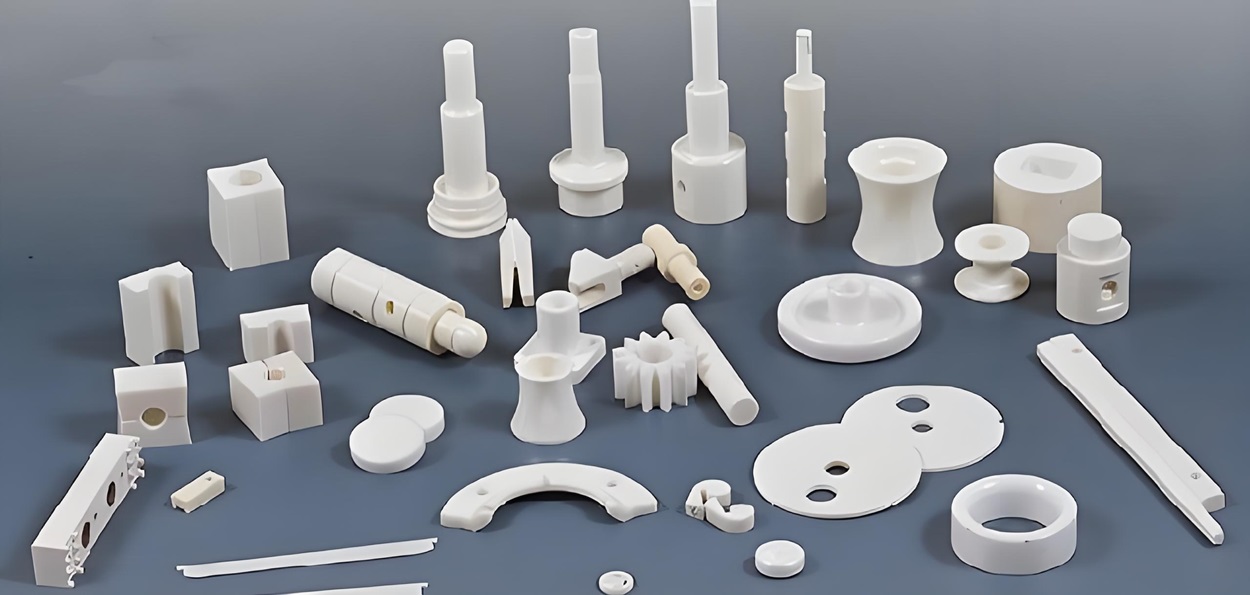
Powder metallurgy and metal ceramics are integral to contemporary manufacturing processes. This cutting-edge technology facilitates the creation of highly accurate components by compacting powdered materials into specific shapes. By merging the benefits of powder metallurgy and metal ceramics, it delivers exceptional properties such as improved strength, superior wear resistance, and enhanced thermal stability. Industries depend on this approach to produce high-performance parts that fulfill rigorous standards. The combination of efficiency and innovation provided by powder metallurgy and metal ceramics makes it essential in fields like automotive, aerospace, and electronics.
Key Takeaways
- Powder metallurgy is a cost-effective manufacturing process that creates components from powdered materials, ensuring high precision and minimal waste.
- The process allows for the production of complex geometries and tailored properties, making it ideal for industries like automotive, aerospace, and electronics.
- Key features of powder metallurgy include material versatility, high precision, enhanced properties, and efficient material usage, contributing to sustainability.
- Sintering is crucial for bonding particles in powder metallurgy, with specific techniques tailored for metals and ceramics to achieve optimal results.
- Post-processing techniques such as machining and heat treatment enhance the performance and appearance of components, ensuring they meet rigorous standards.
- Innovations like 3D printing and the development of sustainable materials are shaping the future of powder metallurgy, driving efficiency and environmental responsibility.
- Automation and AI are transforming powder metallurgy by improving production efficiency and quality control, ensuring consistent high-quality components.
What is Powder Metallurgy and How Does It Work?
Definition and Basic Principles
Powder metallurgy refers to a manufacturing process that involves creating components from powdered materials. This technique relies on compacting metal or ceramic powders into specific shapes, followed by a sintering process to bond the particles. The powder metallurgy process enables the production of parts with precise dimensions and tailored properties. It eliminates the need for extensive machining, making it an efficient and cost-effective approach.
The basic principles of powder metallurgy focus on transforming raw powders into solid components. The process begins with preparing fine powders, which are then mixed to achieve the desired composition. These powders undergo compaction under high pressure to form a green body, a term used to describe the unsintered part. Sintering, the final step, involves heating the compacted material to just below its melting point. This step strengthens the part by bonding the particles at a molecular level.
This process is advantageous for applications requiring complex geometries or unique material properties. It allows manufacturers to combine metals and ceramics, resulting in components with enhanced performance characteristics. Powder metallurgy and metal ceramics have become indispensable in industries that demand precision and durability.
Key Features of Powder Metallurgy and Metal Ceramics
Powder metallurgy and metal ceramics offer several distinctive features that set them apart from traditional manufacturing methods. These features make the process highly versatile and valuable across various sectors.
-
Material Versatility
The process accommodates a wide range of materials, including metals, ceramics, and their combinations. This flexibility allows manufacturers to create components with specific mechanical, thermal, or electrical properties. -
High Precision
Powder metallurgy ensures tight dimensional tolerances. The ability to produce near-net-shape components reduces the need for secondary machining, saving time and resources. -
Enhanced Properties
Components made through this process exhibit superior properties such as increased strength, wear resistance, and thermal stability. The integration of ceramics further enhances these characteristics, making the parts suitable for demanding applications. -
Efficient Material Usage
The process minimizes material waste. Unlike traditional methods, which often involve cutting or machining, powder metallurgy uses nearly all the raw material, contributing to sustainability. -
Scalability
Powder metallurgy supports mass production. Manufacturers can produce large quantities of identical components efficiently, making it ideal for industries like automotive and electronics.
These features highlight the importance of powder metallurgy and metal ceramics in modern manufacturing. The ability to create high-performance parts with minimal waste and maximum precision underscores its value in today’s industrial landscape.
The Processes of Powder Metallurgy
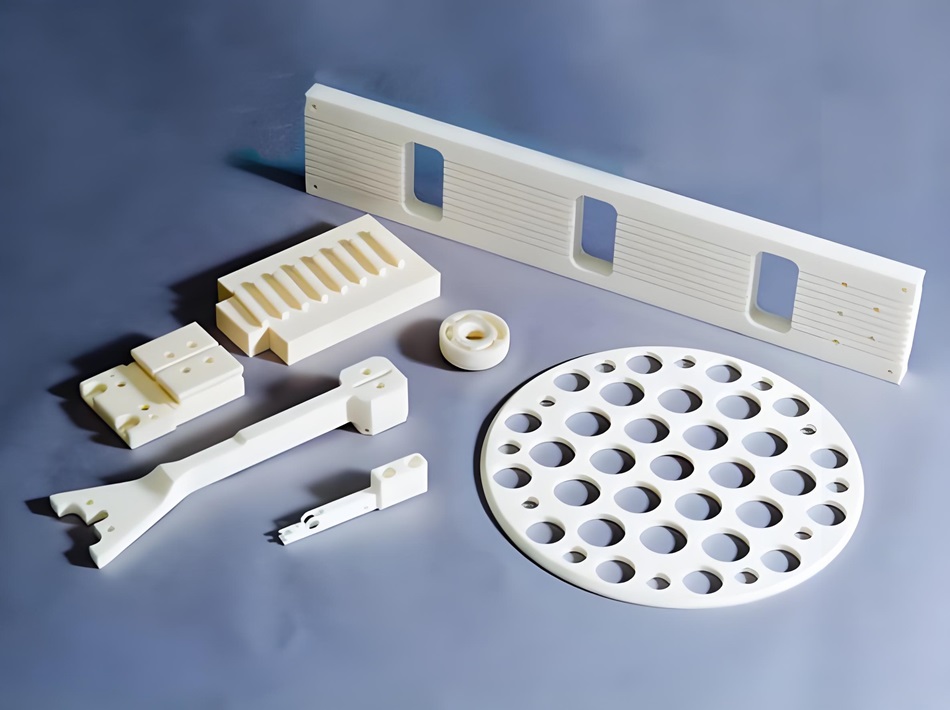
Powder Production
Methods of Powder Production (e.g., atomization, reduction, electrolysis)
Powder production serves as the foundation of powder metallurgy. Manufacturers employ various methods to create fine metal and ceramic powders, each tailored to specific material requirements. powder production serves
-
Atomization
Atomization involves breaking molten metal into fine droplets using high-pressure gas or water. This method produces powders with spherical shapes, which enhance flowability and packing density. -
Reduction
Reduction uses chemical reactions to extract metal powders from their oxides. This process often results in irregularly shaped particles, suitable for applications requiring high surface area. -
Electrolysis
Electrolysis generates metal powders by depositing them onto a cathode during an electrolytic reaction. This technique ensures high purity, making it ideal for specialized applications.
Each method offers unique advantages, allowing manufacturers to select the most appropriate technique based on the desired properties of the final component.
Characteristics of Metal and Ceramic Powders
The properties of metal and ceramic powders significantly influence the performance of the final product. Key characteristics include:
- Particle Size and Shape: Smaller particles with uniform shapes improve compaction and sintering outcomes.
- Purity: High-purity powders reduce the risk of defects in the finished part.
- Flowability: Powders with good flowability ensure consistent filling of molds during compaction.
- Density: High-density powders contribute to the strength and durability of the final component.
Understanding these characteristics helps manufacturers optimize the powder metallurgy process for both metals and ceramics.
Mixing and Blending
Importance of Homogeneity in Powders
Achieving homogeneity in powders is critical for producing components with consistent properties. Uneven distribution of materials can lead to weak points or defects in the final product. Homogeneous mixtures ensure uniformity in composition, enhancing mechanical and thermal performance.
Techniques for Mixing Metal and Ceramic Powders
Manufacturers use advanced techniques to mix metal and ceramic powders effectively:
- Mechanical Mixing: This method uses rotating drums or blades to blend powders. It ensures even distribution of particles but may require additional steps to prevent segregation.
- Ball Milling: Ball milling combines powders by grinding them together in a rotating container with hard balls. This technique achieves fine mixing and reduces particle size simultaneously.
- Spray Drying: Spray drying creates a homogeneous mixture by suspending powders in a liquid medium and then drying them into granules. This method is particularly effective for combining metals and ceramics.
These techniques ensure that the powders are ready for the next stage of the process.
Compaction
Shaping Techniques (e.g., uniaxial pressing, isostatic pressing)
Compaction transforms loose powders into solid shapes, known as green bodies. Two primary shaping techniques dominate this stage:
-
Uniaxial Pressing
Uniaxial pressing applies pressure in a single direction using a rigid die. This method is suitable for simple geometries and high-volume production. -
Isostatic Pressing
Isostatic pressing applies pressure uniformly from all directions using a flexible mold. This technique produces parts with complex shapes and consistent density.
Both methods ensure that the powders achieve the desired form and structure.
Achieving Desired Density and Shape
Compaction aims to achieve the optimal density and shape for the green body. High pressure compresses the powders, reducing porosity and increasing strength. Proper tooling and precise control of pressure ensure that the component meets dimensional and structural requirements. This step lays the groundwork for successful sintering and finishing.
Sintering
The Role of Heat in Bonding Particles
Sintering plays a critical role in powder metallurgy and metal ceramics. This process involves heating compacted powders to a temperature just below their melting point. The heat causes the particles to bond at their contact points, forming a solid and cohesive structure. During sintering, diffusion occurs at the atomic level, which strengthens the material and reduces porosity. The controlled application of heat ensures that the component achieves the desired mechanical properties without losing its shape or dimensions. sintering plays a critical
Manufacturers carefully monitor the sintering temperature and duration to optimize the bonding process. Excessive heat can distort the part, while insufficient heat may result in weak bonds. The success of this stage depends on precise control, which ensures that the final product meets performance and quality standards.
Differences in Sintering for Metals and Ceramics
Sintering methods differ significantly for metals and ceramics due to their distinct material properties. Metals typically require lower sintering temperatures compared to ceramics. The metallic particles bond through solid-state diffusion or partial melting, which enhances their ductility and strength. In contrast, ceramics demand higher temperatures to achieve densification. The process for ceramics often involves grain growth and the elimination of pores, resulting in a hard and brittle structure.
The atmosphere during sintering also varies. Metals often require a reducing or inert atmosphere to prevent oxidation, while ceramics may need specific conditions to maintain their chemical stability. These differences highlight the need for tailored sintering techniques to achieve optimal results for each material type.
Finishing
Common Post-Processing Techniques
Finishing processes refine the properties and appearance of components produced through powder metallurgy and metal ceramics. These techniques address surface imperfections, improve dimensional accuracy, and enhance functionality. Common post-processing methods include:
- Machining: Removes excess material to achieve precise dimensions and smooth surfaces.
- Heat Treatment: Alters the microstructure to improve hardness, strength, or toughness.
- Coating: Applies protective or functional layers, such as corrosion-resistant or wear-resistant coatings.
- Polishing: Enhances surface finish for aesthetic or functional purposes.
Each technique serves a specific purpose, ensuring that the final product meets the required specifications and performs reliably in its intended application.
Enhancing Properties Through Finishing
Finishing processes not only improve the appearance of components but also enhance their performance. Heat treatment, for example, increases the strength and durability of metal parts. Coatings provide additional protection against environmental factors, such as corrosion or abrasion. Polishing reduces surface roughness, which minimizes friction and wear in moving parts.
Manufacturers select finishing techniques based on the component’s application and material properties. Proper finishing ensures that the product delivers optimal performance, extending its lifespan and maintaining its quality over time.
Applications of Powder Metallurgy in Metal Components
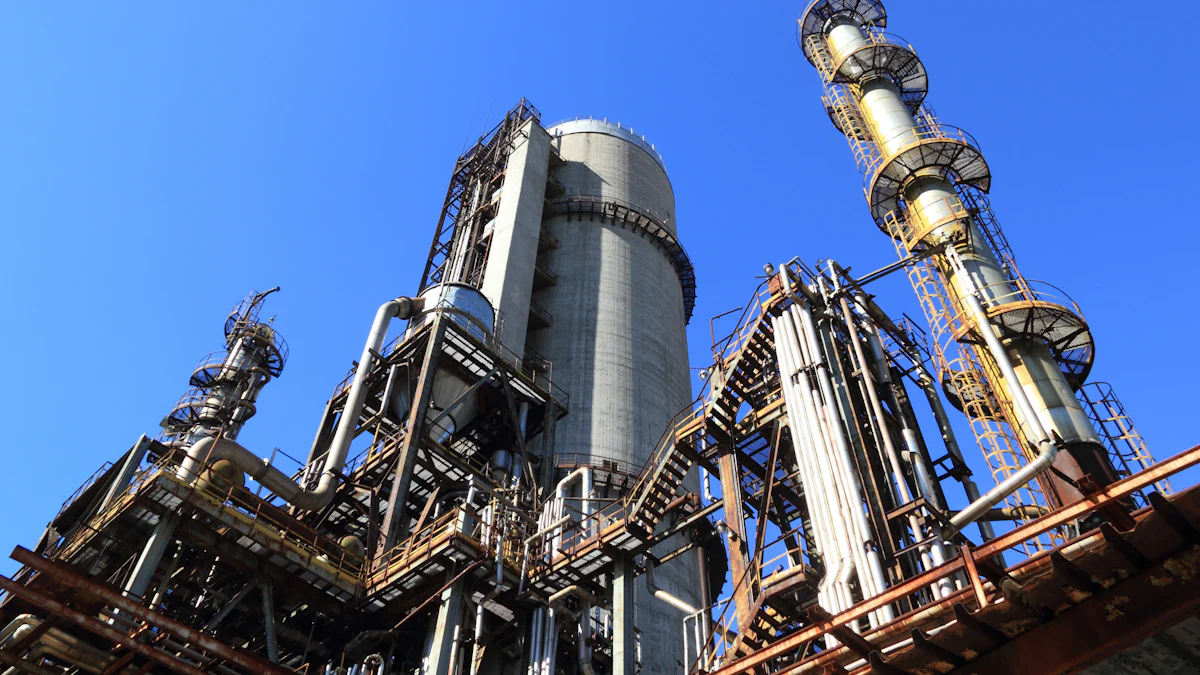
Automotive Industry
Engine Components and Structural Parts
Powder metallurgy plays a vital role in the automotive industry. Manufacturers rely on this process to produce engine components and structural parts with high precision and durability. The ability to create complex geometries makes powder metallurgy ideal for crafting intricate engine parts such as connecting rods, camshaft lobes, and gears. These components benefit from enhanced wear resistance and strength, ensuring reliable performance under extreme conditions.
Structural parts, including brackets and housings, also benefit from powder metallurgy. The process allows for the production of lightweight yet robust components, which contribute to improved fuel efficiency and reduced emissions. By minimizing material waste, powder metallurgy aligns with the automotive industry’s push toward sustainability. Its scalability further supports the mass production of high-quality parts, meeting the demands of modern vehicle manufacturing.
Aerospace Industry
High-Strength and Heat-Resistant Alloys
The aerospace industry demands materials that can withstand high stress and extreme temperatures. Powder metallurgy addresses these requirements by enabling the production of high-strength and heat-resistant alloys. Components such as turbine blades, jet engine parts, and structural elements benefit from the superior properties achieved through this process.
Powder metallurgy allows for precise control over material composition, resulting in alloys with tailored characteristics. This capability ensures that aerospace components maintain their integrity under harsh operating conditions. The integration of ceramics into metal components further enhances thermal stability and wear resistance, making them suitable for critical applications. The process also supports the creation of lightweight parts, which are essential for improving fuel efficiency and reducing overall aircraft weight.
Electronics Industry
Magnetic and Conductive Components
In the electronics industry, powder metallurgy facilitates the production of magnetic and conductive components with exceptional performance. Manufacturers use this process to create parts such as soft magnetic cores, inductors, and connectors. These components require precise material properties to ensure optimal functionality in electronic devices.
Powder metallurgy enables the production of materials with high magnetic permeability and low electrical resistance. This capability ensures efficient energy transfer and minimal power loss in electronic systems. The process also supports the creation of miniaturized components, which are essential for modern electronics. By combining metals and ceramics, manufacturers can achieve unique properties that enhance the performance and reliability of electronic devices.
The versatility of powder metallurgy and metal ceramics makes it indispensable across industries. Its ability to produce high-performance components with tailored properties ensures its continued relevance in automotive, aerospace, and electronics applications.
Applications of Powder Metallurgy in Ceramic Components
Medical Applications
Bioceramics for Implants and Dental Uses
Powder metallurgy enables the production of bioceramics, which play a critical role in modern medicine. These materials exhibit exceptional biocompatibility, making them ideal for implants and dental applications. Manufacturers use powder metallurgy enables to create components such as artificial joints, bone grafts, and dental crowns. These bioceramics integrate seamlessly with human tissue, promoting healing and reducing the risk of rejection.
The process allows precise control over material properties, ensuring that implants meet stringent medical standards. For example, hydroxyapatite, a common bioceramic, mimics the composition of natural bone. This similarity enhances its ability to bond with surrounding tissue. Dental ceramics, produced through this method, offer durability and aesthetic appeal, providing patients with long-lasting and natural-looking solutions. Powder metallurgy ensures that bioceramics deliver consistent quality and performance in critical medical applications.
Industrial Applications
Wear-Resistant Tools and High-Temperature Insulators
Industries rely on powder metallurgy to produce ceramic components that withstand extreme conditions. Wear-resistant tools, such as cutting blades and grinding wheels, benefit from the hardness and durability of ceramics. These tools maintain their performance even under high stress, reducing downtime and improving efficiency in manufacturing processes.
High-temperature insulators, another key application, protect equipment and systems in environments with extreme heat. Ceramics produced through powder metallurgy exhibit excellent thermal stability and low thermal conductivity. These properties make them indispensable in industries such as aerospace, where components must endure intense heat without compromising functionality. The ability to tailor ceramic properties ensures that these tools and insulators meet the specific demands of industrial applications.
Energy Sector
Fuel Cells, Batteries, and Thermal Barrier Coatings
The energy sector leverages powder metallurgy to develop advanced ceramic components for sustainable technologies. Fuel cells, which convert chemical energy into electricity, rely on ceramic electrolytes for efficient ion conduction. These ceramics enhance the performance and lifespan of fuel cells, supporting the transition to cleaner energy sources.
Batteries also benefit from ceramic components, particularly in solid-state designs. Ceramic separators improve safety and energy density, addressing challenges associated with traditional battery technologies. Thermal barrier coatings, another application, protect turbine blades and other components in power generation systems. These coatings, produced through powder metallurgy, resist high temperatures and reduce thermal fatigue, extending the lifespan of critical equipment.
Powder metallurgy and metal ceramics continue to drive innovation in the energy sector. Their versatility and performance enable the development of technologies that support sustainability and efficiency.
Advantages of Powder Metallurgy and Metal Ceramics
Material Efficiency
Minimal Waste and Recyclability
Powder metallurgy and metal ceramics excel in material efficiency. This process uses nearly all the raw material, leaving minimal waste compared to traditional manufacturing methods. By compacting powders directly into the desired shape, manufacturers avoid the excessive material loss often associated with machining or cutting. This efficiency not only reduces costs but also supports sustainable practices in production.
Recyclability further enhances the appeal of this technology. Manufacturers can reuse leftover powders from previous processes, ensuring that resources are not wasted. This capability aligns with the growing emphasis on environmental responsibility in modern industries. By minimizing waste and promoting minimal waste and recyclability, powder metallurgy and metal ceramics contribute to a more sustainable manufacturing ecosystem.
Design Flexibility
Complex Geometries and Tailored Properties
The design flexibility offered by powder metallurgy and metal ceramics sets it apart from conventional methods. This process allows manufacturers to create components with intricate geometries that would be challenging or impossible to achieve through traditional techniques. The ability to produce near-net-shape parts eliminates the need for extensive post-processing, saving time and resources.
Tailoring material properties is another significant advantage. By blending different powders, manufacturers can customize components to meet specific performance requirements. For example, combining metals with ceramics can enhance wear resistance, thermal stability, or electrical conductivity. This level of customization ensures that the final product performs optimally in its intended application. The versatility of this process makes it invaluable across industries that demand precision and tailored material properties.
Cost-Effectiveness
Lower Costs for High-Volume Production
Powder metallurgy and metal ceramics offer a cost-effective solution for high-volume production. The process supports mass manufacturing by enabling the creation of identical components with consistent quality. This scalability reduces per-unit costs, making it an attractive option for industries like automotive and electronics.
The elimination of extensive machining further contributes to cost savings. By producing near-net-shape parts, manufacturers reduce labor and material expenses. Additionally, the efficient use of raw materials minimizes waste, lowering overall production costs. These factors combine to make powder metallurgy and metal ceramics a financially viable choice for large-scale operations.
Limitations of Powder Metallurgy
Size and Shape Constraints
Challenges with Large or Complex Components
Powder metallurgy faces limitations when producing large or highly intricate components. The compaction process, which relies on applying pressure to powders, struggles to maintain uniform density in oversized parts. Uneven density can lead to weak points, reducing the structural integrity of the final product. This issue becomes more pronounced as the size of the component increases.
Complex geometries also present challenges. While powder metallurgy excels at creating near-net-shape parts, certain intricate designs may require additional machining or post-processing. Features such as deep cavities or thin walls can be difficult to achieve due to the limitations of the compaction and sintering processes. These constraints make powder metallurgy less suitable for applications requiring very large or highly detailed components.
Material Limitations
Restricted to Certain Alloys and Ceramics
The range of materials compatible with powder metallurgy remains limited. Not all metals and ceramics can be processed effectively using this method. Some materials, such as those with high melting points or poor sintering characteristics, pose significant challenges. For example, refractory metals like tungsten require extremely high sintering temperatures, which can complicate the manufacturing process.
Certain alloys also exhibit poor flowability or compaction properties, making them unsuitable for powder metallurgy. Additionally, the integration of metals and ceramics, while beneficial in many cases, may not always yield the desired properties due to differences in thermal expansion or bonding behavior. These material restrictions limit the versatility of powder metallurgy in some specialized applications.
High Initial Costs
Expensive Equipment and Expertise Required
The initial investment in powder metallurgy can be prohibitively high. Specialized equipment, such as atomizers for powder production and high-pressure presses for compaction, requires significant capital. Sintering furnaces, often designed to operate under controlled atmospheres, add to the overall cost. These expenses make powder metallurgy less accessible for small-scale manufacturers or low-volume production runs.
Expertise also plays a critical role in the success of powder metallurgy. Skilled professionals must oversee each stage of the process, from powder preparation to sintering. The need for technical knowledge and experience increases operational costs, particularly for complex or high-precision components. While powder metallurgy offers long-term cost savings for mass production, the high upfront costs can deter its adoption in certain industries or projects.
Innovations and Future Trends in Powder Metallurgy
Advances in Additive Manufacturing
Integration with 3D Printing
Additive manufacturing, often referred to as 3D printing, has revolutionized powder metallurgy. This technology enables the creation of complex components by layering powdered materials and fusing them with precision. The integration of 3D printing into powder metallurgy has opened new possibilities for producing intricate designs that were previously unattainable.
Manufacturers now use 3D printing to fabricate prototypes and functional parts directly from digital models. This approach eliminates the need for traditional molds or dies, reducing lead times and production costs. The ability to print components with internal structures, such as lattice designs, enhances performance while minimizing material usage. These advancements have made additive manufacturing a cornerstone of innovation in powder metallurgy.
Industries such as aerospace and healthcare benefit significantly from this integration. For example, aerospace engineers use 3D printing to produce lightweight yet durable parts for aircraft. In the medical field, custom implants and prosthetics are now possible, tailored to individual patients. The combination of powder metallurgy and 3D printing continues to push the boundaries of design and functionality.
Development of New Materials
Nano-Powders and Sustainable Powders
The development of advanced materials has become a focal point in powder metallurgy. Nano-powders, characterized by their ultra-fine particle size, offer unique properties that enhance the performance of components. These powders improve sintering efficiency, resulting in parts with higher density and superior mechanical strength. Nano-powders also enable the creation of materials with enhanced thermal and electrical conductivity.
Sustainability has also emerged as a critical consideration in material development. Researchers are exploring eco-friendly powders derived from recycled materials or renewable sources. These sustainable powders reduce the environmental impact of manufacturing processes while maintaining high performance. For instance, recycled metal powders now serve as viable alternatives for producing high-quality components.
The combination of nano-powders and sustainable materials addresses both performance and environmental concerns. This dual focus ensures that powder metallurgy remains relevant in industries striving for innovation and sustainability.
Automation and AI in Manufacturing
Smart Processes and Quality Control
Automation and artificial intelligence (AI) are transforming the landscape of powder metallurgy. Smart manufacturing processes now incorporate advanced robotics and AI-driven systems to enhance efficiency and precision. Automated equipment handles tasks such as powder mixing, compaction, and sintering with minimal human intervention. This reduces errors and ensures consistent quality across production runs.
AI plays a pivotal role in quality control. Machine learning algorithms analyze data from sensors and cameras to detect defects in real time. These systems identify issues such as uneven density or surface imperfections, allowing manufacturers to address problems before they escalate. Predictive maintenance, powered by AI, ensures that equipment operates at peak performance, minimizing downtime.
The adoption of automation and AI has streamlined production workflows and improved product reliability. These technologies enable manufacturers to meet the growing demand for high-quality components while maintaining cost-effectiveness. As automation and AI continue to evolve, their impact on powder metallurgy will only grow stronger.
Powder metallurgy stands as a cornerstone of modern manufacturing, offering precision and efficiency in producing components. Its ability to create both metal and ceramic parts with tailored properties highlights its versatility. Industries benefit from its capacity to meet demanding performance standards while minimizing waste.
The process continues to evolve, driving innovation through advancements like additive manufacturing and sustainable materials. Its potential to enhance sustainability and enable groundbreaking designs positions it as a vital technology for the future. Powder metallurgy remains indispensable for industries seeking high-quality, cost-effective, and environmentally conscious solutions.