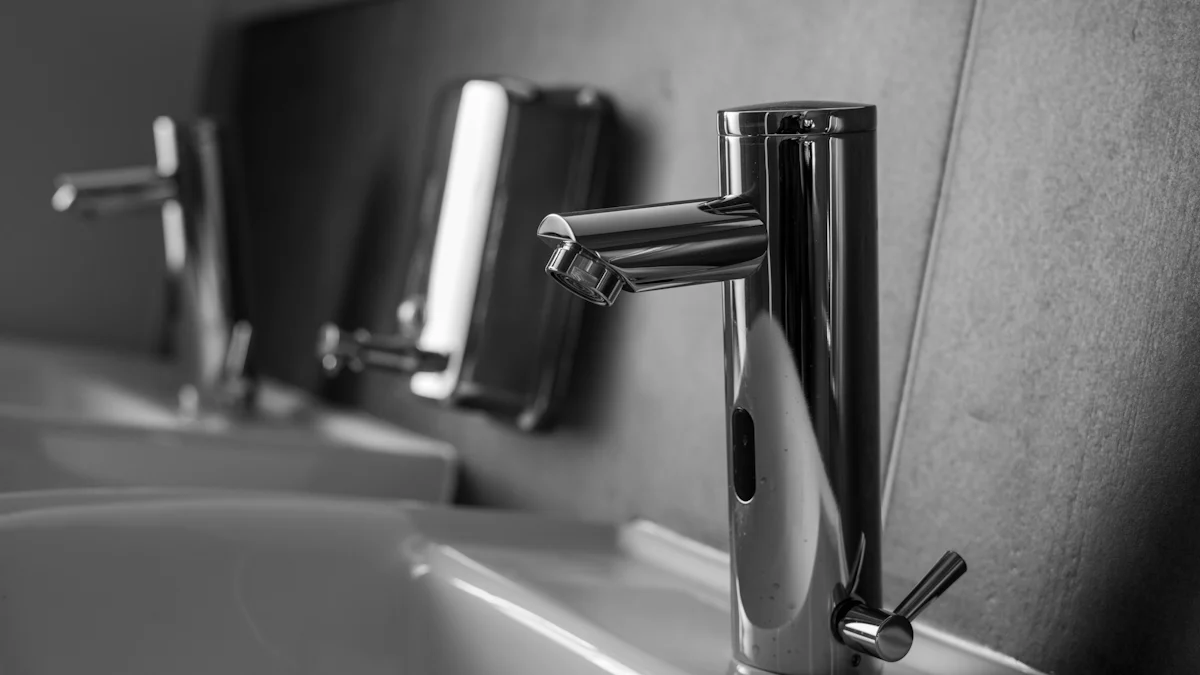
When I compare 316-vs-321-stainless-steel, I notice distinct differences in their chemical compositions and mechanical properties. 316 stainless steel contains higher nickel content, ranging from 10-14%, while 321 stainless steel has a slightly lower nickel content of 9-12%. The chromium content in 321 is higher, between 17-19%, compared to 316’s 16-18%. These variations influence their performance in different environments. Choosing the right stainless steel is crucial for specific applications. The decision impacts durability, corrosion resistance, and cost-effectiveness, making it essential to understand these differences thoroughly.
Key Takeaways
- 316 stainless steel is ideal for environments rich in chlorides, making it perfect for marine and chemical processing applications due to its superior corrosion resistance.
- 321 stainless steel excels in high-temperature settings, making it suitable for aerospace and automotive industries where thermal stability is crucial.
- The presence of molybdenum in 316 enhances its resistance to pitting and crevice corrosion, ensuring longevity in harsh conditions.
- Titanium in 321 stabilizes the alloy, preventing carbide precipitation during welding, which enhances its resistance to intergranular corrosion.
- When choosing between the two, consider the specific application requirements, such as exposure to corrosive environments or high temperatures.
- While 316 stainless steel generally has a higher cost due to its composition, 321 offers a more cost-effective solution for high-temperature applications.
- Understanding the unique properties of each stainless steel type ensures optimal performance and longevity in engineering projects.
Chemical Composition
Understanding the chemical composition of stainless steel is crucial when comparing 316-vs-321-stainless-steel. Each type has unique elements that define its properties and suitability for various applications.
316 Stainless Steel Composition
I find 316 stainless steel particularly interesting due to its robust composition. It contains:
- Chromium: 16-18%
- Nickel: 10-14%
- Molybdenum: 2-3%
- Carbon: 0.03%
The presence of molybdenum significantly enhances its corrosion resistance, especially in chloride-rich environments. This makes 316 stainless steel ideal for use in highly corrosive settings like food processing plants and medical facilities. Its ability to maintain strength at high temperatures further adds to its versatility.
321 Stainless Steel Composition
On the other hand, 321 stainless steel offers a different set of advantages. Its composition includes:
- Chromium: 17-19%
- Nickel: 9-12%
- Titanium: Added to stabilize the alloy
The addition of titanium is a game-changer. It prevents carbide precipitation during welding or exposure to high temperatures, which enhances its resistance to intergranular corrosion. This makes 321 stainless steel a preferred choice for applications requiring excellent weldability and high-temperature stability.
Corrosion Resistance
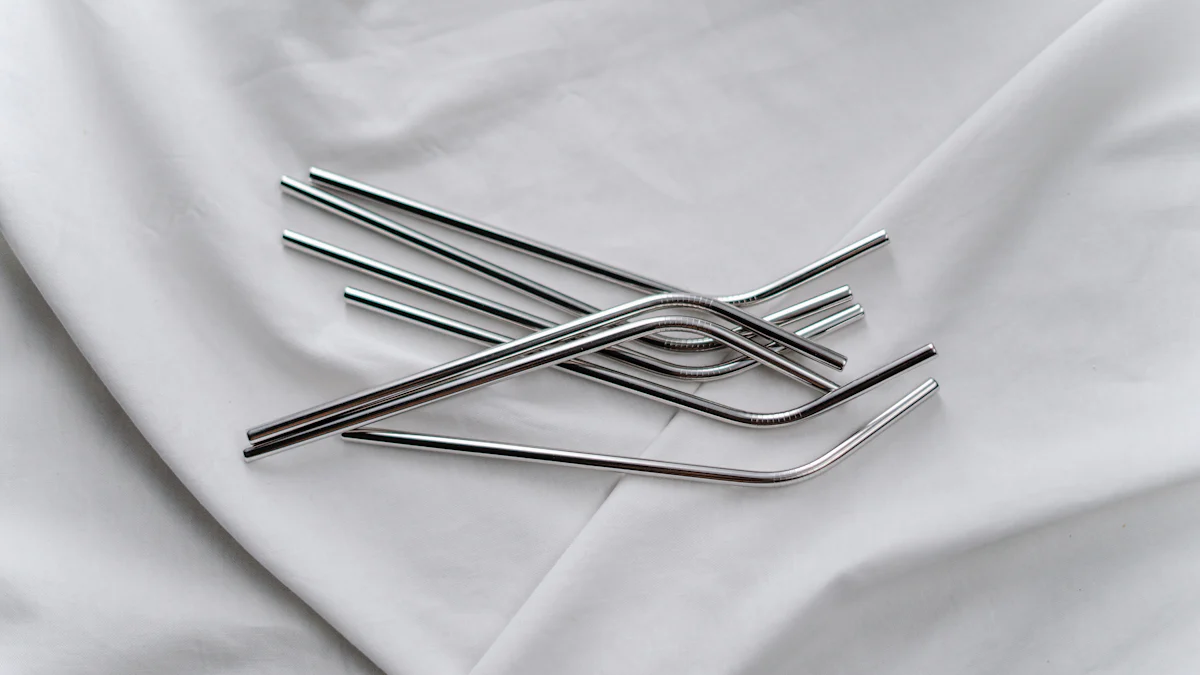
When I delve into the corrosion resistance of 316-vs-321-stainless-steel, I find distinct characteristics that set them apart. Each type of stainless steel offers unique advantages in different environments, making it crucial to understand their specific properties.
316 Stainless Steel Corrosion Resistance
316 stainless steel stands out for its exceptional corrosion resistance, particularly in environments rich in chlorides. The presence of molybdenum, ranging from 2-3%, significantly enhances its ability to withstand pitting and crevice corrosion. This makes 316 stainless steel an ideal choice for applications in marine environments, chemical processing, and even in the construction of desalination plants. Its robust resistance to chloride-induced corrosion ensures longevity and reliability in harsh conditions.
321 Stainless Steel Corrosion Resistance
On the other hand, 321 stainless steel excels in high-temperature applications. The addition of titanium plays a pivotal role in its corrosion resistance. Titanium stabilizes the alloy, preventing carbide precipitation during welding or exposure to elevated temperatures. This characteristic makes 321 stainless steel particularly effective in resisting intergranular corrosion. While it may not match the chloride resistance of 316, its ability to maintain structural integrity at high temperatures makes it invaluable in aerospace and thermal processing industries.
Heat Resistance
When I explore the heat resistance of 316-vs-321-stainless-steel, I uncover fascinating differences that influence their applications in high-temperature environments. Each type of stainless steel offers unique advantages, making it essential to understand their specific properties.
316 Stainless Steel Heat Resistance
316 stainless steel demonstrates commendable performance in moderate heat conditions. Its composition, enriched with molybdenum, provides excellent corrosion resistance, especially in chloride-rich environments. However, when it comes to heat resistance, 316 stainless steel has its limitations. It can withstand temperatures up to approximately 800°C (1472°F) before its structural integrity begins to degrade. This makes it suitable for applications where moderate heat exposure is expected, such as in chemical processing equipment and food industry machinery.
321 Stainless Steel Heat Resistance
In contrast, 321 stainless steel excels in high-temperature applications. The addition of titanium plays a crucial role in enhancing its thermal stability. Titanium acts as a stabilizing element, preventing sensitization and carbide precipitation at elevated temperatures. This characteristic allows 321 stainless steel to maintain its structural integrity even at temperatures reaching 870°C (1598°F). Its superior heat resistance makes it an ideal choice for applications in aerospace, thermal processing, and automotive industries, where prolonged exposure to high temperatures is common.
The scientific research findings highlight that 321 stainless steel offers superior heat resistance and thermal stability compared to 316 stainless steel. The titanium content in 321 stainless steel prevents sensitization, a problem where chromium carbides form at grain boundaries during welding or prolonged heat exposure. This makes 321 stainless steel particularly effective in resisting intergranular corrosion, ensuring its reliability in demanding environments.
Mechanical Properties
When I examine the mechanical properties of 316-vs-321-stainless-steel, I notice distinct differences that influence their applications. Each type of stainless steel offers unique advantages, making it essential to understand their specific mechanical characteristics.
316 Stainless Steel Mechanical Properties
316 stainless steel impresses me with its robust mechanical properties. It exhibits excellent tensile strength and yield strength, which makes it suitable for demanding environments. The presence of molybdenum enhances its overall durability, allowing it to withstand significant stress without deforming. This characteristic proves invaluable in industries where structural integrity is paramount, such as construction and marine applications.
- Tensile Strength: Approximately 515 MPa
- Yield Strength: Around 205 MPa
- Elongation: 40% in 50 mm
The high nickel content in 316 stainless steel contributes to its impressive ductility, enabling it to be formed into various shapes without cracking. This property makes it a preferred choice for manufacturing components that require intricate designs and precise dimensions.
321 Stainless Steel Mechanical Properties
On the other hand, 321 stainless steel offers a different set of mechanical properties that cater to specific needs. The addition of titanium significantly enhances its mechanical stability, especially at elevated temperatures. This makes 321 stainless steel an ideal choice for applications involving prolonged exposure to high heat, such as in aerospace and automotive industries.
- Tensile Strength: Approximately 505 MPa
- Yield Strength: Around 215 MPa
- Elongation: 40% in 50 mm
The titanium content in 321 stainless steel prevents the formation of chromium carbides, which can weaken the material during welding or heat treatment. This feature ensures that 321 stainless steel maintains its mechanical integrity even under challenging conditions, providing reliability and longevity in high-temperature environments.
Applications
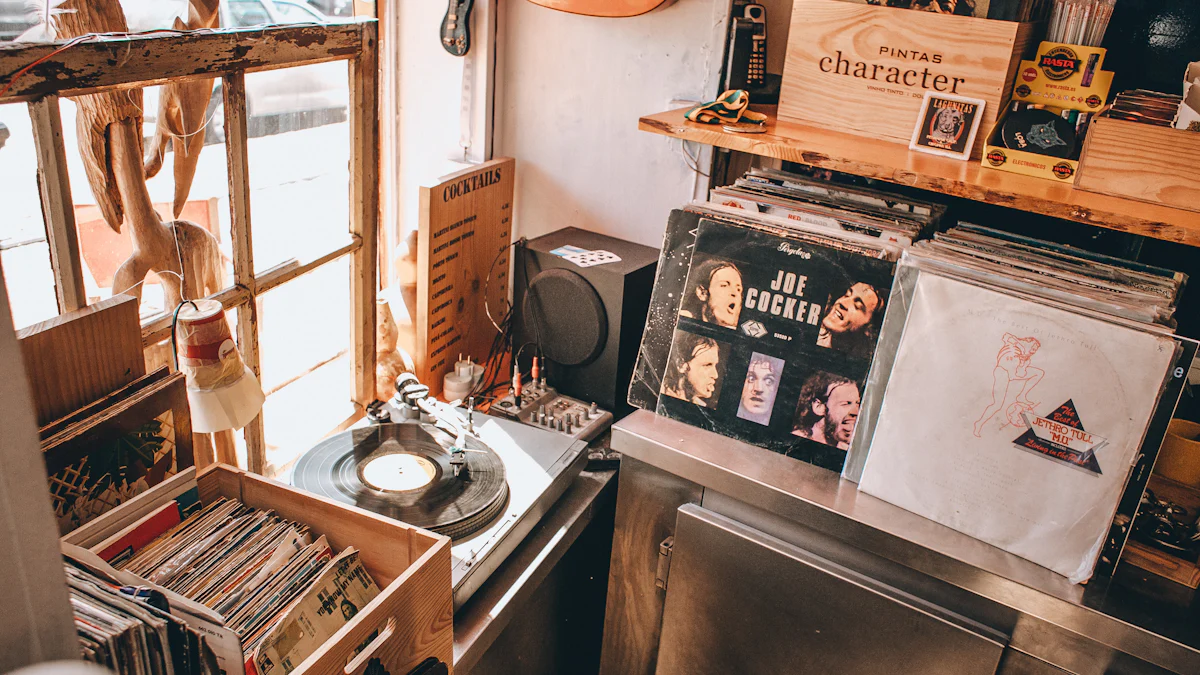
When I explore the applications of 316-vs-321-stainless-steel, I find that each type serves distinct purposes due to their unique properties. Understanding these applications helps in selecting the right material for specific needs.
Common Uses of 316 Stainless Steel
316 stainless steel proves invaluable in environments where corrosion resistance is paramount. Its robust composition makes it ideal for:
- Marine Applications: The high resistance to saltwater corrosion makes 316 stainless steel a preferred choice for boat fittings, marine hardware, and coastal architectural structures.
- Food Processing Equipment: Its ability to withstand various acids and cleaning agents ensures hygiene and durability in food processing plants.
- Chemical Processing Equipment: The material’s resilience against corrosive chemicals makes it suitable for storage tanks, chemical reactors, and piping systems.
- Pharmaceutical Equipment: The non-reactive nature of 316 stainless steel ensures safety and reliability in pharmaceutical manufacturing processes.
Common Uses of 321 Stainless Steel
321 stainless steel excels in high-temperature environments, thanks to its titanium stabilization. This makes it suitable for:
- Aerospace Applications: Its ability to withstand high temperatures and resist intergranular corrosion makes it ideal for jet engine components and exhaust manifolds.
- Automotive Exhaust Systems: The material’s thermal stability ensures longevity and performance in exhaust systems and heat shields.
- Industrial Heat Exchangers: Its resistance to oxidation and scaling at elevated temperatures makes it a reliable choice for heat exchangers and thermal oxidizers.
- Boilers and Furnace Components: The high-temperature stability of 321 stainless steel ensures structural integrity in boilers and furnace components, making it a staple in thermal processing industries.
The choice between 316 and 321 stainless steel depends on the specific requirements of the application, whether it involves exposure to corrosive environments or high temperatures.
Cost Considerations
When I evaluate the cost considerations of 316 vs 321 stainless steel, I find distinct differences that influence their selection for various applications. Understanding these cost factors is crucial for making informed decisions.
Cost of 316 Stainless Steel
316 stainless steel generally commands a higher price compared to 321 stainless steel. This increased cost stems from its composition, which includes higher nickel content and the addition of molybdenum. These elements enhance its corrosion resistance, especially in chloride-rich environments, making it a preferred choice for demanding applications. The investment in 316 stainless steel pays off in environments where superior corrosion resistance and durability are paramount. Industries such as marine, chemical processing, and pharmaceuticals often opt for 316 stainless steel despite its higher cost due to its long-term reliability and performance.
Cost of 321 Stainless Steel
In contrast, 321 stainless steel offers a more cost-effective solution. Its lower nickel content and the presence of titanium for stabilization contribute to its affordability. While it may not match the chloride resistance of 316 stainless steel, 321 excels in high-temperature applications. The cost-effectiveness of 321 stainless steel makes it an attractive option for industries like aerospace and automotive, where thermal stability and resistance to intergranular corrosion are critical. By choosing 321 stainless steel, businesses can achieve significant cost savings without compromising on performance in high-temperature environments.
Understanding the key differences between 316 and 321 stainless steel is crucial for selecting the best material for specific applications. Both grades offer excellent corrosion resistance, but their unique properties cater to different needs.
- 316 Stainless Steel: Ideal for environments rich in chlorides due to its superior corrosion resistance. It suits marine and chemical processing applications.
- 321 Stainless Steel: Excels in high-temperature settings, making it perfect for aerospace and automotive industries.
Choosing the right material ensures the success of engineering projects by aligning with specific application requirements.
FAQ
How is stainless steel 316 different from 321?
When I compare stainless steel 316 to 321, the primary difference lies in their carbon content. 316 stainless steel boasts higher corrosion resistance, making it ideal for environments rich in chlorides. In contrast, 321 stainless steel excels in resisting intergranular corrosion, especially at elevated temperatures. This makes 321 a preferred choice for high-temperature applications.
What are the key differences between 316 and 321 stainless steel?
Both 316 and 321 are austenitic stainless steels known for their excellent corrosion resistance. However, they differ in composition and application suitability. 316 contains molybdenum, enhancing its resistance to pitting and crevice corrosion. Meanwhile, 321 includes titanium, which stabilizes the alloy against carbide precipitation during welding or heat exposure. These differences make each grade better suited for specific industrial needs.
When selecting between 316 and 321 stainless steel, what is essential to consider?
In my experience, selecting between 316 and 321 stainless steel requires careful consideration of the application’s specific requirements. Factors such as exposure to corrosive environments, temperature stability, and mechanical stress play crucial roles. Each grade offers distinct advantages tailored to different industrial needs, ensuring optimal performance and longevity.
Which stainless steel grade is more cost-effective, 316 or 321?
From a cost perspective, 321 stainless steel generally offers a more affordable solution. Its lower nickel content and titanium stabilization contribute to its cost-effectiveness. While 316 may have a higher price due to its molybdenum content, it provides superior corrosion resistance in chloride-rich environments, justifying the investment for certain applications.
Can 316 stainless steel be used in high-temperature applications?
316 stainless steel performs well in moderate heat conditions, withstanding temperatures up to approximately 800°C (1472°F). However, for applications involving prolonged exposure to high temperatures, 321 stainless steel proves more suitable due to its enhanced thermal stability provided by titanium.
Is 321 stainless steel suitable for marine applications?
While 321 stainless steel offers excellent high-temperature stability, it does not match the chloride resistance of 316 stainless steel. For marine applications, where exposure to saltwater is common, 316 stainless steel remains the preferred choice due to its superior corrosion resistance.
What industries commonly use 316 stainless steel?
Industries that prioritize corrosion resistance often choose 316 stainless steel. Its robust composition makes it ideal for marine applications, food processing equipment, chemical processing, and pharmaceutical manufacturing. The material’s ability to withstand various acids and cleaning agents ensures hygiene and durability.
Why is titanium added to 321 stainless steel?
Titanium plays a crucial role in 321 stainless steel by stabilizing the alloy. It prevents carbide precipitation during welding or exposure to high temperatures, enhancing the material’s resistance to intergranular corrosion. This characteristic makes 321 stainless steel particularly effective in high-temperature applications.
How does molybdenum enhance 316 stainless steel?
Molybdenum significantly enhances 316 stainless steel’s corrosion resistance, particularly against pitting and crevice corrosion. This makes 316 an ideal choice for environments rich in chlorides, such as marine and chemical processing applications. The presence of molybdenum ensures the material’s longevity and reliability in harsh conditions.
Can 321 stainless steel be used in aerospace applications?
Yes, 321 stainless steel is well-suited for aerospace applications. Its ability to withstand high temperatures and resist intergranular corrosion makes it ideal for components like jet engine parts and exhaust manifolds. The material’s thermal stability ensures performance and reliability in demanding aerospace environments.