Introduction to Sintered Gears
Sintered gears, also known as powder metal gears, are manufactured using powder metallurgy processes. This involves compacting metal powders into a gear shape and then sintering them at high temperatures. This process creates strong, precise gears suitable for various industrial applications. Powder metallurgy sintered gears which involves the following key steps:
- Mixing metal powders with alloying elements and additives to create the desired composition.
- Compacting the powder mixture into the desired gear shape and size using high pressure.
- Sintering the compacted shape by heating it under controlled temperature and pressure, causing the metal particles to fuse together.
Common applications for sintered gears include
- Automobiles
- Power tools
- Medical instruments
- Domestic appliances
- Outdoor power equipment
- Marine equipment
- Reduction gears
- Transmission systems
- Camshafts and crankshafts
- Oil pump gears
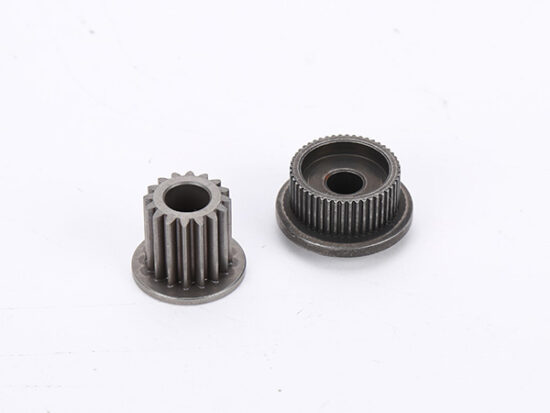
Window opener gear is a mechanical device designed to automatically open and close a window, using a gear system to control the movement of the window. These devices are usually electric or manually operated, and are designed to provide a convenient window operation experience, especially for high or hard-to-reach window locations, and places that require regular ventilation.
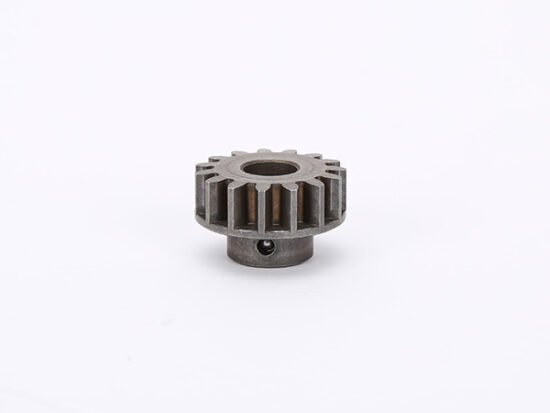
Sports equipment gear refers to critical components used in various sports equipment to transmit power and adjust movement. These gears are typically made from high-strength materials and crafted with precision to ensure durability and reliability under intense use by athletes. Common applications include bicycles, fitness equipment, and outdoor sports gear, where the design and performance of sports equipment gears directly impact safety and athletic performance.
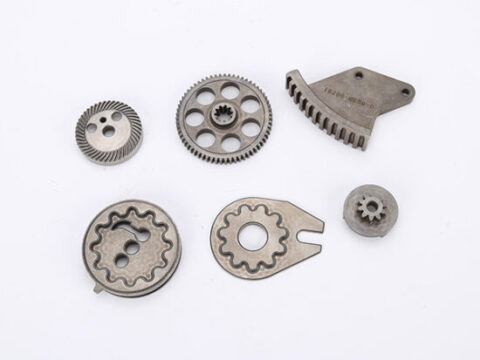
Automotive gears are essential components in vehicles, responsible for transmitting power from the engine to the wheels. These gears include various types such as spur gears, helical gears, bevel gears, and planetary gears, each serving specific functions like speed reduction, torque multiplication, and direction changes. They are precision-engineered using advanced manufacturing techniques to ensure efficiency, durability, and smooth operation within automotive drivetrains, contributing significantly to overall vehicle performance and reliability.
Main materials used for sintered gears include
Sintered gears are typically made from powdered metal alloys that are carefully selected to meet specific performance requirements. The main materials used for sintered gears include:
- Iron-Based Alloys: Low-alloyed iron-based powders are commonly used, especially when superior material strength is required.
- Steel Alloys: Various steel alloys can be used, including sinter-hardened steels which provide high hardness directly after sintering without the need for additional heat treatment.
- Stainless Steel: Some sintered gears are made with a stainless steel base for corrosion resistance.
- Alloy Additives: Manufacturers can incorporate additives such as nickel, molybdenum, and chromium to alter and enhance the properties of the gear.
The choice of material depends on the specific application and desired properties of the gear. For example, automotive transmissions may require different alloy compositions compared to gears used in power tools or industrial machinery.
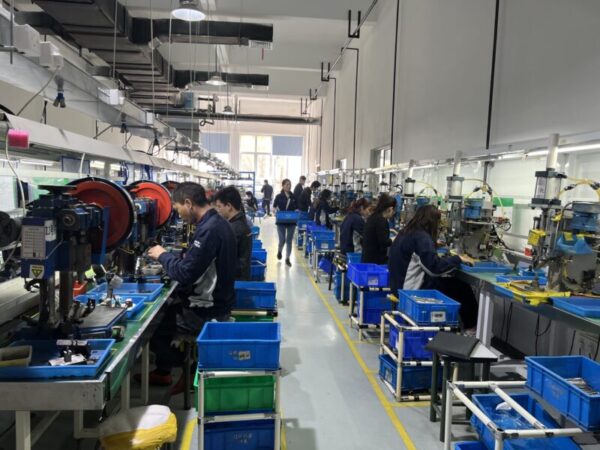
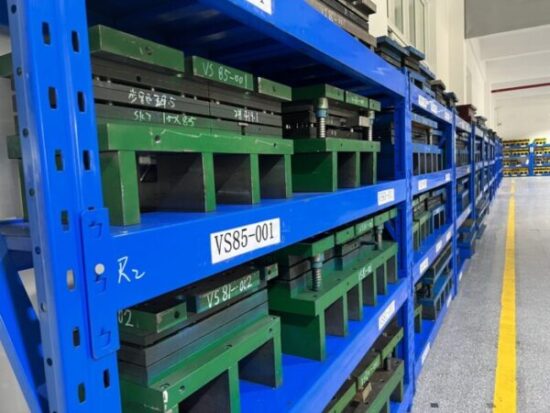
Sintered gears VS machined gears?
- Cost-effectiveness: Sintered gears are typically more economical to produce, especially for high-volume manufacturing, due to reduced material waste and fewer machining operations.
- Design flexibility: The powder metallurgy process allows for complex shapes and features to be created directly during compaction, enabling greater design freedom.
- Tight tolerances: Sintered gears can be produced with tight dimensional tolerances and consistency, often eliminating or reducing the need for additional machining.
- Material utilization: The powder metallurgy process has high material utilization, resulting in minimal waste compared to traditional machining methods.
- Environmental benefits: Sintered gear production is considered a “green” process due to its low energy usage and minimal scrap.
- Customizable material properties: The powder metallurgy process allows for tailoring of material composition to optimize performance for specific application.
- Improved surface finish: Sintered gears can achieve smooth surface finishes, especially when gear rolling is applied, potentially surpassing ground gears in some cases.
- Self-lubricating properties: Sintered gears can be impregnated with lubricants, enhancing their performance in certain applications.
- Weight reduction: In some cases, sintered gears can be designed to reduce overall weight compared to traditional gears.
- Sound dampening: The porous nature of sintered materials can contribute to reduced noise levels in gear operations.
- Suitability for mass production: Sintered gears offer excellent repeatability and consistency, making them ideal for high-volume manufacturing.
Sintered gears mainly include spur gears, helical gears, bevel gears, worm gears, internal gears, planetary gears, rack and pinion gears, etc. Spur gears and helical gears are used for parallel shaft transmission, bevel gears are used for intersecting shaft transmission, worm gears are suitable for large reduction ratios and high torque output, internal gears are often used in planetary gear systems, which have compact structures and high transmission efficiency, while rack and pinion gears convert rotational motion into linear motion.
JHMIM, a leading manufacturer of metal powders products, offers a range of mixes and alloys that can be optimized for each application, providing a balance between performance and cost. The powder metallurgy process allows for great flexibility in material selection and composition, enabling manufacturers to tailor the gear properties to specific requirements.