Helical Gears
Helical Gear is a cylindrical gear with helical teeth. Helical gears can withstand more loads than spur gears and work more quietly, and they are widely used in industry. Helical gear transmission is a widely used and concerned mechanical transmission mode. The transmission device plays a vital role in modern engineering. They are used to transmit power and motion to different mechanical parts, enabling a variety of work tasks. Among many transmission devices, helical gear transmission has been widely used in industry, automobile, aerospace, and other fields for its unique structural characteristics and excellent performance.
More resources
powder metallurgy process | Gear Manufacturing | Automotive Gears
Structural characteristics of helical gear transmission
Helical gear is a common gear transmission device, its basic structure includes two main parts: helical gear and helical gear shaft. The helical gear consists of many helical teeth in the shape of a bevel, which is inclined at an Angle to the drive shaft. The helical gear shaft connects the helical gear and is fixed in the transmission by bearings.
The working principle of Helical gears
The working principle of helical gear drive is based on the meshing and rolling of the bevel helical teeth. When the helical gear rotates, the contact point between the helical teeth and the adjacent teeth gradually moves from the rim to the top of the teeth, so that the pressure between the gears gradually increases. This meshing mode has good contact performance and transmission smoothness.
Because of the bevel shape of the helical teeth, the helical gear generates axial and radial forces in the transmission process, which put forward certain requirements for the support and stability of the bearing and transmission device. Therefore, the effects of these forces need to be considered when designing and manufacturing spiral gear drives to ensure the reliability and stability of the drive.
Helical gears advantages
- High load capacity: The bevel profile of the helical gear enables it to withstand large radial and axial loads and is suitable for applications that transfer high torques and loads.
- Smooth transmission: Due to the spiral teeth rolling and bevel mesh, spiral gear transmission has low vibration and noise levels, smooth and reliable transmission.
- High transmission efficiency: The rolling engagement mode of helical gears reduces the sliding between gears, thereby increasing transmission efficiency.
Disadvantages of helical gears
- More difficult to manufacture: The manufacturing of spiral gears is relatively difficult, requiring special processing technology and equipment to create precise bevel teeth. This increases manufacturing costs and production cycles.
- Axial and radial forces: Due to the bevel shape of the helical teeth, axial and radial forces are generated during the transmission process. These forces impose additional loads on the transmission and bearings, requiring special designs and support structures to counteract these forces.
- Need lubrication: helical gear drives need adequate lubrication during operation to reduce friction and wear. Proper lubrication can extend the service life of the gear but also increase the workload of maintenance and management.
- Space limitation: helical gear drives have a large volume compared to other gear drive structures. This makes the use of helical gear drives in space-limited applications more challenging, requiring proper design and layout.
- High cost: Due to manufacturing complexity and special process requirements, the manufacturing cost of spiral gear drives is relatively high. This may limit its widespread use in some applications.
Helical gear application
- Industrial machinery: helical gear transmission is widely used in industrial machinery. They are commonly used in equipment and machinery that require high torque transfer and precise motion control. For example, equipment such as conveyors, mixers, crushers, and presses in factories often use helical gear transmission for power transmission and motion control. Helical gear drives are widely used in the field of industrial machinery because of their high transmission efficiency, high torque transmission capacity, and low noise level.
- Automotive industry: helical gear transmission also has important applications in the automotive industry. In the automotive transmission system, helical gear transmission is widely used in the transmission and transmission box to transfer engine power to the wheels and achieve different speeds and torque transformations. Helical gear transmission has the advantages of high reliability, high transmission efficiency, and long life in the automotive field, which can meet the requirements of power transmission in automobiles.
- Aerospace field: In the aerospace field, helical gear transmission is widely used in aircraft and spacecraft landing gear, steering gear, wing adjustable devices, and other systems. Helical gear transmission can provide reliable power transmission and precise motion control, and adapt to complex working environments and high performance requirements. In addition, the helical gear drive also has the characteristics of a compact structure, lightweight, shock and vibration resistance, making it an important transmission device in the aerospace field.
- Application cases in other fields: In addition to industrial machinery, automotive, and aerospace fields, spiral gear drives are also widely used in many other fields. For example, they are used in medical equipment, robotics, the energy sector, the Marine industry, metallurgical equipment, etc. These areas have different requirements for the transmission system, but the helical gear drive can meet the transmission needs of different areas due to its flexibility and reliability.
Helical gear design
In the design of helical gear transmission, it is very important to select the appropriate gear parameters. The following are the key gear parameters that need to be selected according to the specific application
- Module: Module refers to the ratio of the number of gear teeth to the diameter of the gear, which affects the size and shape of the gear. The choice of modulus should take into account the transmission torque, transmission ratio, working environment, and other factors.
- Number of Teeth: The number of teeth determines the size and transmission ratio of the gear. According to the actual needs, choose the right number of teeth to meet the transmission needs and space constraints.
- Tooth Profile: The tooth profile of the spiral gear is different from that of the traditional straight gear, with a certain tilt Angle and spiral Angle. Choosing the right tooth shape can improve transmission efficiency and reduce noise.
- Face Width: Tooth width refers to the width of the tooth surface of the gear, which is crucial for transmitting torque and distributing load. The selection of tooth width should take into account factors such as torque transmission capacity, strength, and heat dispersion.
The manufacturing process of spiral gears is crucial to their quality and performance. Here are some common gear manufacturing processes:
- Casting: Casting is a common process for manufacturing large and complex shaped gears. The desired gear shape is obtained by injecting molten metal into the mold, which is then cooled and cured.
- Forging: Forging is the process of changing the shape of the metal by heating it to a malleable temperature and applying pressure. This process can produce high-strength and high-precision gears.
- Machining: Machining is a process in which metal materials are removed by cutting tools to obtain the desired shape. Common cutting processes include milling, turning, grinding, and so on.
When selecting the manufacturing process, factors such as the size, material and accuracy requirements of the gear need to be taken into account to ensure that high-quality gear is manufactured.
The future development trend of helical gear
- Intelligence and automation: With the development of industrial automation, spiral gear transmission will also develop in the direction of intelligence. Intelligent helical gear drives can be monitored and controlled by sensors and control systems to achieve automated operation and maintenance. For example, sensors can be used to monitor the temperature, vibration, and wear of gears to adjust and maintain the drivetrain on time. The intelligent helical gear drive can also be connected to other devices and systems for collaborative work and remote monitoring.
- Energy efficiency and environmental protection: Future helical gear drives will pay more attention to energy efficiency and environmental performance. By optimizing the design and manufacturing process, the friction and energy loss of the transmission system are reduced, and the transmission efficiency is improved. At the same time, the use of advanced lubrication technology and environmentally friendly lubricants, reduce the heat and wear generated by friction and reduce energy consumption and environmental pollution.
- Innovation in materials and manufacturing technology: With the continuous progress of materials science and manufacturing technology, the future of spiral gear transmission will use more advanced materials and manufacturing processes. For example, the use of high-strength, low-friction, and wear-resistant materials, such as advanced alloys and ceramics, improves gear durability and transmission efficiency. In addition, the use of advanced CNC machining and forming technology can achieve higher precision and more complex gear shapes, improving the performance and reliability of the transmission system.
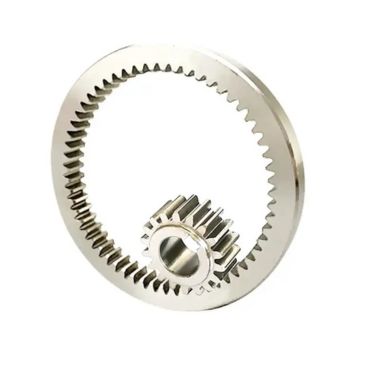
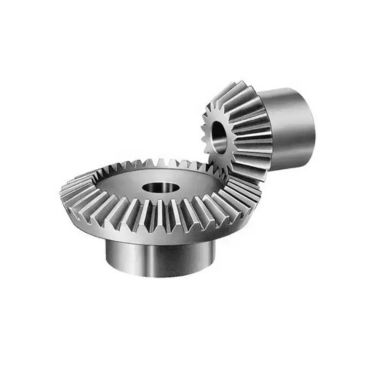
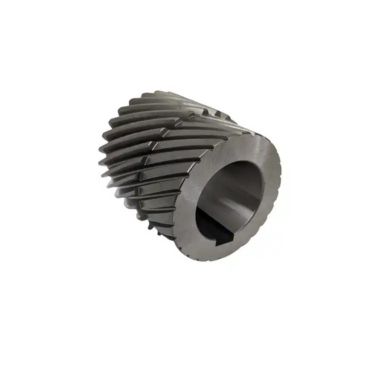
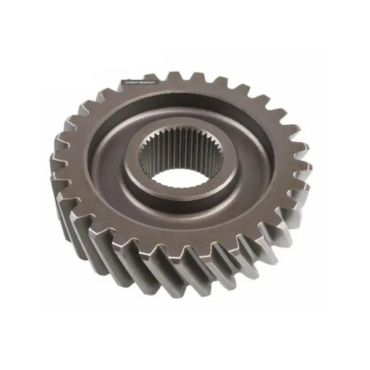
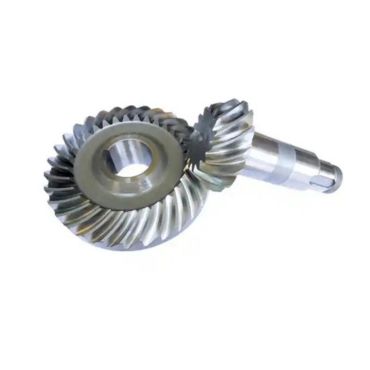
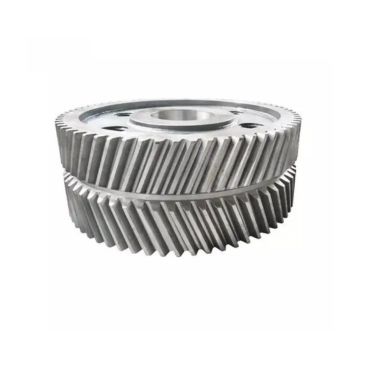
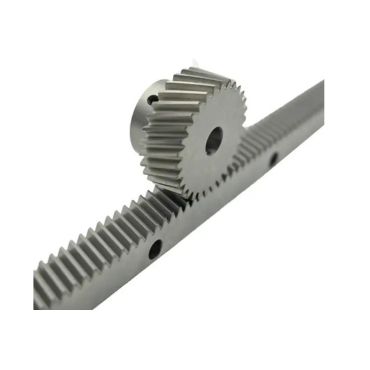
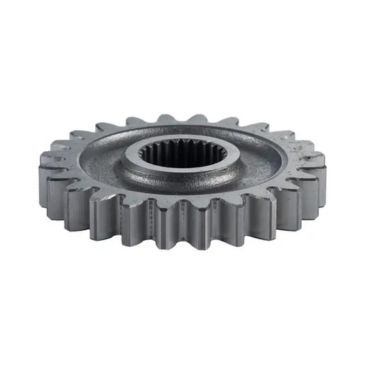
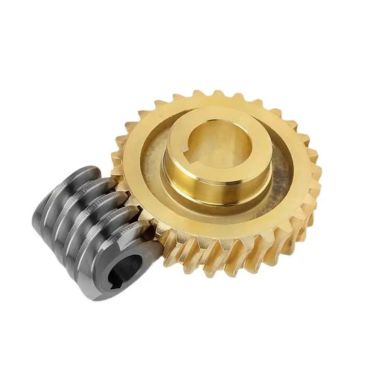
JH MIM is a leading factory specializing in gear production. We have advanced equipment and a team of technical experts dedicated to providing high-quality, high-precision gear products. We can achieve precision manufacturing of complex gears, ensuring product reliability and superior performance.
Whether you need drivetrains, machinery, or gears for the automotive industry, we can provide customized solutions based on your specific needs. Our gear products undergo strict quality control and testing to ensure their durability and reliability and can meet the requirements of various industrial fields.
As a JH MIM customer, you will benefit from the experience of our professional team and superior process flow. We are committed to establishing long-term cooperative relationships with our customers and providing a full range of technical support and quality after-sales service. No matter the size of your project, we will meet your needs in an efficient, flexible, and innovative manner and contribute a reliable gear solution to your business success.
When you choose JH MIM, you get top-notch gear products, reliable delivery times, and an excellent customer experience. Let our team of professionals help you achieve your business goals and drive your success.