like aerospace, automotive, and medical by enabling innovative solutions. Its significance extends to powder metallurgy, where it drives efficiency and performance in applications such as additive manufacturing.
Key Takeaways
- Gas atomization is essential for producing high-quality metal powders with precise properties, crucial for advanced manufacturing applications.
- The process involves melting metal, atomizing it with high-velocity gas, and rapidly cooling the droplets to create uniform, spherical powders.
- Key characteristics of gas-atomized powders include high sphericity, exceptional purity, and controlled particle size, making them ideal for industries like aerospace and medical.
- Adjusting parameters such as gas pressure, flow rate, and nozzle design allows for tailored powder properties, enhancing performance in applications like additive manufacturing.
- Gas atomization supports scalability, making it suitable for both small-scale research and large-scale industrial production of metal powders.
- While gas atomization offers numerous benefits, challenges such as high energy consumption and equipment complexity must be managed to maintain efficiency and cost-effectiveness.
- The versatility of gas atomization enables the production of powders from various metals and alloys, catering to the specific needs of diverse industries.
Understanding Metal-Powders-Gas-Atomization
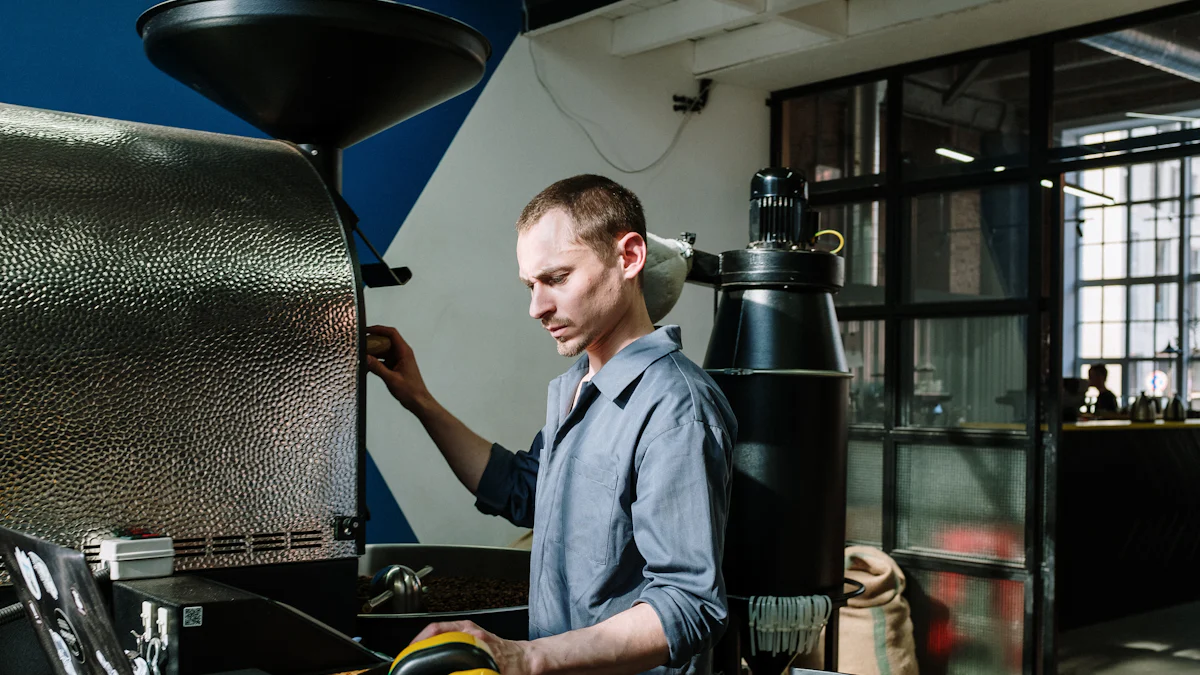
What is Gas Atomization?
Definition and its significance in metal powder production.
Gas atomization is a process that transforms molten metal into fine, spherical particles. You achieve this by using a high-velocity gas stream to break the molten metal into droplets, which then solidify into powders. This method stands out for its ability to produce powders with consistent quality and precise characteristics. In metal powder production, gas atomization plays a crucial role in meeting the demands of industries that require high-performance materials. You rely on this process to create powders suitable for advanced applications like additive manufacturing and powder metallurgy.
Key characteristics of gas-atomized powders (sphericity, purity, size control).
Gas-atomized powders possess unique features that make them ideal for modern manufacturing. Their high sphericity ensures better flowability, which is essential for processes like 3D printing. You also benefit from their exceptional purity, as the controlled environment during atomization minimizes contamination. Additionally, the process allows precise control over particle size, enabling you to produce powders tailored to specific applications. These characteristics make gas-atomized powders indispensable in industries such as aerospace, automotive, and medical.
How Does Gas Atomization Work?
Process overview: Melting, atomization, and solidification.
The gas atomization process involves three main steps. First, you melt the metal to create a liquid state. Then, a high-velocity gas stream atomizes the molten metal, breaking it into fine droplets. Finally, these droplets rapidly cool and solidify into metal powders. This sequence ensures the production of powders with uniform properties and high quality.
Role of high-velocity gas in breaking molten metal into fine droplets.
High-velocity gas plays a critical role in the atomization process. When the gas interacts with the molten metal, it transfers energy that breaks the liquid into tiny droplets. The speed and force of the gas determine the size and shape of the resulting particles. By adjusting the gas velocity, you can control the powder’s characteristics, ensuring they meet specific requirements.
Types of gases used and their impact on powder properties.
Different gases influence the properties of the produced powders. Commonly used gases include nitrogen, argon, and helium. Nitrogen is cost-effective and suitable for many metals, while argon provides an inert environment that prevents oxidation. Helium, with its high cooling capacity, enhances the rapid solidification of droplets. The choice of gas depends on the desired powder properties and the type of metal being processed. By selecting the right gas, you can optimize the quality and performance of the metal powders.
The Science Behind Gas Atomization
Key Scientific Principles
Energy transfer: Momentum transmission from gas to molten metal.
Energy transfer is the foundation of gas atomization. When high-velocity gas interacts with molten metal, it transmits momentum to the liquid. This force breaks the molten stream into fine droplets. The efficiency of this momentum transfer directly affects the size and uniformity of the particles. You can optimize this process by adjusting the gas velocity and pressure. A higher velocity increases the energy imparted to the metal, resulting in smaller and more consistent powder particles.
Heat exchange and rapid cooling during droplet solidification.
Heat exchange plays a critical role in shaping the final properties of metal powders. As the molten droplets form, they rapidly lose heat to the surrounding gas. This quick cooling solidifies the droplets into spherical particles. The rate of cooling determines the microstructure of the powders. Faster cooling produces finer grains, which enhance the mechanical properties of the material. You can control this cooling rate by selecting gases with specific thermal properties, such as helium or argon.
Influence of surface tension and viscosity on droplet formation.
Surface tension and viscosity govern how molten metal behaves during atomization. High surface tension resists the breakup of the liquid stream, leading to larger droplets. Lower viscosity allows the metal to flow more freely, making it easier to form smaller particles. You can manipulate these properties by adjusting the temperature of the molten metal. Higher temperatures reduce viscosity and surface tension, improving the efficiency of the atomization process.
Process Parameters and Their Effects
Gas pressure and flow rate on particle size distribution.
Gas pressure and flow rate are key parameters in controlling particle size. Higher gas pressure increases the force applied to the molten metal, creating finer powders. A consistent flow rate ensures uniform energy distribution, resulting in a narrow particle size range. You can fine-tune these settings to produce powders tailored to specific applications, such as additive manufacturing or powder metallurgy.
Nozzle design and its role in atomization efficiency.
The nozzle design significantly impacts the atomization process. A well-designed nozzle ensures the gas stream interacts effectively with the molten metal. This interaction maximizes energy transfer and improves particle uniformity. You can choose from various nozzle types, such as convergent-divergent or straight-bore designs, depending on your production needs. Proper nozzle maintenance also prevents clogging and ensures consistent performance.
Temperature control and its impact on powder morphology.
Temperature control is essential for achieving the desired powder morphology. Maintaining the optimal temperature keeps the metal in a fully molten state, ensuring smooth atomization. If the temperature drops too low, the metal may partially solidify, leading to irregularly shaped particles. Precise temperature management also influences the cooling rate, which affects the microstructure and mechanical properties of the powders. You can use advanced monitoring systems to maintain consistent temperatures throughout the process.
The Role of Gas Atomization in Powder Metallurgy
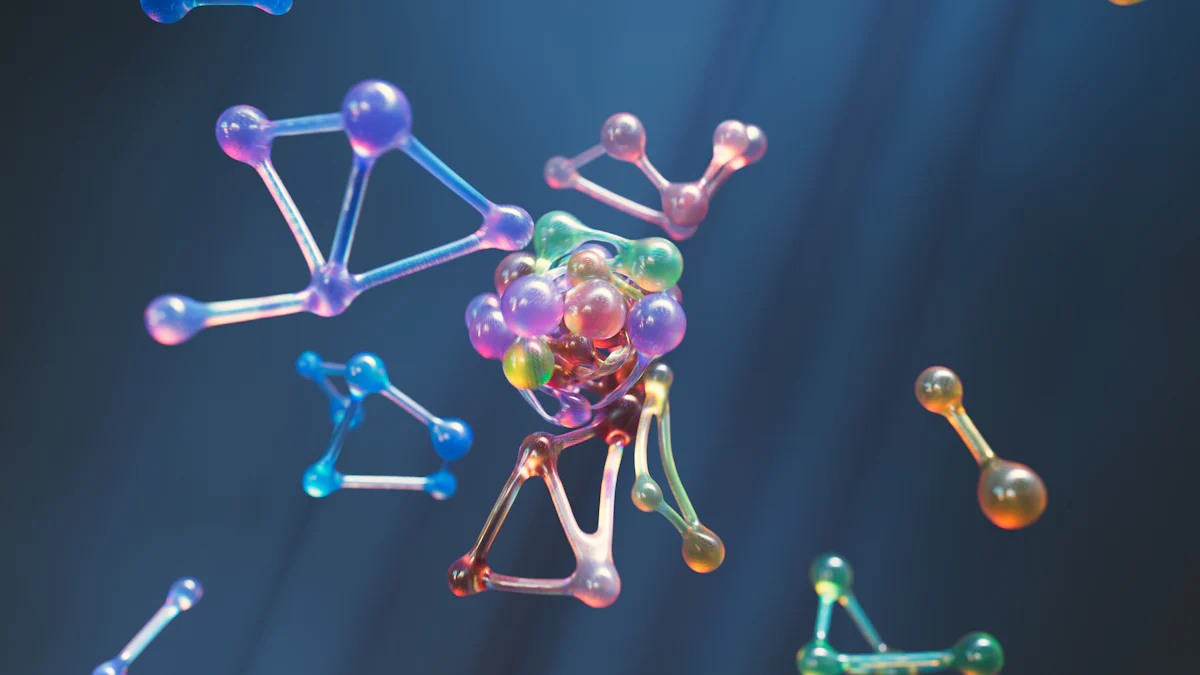
Importance of Powder Quality
Particle size distribution and its relevance to powder metallurgy.
Particle size distribution directly affects the performance of metal powders in powder metallurgy. Uniform particle sizes ensure consistent packing density, which improves the mechanical properties of the final product. You can achieve precise control over particle size through gas atomization. This control allows you to tailor powders for specific applications, such as additive manufacturing or sintering. Consistent particle size also reduces defects during processing, ensuring higher-quality components.
Sphericity and surface finish for advanced applications.
Sphericity plays a critical role in determining how powders behave during manufacturing. Highly spherical particles flow more smoothly, which enhances the efficiency of processes like 3D printing. Smooth surfaces on these particles reduce friction and improve layer adhesion in additive manufacturing. You benefit from gas atomization because it produces powders with excellent sphericity and surface finish. These qualities make the powders ideal for advanced applications requiring precision and reliability.
Purity and chemical composition control in metal powders.
Purity is essential when producing metal powders for high-performance applications. Contaminants can compromise the strength, durability, and functionality of the final product. Gas atomization occurs in a controlled environment, which minimizes contamination and ensures high purity. You can also maintain strict control over the chemical composition of the powders. This precision allows you to meet the stringent requirements of industries like aerospace and medical, where material quality is non-negotiable.
Applications in Powder Metallurgy
Additive manufacturing and 3D printing.
Additive manufacturing relies heavily on high-quality metal powders. Gas atomization provides powders with the sphericity, purity, and size control needed for 3D printing. These powders enable you to create complex geometries with minimal waste. The consistent properties of gas-atomized powders ensure reliable performance in every layer of the printed object. This makes them indispensable for industries pushing the boundaries of design and innovation.
Sintering and hot isostatic pressing (HIP).
Sintering and hot isostatic pressing require powders with specific characteristics to achieve optimal results. Gas-atomized powders offer the uniformity and purity needed for these processes. During sintering, the powders fuse together to form dense and strong components. HIP further enhances the material’s properties by eliminating internal voids. You can rely on gas atomization to produce powders that meet the exacting standards of these techniques, ensuring superior performance in the final products.
Use in aerospace, automotive, and medical industries.
The aerospace, automotive, and medical industries demand materials with exceptional quality and performance. Gas-atomized powders meet these demands by providing the precision and reliability required for critical applications. In aerospace, you use these powders to manufacture lightweight yet durable components. The automotive industry benefits from their ability to create parts with high strength and wear resistance. In the medical field, gas-atomized powders enable the production of biocompatible implants and devices. Their versatility makes them a cornerstone of modern manufacturing across these sectors.
Advantages and Challenges of Metal-Powders-Gas-Atomization
Benefits of Gas Atomization
Production of high-quality powders with consistent properties.
Gas atomization allows you to produce metal powders with exceptional quality. The process ensures uniform particle size, high sphericity, and superior purity. These characteristics make the powders reliable for advanced manufacturing techniques like additive manufacturing and powder metallurgy. You can depend on gas atomization to deliver consistent results, which is critical for industries requiring precision and performance.
Scalability for industrial and commercial applications.
Gas atomization offers scalability, making it suitable for both small-scale and large-scale production. Whether you need powders for research or mass production, this process adapts to your requirements. You can increase production capacity by optimizing equipment and process parameters. This flexibility supports the growing demand for metal powders in industries like aerospace, automotive, and medical.
Versatility in producing powders from various metals and alloys.
The versatility of gas atomization enables you to create powders from a wide range of metals and alloys. From titanium and aluminum to nickel-based superalloys, this process accommodates diverse materials. You can tailor the properties of the powders to meet specific application needs. This adaptability makes gas atomization a preferred choice for producing specialized powders for cutting-edge technologies.
Challenges and Limitations
High energy consumption and operational costs.
Gas atomization requires significant energy to melt metals and generate high-velocity gas streams. This energy demand increases operational costs, which can impact your production budget. You may need to explore energy-efficient technologies or alternative methods to reduce expenses. Balancing cost and quality remains a challenge in maintaining profitability.
Equipment complexity and maintenance requirements.
The equipment used in gas atomization is complex and requires regular maintenance. Nozzles, gas delivery systems, and cooling mechanisms must function flawlessly to ensure consistent powder quality. You need skilled technicians to operate and maintain the machinery. Equipment downtime for repairs or maintenance can disrupt production schedules, posing additional challenges.
Environmental considerations and gas usage.
Gas atomization relies on gases like nitrogen, argon, and helium, which have environmental and cost implications. Helium, for example, is expensive and limited in supply. You must also consider the environmental impact of gas emissions during the process. Implementing sustainable practices, such as recycling gases or using eco-friendly alternatives, can help address these concerns.
Gas atomization stands as a cornerstone in producing high-quality metal powders. You rely on its scientific principles, like energy transfer and rapid cooling, to achieve powders with precise properties. This process plays a vital role in powder metallurgy, ensuring superior performance in applications like additive manufacturing. By mastering gas atomization, you unlock the potential for innovation in industries such as aerospace, automotive, and medical. Its ability to deliver consistent, versatile, and advanced powders makes it indispensable for modern manufacturing technologies.
FAQ
What is gas atomization, and why is it important?
Gas atomization is a process where high-velocity gas breaks molten metal into fine droplets, which then solidify into spherical powders. This method is essential because it produces metal powders with consistent quality, high purity, and precise size control. These powders are critical for advanced manufacturing techniques like additive manufacturing and powder metallurgy.
How does gas atomization differ from other powder production methods?
Gas atomization stands out due to its ability to create highly spherical and ultra-clean powders. Unlike water atomization, which may introduce impurities, gas atomization uses inert gases like argon or nitrogen to prevent oxidation. This process also offers better control over particle size and morphology compared to mechanical or chemical methods.
What types of metals can you process using gas atomization?
You can process a wide range of metals and alloys through gas atomization. Common examples include titanium, aluminum, stainless steel, and nickel-based superalloys. The versatility of this method allows you to tailor powders for specific applications, whether in aerospace, automotive, or medical industries.
Why is sphericity important in metal powders?
Sphericity ensures better flowability and packing density in metal powders. These qualities are crucial for processes like 3D printing, where smooth powder flow improves layer adhesion and reduces defects. Spherical powders also enhance the efficiency of sintering and hot isostatic pressing by promoting uniform densification.
How does the choice of gas affect the properties of metal powders?
The type of gas you use impacts the cooling rate, purity, and oxidation resistance of the powders. For example, argon provides an inert environment that prevents oxidation, while helium offers rapid cooling for finer microstructures. Nitrogen is cost-effective and works well for many metals but may react with certain materials.
What are the main challenges of gas atomization?
Gas atomization faces challenges like high energy consumption, complex equipment maintenance, and environmental concerns. The process requires significant energy to melt metals and generate high-velocity gas streams. Equipment like nozzles and gas delivery systems needs regular upkeep. Additionally, the use of gases like helium can be costly and environmentally impactful.
Can gas atomization produce powders for additive manufacturing?
Yes, gas atomization is the preferred method for producing powders used in additive manufacturing. The process creates powders with the sphericity, purity, and size control required for 3D printing. These powders enable you to achieve precise geometries and consistent performance in printed components.
How do you control particle size during gas atomization?
You can control particle size by adjusting parameters like gas pressure, flow rate, and nozzle design. Higher gas pressure and velocity create finer powders, while consistent flow ensures uniform size distribution. Proper temperature management also plays a role in achieving the desired particle size.
Is gas atomization environmentally friendly?
Gas atomization has environmental considerations, especially regarding gas usage and emissions. While inert gases like argon and nitrogen are less harmful, helium’s limited supply and high cost pose challenges. You can adopt sustainable practices, such as recycling gases, to reduce the environmental impact.
What industries benefit the most from gas-atomized powders?
Industries like aerospace, automotive, and medical benefit significantly from gas-atomized powders. In aerospace, you use these powders to create lightweight yet durable components.