When choosing a manufacturing process, understanding the differences between investment casting vs metal injection molding is crucial. Each method offers unique benefits and limitations that can significantly impact your project’s success. You need to consider factors like material properties, part complexity, and production volume. By grasping these distinctions, you can make informed decisions that align with your design goals and budget. This knowledge ensures that you select the most efficient and cost-effective process for your specific needs.
Key Takeaways
- Investment casting is ideal for producing larger, intricate components with high precision and a wide range of material options, making it suitable for industries like aerospace and automotive.
- Metal injection molding (MIM) excels in creating small, complex parts with tight tolerances, offering significant cost savings in high-volume production, particularly in electronics and medical devices.
- When choosing a manufacturing process, consider part complexity: MIM is better for tiny, detailed designs, while investment casting is more effective for larger parts requiring smooth finishes.
- Evaluate your production volume: investment casting is cost-effective for low to medium runs, whereas MIM is more economical for mass production due to lower per-part costs.
- Material selection is crucial; investment casting supports a broader range of metals and alloys, while MIM is limited to specific materials like stainless steel and titanium.
- Both methods deliver excellent surface finishes, but investment casting may require additional post-processing, while MIM typically produces near-net shape parts with minimal finishing needed.
- Understanding the unique advantages and limitations of each process helps you make informed decisions that align with your project’s specific needs and budget.
Understanding Investment Casting and Metal Injection Molding
When deciding between investment casting and metal injection molding, understanding the processes and materials involved is essential. Each method has unique characteristics that cater to specific manufacturing needs. Let’s explore these two techniques in detail.
Investment Casting
Overview of the process
Investment casting, also known as lost-wax casting, is a manufacturing process that creates precise and detailed components. You start by creating a wax pattern that matches the desired part. This wax model gets coated with a ceramic shell, which hardens to form a mold. Once the mold is ready, the wax is melted and drained, leaving a cavity for molten metal. The metal is poured into the mold, cooled, and solidified. After breaking the ceramic shell, you get a finished part with intricate details.
This process is ideal for producing parts with complex geometries and smooth surface finishes. It works well for medium to large-sized components where precision is critical. Investment casting minimizes material waste and reduces the need for extensive machining.
Common materials used
Investment casting supports a wide range of metals and alloys. You can use stainless steel, carbon steel, aluminum, brass, and bronze. Superalloys like cobalt and nickel are also common for high-performance applications. The versatility of materials makes this process suitable for industries like aerospace, automotive, and medical equipment manufacturing.
Metal Injection Molding (MIM)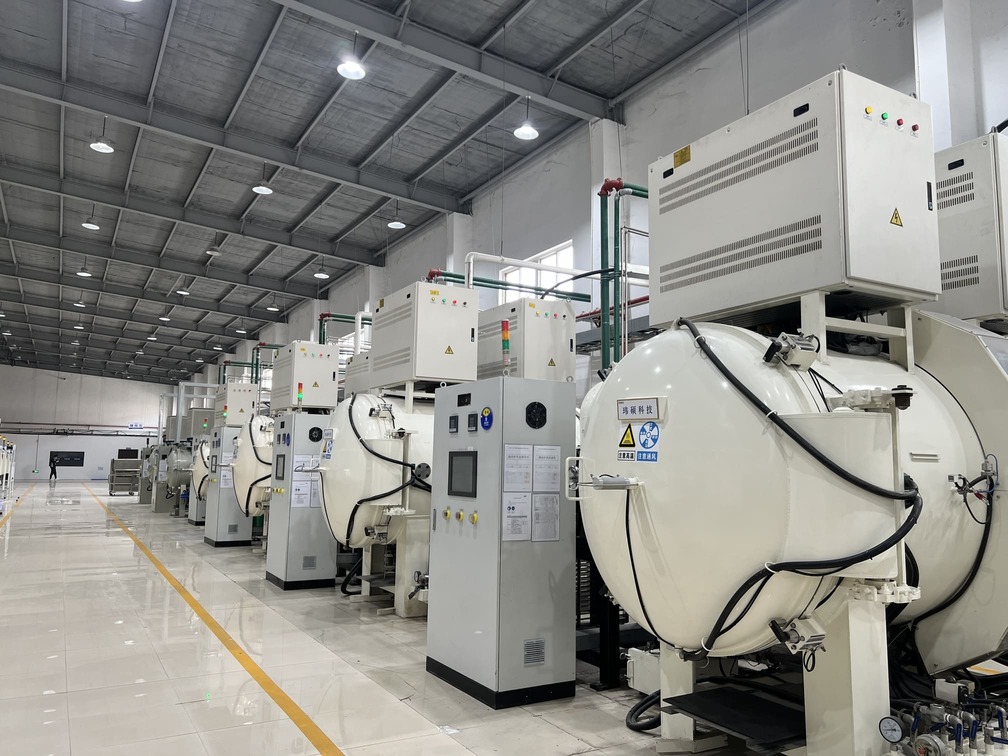
Overview of the process
Metal injection molding (MIM) combines the principles of plastic injection molding with powder metallurgy. You begin by mixing fine metal powders with a binder to create a feedstock. This mixture is injected into a mold under high pressure to form the desired shape. The molded part, known as a “green part,” undergoes debinding to remove the binder. Finally, the part is sintered in a furnace, where the metal particles fuse, resulting in a dense and strong component.
MIM excels at producing small, intricate parts with tight tolerances. It eliminates the need for extensive post-processing and achieves consistent results in high-volume production. This process is particularly effective for manufacturing components with complex geometries that would be challenging to achieve using traditional methods.
Common materials used
MIM primarily uses materials like stainless steel, low-alloy steel, titanium, and tungsten. These materials offer excellent mechanical properties and corrosion resistance. MIM is especially popular in industries such as electronics, medical devices, and firearms, where small, precise parts are essential.
Both investment casting and metal injection molding provide unique advantages. Understanding their processes and material options helps you choose the right method for your project.
Comparing Investment Casting vs Metal Injection Molding
Investment Casting Parts
When deciding between investment casting and metal injection molding, understanding how these processes compare in key areas is essential. Each method offers distinct advantages depending on your project’s requirements. Let’s explore their differences in material options, part complexity, and production volume.
Material Options
Types of metals and alloys supported
Investment casting supports a broad range of metals and alloys. You can work with stainless steel, carbon steel, aluminum, brass, bronze, and even superalloys like cobalt and nickel. This versatility makes it suitable for projects requiring specific material properties, such as high strength or corrosion resistance.
Metal injection molding (MIM), on the other hand, focuses on materials like stainless steel, low-alloy steel, titanium, and tungsten. These materials provide excellent mechanical properties and are ideal for small, intricate parts. However, MIM offers fewer material options compared to investment casting.
Material properties and limitations
Investment casting delivers components with high strength, durability, and resistance to extreme conditions. It works well for parts that need to withstand heavy loads or high temperatures. However, the process may not be as cost-effective for small, lightweight parts.
MIM excels in producing dense, strong components with consistent material properties. It is perfect for applications requiring precision and uniformity. However, the sintering process in MIM may limit the size of parts you can produce, making it less suitable for larger components.
Part Complexity
Ability to produce intricate designs
Investment casting allows you to create complex geometries with smooth surface finishes. The wax pattern technique enables the production of detailed designs that would be challenging with other methods. This makes it ideal for components with intricate shapes or internal cavities.
MIM takes part complexity to another level. It can produce extremely small and detailed parts with tight tolerances. The injection molding process ensures that even the most intricate designs are achievable. If your project involves tiny, precise components, MIM is often the better choice.
Tolerances and precision
Investment casting offers good precision but may require additional machining for tight tolerances. The process achieves excellent results for medium to large parts but may struggle with the same level of detail as MIM for smaller components.
MIM provides superior precision and consistency. The process minimizes the need for post-processing, ensuring that parts meet exact specifications. This makes MIM a preferred option for industries like electronics and medical devices, where precision is critical.
Production Volume
Suitability for low vs. high production runs
Investment casting is well-suited for low to medium production volumes. The process involves lower initial tooling costs, making it a cost-effective choice for smaller batches. However, it becomes less economical for high-volume production due to longer lead times.
MIM shines in high-volume manufacturing. The process requires higher upfront tooling costs, but these are offset by lower per-part costs in large production runs. If you need thousands or even millions of parts, MIM offers significant cost advantages.
Scalability of each process
Investment casting provides flexibility for scaling production. You can adjust batch sizes based on demand, but the process may not scale as efficiently as MIM for very large volumes.
MIM offers excellent scalability. Once the tooling is in place, you can produce large quantities of parts quickly and consistently. This makes it an ideal choice for industries requiring mass production of small, intricate components.
Understanding these differences in material options, part complexity, and production volume helps you make informed decisions. By evaluating your project’s specific needs, you can choose the process that aligns best with your goals.
Surface Finish and Post-Processing
Surface quality achievable
When evaluating surface quality, both investment casting and metal injection molding deliver impressive results. Investment casting produces parts with smooth and detailed surfaces. The ceramic mold used in this process captures fine details, resulting in a high-quality finish. This makes it suitable for components where aesthetics or minimal machining is essential.
Metal injection molding also achieves excellent surface finishes, especially for small and intricate parts. The injection process ensures uniformity, which reduces the need for additional smoothing. However, the surface quality may slightly vary depending on the material and sintering process.
Need for additional finishing steps
Investment casting often requires post-processing to meet specific requirements. You might need to perform machining, polishing, or coating to achieve tighter tolerances or enhanced surface properties. These additional steps can increase production time and costs but provide flexibility for customization.
Metal injection molding minimizes the need for post-processing. The parts typically come out of the mold with near-net shape and precise dimensions. In most cases, you can skip extensive finishing steps, which saves time and reduces costs. However, for certain applications, minor polishing or coating might still be necessary.
Both methods offer high-quality surfaces, but your choice depends on the level of finishing required and the complexity of your project.
Cost Efficiency
Initial setup costs
Initial setup costs differ significantly between investment casting and metal injection molding. Investment casting involves lower tooling costs, making it a cost-effective option for small production runs. The wax patterns and ceramic molds are less expensive to produce compared to MIM tooling.
Metal injection molding requires higher upfront costs due to the complex molds and feedstock preparation. The tooling process is more intricate, which increases the initial investment. This makes MIM more suitable for projects with high production volumes, where the costs can be spread across a larger number of parts.
Cost per part for small and large volumes
For small production volumes, investment casting offers better cost efficiency. The lower setup costs make it an economical choice for limited runs. However, as production scales up, the per-part cost remains relatively constant, which may not be ideal for large batches.
Metal injection molding excels in high-volume production. While the initial costs are higher, the per-part cost decreases significantly as the volume increases. This makes MIM a more economical option for manufacturing thousands or millions of parts. If your project demands mass production, MIM provides a clear cost advantage.
Understanding the cost dynamics of each process helps you align your budget with your production needs.
Applications
Typical industries and use cases for investment casting
Investment casting serves industries that require precision and durability. Aerospace companies use it for turbine blades and structural components. Automotive manufacturers rely on it for engine parts and exhaust systems. The medical field benefits from its ability to produce surgical instruments and implants. Its versatility also extends to art and jewelry, where intricate designs are essential.
Typical industries and use cases for metal injection molding
Metal injection molding finds its niche in industries needing small, complex parts. Electronics manufacturers use it for connectors and housings. The medical industry values it for producing surgical tools and orthodontic brackets. Firearms manufacturers depend on MIM for triggers and other small components. Its ability to produce high volumes of precise parts makes it indispensable in these fields.
By understanding the applications of each process, you can determine which method aligns with your industry and project requirements.
Advantages and Disadvantages of Investment Casting vs Metal Injection Molding
Advantages of Investment Casting
High precision and detail
Investment casting delivers exceptional precision and intricate details. You can achieve complex geometries and smooth surface finishes with this process. The ceramic mold captures even the finest features, making it ideal for parts requiring high accuracy. This level of detail reduces the need for additional machining, saving time and resources. If your project demands components with tight tolerances and aesthetic appeal, investment casting provides a reliable solution.
Wide range of material options
This process supports a broad selection of metals and alloys. You can work with stainless steel, carbon steel, aluminum, brass, bronze, and superalloys like cobalt and nickel. This versatility allows you to choose materials that meet specific performance requirements, such as strength, corrosion resistance, or heat tolerance. Whether you need durable aerospace components or decorative art pieces, investment casting offers the flexibility to match your material needs.
Disadvantages of Investment Casting
Higher costs for small production runs
Investment casting involves significant labor and material costs, especially for small batches. Creating wax patterns and ceramic molds requires time and expertise. For low production volumes, these costs can outweigh the benefits, making the process less economical. If your project involves limited quantities, you may need to explore alternative methods to manage expenses effectively.
Longer lead times
The investment casting process takes time due to its multiple steps. Creating molds, melting wax, and pouring molten metal require careful execution. These stages contribute to longer lead times compared to other manufacturing methods. If your project has tight deadlines, this process might not align with your schedule. Planning ahead becomes essential to accommodate the extended production timeline.
Advantages of Metal Injection Molding
Cost-effective for high volumes
Metal injection molding (MIM) excels in high-volume production. Once the tooling is complete, you can produce thousands or even millions of parts efficiently. The per-part cost decreases significantly as the volume increases, making MIM a cost-effective choice for large-scale manufacturing. If your project demands mass production, this process offers substantial savings over time.
Excellent for small, complex parts
MIM specializes in creating small, intricate components with tight tolerances. The injection molding process ensures consistent results, even for the most detailed designs. You can achieve near-net shape parts that require minimal post-processing. This capability makes MIM ideal for industries like electronics and medical devices, where precision and complexity are critical.
Understanding the advantages and disadvantages of investment casting vs metal injection molding helps you evaluate which process aligns with your project’s goals. By considering factors like precision, material options, cost, and production volume, you can make an informed decision.
Disadvantages of Metal Injection Molding
Limited material options
Metal injection molding (MIM) restricts your choice of materials compared to other manufacturing methods. The process primarily supports metals like stainless steel, low-alloy steel, titanium, and tungsten. While these materials offer excellent mechanical properties, they may not meet the specific needs of every project. For example, if your design requires aluminum or certain superalloys, MIM might not be the right fit.
This limitation arises because the feedstock used in MIM must combine fine metal powders with a binder. Not all metals can be processed into the fine powders required for this technique. You should carefully evaluate whether the available material options align with your project’s performance requirements before committing to MIM.
Higher initial tooling costs
MIM involves significant upfront costs due to the complexity of its tooling. The molds used in this process require precise engineering and high-quality materials to withstand the high pressures involved. These factors drive up the initial investment, making MIM less economical for small production runs or prototypes.
If your project demands only a limited number of parts, the high tooling costs may outweigh the benefits of MIM. You might find alternative methods, like investment casting, more cost-effective for smaller batches. However, for large-scale production, the higher initial costs of MIM often pay off through reduced per-part expenses over time.
Understanding these disadvantages helps you assess whether MIM aligns with your project’s needs. By considering material requirements and budget constraints, you can make an informed decision about the best manufacturing process for your goals.
Decision-Making Guide: Investment Casting vs Metal Injection Molding
Choosing between investment casting and metal injection molding requires careful evaluation of your project’s needs. By focusing on specific factors, you can determine which process aligns best with your goals.
Key Factors to Consider
Part complexity and design requirements
Evaluate the complexity of your part. If your design includes intricate geometries or fine details, metal injection molding (MIM) offers superior precision. MIM excels at producing small, complex components with tight tolerances. For larger parts or designs requiring smooth surface finishes, investment casting provides excellent results. The wax pattern technique in investment casting allows for detailed designs, but it may not match the precision of MIM for very small parts.
Production volume and budget
Consider your production volume and budget. Investment casting works well for low to medium production runs due to its lower initial tooling costs. It becomes less economical for high-volume manufacturing because of longer lead times. MIM, on the other hand, requires a higher upfront investment but offers significant cost savings for large-scale production. If you plan to produce thousands or millions of parts, MIM provides better cost efficiency over time.
Material properties and application needs
Assess the material requirements of your project. Investment casting supports a wider range of metals and alloys, including stainless steel, aluminum, and superalloys. This versatility makes it suitable for applications requiring specific material properties, such as high strength or heat resistance. MIM focuses on materials like stainless steel, titanium, and tungsten, which offer excellent mechanical properties. However, its material options are more limited compared to investment casting. Choose the process that matches your material and performance needs.
Understanding the differences between investment casting and metal injection molding helps you make informed manufacturing decisions. Each process offers unique advantages and limitations. Investment casting excels in material versatility and precision for larger parts, while metal injection molding shines in producing small, intricate components at high volumes. Aligning the manufacturing method with your project’s specific needs ensures efficiency and cost-effectiveness. For complex decisions, consulting experts can provide tailored solutions that match your goals and requirements.
FAQ
What is the main difference between investment casting and metal injection molding?
The primary difference lies in the manufacturing process and the type of parts they produce. Investment casting uses a wax pattern and ceramic mold to create larger, detailed components. Metal injection molding (MIM) involves injecting a metal powder-binder mixture into a mold, making it ideal for small, intricate parts with tight tolerances.
Which process is better for high-volume production?
Metal injection molding is better for high-volume production. It offers lower per-part costs once the tooling is complete, making it cost-effective for manufacturing thousands or millions of parts.
Can both methods handle complex designs?
Yes, both methods can handle complex designs, but their capabilities differ. Investment casting works well for intricate geometries in medium to large parts. MIM excels at producing extremely small and detailed components with superior precision.
What materials can I use with each process?
Investment casting supports a wide range of metals and alloys, including stainless steel, aluminum, brass, bronze, and superalloys like cobalt and nickel. MIM primarily uses materials like stainless steel, titanium, tungsten, and low-alloy steel. If your project requires a specific material, investment casting offers more options.
Which method provides better surface finishes?
Both methods deliver excellent surface finishes. Investment casting produces smooth surfaces due to the ceramic mold, making it suitable for aesthetic components. MIM achieves uniform finishes, especially for small parts, and often requires minimal post-processing.
Is one process more cost-effective than the other?
The cost-effectiveness depends on your production volume. Investment casting has lower initial tooling costs, making it economical for small production runs. MIM involves higher upfront costs but becomes more cost-efficient for large-scale manufacturing due to reduced per-part expenses.
How do I decide which process to use for my project?
To decide, evaluate your project’s requirements. Consider factors like part size, complexity, material needs, production volume, and budget. Investment casting suits larger parts and diverse materials, while MIM is ideal for small, intricate components in high volumes.
Are there size limitations for parts in these processes?
Yes, size limitations exist. Investment casting can produce larger components, making it suitable for medium to large parts. MIM is better for small parts due to the constraints of the sintering process, which limits the size of components it can handle.
Do both methods require post-processing?
Investment casting often requires post-processing steps like machining, polishing, or coating to meet specific requirements. MIM minimizes the need for post-processing, as parts typically come out of the mold with near-net shape and precise dimensions.
Which industries commonly use these processes?
Investment casting serves industries like aerospace, automotive, and medical equipment manufacturing, where precision and durability are essential. MIM is popular in electronics, medical devices, and firearms industries, where small, complex parts are in demand.