1. Feedstock Compounding
The Metal Injection Molding (MIM) process needs to prepare the raw material Feedstock first. It is made by mixing fine metal powder with a diameter of less than 20µ and binders, such as waxes and different polymers, at a ratio of about 60:40 (the specific mixing ratio is determined according to the material of the metal powder and the shrinkage rate). The mixture is placed in advanced mixing equipment and heated to a temperature that causes the binder to melt, allowing the metal powders to mix thoroughly. After cooling, the raw material is pelletized into pellets, which makes the raw material Feedstock. This process is important in order to ensure the quality and consistency of the products produced.
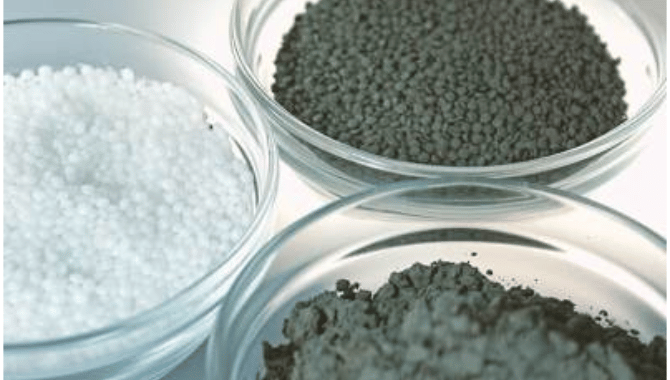
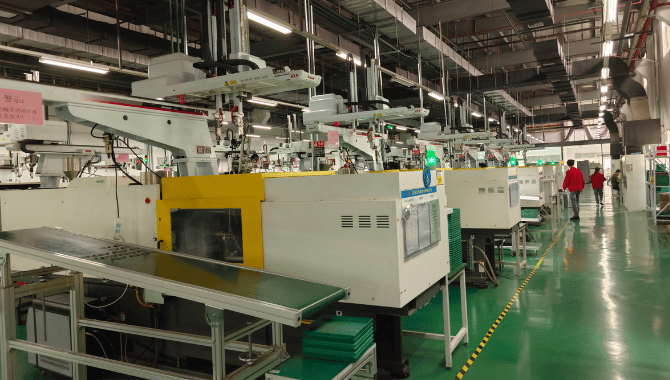
2. Injection Molding
Similar to the method of plastic injection molding, the feedback passes through the feed port of the injection molding machine, and when heated to about 200°, the feedstock will melt into a fluid state and be injected into the mold under high pressure. After cooling, the product is ejected from the molding to form a “green part”
3.Debinding
After injection molding, “green parts” will enter the next step, the degreasing process. Metal injection molding adopts two main methods of catalytic method and the solvent method to remove the binder, and the product is in the degreasing furnace for about 12 hours to remove the most Part adhesive. The MIM parts after this process, we call “brown parts”.
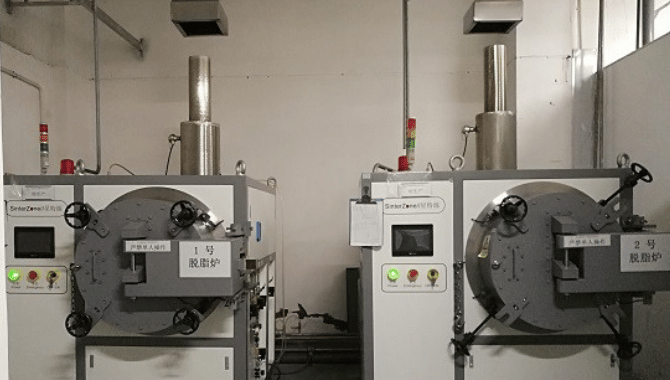
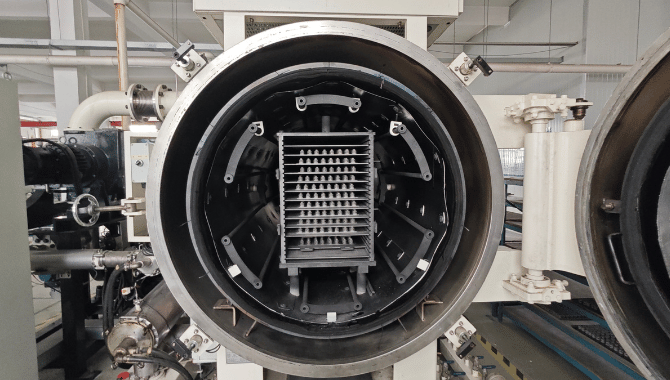
4.Sintering Process – Sintered Parts
The degreased parts “brown parts” are placed on the ceramic spacers and loaded into the sintering furnace. The brown part is heated to close to its melting point in a nitrogen-filled protective atmosphere. All remaining binders are completely removed. The high temperature causes the metal particles to be bonded together. The part shrinks and densifies, developing the final strength and shape of the metal part. Usually the shrinkage rate is around 20%.
JH MIM, which started as MIM, has established a sound product ecology by investing in advantageous enterprises in related industries. Now it can provide customers with one-stop services such as PM, Die Casting, CNC, and 3D printing. It is equipped with integrated assembly capabilities and the quality of quality suppliers mentioned above. Please click the link below for more detailed information.
Resource:
MIM Process – Source: Wikipedia
Yes, this is a routine operation for most companies before making an inquiry.
We have metal 3D printing equipment and can provide sample 3D printing.
3D drawings allow engineers to better understand the structure of the product, and 2D documents can provide more information, including materials, tolerances, surface treatment, etc. More detailed information is conducive to more accurate quotation by engineers.
In the case of detailed inquiry drawings and information, it usually only takes 2-3 days for us to give you a detailed quotation, including product price and mold price.
After confirming the order, we usually take 5-7 days to prepare the DFM report of the product. After confirmation, we spend 25 days to complete the mold, and provide T1 samples to customers for testing in the following 10-15 days.
If there is a problem with the test, we will re-sample it for free based on the feedback and provide a suitable sample.
MIM products MOQ 2000 PCS,
CNC products MOQ 2000 PCS,
Alu die casting, MOQ 2000 PCS
PM product MOQ 5000 PCS
Typically, the lead time for processing and submitting samples is 30 days. However, according to the order quantity and special requirements of customers, we can extend or shorten the delivery cycle accordingly.
1-year product warranty
World-class testing equipment
30+QC Workers
Key sizes 100% checking before shipment
ISO9001+IATF16949
Usually T/T is used as the payment method
Mold: 50% deposit, 50% payment after confirming the sample.
Bulk production: 30% deposit, 30% see bill of lading Copy, pay 70% balance.