What Is Sintered Stainless Steel?
Sintered stainless steel is a material produced through a process known as powder metallurgy, specifically sintering. In this process, fine stainless steel powder is compacted into a desired shape and then heated below its melting point, allowing the particles to bond together without fully liquefying. This results in a solid, porous structure that retains the essential properties of stainless steel, such as corrosion resistance, strength, and durability.
The Stainless Steel Sintering Process
The stainless steel sintering process is part of powder metallurgy, where stainless steel powder is compacted into a desired shape and then subjected to controlled heating. This process allows the material to achieve high strength and specific mechanical properties while maintaining the benefits of stainless steel, such as corrosion resistance. Here’s a detailed breakdown of the stainless steel sintering process:
-
Powder Production
The first step is the production of fine stainless steel powder. There are two primary methods:
- Atomization: Stainless steel is melted and then atomized using gas or water, breaking it into fine particles.
- Mechanical Pulverization: Stainless steel is ground into powder mechanically, though this is less common for high-quality powders.
-
Blending and Mixing
Before sintering, the stainless steel powder is blended with additives such as lubricants or binders. These additives:
- Improve flow during compaction.
- Aid in the removal of the green part from the mold.
- Help in controlling shrinkage and porosity during sintering.
-
Compaction
The blended stainless steel powder is compacted in a die or mold under high pressure (often 200-1000 MPa). This creates a “green part,” a semi-solid but fragile shape that has the desired geometry of the final product but lacks strength.
- Cold Isostatic Pressing (CIP) and Uniaxial Pressing are common methods for compaction.
- The green part has low strength and density, so further steps are required to densify it.
-
Sintering
Sintering is the critical phase of the process, where the compacted powder is heated in a furnace. The furnace temperatures are typically 70-90% of the stainless steel’s melting point (around 1100°C-1350°C). During sintering:
- The stainless steel particles bond (through solid-state diffusion) without fully melting.
- Densification occurs, meaning the pores within the part shrink, and the material becomes more solid.
- A controlled atmosphere (inert gases like argon, hydrogen, or nitrogen) is used to prevent oxidation and control the sintering environment.
-
Cooling
After sintering, the material is cooled in a controlled manner to maintain its shape and mechanical properties. Rapid cooling may cause stresses or distortions, so gradual cooling is preferred.
-
Post-Sintering Operations (Optional)
Depending on the application, additional steps may be performed after sintering to further enhance the properties:
- Secondary machining: Further refining of the dimensions or surface finish.
- Heat treatment: To enhance mechanical properties like hardness and strength.
- Infiltration: Filling remaining pores with another material to improve density.
- Surface treatment: Coatings, polishing, or passivation to improve corrosion resistance or appearance.
Key Considerations in Stainless Steel Sintering:
- Atmosphere Control: Stainless steel can oxidize easily, so sintering must occur in a controlled, reducing, or inert atmosphere to avoid contamination.
- Shrinkage: Parts shrink during sintering due to the densification process, and the design must account for this.
- Porosity: The final product may still have some controlled porosity, which can be beneficial or undesirable depending on the application (e.g., filters vs. structural components).
Benefits of Sintered Stainless Steel for Parts
-
Cost Efficiency:
- Minimal Waste: Sintering uses near-net-shape production, meaning less material waste compared to traditional machining.
- Lower Material Costs: Powder metallurgy often allows the use of less raw material, reducing overall costs.
- High-Volume Production: Once tooling is created, the process is highly repeatable, making it efficient for mass production.
-
Design Flexibility:
- Complex Geometries: Sintering enables the production of intricate shapes and detailed designs that would be challenging or expensive to machine.
- Customizable Properties: Through process control, manufacturers can tailor properties like density, porosity, and strength for specific applications.
-
Consistent Quality:
- Precision Tolerance: Sintering allows for tight dimensional tolerances, reducing the need for secondary machining.
- Homogeneous Material: The powder metallurgy process ensures uniform material distribution, resulting in consistent mechanical and chemical properties throughout the part.
-
Mechanical Strength:
- Durability: Sintered stainless steel retains excellent strength and toughness, comparable to wrought stainless steel in many cases.
- Wear Resistance: Parts produced using sintering can be highly wear-resistant, making them ideal for demanding environments.
-
Corrosion Resistance:
- Sintered stainless steel maintains the corrosion-resistant properties of stainless steel, making it suitable for applications exposed to moisture, chemicals, or harsh environments.
-
Porosity Control:
- Porous Structures: The sintering process can produce parts with controlled porosity, which is valuable in applications like filtration and fluid distribution systems.
-
Environmentally Friendly:
- Energy Efficiency: The sintering process uses lower temperatures than traditional melting methods, reducing energy consumption.
- Reduced Emissions: Sintering typically requires fewer emissions and less environmental impact compared to traditional metal casting or forging.
The typical materials used to make sintered stainless steel parts are:
-
Austenitic Stainless Steels (300 Series)
- Common Grades: 304L, 316L
- Properties: Austenitic stainless steels are non-magnetic and highly resistant to corrosion, particularly in environments containing moisture, acids, or chloride. They also maintain good strength at high temperatures.
- Applications: These are used in applications where excellent corrosion resistance is crucial, such as medical implants, food processing equipment, and chemical processing machinery.
- Powder Type: Low-carbon versions (denoted by “L”) are commonly used to prevent carbide precipitation during sintering, ensuring better corrosion resistance and toughness.
-
Martensitic Stainless Steels (400 Series)
- Common Grades: 410, 420
- Properties: Martensitic stainless steels are magnetic, possess high strength and hardness, and offer moderate corrosion resistance. These steels can be hardened by heat treatment, which enhances their wear resistance and toughness.
- Applications: These materials are ideal for producing sintered parts like cutting tools, bearings, and wear-resistant components that require high mechanical strength.
- Powder Type: Typically, martensitic stainless steel powders are selected for applications where high hardness and wear resistance are more important than corrosion resistance.
-
Ferritic Stainless Steels (400 Series)
- Common Grades: 434, 430L
- Properties: Ferritic stainless steels are magnetic and offer good corrosion resistance, particularly against stress corrosion cracking. They have lower cost compared to austenitic steels and can withstand high temperatures but cannot be hardened by heat treatment.
- Applications: These steels are often used in automotive exhaust systems, heat exchangers, and other components where moderate corrosion resistance and cost-effectiveness are required.
- Powder Type: Ferritic stainless steel powders provide excellent thermal conductivity and resistance to oxidation at high temperatures.
-
Precipitation-Hardening (PH) Stainless Steels
- Common Grades: 17-4 PH
- Properties: PH stainless steels combine high strength, good corrosion resistance, and the ability to be hardened through precipitation heat treatment. These steels are particularly known for their superior mechanical properties.
- Applications: These are used in aerospace, medical, and industrial applications where high strength and corrosion resistance are necessary, such as turbine blades, shafts, and surgical tools.
- Powder Type: 17-4 PH powders are widely used in sintering to produce parts that require a balance of strength and corrosion resistance with minimal post-processing.
-
Duplex Stainless Steels
- Common Grades: 2205
- Properties: Duplex stainless steels are a mix of austenitic and ferritic microstructures, offering better strength and corrosion resistance than either phase alone. They are particularly resistant to stress corrosion cracking and pitting.
- Applications: Used in demanding applications such as oil and gas equipment, chemical processing, and marine environments.
- Powder Type: Duplex stainless steel powders provide both high strength and superior resistance to corrosive environments, especially in marine and oil and gas sectors.
-
Powder Additives and Binders
- Carbon: Small amounts of carbon can be added to improve the strength and hardness of the sintered part. However, careful control is needed to avoid excessive carbon content, which can negatively impact corrosion resistance.
- Binders/Lubricants: Organic binders or lubricants are often added to stainless steel powders to improve flowability and compaction. These additives burn off during sintering, leaving behind a solid, compacted metal part.
Custom Powder Blends
In many cases, custom blends of stainless steel powders are used to optimize specific properties for the intended application. By varying the levels of elements such as chromium, nickel, molybdenum, and manganese, manufacturers can adjust the alloy’s mechanical and chemical characteristics to meet precise specifications.
Types of Sintered Stainless Steel Parts
Structural Parts
- Description: Sintered stainless steel is often used to create strong, durable structural components with complex geometries that may be difficult or expensive to machine.
- Characteristics: High strength, wear resistance, and excellent dimensional accuracy.
- Examples:
- Gears
- Bushings
- Bearings
- Connectors
Porous Parts
- Description: Some sintered stainless steel parts are designed with controlled porosity, making them ideal for applications where filtering, fluid flow, or gas diffusion is needed.
- Characteristics: Engineered porosity, good corrosion resistance, and thermal stability.
- Examples:
- Filters
- Fluid distribution systems
- Catalytic converters
Magnetic Parts
- Description: Certain grades of stainless steel, such as martensitic or ferritic types, can be sintered into parts that require magnetic properties.
- Characteristics: High strength and magnetic properties.
- Examples:
- Motor components
- Sensors
- Electromagnetic actuators
Wear-Resistant Parts
- Description: Sintered stainless steel components designed to withstand high friction and wear are often used in mechanical systems that involve repetitive movement or contact.
- Characteristics: Excellent hardness, wear resistance, and mechanical durability.
- Examples:
- Cutting tools
- Valve components
- Machine tools
Heat-Resistant Parts
- Description: These parts are made from stainless steel alloys designed to operate at elevated temperatures without losing strength or corroding.
- Characteristics: High temperature resistance and oxidation resistance.
- Examples:
- Exhaust system components
- Heat shields
- Furnace components
Sintered Metal Parts (3)
About Us
Sintered stainless steel parts offer numerous benefits for a wide range of applications. JHMIM, a leader in custom metal solutions, specializes in delivering high-precision, high-quality, and cost-effective sintered metal components. We collaborate closely with our customers to provide tailored engineering solutions, ensuring the success of even the most complex projects.
To learn more about our sintered stainless steel capabilities or to request a quote, contact JHMIM today for reliable and expert support.
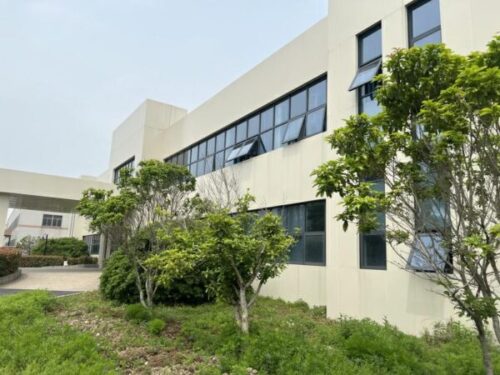
The production process involves several key steps:
- Powder Production: Creating fine metal powders from various metals or alloys.
- Compaction: Compressing the metal powder into a mold to form a “green” part.
- Sintering: Heating the green part in a controlled atmosphere to bond the metal particles.
- Secondary Operations: Additional processes like sizing, coining, heat treatment, machining, or surface treatment to achieve the final specifications.
Sintered metal parts can be made from a variety of materials, including:
- Iron and steel
- Copper and its alloys
- Aluminum
- Titanium
- Nickel
- Tungsten and more
The choice of material depends on the required properties of the final part, such as strength, hardness, electrical conductivity, or corrosion resistance.
Sintered metal parts offer several advantages over traditionally manufactured parts:
- Efficiency: Less material waste and often lower production costs.
- Precision: High dimensional accuracy and uniformity.
- Complexity: Ability to create complex shapes that might be challenging or impossible with traditional methods.
- Customization: Easier to produce custom parts in high volumes.
Sintered metal parts can achieve comparable strength and durability to forged or machined parts, especially when additional processes like heat treatment or machining are applied. The choice of metal powder and sintering conditions also play a crucial role in determining the final mechanical properties.
Yes, sintered metal parts can be heat-treated to enhance their mechanical properties such as hardness and strength. Heat treatment is a common secondary operation for improving the performance of sintered parts.
The maximum size of sintered metal parts is generally limited by the capabilities of the compaction equipment and the sintering furnace. However, advancements in technology are continually increasing the size limits. For very large parts, other manufacturing methods might be more suitable.
Quality assurance for sintered metal parts involves:
- Material Selection: Using high-quality metal powders.
- Process Control: Monitoring and controlling the compaction and sintering processes.
- Inspection: Conducting dimensional checks and mechanical testing on finished parts.
- Certification: Adhering to industry standards and certifications.
The lead time for producing sintered metal parts depends on several factors, including the complexity of the part, the volume of production, and the availability of materials. Generally, the powder metallurgy process allows for faster production times compared to traditional manufacturing methods, especially for large batches.